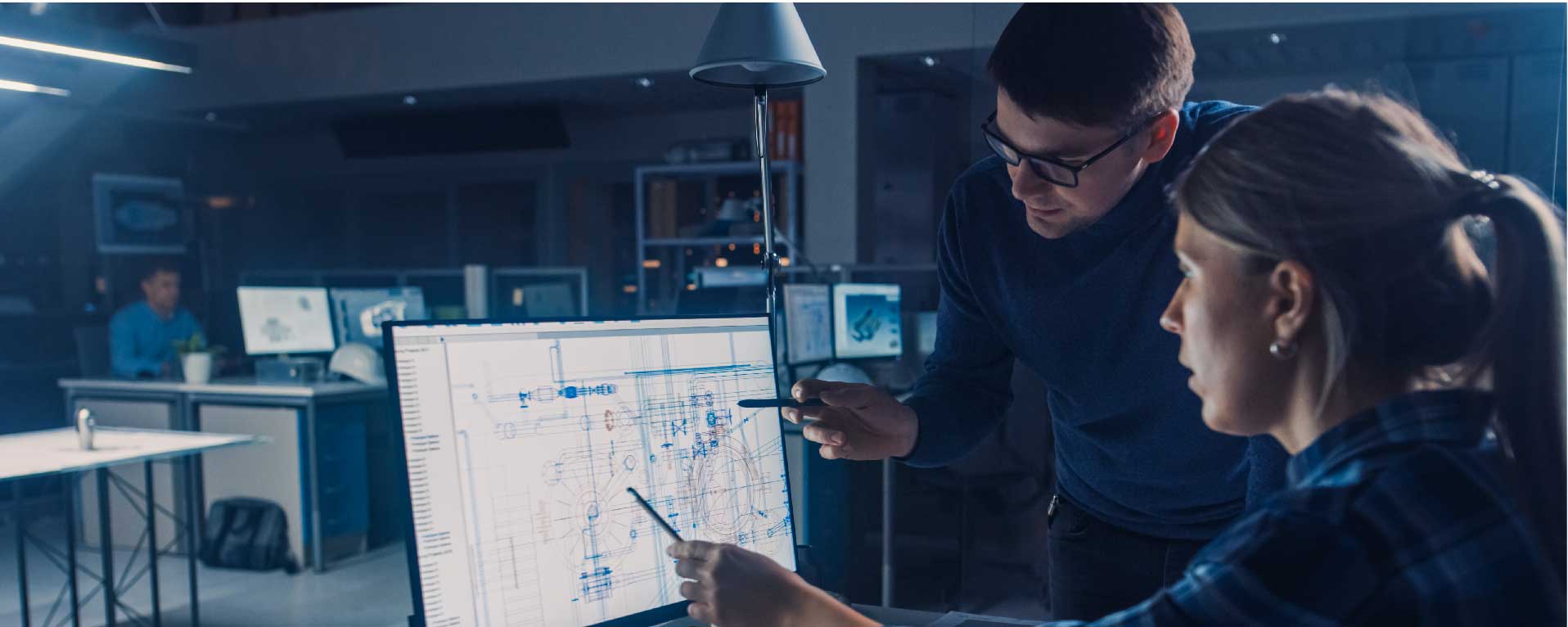
A Comprehensive CMMS Work Order Management System
Here's everything you should look for in a comprehensive CMMS work order management system.
Solutions
Workplace Management Solutions
Real Estate Management Solutions
Maintenance Management Solutions
Energy Management Solutions
Engineering Document Management Solutions
Asset Management Solutions
Automate campus scheduling for classes, meetings, and exams with our EMS software.
Plan and manage conferences effortlessly with EMS software to impress guests and streamline operations.
Boost workplace flexibility and maximize space use with seamless desk and room booking.
Organize workplace or campus events smoothly, creating memorable experiences.
Optimize workspace, manage allocations efficiently, and reduce costs with our space management solutions.
Deliver projects on time and within budget by improving communication, collaboration, and efficiency with our software.
Streamline lease accounting for ASC 842, IFRS, and GASB compliance.
Manage leases efficiently by tracking key dates, analyzing costs, and ensuring compliance.
Centralize data and analytics for better insights, faster negotiations, and revenue growth.
Centralize facility and asset maintenance, automate work orders, and ensure compliance with our CMMS software.
