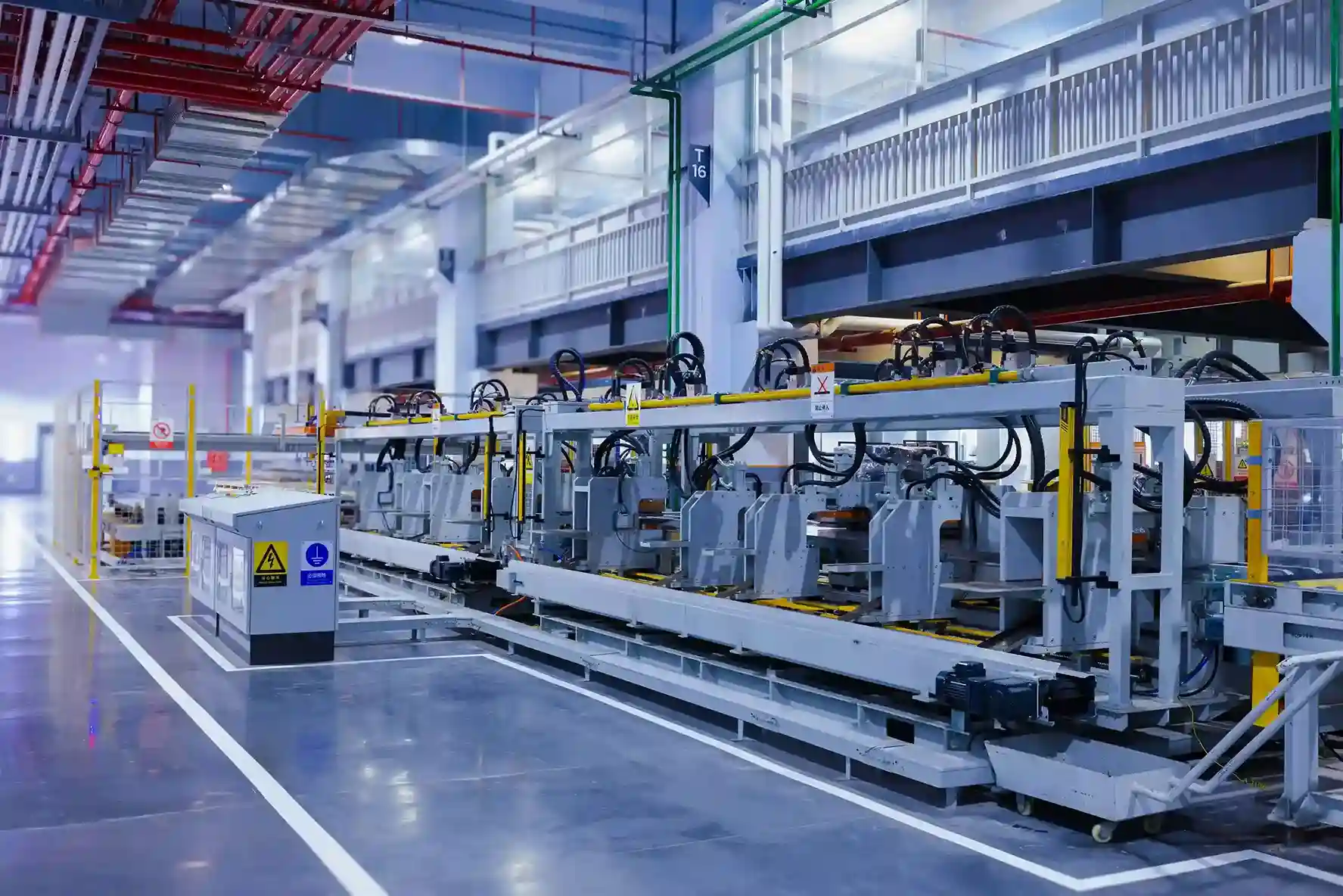
What is Scheduled Maintenance? Best Practices & Software
Learn more about the significance of scheduled maintenance, adopt best practices, and leverage software solutions for optimal efficiency.
Solutions
Workplace Management Solutions
Real Estate Management Solutions
Maintenance Management Solutions
Energy Management Solutions
Engineering Document Management Solutions
Asset Management Solutions
Automate campus scheduling for classes, meetings, and exams with our EMS software.
Plan and manage conferences effortlessly with EMS software to impress guests and streamline operations.
Boost workplace flexibility and maximize space use with seamless desk and room booking.
Organize workplace or campus events smoothly, creating memorable experiences.
Optimize workspace, manage allocations efficiently, and reduce costs with our space management solutions.
Deliver projects on time and within budget by improving communication, collaboration, and efficiency with our software.
Streamline lease accounting for ASC 842, IFRS, and GASB compliance.
Manage leases efficiently by tracking key dates, analyzing costs, and ensuring compliance.
