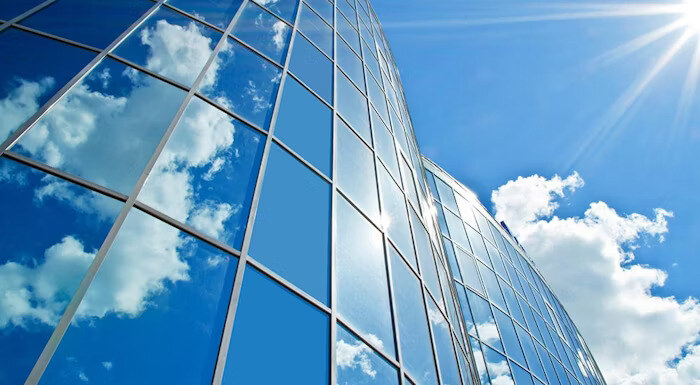
How an Enterprise CMMS can Help you Manage Multiple Locations for Enterprise-Wide Visibility
Explore how enterprise CMMS can help you increase visibility and manage multiple locations for your organization.
Solutions
Workplace Management Solutions
Real Estate Management Solutions
Maintenance Management Solutions
Energy Management Solutions
Engineering Document Management Solutions
Asset Management Solutions
Automate campus scheduling for classes, meetings, and exams with our EMS software.
Plan and manage conferences effortlessly with EMS software to impress guests and streamline operations.
Boost workplace flexibility and maximize space use with seamless desk and room booking.
Organize workplace or campus events smoothly, creating memorable experiences.
Optimize workspace, manage allocations efficiently, and reduce costs with our space management solutions.
Deliver projects on time and within budget by improving communication, collaboration, and efficiency with our software.
Streamline lease accounting for ASC 842, IFRS, and GASB compliance.
Manage leases efficiently by tracking key dates, analyzing costs, and ensuring compliance.
Centralize data and analytics for better insights, faster negotiations, and revenue growth.
Centralize facility and asset maintenance, automate work orders, and ensure compliance with our CMMS software.
Extend asset life, reduce downtime, and prevent costly repairs with data-driven monitoring.
Prevent equipment failures and extend asset life by detecting and addressing issues early.
Make sustainable, cost-efficient energy decisions by monitoring and optimizing power consumption.
Remotely monitor and control equipment with real-time data to predict issues, boost efficiency, and reduce downtime.
Easily share and collaborate on documents, creating a single source of truth for engineers and contractors.
Manage and analyze assets across their lifecycle to schedule maintenance, reduce downtime, and extend lifespan.
Improve visibility, automate work orders, and ensure compliance for efficient facility and asset management.
Resources
Browse our full library of resources all in one place, including webinars, whitepapers, podcast episodes, and more.
Support
Looking for access to technical support, best practices, helpful videos, or training tools? You’ve come to the right place.
About Accruent
Get the latest information on Accruent, our solutions, events, and the company at large.
A multi-site, multi-device CMMS can help your company grow and scale with ease. Learn about other key benefits here.
Growth is something every company desires to add to their portfolio description but with growth comes many hurdles to successfully maneuver. For managers, growth can mean new locations, new assets, new budgets and new employees. An enterprise maintenance management software can handle growth and change with ease and excellence.
With an enterprise CMMS, management and staff can stay connected, ramp up new facilities with ease, and manage analytics to prepare for future operations. So what is an enterprise maintenance management system in comparison to a basic CMMS? According to Better Buys, it is a more robust version of a CMMS. An enterprise CMMS is a long-term, expandable, comprehensive solution that includes all the CMMS functions… however, is able to work with larger sets of users from multiple sites. The system is also able to monitor all aspects of a maintenance strategy, from notification to follow-up… This is why companies who have multiple-sites benefit from an enterprise CMMS solution, like Maintenance Connection.
Managing one location is an easy task but managing several locations is a large accomplishment. Maintenance Connection provides companies with the ability to monitor the performance of assets across multiple locations within one application. Notifications and dashboards can also be established to aid in real-time notifications of items like downtime, abnormal readings, and repair status. With cloud-hosted, browser ability, performance is seen in real time data feeds. Performance management can become as easy as checking the internet for the daily news.
Growth initiates new equipment, new parts, new labor and new maintenance. Maintenance Connection has made these tasks streamlined and easy to reproduce. For example, organizations who take time to organize and set up their first facility’s assets into a logical and well-organized asset tree can quickly use the asset tree as the framework for new sites in the future. Procedures currently in place at one location can easily be cloned and applied to new locations. Parts can be added to new warehouses with just the click of a button. Adding new labor to locations and assigning employee attributes can be done in minutes with predefined fields and options provided by the software. Another great feature Maintenance Connection offers that is especially beneficial to its enterprise customers is the ability to transfer work, assets, and attributes from one employee to another employee with ease.