Extend asset life, reduce downtime, and prevent costly repairs with data-driven monitoring.
Prevent equipment failures and extend asset life by detecting and addressing issues early.
Make sustainable, cost-efficient energy decisions by monitoring and optimizing power consumption.
Remotely monitor and control equipment with real-time data to predict issues, boost efficiency, and reduce downtime.
Easily share and collaborate on documents, creating a single source of truth for engineers and contractors.
Manage and analyze assets across their lifecycle to schedule maintenance, reduce downtime, and extend lifespan.
Improve visibility, automate work orders, and ensure compliance for efficient facility and asset management.
Resources
Browse our full library of resources all in one place, including webinars, whitepapers, podcast episodes, and more.
Support
Looking for access to technical support, best practices, helpful videos, or training tools? You’ve come to the right place.
About Accruent
Get the latest information on Accruent, our solutions, events, and the company at large.
Learn the basics of work orders, the elements of a maintenance work order, and how to optimize the process throughout the work order life cycle.
A work order is a formal digital or paper request made to replace, restore or repair a particular asset. Typically, each work order is assigned to a particular technician, and it can be generated as part of scheduled maintenance, in response to an emergency, or in response to an audit or inspection.
Today, this work order definition has changed slightly, as work order requests are becoming digitized in computerized maintenance management systems or enterprise asset management (EAM) systems. This can help ensure that the work order is seen and completed in a timely manner. It can also help users be sure to include all important details. That said, the fundamental work order meaning remains unchanged.
A work order’s purpose is to provide clear information about work that is supposed to be performed, along with the data needed to execute, monitor and update that work. Ultimately, a work order can help organizations maintain uptime and streamline operations and maintenance in any business that has assets.
When considering how to make a work order, it’s important to keep in mind that work orders are used to:
With an effective work order software, organizations can maximize uptime, control labor costs, remain compliant and make incremental improvements to their operations.
There are many types of work orders or work order categories, including:
1. Inspection: These work orders are especially important in highly regulated industries, as they help verify the functionality and the performance of key assets, asset components and business systems.
2. Maintenance work orders: Maintenance work orders include any work orders meant to help with corrective, condition-based, preventive or predictive maintenance strategies (more on this in the next section)
3. Electrical: Electrical work orders deal with installation of wiring, electrical repairs and more.
4. Emergency: Emergency work orders are created to address critical and urgent emergencies. They are used to solve immediate problems and protect the life of assets.
5. Special project: Installing a new asset? Looking to increase productivity or efficiency? A special project work order can initiate this task.
6. Safety: Safety work orders help start activities that reduce the risk of harm and injury from falls, chemical spills, COVID risks and more.
Within manufacturing, there are a variety of maintenance and repair work orders that can be created to maximize uptime and streamline maintenance tasks. These maintenance work order types include:
1. Corrective maintenance: This type of maintenance is carried out when an anomaly or flaw is detected. The goal of this maintenance practice is to fix the flaw and maintain uptime. Corrective maintenance tasks may be more cost-effective than preventive maintenance in the short-term, but its short-sighted nature makes it an ineffective long-term strategy.
2. Preventive maintenance: Preventive maintenance strategy involves scheduled, forward-thinking maintenance based on key metrics and data points. An effective preventive maintenance strategy can ultimately increase asset life, maximize revenue and decrease equipment downtime.
3. Condition-based maintenance: Condition-based maintenance aims to prevent failure through regular asset-checkups and performance monitoring. In other words, equipment is constantly assessed and maintained, which requires significantly more coordination and manpower than other strategies.
4. Predictive maintenance: Predictive maintenance, as the name suggests, aims to preemptively predict asset failures before they arise using data, sensors and IoT technology. Because it relies so intrinsically on data and technology, predictive maintenance comes with a higher up-front cost, and it is not yet feasible for many organizations.
A maintenance work order is a formal request for maintenance or repair tasks, ensuring that facilities and equipment are running efficiently and safely. These work orders are critical for managing resources, tracking progress, and maintaining a history of completed tasks. They streamline the process of organizing, prioritizing, and assigning responsibilities within the maintenance team.
A maintenance work order is any form that helps initiate a repair or replace task. There are many types of maintenance work order forms and service orders that can help with each type of maintenance, though the term “service order” generally refers to work completed for external entities, while a “work order” is more frequently in-house or internal. The types of work orders include:
1. Standard: A standard work order is generally issued for non-critical, routine maintenance tasks. For example, setting up a new piece of equipment or hauling away an old asset would fall under the standard work order category.