Centralize data and analytics for better insights, faster negotiations, and revenue growth.
Centralize facility and asset maintenance, automate work orders, and ensure compliance with our CMMS software.
Extend asset life, reduce downtime, and prevent costly repairs with data-driven monitoring.
Prevent equipment failures and extend asset life by detecting and addressing issues early.
Make sustainable, cost-efficient energy decisions by monitoring and optimizing power consumption.
Remotely monitor and control equipment with real-time data to predict issues, boost efficiency, and reduce downtime.
Easily share and collaborate on documents, creating a single source of truth for engineers and contractors.
Manage and analyze assets across their lifecycle to schedule maintenance, reduce downtime, and extend lifespan.
Improve visibility, automate work orders, and ensure compliance for efficient facility and asset management.
Resources
Browse our full library of resources all in one place, including webinars, whitepapers, podcast episodes, and more.
Support
Looking for access to technical support, best practices, helpful videos, or training tools? You’ve come to the right place.
About Accruent
Get the latest information on Accruent, our solutions, events, and the company at large.
Discover the essentials of maintenance scheduling, from industry-recommended best practices to the tangible benefits and innovative software that support them. This resource is a must-read for manufacturing professionals looking to optimize their maintenance strategies and improve operational efficiency.
Table of contents
Downtime in maintenance is the enemy. And yet, did you know that 82% of companies have experienced at least one unplanned downtime incident in the last two years? Most have suffered two or more.
This reality underscores the need for maintenance scheduling, a strategy that keeps this adversary at bay. Ensuring equipment gets serviced and inspected precisely when needed minimizes interruptions and extends machinery life.
Here is a guide to maintenance scheduling, how it works, and how to utilize the right maintenance scheduling software to automate common solutions.
Maintenance scheduling is a strategic process within maintenance management aimed at organizing and executing tasks such as equipment inspections, preventive maintenance, and corrective repairs. This systematic approach ensures that all necessary maintenance activities are performed in a timely manner, which prevents unforeseen equipment failures.
The primary objective of maintenance scheduling is to minimize downtime while maximizing the efficiency and lifespan of equipment. By adhering to a well-defined schedule, organizations can achieve a higher level of reliability and performance. This ensures that machinery and assets continue to function without issues over time.
Finding synergy between maintenance planning and scheduling is the backbone of an effective maintenance strategy. Planning identifies what maintenance tasks need to be executed while scheduling pinpoints the best timing for these activities. The collaboration is vital for preventing unexpected equipment breakdowns while managing maintenance costs.
Moreover, this harmony in process means that maintenance operations are conducted with maximum efficiency. Nailing this will significantly minimize downtime. Through meticulous planning and scheduling maintenance, organizations will optimize their equipment. In turn, that supports continuous production – improving the overall product and productivity.
Download the Free Maintenance KPIs Guide to track performance, improve operations, and keep your maintenance strategy on point.
Efficient maintenance is not about fixing what is broken. It is about preventing problems before they start. Utilize these best practices to harness the full potential of scheduled maintenance.
Know what is wrong before it happens. The foundation of any maintenance program is the regular inspection of equipment. These inspections should be systematic, utilizing detailed checklists to make sure no step is overlooked. Determine the frequency of these inspections based on the equipment’s usage rates and the manufacturer’s recommendations. By identifying issues early, maintenance teams can address them before they escalate into costly repairs – or result in equipment downtime.
Foster an environment that looks to solve problems now – not later. Preventive maintenance software schedules maintenance activities for equipment before issues arise. The proactive approach follows equipment manufacturers’ maintenance guidelines and keeps meticulous records of all maintenance activities and inspections. This transparency supports a culture of accountability and continuous improvement while providing valuable data for future planning.
Smart organizations continuously analyze their operations. Use sensors and monitoring systems to regularly track equipment performance. This data is vital for condition-based maintenance, where maintenance tasks are performed based on the actual condition of the equipment rather than on a predetermined schedule. Combine this information with predictive maintenance techniques to accurately forecast potential failures. This means maintenance can be scheduled at the most opportune times while avoiding unplanned downtime.
Knowledge is power – and empowering. A well-trained maintenance team is the fuel that powers maintenance programs. Training should cover routine procedures along with troubleshooting and emergency response. Keep open lines of communication between the maintenance team, operations staff, and management. Share insights and action points that can lead to process improvements. Encourage feedback from staff to build more innovative solutions and a more cohesive maintenance strategy.
Look how to get better every day. The maintenance process should be dynamic, with regular reviews of schedules, procedures, and outcomes. Incorporate learnings and feedback from maintenance staff and equipment operators. Know that there is always an opportunity to become more efficient and effective. Embrace and utilize modern technologies and techniques to drive innovation and improve equipment performance.
