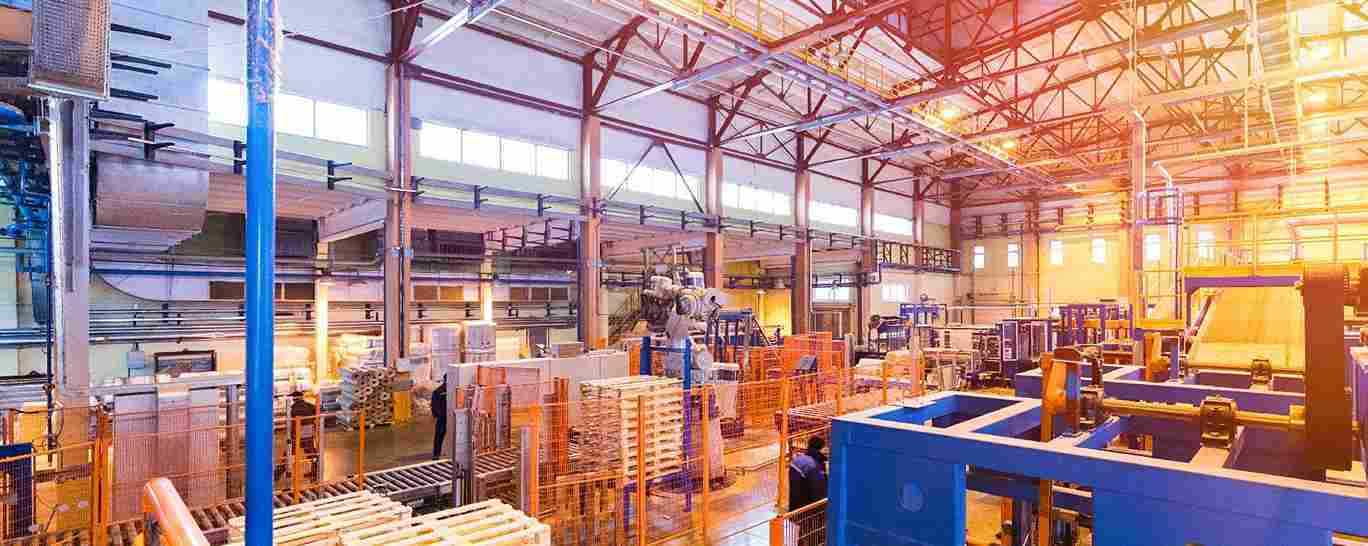
What is Maintenance Management Software?
Maintenance Connection is a leading maintenance management CMMS software that helps businesses maximize operational efficiency.
Solutions
Workplace Management Solutions
Real Estate Management Solutions
Maintenance Management Solutions
Energy Management Solutions
Engineering Document Management Solutions
Asset Management Solutions
Automate campus scheduling for classes, meetings, and exams with our EMS software.
Plan and manage conferences effortlessly with EMS software to impress guests and streamline operations.
Boost workplace flexibility and maximize space use with seamless desk and room booking.
Organize workplace or campus events smoothly, creating memorable experiences.
Optimize workspace, manage allocations efficiently, and reduce costs with our space management solutions.
Deliver projects on time and within budget by improving communication, collaboration, and efficiency with our software.
Streamline lease accounting for ASC 842, IFRS, and GASB compliance.
Manage leases efficiently by tracking key dates, analyzing costs, and ensuring compliance.
Centralize data and analytics for better insights, faster negotiations, and revenue growth.
Centralize facility and asset maintenance, automate work orders, and ensure compliance with our CMMS software.
Extend asset life, reduce downtime, and prevent costly repairs with data-driven monitoring.
Prevent equipment failures and extend asset life by detecting and addressing issues early.
Make sustainable, cost-efficient energy decisions by monitoring and optimizing power consumption.
Remotely monitor and control equipment with real-time data to predict issues, boost efficiency, and reduce downtime.
Easily share and collaborate on documents, creating a single source of truth for engineers and contractors.
Manage and analyze assets across their lifecycle to schedule maintenance, reduce downtime, and extend lifespan.
Improve visibility, automate work orders, and ensure compliance for efficient facility and asset management.
Resources
Browse our full library of resources all in one place, including webinars, whitepapers, podcast episodes, and more.
Support
Looking for access to technical support, best practices, helpful videos, or training tools? You’ve come to the right place.
About Accruent
Get the latest information on Accruent, our solutions, events, and the company at large.
A CMMS or computerized maintenance management system is software that helps plan, monitor, & report maintenance tasks, track work orders & schedule maintenance.
Table of contents
At a high level, maintenance teams large and small use a CMMS to easily and efficiently get maintenance work done. But what exactly is CMMS maintenance software, how is it used, and what benefits does it provide?