2. Preventive maintenance: Preventive maintenance work orders are forward-thinking work orders that focus on scheduled tasks and repairs. The goal with preventive work orders is to address maintenance needs before they become larger concerns, thereby extending asset life, reducing equipment downtime and decreasing expensive repairs over time.
3. Reactive: A reactive work order, on the other hand, is generated when there is a breakdown or an emergency with a piece of equipment. The issue needs to be addressed ASAP when a reactive work order is issued.
4. Corrective maintenance: A corrective maintenance work order aims to resolve flaws or asset issues that are not emergencies by nature.
5. Prepare for inspections: A prepare for inspections work order is a work order that uses predetermined inspection parameters to help ensure that assets – and your facility as a whole – remain compliant with inspections.
This comprehensive pricing calculator is designed to provide you with a clear, customized cost breakdown for Accruent's maintenance management software to help you streamline your work order management.
The work order process flow is the entire stream of steps in which maintenance is requested, completed and documented. There are six primary steps to the work request process:
1. Task identification: This can be noticed reactively (I.e. you see a noticeable malfunction) or proactively using time-based or usage-based triggers.
2. Creation of work order: Using a CMMS like Maintenance Connection, the entire work order request process can be completed through a centralized, easy-to-use interface.
3. Approval of work order: This step is generally completed by a maintenance manager. This is also when any special parts or equipment are ordered.
4. Assignment of work order: When considering how to prioritize maintenance work orders and assign them, you can do so based on factors like urgency, team workload, overall impact of the issue and individual technician skillset
5. Work order close: Information included here includes time spent performing maintenance, any associated costs and images.
6. Review of work order: This can be done immediately upon completion and periodically as part of a more comprehensive preventive maintenance schedule.
To streamline this flow and make sure the task is completed correctly, you must be thorough about how to complete your work order. Any maintenance work order forms should include key work order details like:
This information will help schedule resources, establish costs for repairs and labor, provide instructions and explain the work order’s purpose.
Similarly, a formalized work order approval process will proactively catch and prevent any work order submission issues.
Here are examples of a maintenance work order that show you how to complete a work order within the Maintenance Connection CMMS system and MC Express mobile app:
Taking a step back, you encounter work order management more generally – which, as the name suggests, refers to broader work request management. This is the process by which you submit work order requests, manage work requests and more.
And there are many work order management styles still in use today. These include:
1. Pen and paper management: Pen and paper systems rely on printed forms to request, schedule and document work order requests. This method may work for small organizations with few employees and work orders, though this increases the risk of incomplete work orders, duplicate information and less-than-ideal collaboration.
2. Whiteboard management: This is like pen and paper management, though maintenance managers usually organize work order requests on a whiteboard. This can be a great way for managers to see all maintenance tasks at-a-glance. That said, some work orders can fall through the cracks and maintenance managers could lose efficiency and big-picture metrics.
3. Spreadsheet work order management: The next option is to organize work orders via Excel or Google Sheets. Companies that use this strategy often use Google Forms as work order request forms. Though this strategy is digitized (and therefore more readily available than paper or whiteboard options), it can be hard to modify these e work orders, share data or gather all relevant information.
4. CMMS software: Computerized maintenance management system software is the most comprehensive work order management system. Using a CMMS repair work order software, technicians and managers can create work orders, attach all relevant documentation, update information, gather inventory data and more. Managers also have a clear work order management dashboard, and they can easily access a work order status report whenever necessary.
To facilitate work order management tasks, you can use a web-based work order system like a CMMS software or an enterprise asset management (EAM) system. This kind of cloud-based work order software or on-prem software will streamline work order management and automates key processes. It will also help you execute tasks like:
A CMMS work order system can help you create, view and update your work orders effectively so you can maximize uptime, improve efficiency and streamline maintenance practices in your organization.
Here's everything you should look for in a comprehensive CMMS work order management system.
Understand the basics of work order software and how it can be used to streamline operations, increase efficiency, and facilitate data-driven ...
Discover the secrets to maintenance success with our ultimate guide on work order management. Learn how to streamline processes and boost ...
Subscribe to stay up to date with our latest news, resources and best practices