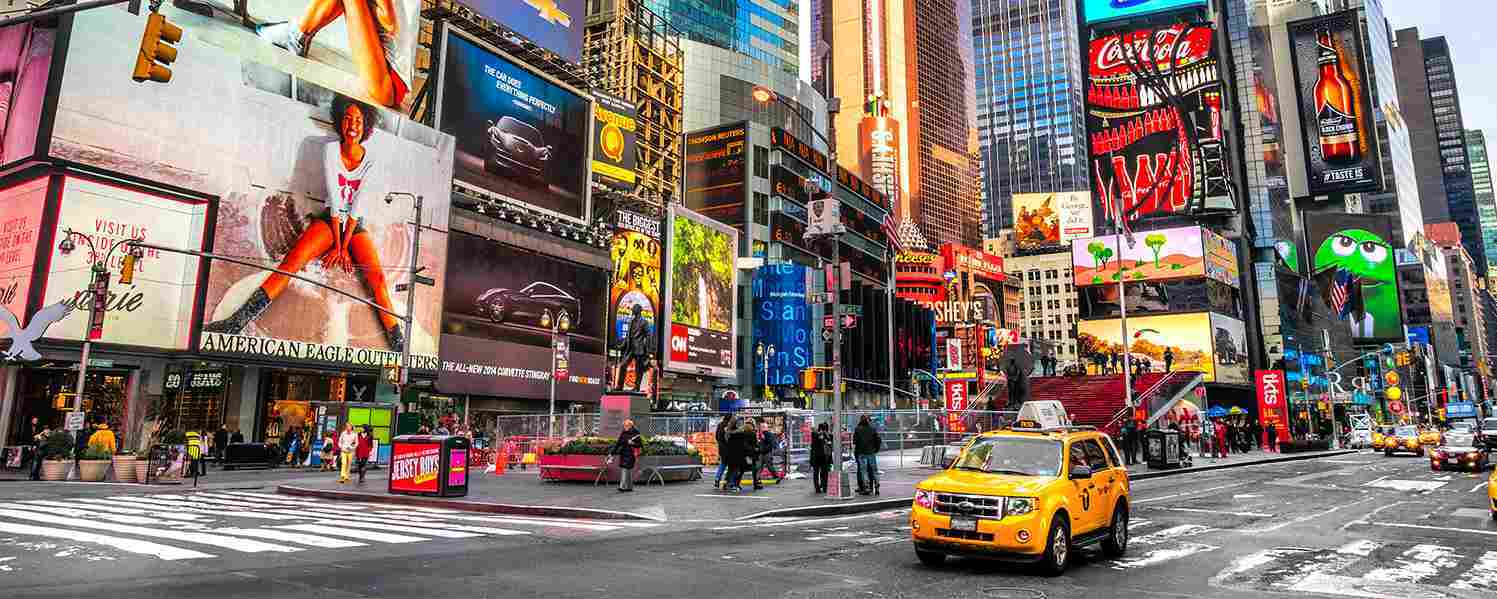
How The New York Times Improved Asset Organization and Performance Reporting with CMMS
Learn how Maintenance Connection helped The New York Times automate reports, allocate resources, and improve labor productivity.
Solutions
Workplace Management Solutions
Real Estate Management Solutions
Maintenance Management Solutions
Energy Management Solutions
Engineering Document Management Solutions
Asset Management Solutions
Automate campus scheduling for classes, meetings, and exams with our EMS software.
Plan and manage conferences effortlessly with EMS software to impress guests and streamline operations.
Boost workplace flexibility and maximize space use with seamless desk and room booking.
Organize workplace or campus events smoothly, creating memorable experiences.
Optimize workspace, manage allocations efficiently, and reduce costs with our space management solutions.
Deliver projects on time and within budget by improving communication, collaboration, and efficiency with our software.
Streamline lease accounting for ASC 842, IFRS, and GASB compliance.
Manage leases efficiently by tracking key dates, analyzing costs, and ensuring compliance.
Centralize data and analytics for better insights, faster negotiations, and revenue growth.
Centralize facility and asset maintenance, automate work orders, and ensure compliance with our CMMS software.
Extend asset life, reduce downtime, and prevent costly repairs with data-driven monitoring.
Prevent equipment failures and extend asset life by detecting and addressing issues early.
Make sustainable, cost-efficient energy decisions by monitoring and optimizing power consumption.
Remotely monitor and control equipment with real-time data to predict issues, boost efficiency, and reduce downtime.
Easily share and collaborate on documents, creating a single source of truth for engineers and contractors.
Manage and analyze assets across their lifecycle to schedule maintenance, reduce downtime, and extend lifespan.
Improve visibility, automate work orders, and ensure compliance for efficient facility and asset management.
Resources
Browse our full library of resources all in one place, including webinars, whitepapers, podcast episodes, and more.
Support
Looking for access to technical support, best practices, helpful videos, or training tools? You’ve come to the right place.
About Accruent
Get the latest information on Accruent, our solutions, events, and the company at large.
Learn how L'Oreal used Maintenance Connection to improve reporting, extend asset life and more throughout their enterprise.
With five major manufacturing facilities and 15 distribution centers in the U.S. alone, L’Oréal has thousands of employees to keep track of – not to mention assets. At a time of high growth, the company recognized its need for better maintenance management.
L’Oréal sought out an easy-to-use solution to help maintain the lifespan of its equipment and track asset health, so they chose Maintenance Connection’s CMMS.
Before implementing a CMMS, L’Oréal didn’t have an easy way to report on performance KPIs, including causes of asset downtime. The global cosmetics manufacturer searched for a strategy that considered both capital and maintenance team performance.
With the help of Maintenance Connection, L’Oréal is able to successfully report on performance KPIs, including causes for asset downtime from anywhere in the field. For example, the team is able to pinpoint how and why downtime is occurring. This makes it easy for L’Oréal to track maintenance-related issues and provide viable solutions through executive reporting.
Since reporting is critical at L’Oréal, the team utilizes Maintenance Connection to quantify performance. The team relies on the CMMS for:
A CMMS provides the L’Oréal team with the ability to produce detailed reports, house all asset information into one place, increase mechanic utilization on the floor and decrease the risk of downtime associated with a breakdown.
Learn how you can diminish downtime and improve team reporting with a CMMS. Download our latest case study to learn more about how L’Oréal improved operations with Maintenance Connection.
Plan your investment with our CMMS pricing guide and ROI calculator.
Learn how Maintenance Connection helped The New York Times automate reports, allocate resources, and improve labor productivity.
Learn how to create automated equipment downtime reports in your CMMS -- and how to use these reports to optimize repairs and minimize downtime ...
Looking to improve your Overall Equipment Effectiveness (OEE)? Here's how Maintenance Connection can help make that happen.
Subscribe to stay up to date with our latest news, resources and best practices