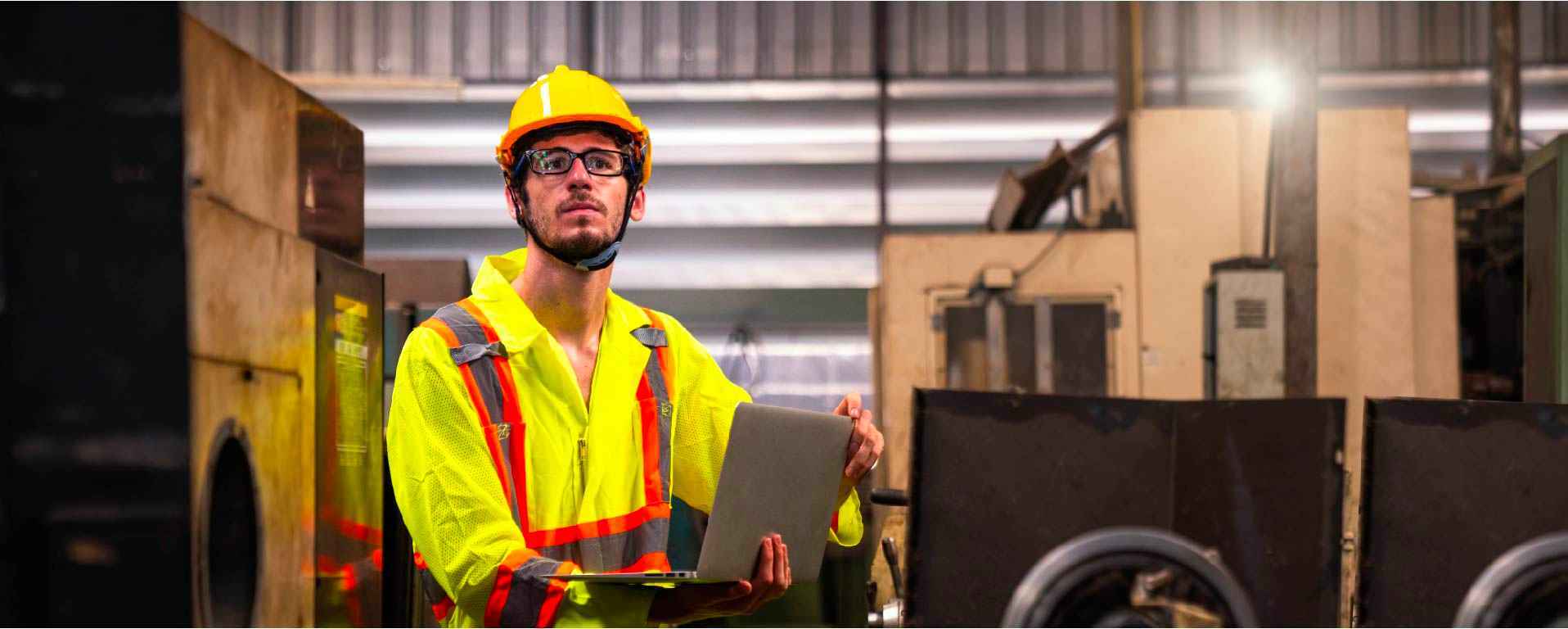
Preventive vs Predictive Maintenance: Taking Your Facility to the Next Step
What maintenance strategy -- or combination of strategies -- will work most effectively for your organization? Here are the key differences and ...
Solutions
Workplace Management Solutions
Real Estate Management Solutions
Maintenance Management Solutions
Energy Management Solutions
Engineering Document Management Solutions
Asset Management Solutions
Automate campus scheduling for classes, meetings, and exams with our EMS software.
Plan and manage conferences effortlessly with EMS software to impress guests and streamline operations.
Boost workplace flexibility and maximize space use with seamless desk and room booking.
Organize workplace or campus events smoothly, creating memorable experiences.
Optimize workspace, manage allocations efficiently, and reduce costs with our space management solutions.
Deliver projects on time and within budget by improving communication, collaboration, and efficiency with our software.
Streamline lease accounting for ASC 842, IFRS, and GASB compliance.
