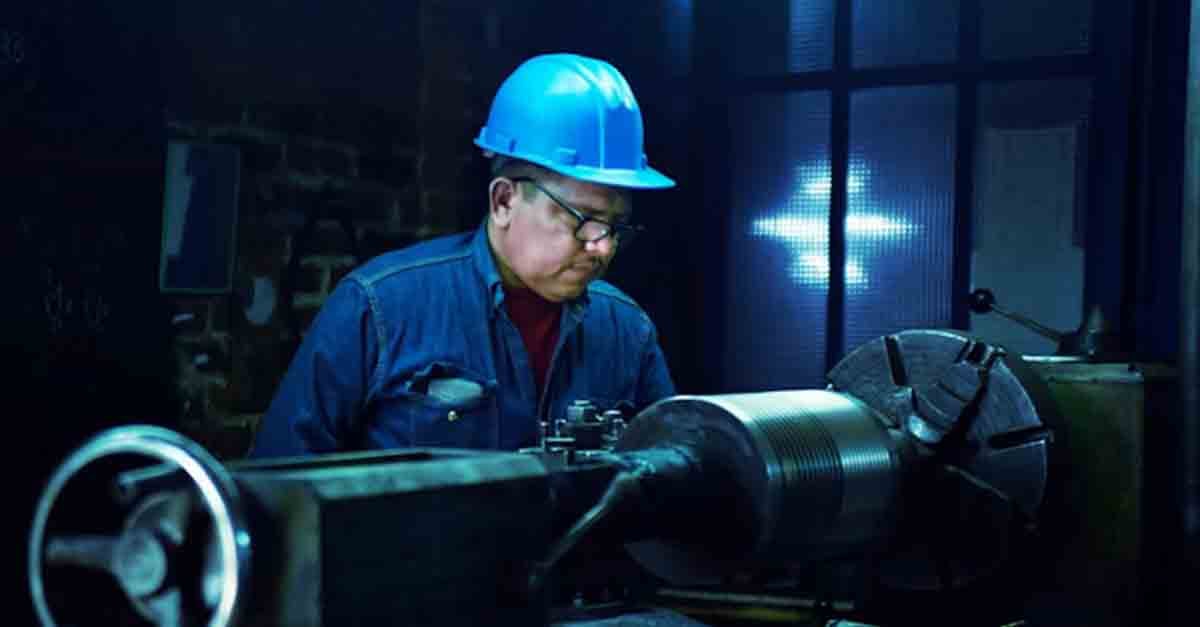
Maintenance Management: 7 Key Strategies for Success
Discover the meaning and secrets to successful maintenance management in 2024. Explore strategies to cut maintenance costs and boost operational ...
Solutions
Workplace Management Solutions
Real Estate Management Solutions
Maintenance Management Solutions
Energy Management Solutions
Engineering Document Management Solutions
Asset Management Solutions
Automate campus scheduling for classes, meetings, and exams with our EMS software.
Plan and manage conferences effortlessly with EMS software to impress guests and streamline operations.
Boost workplace flexibility and maximize space use with seamless desk and room booking.
Organize workplace or campus events smoothly, creating memorable experiences.
Optimize workspace, manage allocations efficiently, and reduce costs with our space management solutions.
Deliver projects on time and within budget by improving communication, collaboration, and efficiency with our software.
Streamline lease accounting for ASC 842, IFRS, and GASB compliance.
Manage leases efficiently by tracking key dates, analyzing costs, and ensuring compliance.
Centralize data and analytics for better insights, faster negotiations, and revenue growth.
Centralize facility and asset maintenance, automate work orders, and ensure compliance with our CMMS software.
Extend asset life, reduce downtime, and prevent costly repairs with data-driven monitoring.
Prevent equipment failures and extend asset life by detecting and addressing issues early.
Make sustainable, cost-efficient energy decisions by monitoring and optimizing power consumption.
Remotely monitor and control equipment with real-time data to predict issues, boost efficiency, and reduce downtime.
Easily share and collaborate on documents, creating a single source of truth for engineers and contractors.
Manage and analyze assets across their lifecycle to schedule maintenance, reduce downtime, and extend lifespan.
Improve visibility, automate work orders, and ensure compliance for efficient facility and asset management.
Resources
Browse our full library of resources all in one place, including webinars, whitepapers, podcast episodes, and more.
Support
Looking for access to technical support, best practices, helpful videos, or training tools? You’ve come to the right place.
About Accruent
Get the latest information on Accruent, our solutions, events, and the company at large.
Learn how effective work order management can streamline maintenance processes and boost productivity. Discover key strategies and software to achieve maintenance success.
Table of contents
The best manufacturing companies are built on effective work order management. The system builds an infrastructure where every task is identified, scheduled, executed, and reviewed – all done with precision. But what does that look like in practice?
This guide dives into the basics of work order management. It focuses on how a strategic approach can streamline workflows, cut costs, and boost productivity. With the right system in place, companies find a competitive advantage.
Work order management (WOM) is a systematic approach to organizing and controlling every aspect of maintenance tasks – from initiation to completion. It includes defining the work scope, scheduling, assigning tasks, executing work, and recording outcomes.
WOM prioritizes tasks, optimizes resources, and executes maintenance activities. Streamlining these processes minimizes downtime, extends asset life, and helps companies maintain compliance with safety and industry standards. Implementing it significantly boosts productivity across all sectors of an organization.
The work order management process is a comprehensive cycle that handles tasks from inception to analysis. The structured approach maintains operational integrity while maximizing asset performance. Here is what each stage looks like.
The initial step is to recognize the need for maintenance or repair. This comes from routine inspections, automated alerts, or staff reports. Once identified, the specific details of the task – including its nature, location, and the resources required – are outlined. Assigning priority and due dates to these tasks means urgent issues get addressed without resource waste.
