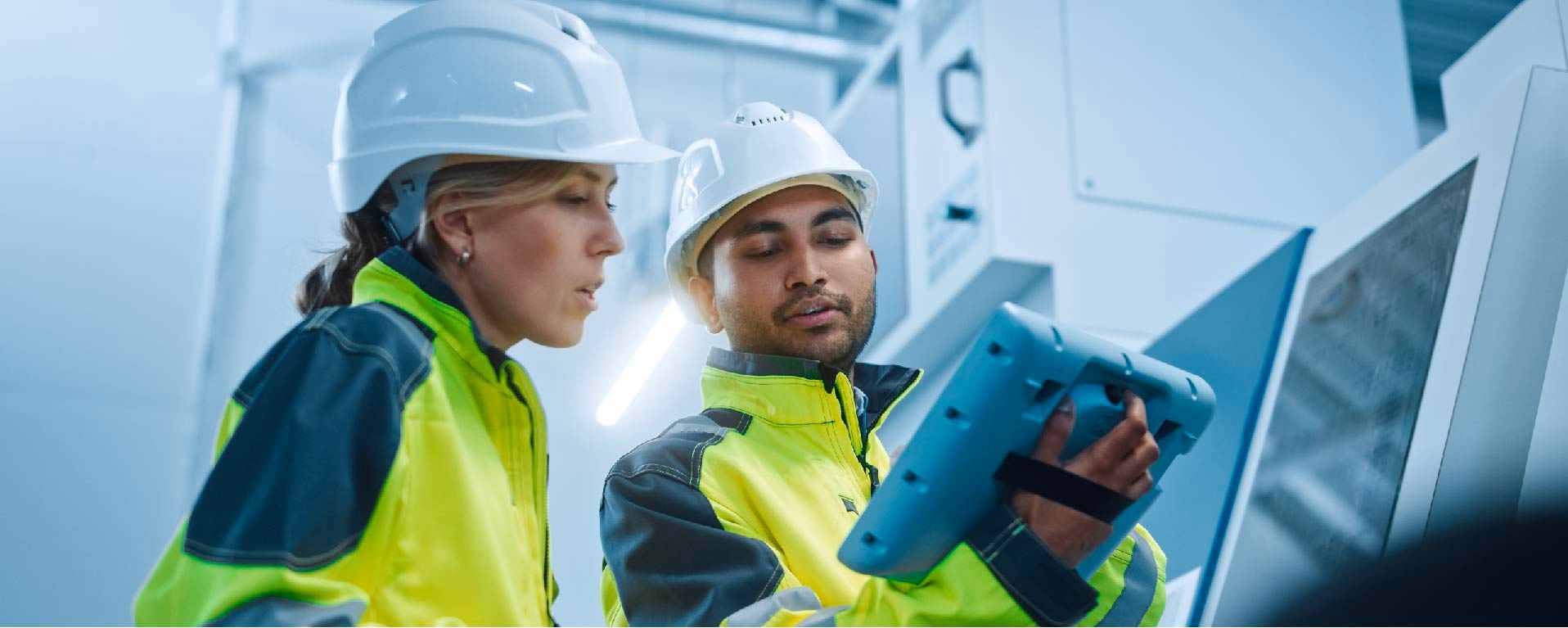
How Maintenance Managers Extend Asset Life and Decrease Downtime with CMMS
The right CMMS can help your organization minimize downtime and extend asset life. Here's how.
Solutions
Workplace Management Solutions
Real Estate Management Solutions
Maintenance Management Solutions
Energy Management Solutions
Engineering Document Management Solutions
Asset Management Solutions
Automate campus scheduling for classes, meetings, and exams with our EMS software.
Plan and manage conferences effortlessly with EMS software to impress guests and streamline operations.
Boost workplace flexibility and maximize space use with seamless desk and room booking.
Organize workplace or campus events smoothly, creating memorable experiences.
Optimize workspace, manage allocations efficiently, and reduce costs with our space management solutions.
Deliver projects on time and within budget by improving communication, collaboration, and efficiency with our software.
Streamline lease accounting for ASC 842, IFRS, and GASB compliance.
Manage leases efficiently by tracking key dates, analyzing costs, and ensuring compliance.
Centralize data and analytics for better insights, faster negotiations, and revenue growth.
Centralize facility and asset maintenance, automate work orders, and ensure compliance with our CMMS software.
Extend asset life, reduce downtime, and prevent costly repairs with data-driven monitoring.
Prevent equipment failures and extend asset life by detecting and addressing issues early.
Make sustainable, cost-efficient energy decisions by monitoring and optimizing power consumption.
Remotely monitor and control equipment with real-time data to predict issues, boost efficiency, and reduce downtime.
Easily share and collaborate on documents, creating a single source of truth for engineers and contractors.
Manage and analyze assets across their lifecycle to schedule maintenance, reduce downtime, and extend lifespan.
Improve visibility, automate work orders, and ensure compliance for efficient facility and asset management.
Resources
Browse our full library of resources all in one place, including webinars, whitepapers, podcast episodes, and more.
Support
Looking for access to technical support, best practices, helpful videos, or training tools? You’ve come to the right place.
About Accruent
Get the latest information on Accruent, our solutions, events, and the company at large.
Looking to improve your Overall Equipment Effectiveness (OEE)? Here's how Maintenance Connection can help make that happen.
