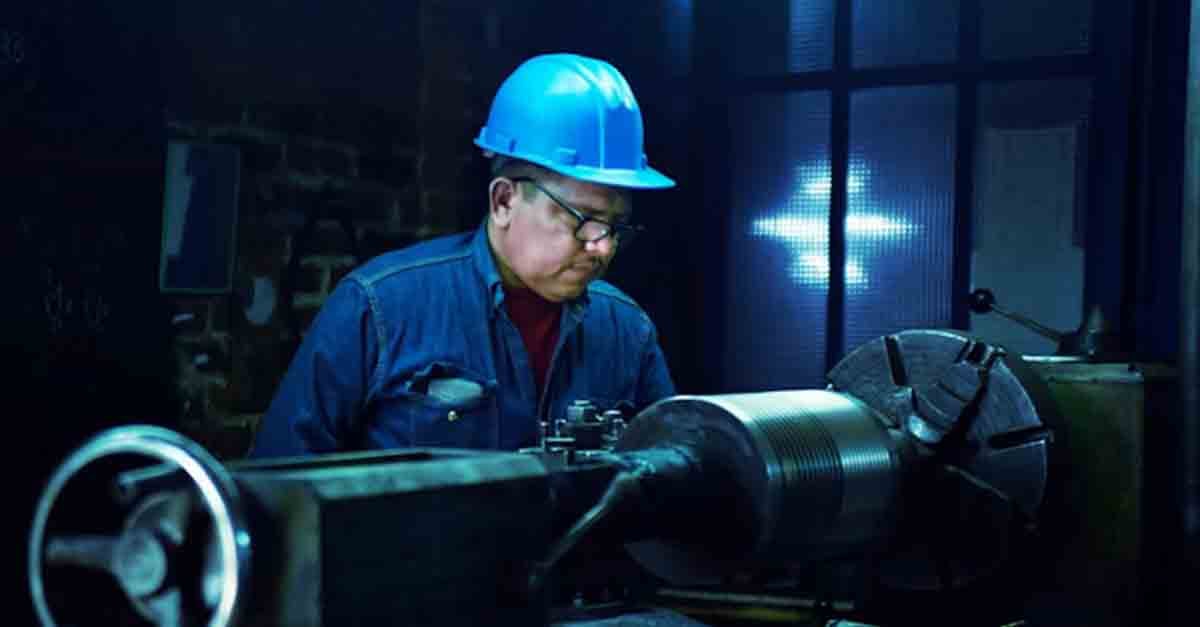
Maintenance Management: 7 Key Strategies for Success
Discover the meaning and secrets to successful maintenance management in 2024. Explore strategies to cut maintenance costs and boost operational ...
Solutions
Workplace Management Solutions
Real Estate Management Solutions
Maintenance Management Solutions
Energy Management Solutions
Engineering Document Management Solutions
Asset Management Solutions
Automate campus scheduling for classes, meetings, and exams with our EMS software.
Plan and manage conferences effortlessly with EMS software to impress guests and streamline operations.
Boost workplace flexibility and maximize space use with seamless desk and room booking.
Organize workplace or campus events smoothly, creating memorable experiences.
Optimize workspace, manage allocations efficiently, and reduce costs with our space management solutions.
Deliver projects on time and within budget by improving communication, collaboration, and efficiency with our software.
Streamline lease accounting for ASC 842, IFRS, and GASB compliance.
Manage leases efficiently by tracking key dates, analyzing costs, and ensuring compliance.
Centralize data and analytics for better insights, faster negotiations, and revenue growth.
Centralize facility and asset maintenance, automate work orders, and ensure compliance with our CMMS software.
Extend asset life, reduce downtime, and prevent costly repairs with data-driven monitoring.
Prevent equipment failures and extend asset life by detecting and addressing issues early.
Make sustainable, cost-efficient energy decisions by monitoring and optimizing power consumption.
