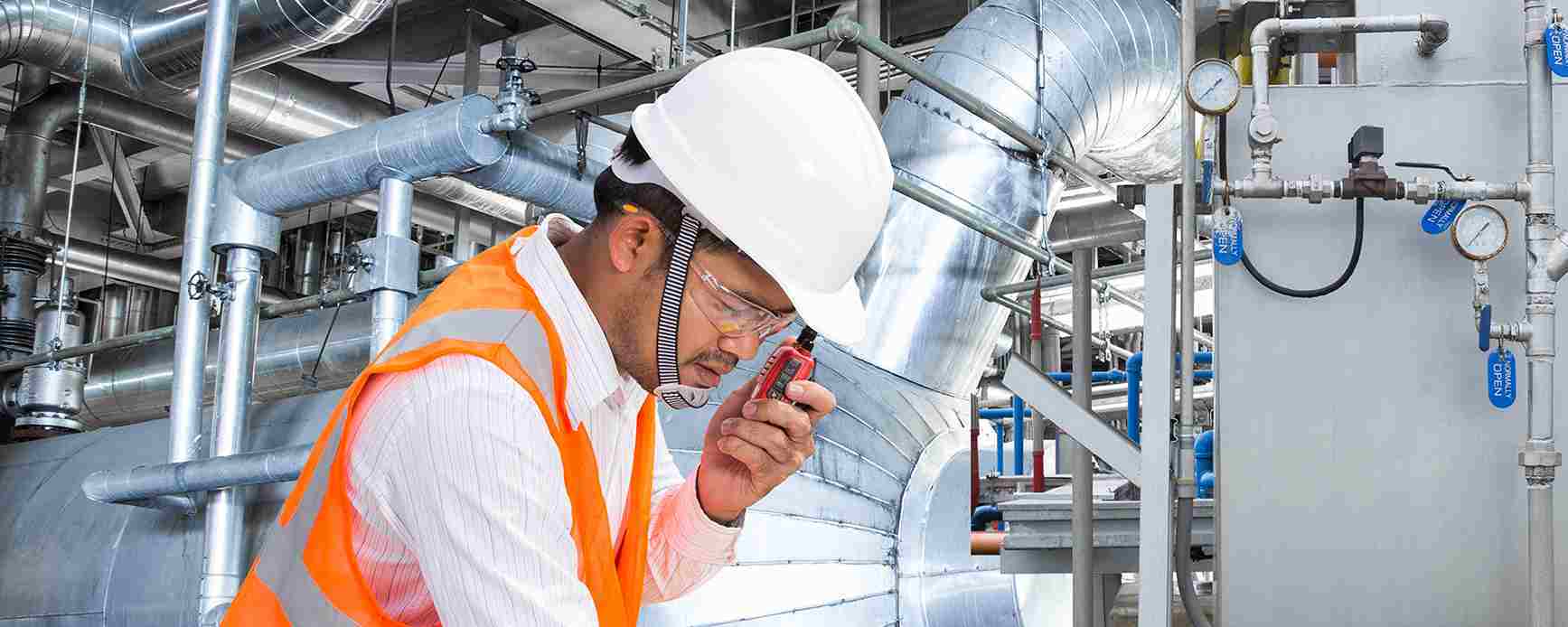
How to Create an Equipment Downtime Report in a CMMS
Use real-time data in Maintenance Connection's downtime reports to better understand your downtime causes and reduce it altogether.
Solutions
Workplace Management Solutions
Real Estate Management Solutions
Maintenance Management Solutions
Energy Management Solutions
Engineering Document Management Solutions
Asset Management Solutions
Automate campus scheduling for classes, meetings, and exams with our EMS software.
Plan and manage conferences effortlessly with EMS software to impress guests and streamline operations.
Boost workplace flexibility and maximize space use with seamless desk and room booking.
Organize workplace or campus events smoothly, creating memorable experiences.
Optimize workspace, manage allocations efficiently, and reduce costs with our space management solutions.
Deliver projects on time and within budget by improving communication, collaboration, and efficiency with our software.
Streamline lease accounting for ASC 842, IFRS, and GASB compliance.
Manage leases efficiently by tracking key dates, analyzing costs, and ensuring compliance.
Centralize data and analytics for better insights, faster negotiations, and revenue growth.