Table of contents
In a 2017 report Asset Performance Management: Blazing A Better Path To Operational Excellence, the Aberdeen Group noted that best-in-class manufacturers had Overall Equipment Effectiveness (OEE) scores of 90% compared to just 84% for average performers.
Manufacturing companies use Overall Equipment Effectiveness (OEE) as an important manufacturing productivity metric. The OEE metric is essential to helping companies understand total productive maintenance (TPM) and identify maintenance performance improvement opportunities.
Manufacturing companies need to clearly understand the parameters around calculating OEE and consider how to use the metric to improve operational performance. OEE is about:
Availability is the ratio of scheduled operating time, minus any downtime, divided by the scheduled operating time. For example, if an extruder is planned for 12 hours of production use but is down for 3 hours of that time, then the extruder’s availability rate is 75%.
Performance rate is calculated by dividing actual output by standard output. Many manufacturers struggle with what to use for standard output. While some companies use an equipment’s design rate, this metric is not a helpful number if it is not an accurate depiction of standard output. The rule of thumb for standard output is to use the best output rate known to be produced on the machine, regardless of whether that is above or below design speed according to this Industry Week article.
Quality rate measures the quality output against overall production output. Quality rate is calculated by dividing right-first-time production output against overall production output.
Once the availability, performance, and quality rates are captured, they are multiplied to provide an OEE metric as shown below.
OEE (%) = Availability rate × Performance rate × Quality rate
A comprehensive CMMS can have a significant positive impact on equipment availability and performance rate and, to a lesser degree, quality rate. As a leading CMMS, Maintenance Connection reduces unplanned downtime and minimizes repair time when unplanned downtime does occur.
Drive performance improvement with your CMMS. Get the report - 2018 CMMS Benchmarks & Best Practices to Improve Maintenance Operations.
Many manufacturing companies continue to operate with a reactive mindset, responding to unexpected downtime events without the necessary asset insight to shift to a more proactive approach. By optimizing preventive maintenance, many unplanned equipment outages can be avoided. This approach has a positive impact both on availability and performance rates. Properly maintained equipment is more apt to perform at its optimal level, functioning per design.
Maintenance Connection’s preventive maintenance (PM) capability helps companies to alter their maintenance approach from unscheduled events to planned maintenance, avoiding more costly downtime. Manufacturers can monitor unlimited metrics and equipment specifications in Maintenance Connection, empowering them to make better decisions about how and when preventive maintenance should be performed. As an asset’s history is created, trends can be identified, and automated PM schedules based on calendar-based or utilization-based triggers can be implemented.
Consider a conveyor that is used intermittently as a backup for the primary conveyor. When needed, the backup conveyor must operate effectively. Without a readily available online asset history, it might be difficult to identify any failure patterns with this conveyor. However, when these asset records are easily accessible, you can see that parts in the secondary conveyor could fail over the course of a year, if not greased after 50 hours of use.
With Maintenance Connection’s preventive maintenance capability, it is easy to spot these trends, and then establish a PM schedule that monitors conveyor utilization and automatically creates a PM work order when usage nears 50 hours. Over time, preventive maintenance programs improve equipment availability, help equipment operate at optimal levels, and elevate OEE performance.
Maintenance Connection’s work order management software is fundamental to a strong and efficient maintenance program that reduces downtime. Consider the value of an expedited work order process when a production operator can make a repair request. The maintenance manager assigns a priority work order to a specific technician, then the designated maintenance technician immediately receives the priority work order (without having to complete paperwork or spend time filling out form fields in multiple software programs).
With MC Express, the assigned technician can use a mobile device to:
When finished, the technician completes the work order and puts the asset back in service.
See how Maintenance Connection’s CMMS streamlines the work order process, minimizing repair time when equipment is down? This functionality helps increase the equipment availability number and improve the overall OEE performance.
Organizations often struggle to determine whether they are maximizing equipment performance, which is critical to optimizing overall manufacturing operations.
Maintenance Connection establishes a real-time and historical record system for asset maintenance that moves beyond paper-based systems or spreadsheets to find equipment performance data faster. Using this asset and maintenance intelligence also makes it easier to understand and calculate OEE variables such as availability and performance rate.
With Maintenance Connection Reporting, you can monitor equipment downtime and quickly calculate availability. The asset data you need is accessible, and reports can be configured to provide meaningful data that integrates into your organization’s OEE program efforts.
Across the manufacturing industry, OEE is a valuable tool for benchmarking and driving total maintenance performance improvement. Maintenance Connection can be a foundational element for effective OEE programs:
See how establishing manufacturing excellence means measuring equipment performance and identifying improvement opportunities? Driving equipment availability increases, enhancing performance rates and maximizing both quality & quantity of output.
Maintenance Connection can help drive OEE performance improvement by reducing downtime, shifting organizations to proactive maintenance models, improving preventive maintenance planning and scheduling, and optimizing labor resource efficiency.
Ready to learn more about driving performance improvement with a CMMS? Get the report - 2018 CMMS Benchmarks & Best Practices to Improve Maintenance Operations. Ready to get started? Schedule a demo today!
The right CMMS can help your organization minimize downtime and extend asset life. Here's how.
Relying exclusively on reactive maintenance practices can lead to many unintended consequences, like shortened asset life, reduced safety and high ...
How comprehensive asset intelligence, effective preventive maintenance, and efficient labor scheduling can lead to success in the chemical industry.
Subscribe to stay up to date with our latest news, resources and best practices