Manage leases efficiently by tracking key dates, analyzing costs, and ensuring compliance.
Centralize data and analytics for better insights, faster negotiations, and revenue growth.
Centralize facility and asset maintenance, automate work orders, and ensure compliance with our CMMS software.
Extend asset life, reduce downtime, and prevent costly repairs with data-driven monitoring.
Prevent equipment failures and extend asset life by detecting and addressing issues early.
Make sustainable, cost-efficient energy decisions by monitoring and optimizing power consumption.
Remotely monitor and control equipment with real-time data to predict issues, boost efficiency, and reduce downtime.
Easily share and collaborate on documents, creating a single source of truth for engineers and contractors.
Manage and analyze assets across their lifecycle to schedule maintenance, reduce downtime, and extend lifespan.
Improve visibility, automate work orders, and ensure compliance for efficient facility and asset management.
Resources
Browse our full library of resources all in one place, including webinars, whitepapers, podcast episodes, and more.
Support
Looking for access to technical support, best practices, helpful videos, or training tools? You’ve come to the right place.
About Accruent
Get the latest information on Accruent, our solutions, events, and the company at large.
Learn the basics of preventive maintenance concepts, as well as how to implement preventive maintenance processes.
Table of contents
Preventive maintenance (PM) is the routine maintenance of assets and equipment to reduce equipment failure, maximize uptime and optimize long-term asset management. Effective facility and asset management today requires great preventive maintenance. But what are the details of preventive maintenance, what are its benefits, and how can organizations effectively execute preventive maintenance strategies? This comprehensive guide to PM concepts and tools will cover everything you need to know.
Preventive maintenance is routine, systematic, and planned asset and facilities maintenance that is performed to reduce equipment failure, cut costs and maximize efficiency over time.
When it comes to the broader range of maintenance practices, preventive maintenance falls in complexity between reactive maintenance (whereby organizations perform maintenance after an asset has failed) and predictive maintenance, whereby maintenance needs are fully predicted and automated using artificial intelligence (AI) and the Industrial Internet of Things (IIoT).
While it’s more forward-thinking than reactive maintenance, preventive maintenance can’t magically predict problems before they happen. Instead, it uses data to develop effective maintenance schedules and correct issues before they become equipment failures. In this way, PM can slow down failures, depreciation and rate of malfunction over time.
To get it right, preventive maintenance efforts must include:
The right software can help organizations automate, access and organize their PM tasks, which is particularly important for organizations with many assets or complex maintenance schedules.
While preventive maintenance practices dictate that users must address maintenance concerns before they become issues, reactive or corrective maintenance strategy encourage users to wait until the problem or malfunction is already there before action is taken. This is also known as the “run-to-failure” method, and it comes with significant drawbacks like:
In the modern maintenance world, these reactive/corrective/run-to-failure strategies just don’t cut it, and organizations that deploy reactive maintenance practices will find it difficult to remain competitive in their industry.
Predictive maintenance (PdM), on the other hand, is essentially advanced preventive maintenance powered by AI, the IIoT and other smart manufacturing tools. More specifically, predictive maintenance utilizes equipment readers, historical data and industry data to automate and predict maintenance needs. When compared directly to preventive maintenance, PdM is:
Overall, though, predictive strategies can reduce the number of necessary planned tasks and maximize efficiency – and the more data you have, the more effective your PdM efforts will be. Many modern organizations are moving ever closer toward a predictive environment, though it’s complex, expensive, time-consuming and extremely difficult to achieve.
There are many benefits to effective preventive maintenance, particularly related to ROI, safety and efficiency. Namely, preventive maintenance can lead to:
Preventive maintenance may not always be the most necessary or appropriate approach, but it is suitable to use preventive maintenance when asset have:
Conversely, preventive maintenance may not be suitable for assets that:
There are a few disadvantages – or, more accurately, challenges – associated with preventive maintenance, including:
Effective preventive maintenance requires the right program or strategy, which will help determine maintenance tasks and frequency. Getting this right is important. If you maintain assets too infrequently, you risk breakdowns. Maintain them too frequently, and it will cost you too much time and money. Perform the wrong maintenance on an asset, and you miss the point altogether. The strategy, then, is all-important. Following the PDCA Model can help you get preventive maintenance right.