This guide is here to help you deepen your understanding of:
A CMMS ― computerized maintenance management system ― helps you plan, monitor, report, and optimize your maintenance activities ― so you can easily track work orders, maintain assets, and schedule maintenance.
CMMS software provides a single source of truth for all facility and maintenance information maintenance operations need, all from one centralized, real-time system.
With a CMMS, your organization can more easily:
Modern CMMS systems can also provide EAM-level functionalities and integrate with other integral tools like space planning, mobile surveying tools, an EAM system, preventive maintenance scheduling, and IoT remote monitoring tools.
A modern CMMS system should be easy-to-use and device agnostic on mobile so technicians and key personnel in the field can easily retrieve procedures and documentation, check part availability, initiate orders, evaluate maintenance history, maintain compliance and update work orders.
Your CMMS must integrate with other mission-critical systems and equipment so your team can effectively capture, analyze and utilize critical data. This is straightforward using Accruent’s Maintenance Connection RESTful API, which can instantly connect key applications to your CMMS.
User adoption is essential to the success of a CMMS implementation. Easy-to-use, intuitive software is much more likely to be adopted, so look for a CMMS system that is suited to your employees’ processes and responsive to their maintenance activity needs.
Modern, top-tier CMMS systems come equipped with many features to keep your sensitive information safe, including single sign-on for secure authentication, secure cloud storage and refined access to controls, authorizations and restrictions.
CMMS implementation will require data migration from disparate, legacy systems. These migrations should be straightforward in your CMMS solution so you can facilitate collaboration and ensure that your data is comprehensive, up-to-date and actionable.
While a vendor’s CMMS software itself is the most important factor in selection and buying process, the CMMS vendor organization should be equally important. The right CMMS provider will be your partner and offer help with implementation, training, and ongoing support.
Effective facility maintenance work requires smooth work order management and field service execution. A robust CMMS facilitates this by allowing users to review, prioritize, assign, schedule and track both work orders and associated maintenance tasks. It will also provide full visibility into work orders, work order history, part history and more.
Many automations should be available in your CMMS, including the ability to schedule maintenance - by setting up time, usage or condition-based maintenance triggers – and automated alerts to technicians including details like repair histories, checklists, asset manuals and more.
Using customized CMMS reports and analytics, you should be able to extract meaningful data that your maintenance operations can use to pinpoint preventive maintenance needs, manage KPIs and optimize facility management processes and performance.
Your CMMS maintenance management software should help you keep a trail of the information most compliance audits look for when assessing if an organization has meet the necessary standards. Specifically, demonstrate that you maintain employee compliance, keep searchable work records, and generate the automated audit logs you need to simplify compliance with regulatory, industry, geographic and other audits.
Check out the key features that have earned Maintenance Connection top acknowledgements in G2’s Grid Report.
When you use a powerful CMMS like Maintenance Connection, you can see great impacts on your maintenance management processes and business goals:
Notifications and reporting help make great decisions on what's important. Accurate and easy-to-understand information helps organize and direct the people that perform the work.”
― Data Analyst, Capterra review
Notifications and reporting help make great decisions on what's important. Accurate and easy-to-understand information helps organize and direct the people that perform the work.”
― Data Analyst, Capterra review
The advances we have made in scheduling and reporting have taken our daily operations to the next level of performance.”
— Director for Facilities & Maintenance, Capterra review
Seamless SAP integration for asset parts ordering. Asset hierarchy structure for relevant PM reliability concepts. Can easily be configured in so many different ways for future forward asset configuration and auto add PM configuration based on asset class.”
— Maintenance Supervisor, G2 review
Communication within our department is streamlined with work order assignment notifications and the use of the MC mobile app by our technicians. Updates to work orders can be made in real time, so the base office is aware as soon as repairs are completed. We can also directly email contractors their new work orders and allow requesters to view the status of their requests."
— CSU Chico
A flexible, versatile and highly reliable CMMS … so you can see all levels of the maintenance operation which includes maintenance history, WO status, work history, asset history, purchasing and all other aspects of maintenance.”
― Maintenance Planner, Capterra review
Learn more about how our customers improved work order processes, implemented preventive maintenance schedules, and more by checking out our customer case studies.
This comprehensive pricing calculator is designed to provide you with a clear, customized cost breakdown for Maintenance Connection’s CMMS software.
Many modern CMMS systems are using machine learning and AI developments to expand their predictive maintenance management capabilities. Ultimately, this kind of physical asset insight can help your business increase efficiency, connect systems, improve team management, budget effectively, prioritize work orders, reduce downtime, manage assets and equipment, and more – all from one centralized, easy-to-use system.
A good CMMS provider will want to be your partner, and they will provide help with implementation, training and ongoing support. The right vendor will also help you customize your functionality and user experience so your CMMS fits the unique needs and preferences of your maintenance team.