Remotely monitor and control equipment with real-time data to predict issues, boost efficiency, and reduce downtime.
Easily share and collaborate on documents, creating a single source of truth for engineers and contractors.
Manage and analyze assets across their lifecycle to schedule maintenance, reduce downtime, and extend lifespan.
Improve visibility, automate work orders, and ensure compliance for efficient facility and asset management.
Resources
Browse our full library of resources all in one place, including webinars, whitepapers, podcast episodes, and more.
Support
Looking for access to technical support, best practices, helpful videos, or training tools? You’ve come to the right place.
About Accruent
Get the latest information on Accruent, our solutions, events, and the company at large.
Maintenance KPIs are essential for evaluating maintenance efficiency, boosting equipment reliability, and optimizing operations. This guide explores key metrics, their benefits, and how tools like CMMS simplify tracking for improved decision-making and cost savings.
Table of contents
If an organization isn’t analyzing its actions, it’s falling behind. According to a survey of senior executives conducted by PwC, organizations are three times more likely to see significant improvements in decision-making.
In the manufacturing world, Key Performance Indicators (KPIs) measure the efficiency and effectiveness of maintenance operations. Tracking these KPIs improves decision-making, equipment reliability, and overall operations.
This guide covers essential maintenance KPIs, their calculations, examples, and the benefits of monitoring them.
While intuition can provide a hunch or spark that starts you down a particular path, it's through data that you verify, understand, and quantify.”
A Maintenance KPI is a metric used to evaluate the performance of maintenance activities within an organization. It provides quantitative data that helps assess maintenance strategies' effectiveness and identify improvement areas. These metrics provide valuable information, illustrate the efficiency of maintenance processes, and help maximize equipment reliability.
Industries, like manufacturing, utilities, transportation, and healthcare, commonly use maintenance KPIs. In these sectors, clear and actionable data is crucial for making informed decisions and addressing the complexities of maintenance processes. By tracking KPIs like equipment downtime, work order completion rates, and maintenance costs, organizations can enhance productivity, ensure safety, and refine their maintenance management strategies.
Download the Free Maintenance KPIs Guide to track performance, improve operations, and keep your maintenance strategy on point.
Knowing maintenance KPIs is essential for optimizing operations. But what KPIs should organizations consider and prioritize? In this guide, we explore eight key examples that provide actionable insights into maintenance performance and efficiency.
MTBF measures the average time equipment operates before a failure occurs. It provides insights into equipment reliability, which helps predict future failures. A high MTBF indicates fewer frequent failures, which improves uptime and productivity.
MTTR calculates the average time required to repair equipment and return it to operational status. It helps understand the efficiency of maintenance processes. Lower MTTR means faster repairs and reduced downtime.
PMP measures the proportion of planned maintenance hours versus total maintenance hours. It indicates the effectiveness of preventive maintenance scheduling. A high PMP suggests a proactive approach, reducing unplanned downtime.
OEE evaluates equipment utilization by combining availability, performance, and quality. It provides a clear picture of equipment efficiency. High OEE means the equipment achieves optimal performance, resulting in high productivity and quality output.
The maintenance backlog is the total amount of pending maintenance work. It helps prioritize tasks. Managing the backlog means that tasks are completed in a timely manner, which prevents potential failures.
This measures total maintenance cost relative to the number of units produced. It assesses and helps analyze cost efficiency. Lower cost per unit indicates operations are working as desired, which contributes to cost savings in the long run.
This metric calculates the proportion of maintenance hours spent on emergency repairs versus total maintenance hours. It provides complex data on the frequency of unexpected failures. Reducing this percentage means more stable operations and lower repair costs.
PM Compliance measures the percentage of scheduled preventive maintenance tasks completed on time. It confirms preventive tasks are performed as planned, which will prevent any breakdowns. Additionally, high compliance improves equipment reliability.