Centralize facility and asset maintenance, automate work orders, and ensure compliance with our CMMS software.
Extend asset life, reduce downtime, and prevent costly repairs with data-driven monitoring.
Prevent equipment failures and extend asset life by detecting and addressing issues early.
Make sustainable, cost-efficient energy decisions by monitoring and optimizing power consumption.
Remotely monitor and control equipment with real-time data to predict issues, boost efficiency, and reduce downtime.
Easily share and collaborate on documents, creating a single source of truth for engineers and contractors.
Manage and analyze assets across their lifecycle to schedule maintenance, reduce downtime, and extend lifespan.
Improve visibility, automate work orders, and ensure compliance for efficient facility and asset management.
Resources
Browse our full library of resources all in one place, including webinars, whitepapers, podcast episodes, and more.
Support
Looking for access to technical support, best practices, helpful videos, or training tools? You’ve come to the right place.
About Accruent
Get the latest information on Accruent, our solutions, events, and the company at large.
Learn how to create automated equipment downtime reports in your CMMS -- and how to use these reports to optimize repairs and minimize downtime altogether.
Those assets include machines, equipment, technicians performing day-to-day tasks, and more. One of the most critical components across your facility is having equipment up and running as much as possible with little or no equipment downtime. Therefore downtime reporting becomes critical to planning, most especially to profit and loss reporting.
To keep assets operating smoothly, understanding what causes breakdowns and how often repairs are made is essential. An equipment downtime report puts this information at your fingertips.
When it comes to creating an asset downtime report, consider your options:
While an organized equipment report seems like the best option, 48% of maintenance managers still rely on manual methods like spreadsheets.
Produce equipment downtime reports quickly. Read this article on How to Create an Equipment Downtime Report in a CMMS Software System
With an easy-to-understand, connected reporting system, you can produce downtime reports quickly, gather accurate and real-time data, and minimize downtime altogether.
Accruent’s computerized maintenance management system (CMMS) helps create fast, legible asset downtime reports.
If your company still relies on manual asset tracking and reporting, it’s frustrating to navigate through spreadsheets. Eliminate the need for spreadsheets (with thousands of rows of assets for each location) with a functional CMMS.
When you implement a CMMS, you gain real-time visibility and insights that minimize downtime and reduce lost profits. Rather than a list, users can organize all assets in one place in a hierarchical structure for an easy-to-scan downtime report.
With a CMMS, you can add equipment to work orders as you populate the work orders. Then, you can sort by overall asset, brand or lifecycle stage, or choose to see assets by location. In one click, you can sort assets or locations by downtime to generate quick, data-driven reports for future decisions.
It can take hours or even days to update a manual asset log. Each asset has unique descriptions, needs, specifications and a location to inventory. Without a CMMS, managing new or old assets is a disorganized, manual process.
The ability to update assets immediately in a CMMS stands in stark contrast to the outdated, manual method of spreadsheet data input and reporting. A top-notch CMMS gives you drag and drop functionality to add new assets, or search and filter to find the assets quickly within your database. As a result, you get quick updates, and an easily navigable database to track your assets.
What if you could tackle machine downtime before it even occurs? With the proper preventive maintenance strategy, it’s possible.
In a recent study, 31% of survey respondents indicated that they plan to implement preventive maintenance to decrease future unscheduled downtime. While it would be great to predict when a breakdown occurs, it’s difficult without the right database.
With a CMMS, you can input data from the description of an asset model and past service history, and create or follow recommended predictive maintenance schedules. This functionality enables you to assign preventive care tasks automatically to available technicians – minimizing the risk of downtime before it occurs. In turn, you’ll also boost technician productivity, as preventive repairs are often less intensive and costly.
Many organizations are still performing reactive, instead of preventive maintenance, and lack the data that they need to drive decisions. You need the right CMMS to reduce costs and increase productivity while anticipating and supporting your business goals.
Move away from manual equipment reports with a top-notch CMMS. Discover CMMS Reporting and Analytics solutions.
Use real-time data in Maintenance Connection's downtime reports to better understand your downtime causes and reduce it altogether.
The right CMMS can help your organization minimize downtime and extend asset life. Here's how.
Want to overcome recurring pain points and reach goals like decreased downtime, increased productivity and maximized transparency? Then you need a ...
Subscribe to stay up to date with our latest news, resources and best practices