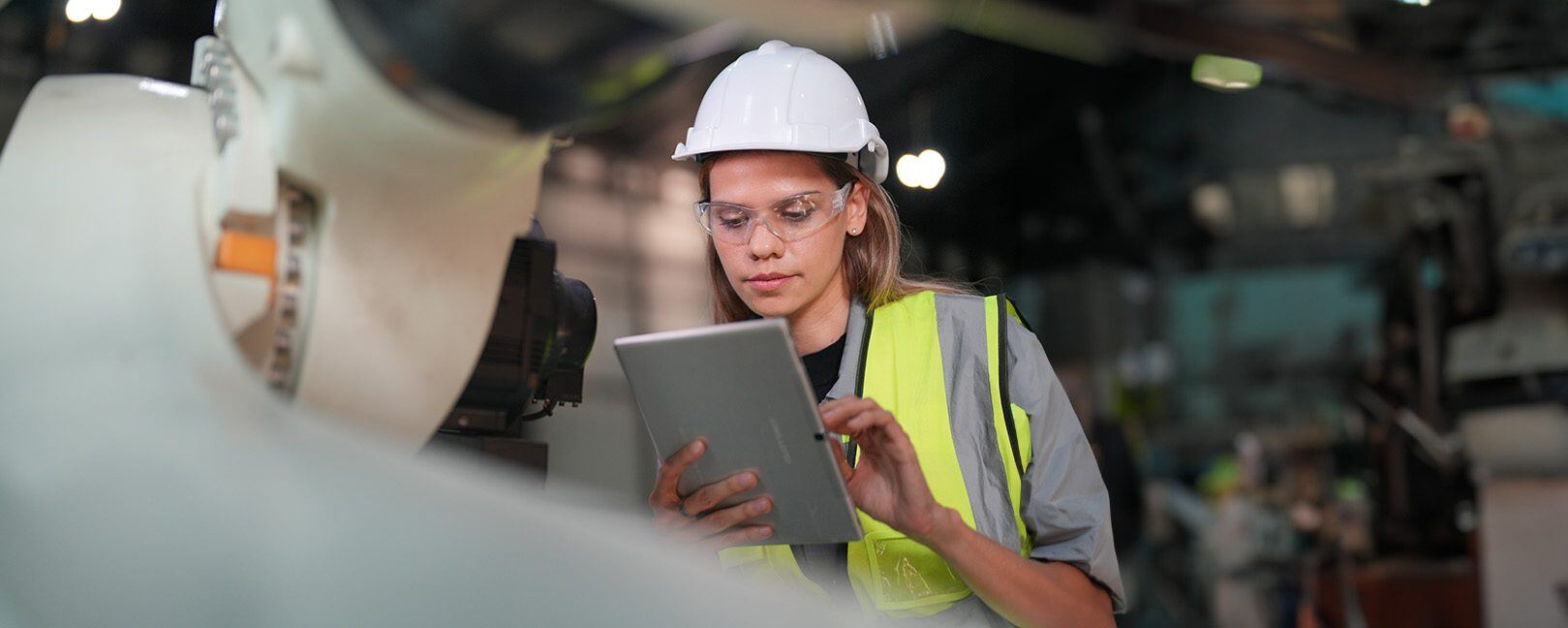
SSAB
Discover how a CMMS helps keep assets fully managed, improve equipment lifespan, increase preventive maintenance, eliminate downtime, and lower costs.
Solutions
Workplace Management Solutions
Real Estate Management Solutions
Maintenance Management Solutions
Energy Management Solutions
Engineering Document Management Solutions
Asset Management Solutions
Automate campus scheduling for classes, meetings, and exams with our EMS software.
Plan and manage conferences effortlessly with EMS software to impress guests and streamline operations.
Boost workplace flexibility and maximize space use with seamless desk and room booking.
Organize workplace or campus events smoothly, creating memorable experiences.
Optimize workspace, manage allocations efficiently, and reduce costs with our space management solutions.
Deliver projects on time and within budget by improving communication, collaboration, and efficiency with our software.
Streamline lease accounting for ASC 842, IFRS, and GASB compliance.
Manage leases efficiently by tracking key dates, analyzing costs, and ensuring compliance.
Centralize data and analytics for better insights, faster negotiations, and revenue growth.
Centralize facility and asset maintenance, automate work orders, and ensure compliance with our CMMS software.
Extend asset life, reduce downtime, and prevent costly repairs with data-driven monitoring.
Prevent equipment failures and extend asset life by detecting and addressing issues early.
Make sustainable, cost-efficient energy decisions by monitoring and optimizing power consumption.
Remotely monitor and control equipment with real-time data to predict issues, boost efficiency, and reduce downtime.
Easily share and collaborate on documents, creating a single source of truth for engineers and contractors.
Manage and analyze assets across their lifecycle to schedule maintenance, reduce downtime, and extend lifespan.
Improve visibility, automate work orders, and ensure compliance for efficient facility and asset management.
Resources
Browse our full library of resources all in one place, including webinars, whitepapers, podcast episodes, and more.
Support
Looking for access to technical support, best practices, helpful videos, or training tools? You’ve come to the right place.
About Accruent
Get the latest information on Accruent, our solutions, events, and the company at large.
Learn how L'Oreal decreased asset downtime, improved reporting and maximized asset life with Maintenance Connection CMMS.
Table of contents
For more than 100 years, L’Oréal has been known as the world’s largest cosmetics company. Headquartered in Clichy, Hauts-de-Seine, France, the company also has five major manufacturing facilities and 15 distribution centers in the United States. L’Oréal’s business and manufacturing plants are home to thousands of employees.
ANNUAL SALES
Brands
MANUFACTURING FACILITIES
Distribution Centers
Now, when we look at performance results, we’re able to look at reasons for downtime or other maintenance-related issues. Breakdown is no longer a key issue. The ability to maintain the equipment has proven to be a massive benefit to L’Oréal."
—Harry Silverman, AVP Engineering
As L’Oréal continued to expand across the United States, the company recognized that performance improvement was key to equipment maintenance. L’Oréal needed a solution to track asset health and help the team increase the lifespan of equipment. The team wanted a system to house asset information, including unique equipment and products manufactured on a location-by-location basis.
One factor we measure is the utilization of our mechanics. We are always trying to bring that percentage up as high as we can. Now, one way we can do that is by not having them waste time going back to a central location to close out a work order. Everything is done remotely."— Harry Silverman, AVP Engineering
L’Oréal selected Maintenance Connection as its computerized maintenance management system (CMMS) due to its ease of use. The solution was implemented across all United States plants to minimize maintenance costs and maintain equipment of all types.
Ease of use was critical for us because we needed the team to recognize the value of the software and how it could help us. More importantly, we had to get people to use it."— Harry Silverman, AVP Engineering
With Maintenance Connection, the L’Oréal team can quantify performance by producing detailed reports on top performance KPIs, house all asset information in one location, increase mechanic utilization on the floor, and decrease the risk of downtime associated with equipment breakdown. The team can now even pinpoint how and why downtime is occurring.
Discover how a CMMS helps keep assets fully managed, improve equipment lifespan, increase preventive maintenance, eliminate downtime, and lower costs.
Learn how Cook Medical created an organized database of all assets, past equipment failures, and service history to improve processes.
See how the publishing plant easily organized all assets and implemented a preventive maintenance schedule to service equipment before it breaks.
Subscribe to stay up to date with our latest news, resources and best practices