The ability to see how several locations are performing is a requirement of any company with multiple locations. Maintenance Connection offers not only this visibility but also a global search feature which makes finding any information simple so analysis can be done quickly and maintenance records can be found. Not only can you see the performance of all your locations but, with MC, a company can also see metrics, amounts, and supplies. A great benefit our customers have seen from using Maintenance Connection is the ability to easily standardize each new site, visibility of all locations and realize what true ease of use means, said Paul Klein, a MC enterprise implementation specialist who hears enterprise user’s perspectives in his day-to-day work.
The top-notch visibility that an enterprise solution offers into an organization’s performance goes well beyond the ability to locate maintenance records. Maintenance Connection offers a robust, enterprise reporting module which allows management to see budgets, downtime, costs of operations, part needs, and much more. With customizable reports, automated messaging and global data tracking, information for each location are at the touch of your fingers within minutes. Not only does this type of visibility cut costs and lower maintenance needs, it also allows for detailed planning and maintenance forecasting. Another great benefit of visibility is the health, safety, and compliance of the company. Visibility provides needed documentation of industry compliance and ensures the safety of employees.
When operations become streamline and maintenance needs are planned, costs will begin to decrease. Efficiency and planning equals company budget savings. With Maintenance Connection’s detailed reporting capabilities, maintenance costs can be analyzed to save labor time and even eliminate duplicate repairs. With the robust MC inventory module, seeing inventory needs across locations allows for bulk part ordering, part tracking, and efficient use, or in some cases, return of overstocked parts. Management can also see real-time work being performed to make better use of an employee’s time to avoid overstaffing. Operating costs decrease with better asset performance and resource usage. For example, assets requiring excessive repair or overuse of resources can now be clearly seen and mitigated with more efficient equipment. According to a recent study, 88% of facilities with an enterprise CMMS implementation have significant cost savings, from tens of thousands to millions of dollars. This insight proves that enterprise CMMS provides an ROI, improved decision-making, and facility assets, processes and labor alignment. An enterprise CMMS like Maintenance Connection can save a company thousands of dollars on their maintenance costs. This means funds can be placed back into an organization’s budget, to meet other company goals like financing new capital projects.
Streamlining company operations is a great benefit of an enterprise CMMS. Most companies have other software applications that would greatly benefit from integrating with the CMMS. Maintenance Connections offers many years of experience of successful third-party software integrations for our customers. Some of the most common integrations Maintenance Connection partners with are with financial software, gas reading software, and ERP software. Once an integration is successfully done at one site, then a company can easily expand to multiple locations. The integration model already set up can carry over as a blueprint to follow for future sites and growth.
Maintenance Connection continues to lead the enterprise CMMS industry. It is not just an asset management software but a full-bodied, enterprise maintenance management suite. From asset management, PMs, work orders, purchase orders, labor management and more, Maintenance Connection has included every aspect needed to have an excellent maintenance management solution that has consistently achieved acclaimed reviews by maintenance management and technicians who are end users. Maintenance Connection understands more than just their customer’s needs, but the detailed needs of the industries they serve. From the start, Maintenance Connection provides a personalized approach and staff industry specialist to determine company goals, best practices, and the project plan. Maintenance Connection also brings their award-winning software and customer service team to aid in a one-of-a-kind successful implementation. Once a customer is on board, Maintenance Connection follows them along each step of the way to ensure their maintenance management implementation is a success! From an extensive online training portal to on-site visits and a hands-on yearly customer user group events, Maintenance Connection goes above and beyond to see customers succeed.
Just listen to what a few of our customers have said about Maintenance Connection.
We use Maintenance Connection within our daily operation of a Public Works Facility. We use the software for maintaining all of our 30,000 assets. It is a very powerful tool for processing work orders, as well as managing assets and inventory.”
- Bobby, CH2M Hill
With this program you can see all levels of the maintenance operation which includes, maintenance history, WO status, work history, asset history, purchasing and all other aspects of maintenance.”
- Kevin, Pentair Water
Also, see how successful our customers have been since implementing MC from well know companies like L’Oreal and The New York Times. Maintenance Connection can take a company to the top of the maintenance program and usher in improvements to operations that will bring great cost savings and visibility. The benefits from using a CMMS software are limitless for your company. So how do your CMMS and skills measure up? Get your CMMS Score today with our cost-savings calculator.
Explore how enterprise CMMS can help you increase visibility and manage multiple locations for your organization.
A localized, multi-language CMMS can help you increase transparency, avoid mistakes, and utilize data across sites and departments. Learn more.
In this article, we will explore why CMMS and IoT integration has become pivotal for multi-site retail food refrigeration companies.
Subscribe to stay up to date with our latest news, resources and best practices