A cloud-based, SaaS CMMS deployment offers many benefits over an on-premise deployment, including increased mobility, maximized scalability, full integration with other systems, increased security and decreased need for a robust in-house IT infrastructure.
At minimum, a CMMS system should offer reporting, mobile CMMS maintenance capabilities, asset management and MRO inventory management. That said, you must strategically and proactively choose extended features of your implementation to develop a system that works best for your team.
A CMMS system can replace outdated disparate systems – like Excel sheets, Word documents and physical paperwork – to help users effectively manage assets, supplies, work orders and related information. This can ultimately increase efficiency and transparency.
Key CMMS features – including key and lock management, mobile access, a browser and device-agnostic user interface, API access, and barcode-enabled workforce tracking – can allow businesses to better manage teams and employees.
Emergency repairs, incomplete asset information, and reactive maintenance practices can skyrocket facility maintenance costs. A robust CMMS can significantly reduce these costs by streamlining key maintenance task processes, including work order management, MRO (maintenance, repair, and operating supply) inventory management and more.
By reducing concerns like unavailable inventory, unexpected downtime or emergency breakdowns, a CMMS can ultimately help increase operational efficiency, maximize uptime and answer questions related to service history, vendor track record and more.
You can use a CMMS to get accurate historical and real-time data about any work request, billing and invoicing, reporting and analytics, inventory and asset management information and service history. This information can also be consolidated in customizable reports to facilitate informed decision-making.
A robust CMMS can maximize employee safety by simplifying audits, making safety procedures more accessible and allowing your maintenance manager to easily stay on top of safety training.
MRO inventory involves the order, use, and tracking of thousands of spare parts. A CMMS simplifies MRO management and improves inventory accuracy by automating purchases, tracking part information and measuring big-picture metrics like inventory costs and usage statistics.
Maintenance Connection CMMS work order management system can help you submit, manage and track work orders so you can streamline your workflows, simplify your work order management, prepare for audits, decrease equipment downtime and ultimately increase your preventive maintenance practices.
Low visibility into key asset information like usage, repair history, and performance can lead to inefficiency and costly reactive maintenance practices. CMMS software can solve these problems by providing all relevant asset data in one integrated, easy-to-access platform.
of all CMMS Implementations Fail
Implementation Success Rate with Maintenance Connection
Maintenance Connection Customer Renewal Rate
The right CMMS can maximize your ROI by allowing your business to increase efficiency, connect systems, reduce downtime, make data-driven decisions, budget effectively, prioritize work orders and more – all from one customizable, centralized solution. This can ultimately help you save time, save money and get organized.
CMMS and enterprise asset management (EAM) systems were once considered to be vastly different tools. Now, thanks in part to Wi-Fi, the fourth Industrial Revolution and rising IoT capabilities, many modern CMMS systems can offer enterprise-wide solutions and EAM-type functionality. What’s more, they can easily merge with other providers to strengthen their offerings.
That said, there can still be differentiation between the tools:
CMMS: Computerized maintenance management systems can be considered as dedicated tools created to facilitate asset maintenance management and extend equipment life. They are not made to provide extended functionality beyond that scope.
EAM: Enterprise asset management (EAM) software provides a wider range of features to track, manage, and analyze asset performance and costs through the whole asset lifecycle, from acquisition to disposal.
Accruent Maintenance Connection solution can serve as both a CMMS software or a full-function EAM system.
Industries that can benefit from a computerized maintenance management system (CMMS) or enteprise asset management system (EAM) include:
Computerized Maintenance Management System (CMMS) solutions are used by organizations looking for effective asset and facility maintenance management. Users can be found in many industries, including manufacturing, retail, healthcare, oil & gas, utilities, education, and corporate. A CMMS can help with five use cases across these industries, including linear asset maintenance, facility maintenance, production and manufacturing maintenance, field services maintenance, and fleet maintenance. It is most helpful for those who have struggled with common asset and facility maintenance concerns, including unplanned asset downtime, costly reactive maintenance practices, difficulty scheduling preventive maintenance, low visibility into asset health, and little transparency into big-picture historical and real-time data.
A dedicated Computerized Maintenance Management System (CMMS) administrator oversees the implementation and maintenance of a CMMS solution. A CMMS is a complicated tool that requires data development and management, metrics management, ongoing compliance, consistent upgrades, development and management of reports, employee training and more. If these tasks are left to existing employees, it can lead to inconsistent data, a loss of system integrity, and a return to reactive maintenance practices. Having a CMMS administrator, on the other hand, helps organizations make the most of a CMMS, increasing employee adoption and making data more transparent.
The cost of a CMMS software can vary based on the size of your business and the breadth of features that you’re looking for— and you can always get an accurate quote by reaching out directly. That said, general pricing includes:
If you choose the right CMMS, though, the savings and ROI that are attained from increased productivity and overall cost savings will certainly make it a worthwhile investment.