The next phase schedules work and allocates appropriate personnel and resources. This step requires a thorough understanding of each task’s requirements and the availability of resources. Then, that information determines realistic completion timelines and, when necessary, whether other departments or teams need to be coordinated.
Once scheduled, tasks are dispatched to the assigned technicians or teams. Clear communication is important. Provide all the necessary tools, parts, and information to execute the task. Confirm the schedule and availability of the resources to streamline the process.
Now this is where the maintenance or repair work is physically carried out. It requires strict adherence to safety and quality standards to prevent accidents and ensure the work is done correctly. Document the process in detail, including any challenges encountered or changes made.
Upon completion, the work is thoroughly inspected to verify that it meets the required standards and fully addresses the issue. The work order status is then updated to close, and feedback is gathered from both technicians and stakeholders. This feedback loop helps identify any areas that may require further attention.
The final stage is a comprehensive review of the process. This is where analysis happens to determine effectiveness. Evaluate how well tasks were identified, scheduled, and executed.
Was the desired outcome achieved? Use this to identify areas for improvement or optimization for future maintenance strategies. This post-mortem stage helps organizations uncover insights that drive better decision-making.
Download your free Work Order Template to streamline maintenance requests, improve task tracking, and keep your operations running smoothly.
The future will be built on automation, and the statistics back it up. For instance, businesses that utilize work order management software experience a 20% reduction in equipment downtime and material costs. That is just one of the many benefits of effective work order management.
At its core, effective work order management simplifies complex maintenance workflows. By centralizing task tracking and management, it creates a unified platform where all maintenance activities are visible and manageable from a single point of control. This centralization automates maintenance scheduling and dispatching. That not only reduces manual coordination but improves communication between teams.
A tangible benefit is the impact on costs. Efficient resource allocation prevents over-expenditure while a proactive maintenance approach will lower the expenses associated with emergency repairs. By minimizing waste through improved planning and execution, organizations achieve a leaner, more cost-effective operation.
Work order management helps maintain comprehensive records of all activities. Detailed documentation allows for easy retrieval and analysis of historical data. This means teams can easily learn from past experiences. It also ensures compliance with regulatory standards by providing evidence of adherence to protocols and safety measures.
Informed decisions are the best decisions. With work order management, organizations have access to actionable insights to drive data-driven decisions. The system highlights trends and patterns to encourage proactive planning. This information supports informed strategies built towards future improvements and optimizations. It is about solid data – not guesswork.
To achieve the benefits of WOM, leaders must set their organizations up for success. Here are some useful strategies to get the most value out of these systems.
A well-organized work order system starts with prioritization. By establishing a clear system based on urgency and importance, teams tackle the most important tasks. Categorizing work orders means efficient resource allocation. It is vital to regularly review and adjust these priorities to reflect changing demands and ensure continuous improvement in processes.
Standard operating procedures (SOPs) are the backbone of consistent work order execution. Developing and enforcing these guidelines ensures that every task is performed to a set standard. It promotes uniformity and quality across all maintenance activities. Train staff in these procedures to ensure uniformity and quality. Regularly update the SOPs with learnings and feedback to foster an environment of continuous improvement.
Continuously monitor operations to elevate overall operations. Setting key performance indicators (KPIs) provides a measurable way to track the system’s efficiency and effectiveness. Conduct regular audits and reviews to identify areas that require attention or improvement. Use feedback and data analysis to refine strategies and find areas of improvement.
Work order software will significantly improve workflows. These solutions automate scheduling, tracking, and reporting. They drastically reduce manual effort while minimizing errors. With features such as real-time updates and communication, the software ensures that everyone involved is informed and aligned. It makes it much easier to manage tasks and respond to issues.
Accruent’s Maintenance Connection is a leading Computerized Maintenance Management System (CMMS). It is a comprehensive platform designed to streamline maintenance operations, boost efficiency, and cut costs. The software excels in managing work orders from start to finish.
Key features of Maintenance Connection include the following:
With these features, the CMMS software enhances overall work order efficiency. It simplifies workflows, automates tasks, and minimizes errors. Overall, it is a valuable strategic tool for elevating maintenance operations.
Automation is perfect for handling routine tasks, allowing your team to focus on what they do best: Innovate, create, and solve complex problems."— Forbes Business Council
There’s true transformative power for businesses that utilize Accruent’s Maintenance Connection. Experience firsthand how this CMMS can streamline operations, enhance efficiency, and reduce costs. Do not miss elevating your maintenance strategy – request a demo or reach out to the Accruent sales team today
The five main functions of a work order include identifying maintenance tasks, scheduling and allocating resources, dispatching tasks to personnel, executing and documenting the work, and verifying and closing the task upon completion. These steps ensure efficient and effective maintenance workflows.
A work order management system is a digital tool designed to streamline the creation, assignment, tracking, and completion of maintenance tasks. It automates processes, enhances communication, and provides a centralized platform for managing maintenance operations. This ensures tasks are completed efficiently and effectively.
Organizing work orders involves prioritizing tasks based on urgency, categorizing them for easy tracking, and then assigning them to the appropriate personnel. Utilizing a work order management system can automate these steps. It ensures resources are allocated in a way that makes sense and tasks are scheduled logically. This minimizes downtime and disruptions.
Discover the meaning and secrets to successful maintenance management in 2024. Explore strategies to cut maintenance costs and boost operational ...
Discover the power of Enterprise Asset Management (EAM) in optimizing maintenance processes, enhancing efficiency, and reducing downtime. Learn more ...
Explore key factors to find the best CMMS software for manufacturing and elevate your facility's maintenance efficiency and productivity to the next ...
Subscribe to stay up to date with our latest news, resources and best practices