Tracking maintenance KPIs is more than just a numbers game—it’s a powerful way to drive smarter decision-making, boost profitability, and fuel revenue growth. By focusing on the right KPIs, organizations can achieve meaningful improvements and tangible results.
Tracking maintenance KPIs provides accurate and up-to-date information, encouraging informed decision-making. Identifying areas needing improvement helps prioritize maintenance tasks and allocate resources more effectively. The result is promptly addressing the most critical issues.
Maintenance KPIs identify trends and patterns affecting equipment reliability. This information helps benefit preventive maintenance programs. Additionally, the proactive approach reduces unexpected breakdowns and extends the lifespan of equipment.
Maintenance KPIs help inform maintenance scheduling and resource use, reducing potential waste. This leads to more efficient use of maintenance staff and materials, driving significant cost savings and efficiency.
Tracking maintenance KPIs requires practical tools to centralize and analyze data. Here are some useful tools:
CMMS software centralizes maintenance data, schedules, and logs, making it an effective tool for tracking maintenance KPIs. CMMS software features automated work orders, preventive maintenance scheduling, and real-time reporting. For example, Accruent Maintenance Connection is a tool that helps organizations track KPIs to improve overall efficiency.
Spreadsheets are helpful for manual tracking and calculations, especially for smaller operations or as a supplemental tool. However, they can become cumbersome and less efficient for large-scale operations.
Dashboards offer visual tools that aggregate KPI data for quick reference and analysis to provide a clear, real-time view of key metrics. The layout helps teams stay informed and responsive to whatever is needed at any given moment.
Accruent Maintenance Connection is a leading maintenance tracking software designed to simplify maintenance operations and improve efficiency and overall effectiveness. The robust platform centralizes maintenance data, schedules, and logs and offers comprehensive ways to track maintenance KPIs within that data. The result is improved equipment reliability, which benefits operations overall.
Key features of Accruent Maintenance Tracking Software include the following:
Maintenance Connection serves various industries, including manufacturing, utilities, transportation, and healthcare. It is designed to accommodate multiple asset types to provide comprehensive maintenance management across different sectors.
It’s particularly beneficial for decision-makers such as managers, supervisors, and other floor leaders. The information provided helps organizations use actual, complex data to inform their decision-making. The ease of access to KPIs and other valuable metrics makes it a worthwhile investment for any company looking to improve maintenance management operations.
In modern manufacturing, data-driven decisions drive innovation. Organizations can rethink how they manage and optimize operations using Maintenance Connection. It’s about moving from reactive to proactive strategies.
Ready to see what’s possible? Learn about how Maintenance Connection can truly transform maintenance management. Book a demo today!
Here are common questions about maintenance KPIs.
The most important maintenance KPIs include Mean Time Between Failures (MTBF), Mean Time to Repair (MTTR), Planned Maintenance Percentage (PMP), and Overall Equipment Effectiveness (OEE). These KPIs monitor equipment reliability, maintenance efficiency, and overall operational performance. They provide valuable insights for an organization to focus on continuous improvement.
To improve PMP, focus on proactive maintenance task scheduling. Plan all preventive maintenance activities well in advance and allocate accurate resources for them. A CMMS like Maintenance Connection will automate and simplify these processes. When utilized correctly, it makes it easier to track and increase PMP.
Tracking Maintenance Cost per Unit of Production helps an organization understand the cost-efficiency of maintenance operations. It identifies areas where maintenance costs can be reduced and guarantees effective resource allocation. Lowering this cost can and will significantly impact overall profitability.
Discover the meaning and secrets to successful maintenance management in 2024. Explore strategies to cut maintenance costs and boost operational ...
Discover the importance of equipment maintenance, explore best practices, and find the right software solutions. Optimize your maintenance strategy ...
Learn how to develop a robust preventive maintenance program. Explore step-by-step guidelines and expert tips to streamline maintenance operations.
Subscribe to stay up to date with our latest news, resources and best practices