Recurring and renewal costs, which include the monthly subscription fee, pricing plan, customization cost and training services.
CMMS training refers to both immediate and ongoing training services offered by your CMMS vendor. Comprehensive training is absolutely necessary to streamline implementation and to ensure that your team makes the most out of your CMMS tool. The right partner will offer a range of training materials, including training videos and modules, articles, demos and free trials.
At Accruent, this kind of training is included in the Accruent Academy Learning Center. The Accruent Academy continuous training resources are there to help your team drive adoption, maximize ROI and meet compliance regulations.
A CMMS software can replace many antiquated or manual business systems, including but not limited to:
Uptime is critically important when it comes to facility and asset maintenance because high uptime means effective operations, maximized efficiency and substantial revenue. An effective CMMS or EAM system, otherwise known as a preventive management system, can increase uptime by providing the tools you need to implement effective preventive maintenance strategies. This can not only help you achieve reliable uptime, but also allow you to:
When selecting a CMMS software for your organization, it’s important to consider your business’ unique needs related to functionality, IT capabilities and your broader technological ecosystems. Most centrally, you should consider:
The push to SaaS is happening, with many CMMS and EAM solutions being deployes on the cloud as software as a service (SaaS). There are many benefits to a SaaS deployment that you should know about. Namely, a move to the cloud, or to a SaaS application, can:
Additionally, it can help your organization stay relevant and prepared for the future. The future is in SaaS, and organizations that continue to rely on on-premise systems will struggle to maintain strong communications, data integrity and clarity across their team members and facilities.
ERP (Enterprise Resource Planning) and CMMS (Computerized Maintenance Management System) are both software solutions used by organizations, but they serve distinct purposes. ERP is a comprehensive system that integrates various business processes like finance, HR, inventory, and sales into a unified platform. It provides a holistic view of an organization's operations to enhance efficiency and decision-making.
On the other hand, CMMS is specialized software focused specifically on managing maintenance activities, work orders, assets, and facilities. It streamlines maintenance operations by scheduling tasks, tracking maintenance history, and optimizing preventive maintenance.
While both systems can have some overlapping features, ERP is broader in scope, aiming to manage multiple aspects of business operations, while CMMS is laser-focused on optimizing maintenance processes. Organizations use ERP to manage their entire enterprise, while CMMS is used by maintenance teams to ensure equipment reliability, minimize downtime, and improve maintenance efficiency.
An example of a CMMS (Computerized Maintenance Management System) is the "Accruent CMMS Maintenance Software." Accruent CMMS is a comprehensive software solution designed to optimize maintenance operations for various industries. It offers features such as work order management, preventive maintenance scheduling, asset tracking, inventory control, and robust reporting capabilities. The software helps organizations streamline maintenance tasks, track equipment history, and improve overall operational efficiency.
Accruent CMMS allows users to create, assign, and manage work orders, ensuring that maintenance tasks are performed promptly and effectively. It facilitates preventive maintenance by scheduling routine tasks based on time or usage, minimizing equipment downtime and extending asset lifespan. With its asset tracking functionality, organizations can monitor the health and performance of their equipment.
The software's integration with other business systems and data analytics features helps organizations make informed decisions and optimize maintenance strategies. Accruent CMMS is used across industries like manufacturing, healthcare, facilities management, and more, to enhance maintenance processes and asset management.
Two types of CMMS (Computerized Maintenance Management System) are:
On-Premises CMMS: This type involves hosting the CMMS software locally within an organization's infrastructure. It is installed and maintained on the organization's own servers or hardware.
Cloud-Based CMMS: Also known as web-based or SaaS (Software as a Service) CMMS, this type is hosted and maintained by a third-party provider in the cloud. Users access the CMMS through a web browser.
Accruent’s CMMS Maintenance Connection Software offers both deployment options.
CMMS stands for computerized maintenance management system. Maintenance CMMS software helps maintenance teams optimize their activities by allowing them to easily track work orders, maintain assets, and schedule preventative maintenance. It is essential software for all enterprise maintenance departments.
The purpose of CMMS maintenance software is to efficiently manage maintenance operations in organizations. CMMS maintenance software helps teams schedule maintenance tasks, manage work orders, track inventory and costs, ensure compliance, optimize performance, extend asset lifespan, and promote safety in the workplace.
Maintenance Connection is a leading maintenance management CMMS software that helps businesses maximize operational efficiency.
Discover the meaning and secrets to successful maintenance management in 2024. Explore strategies to cut maintenance costs and boost operational ...
Preventive maintenance software is a tool that can help maintenance professionals prevent asset breakdown, extend asset life, and maximize technician ...
Subscribe to stay up to date with our latest news, resources and best practices