Do not ignore the potential of technology. For instance, a Computerized Maintenance Management System (CMMS) will transform maintenance scheduling from a complex, time-consuming process into a streamlined operation. Key features of maintenance management software include automated scheduling of maintenance tasks, easy access to maintenance records, and the ability to generate reports and other useful data. Integrate the software with other systems – such as inventory management or operational monitoring – to provide a comprehensive view of the organization’s maintenance needs and performance.
The ability to capture, process, analyze, and act on data in real time allows brands to automate demand forecasting and supply-chain planning to optimize everything from inventory assortment to customer engagement and promotions.”— Harvard Business Review
Stay ahead of problems and avoid issues. Maintenance scheduling stays ahead of equipment failures and therefore minimizes unscheduled downtime. By systematically planning maintenance activities, it ensures machinery undergoes necessary upkeep before breakdowns occur. This proactive approach reduces major failures and ensures an uninterrupted operational flow. The ripple effects can be profound – enhancing productivity while making sure production targets are consistently met.
Tap the full potential of resources. Regularly scheduled maintenance is key for maintaining equipment at its peak performance. Through routine care, each piece of equipment avoids any major setbacks while improving the lifespan of the machinery. This means a significant reduction in replacements or other unexpected costs. It is about optimizing equipment to the highest level while getting the most out of equipment over its life.
Do not spend money that does not need to be spent. Maintenance scheduling helps avoid expensive repairs due to equipment neglect or sudden failures. It allows for the early detection of minor issues and prevents them from evolving into more severe and costly problems. The sum of these savings can contribute significantly to an organization’s financial health. Use those funds for more strategic investments.
Keep team members safe and remain compliant. Routine safety checks and verifications ensure that all equipment adheres to the highest safety standards. That reduces the likelihood of accidents while providing a safe work environment for employees. It also streamlines compliance with tricky industry regulations. That protects an organization from potential fines or legal complications. It fosters a culture of safety and compliance that increases overall efficiency while considering the well-being of every individual on the production floor.
Modern technology is a momentous change in the realm of maintenance management. By revolutionizing the planning and scheduling process, maintenance scheduling software streamlines operations and makes them more efficient.
The software empowers managers with the data necessary for informed decision-making – but that is just the beginning. The right CMMS software’s capabilities extend beyond mere scheduling: it excels in tracking, reporting, and analysis.
For organizations looking to optimize their operations, a CMMS offers clarity, efficiency, and actionable insights that drive performance and reliability. It is about building a culture that looks inward while it looks forward, using the power of automation to fuel the engine of change.
Accruent’s Maintenance Connection is one of the leading CMMS solutions. It offers unparalleled support for comprehensive maintenance scheduling. This software offers an array of features that help organizations get more efficient, effective, and optimized, such as the following:
Maintenance Connection is a choice tool for several industries, such as manufacturing, healthcare, and IT support. It helps streamline and automate schedules, repairs, and traditionally manual tasks.
For manufacturing professionals, plant managers, production supervisors, and maintenance managers, the software is vital for achieving operational excellence. It optimizes and automates maintenance scheduling, which frees up valuable time for staff to focus on strategic planning and oversight. This means maintenance tasks are executed more swiftly and effectively, and that directly contributes to the bottom line.
Managers are empowered to make informed decisions based on data, not just instincts. It is a dynamic tool that encourages organizational leaders to look beyond the task at hand, but the potential of the future.
The ability to capture, process, analyze, and act on data in real time allows brands to automate demand forecasting and supply-chain planning to optimize everything from inventory assortment to customer engagement and promotions.”— Harvard Business Review
Greatness comes to those who prepare, not react. By utilizing leading CMMS software like Accruent’s Maintenance Connection, organizations equip themselves and their teams with the technology to enhance efficiency, reduce costs, and optimize operations.
Want to know how? Discover the transformative features of Maintenance Connection today. Build a foundation for the future on data, analysis, and automation.
Scheduled maintenance preempts breakdowns and ensures equipment runs smoothly with minimal interruptions. By preventing major repairs through routine checks and maintenance, organizations avoid the excessive costs associated with downtime and emergency repairs. This leads to critical time and financial savings.
Maintenance planning and scheduling is the strategic approach to maintaining equipment in optimal condition. Planning identifies what maintenance tasks are needed while scheduling determines the best timing for these tasks. This balance ensures equipment reliability and efficiency, regardless of the demands.
Creating a maintenance schedule starts with understanding your equipment’s needs:
Learn more about the significance of scheduled maintenance, adopt best practices, and leverage software solutions for optimal efficiency.
Discover the importance of equipment maintenance, explore best practices, and find the right software solutions. Optimize your maintenance strategy ...
Learn how to develop a robust preventive maintenance program. Explore step-by-step guidelines and expert tips to streamline maintenance operations.
Subscribe to stay up to date with our latest news, resources and best practices