The PDCA model is as follows:
This, of course, can be simplified using the right CMMS software for your business, which can help you organize work orders, trigger maintenance requests, keep technicians accountable and update maintenance plans for critical equipment.
Preventive maintenance can be divided into many categories and organization types, including:
The type of maintenance trigger you set will vary based on the asset, manufacturer recommendations and other key data. You can also prioritize preventive maintenance based on task importance and prioritization. This includes:
The "10% Rule" in preventive maintenance is a guideline that recommends performing maintenance on equipment when the cost of maintenance or repairs is less than 10% of the equipment's replacement cost. In essence, if the cost to fix or maintain the equipment falls below this 10% threshold, it is typically considered cost-effective to proceed with maintenance. However, if the repair costs exceed 10% of the replacement cost, it may be more economical to replace the equipment altogether.
This rule serves as a practical decision-making tool for organizations to determine whether to invest in maintaining aging equipment or to allocate resources towards purchasing new, more efficient machinery. It helps strike a balance between extending the life of equipment through preventive maintenance and avoiding unnecessary expenses when equipment becomes too costly to maintain.
It's essential to note that the 10% Rule is a general guideline, and actual decisions may involve more complex factors, such as equipment criticality, safety considerations, operational requirements, and the organization's financial situation. Nevertheless, it provides a useful starting point for evaluating the cost-effectiveness of maintenance actions, aiming to optimize asset management and minimize downtime.
Examples of preventive maintenance tasks include:
You can create a preventive maintenance checklist to ensure that your workflow runs smoothly and that you have a clear roadmap outlining how and when to maintain your assets. There are many approaches to making this checklist – and no one-size-fits-all approach – but here are some general steps to getting started.
Maintenance management software can help organizations in many asset-heavy industries streamline their asset management, maximize productivity and ultimately increase uptime and ROI. This includes:
Preventive maintenance software, as we’ve mentioned, is a tool that helps users execute preventive maintenance and effectively maintain, analyze and manage their physical assets and infrastructure. Whether your preventive maintenance software classifies itself as a CMMS or an EAM doesn’t matter too much these days (there is a lot of overlap between the two, which you can read more about here).
What does matter is that your software includes key features like:
You can learn more about each feature and its importance here. That said, these features will generally help you reap the benefits of your preventive maintenance software, which include:
Just make sure that you choose the right CMMS software for your business. In general, this will be a system that your team is on board with (since adoption is the key to successful implementation), that integrates with your existing technological ecosystem and that is user-friendly and intuitive. You can learn more about how to choose the right system for your business here.
Bottom line? Preventive maintenance is routine, systematic and planned asset and facilities maintenance that is performed to reduce equipment failure, cut costs and maximize efficiency over time – and effective preventive maintenance is key to asset and facility management.
Start by identifying and categorizing all critical assets based on usage, age, and function. Define clear maintenance goals—such as reducing downtime or extending equipment life—and develop a schedule based on manufacturer recommendations or usage data. Use a CMMS or similar tool to assign tasks, track work history, and monitor performance. Finally, review data regularly to improve and refine your program over time.
Proper Equipment Installation: Ensuring equipment is installed correctly to prevent future issues.
Regular Inspections: Conducting routine checks to identify signs of wear, damage, or potential problems.
Routine Testing: Performing tests to assess equipment performance and detect hidden issues.
Scheduled Servicing: Carrying out regular maintenance tasks like cleaning, lubrication, and part replacements.
Calibration: Ensuring measuring instruments are accurate to maintain product quality and safety.
The frequency depends on several factors, including manufacturer guidelines, asset criticality, operating conditions, and usage intensity. Some equipment may require weekly checks, while others might only need quarterly or annual servicing. Reviewing equipment data regularly helps fine-tune the right intervals.
What maintenance strategy -- or combination of strategies -- will work most effectively for your organization? Here are the key differences and ...
Learn how a successful CMMS implementation can help you overcome reactive maintenance inefficiencies and maximize your overall return on investment ...
Explore effective facility management tips for the beverage industry with Accruent. Learn to reduce asset downtime and enhance operational efficiency.
Subscribe to stay up to date with our latest news, resources and best practices