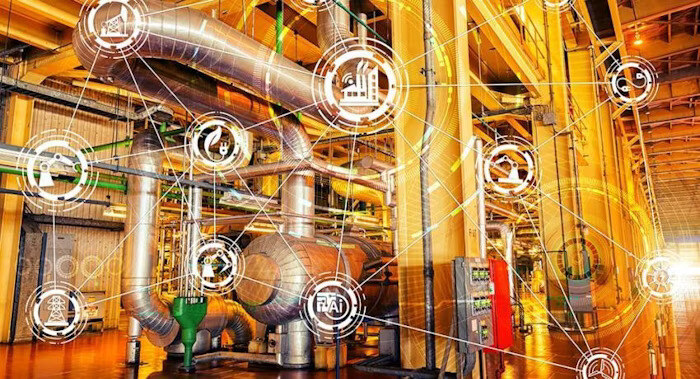
3 IoT Strategies for Improving Your Manufacturing Processes with Maintenance Connection
Explore three IoT strategies that improve processes and efficiency using maintenance connection software.
Solutions
Workplace Management Solutions
Real Estate Management Solutions
Maintenance Management Solutions
Energy Management Solutions
Engineering Document Management Solutions
Asset Management Solutions
Automate campus scheduling for classes, meetings, and exams with our EMS software.
Plan and manage conferences effortlessly with EMS software to impress guests and streamline operations.
Boost workplace flexibility and maximize space use with seamless desk and room booking.
Organize workplace or campus events smoothly, creating memorable experiences.
Optimize workspace, manage allocations efficiently, and reduce costs with our space management solutions.
Deliver projects on time and within budget by improving communication, collaboration, and efficiency with our software.
Streamline lease accounting for ASC 842, IFRS, and GASB compliance.
Manage leases efficiently by tracking key dates, analyzing costs, and ensuring compliance.
Centralize data and analytics for better insights, faster negotiations, and revenue growth.
Centralize facility and asset maintenance, automate work orders, and ensure compliance with our CMMS software.
Extend asset life, reduce downtime, and prevent costly repairs with data-driven monitoring.
Prevent equipment failures and extend asset life by detecting and addressing issues early.
Make sustainable, cost-efficient energy decisions by monitoring and optimizing power consumption.
Remotely monitor and control equipment with real-time data to predict issues, boost efficiency, and reduce downtime.
Easily share and collaborate on documents, creating a single source of truth for engineers and contractors.
Manage and analyze assets across their lifecycle to schedule maintenance, reduce downtime, and extend lifespan.
Improve visibility, automate work orders, and ensure compliance for efficient facility and asset management.
Resources
Browse our full library of resources all in one place, including webinars, whitepapers, podcast episodes, and more.
Support
Looking for access to technical support, best practices, helpful videos, or training tools? You’ve come to the right place.
About Accruent
Get the latest information on Accruent, our solutions, events, and the company at large.
If you want to make your food and beverage operations more scalable, standardized, and sustainable, a CMMS can help.
Table of contents
The ability to achieve modernization in the food and beverage industry is required by the Food Safety Modernization Act (FSMA) and is a path to better lean management and profitability.
Sustainability, scalability and standardization are just a few of the benefits gained through compliance. Innovation in modernization does not have to be a cost; it can provide streamlined processes that sustain and boost the bottom line rather than drain it.
A well-known example is the innovation and implementation of Lean Manufacturing at Toyota, which was so successful in every sector of manufacturing that it expanded into other industries. If you are not familiar with the Lean methodology, it emphasizes maximizing customer value while minimizing waste. Simply put, Lean means creating more value for customers with fewer resources.
With many organizations having already implemented Lean methodologies, they are already doing more with less, cutting costs to the minimum. So, what more can be done? Research has shown through the Theory of Constraints and Lean Thinking that a company can move beyond Lean Manufacturing, through an organizational process focused on profit improvement.
How do you go beyond lean?
You need a solution, such as a computerized maintenance management system (CMMS) or an enterprise asset management solution (EAM) that will help you find your overall equipment effectiveness (OEE). This ensures your assets and processes are sustainable, cost-effective and scalable. The sustainability, standardization and scalability offered by these solutions are what will ultimately take you beyond Lean.
Embedding sustainability through your maintenance plan helps your bottom line. Federal regulations and society, through buying practices, dictate that manufacturers observe green business practices. Often times, green does not translate to Lean. However, have you considered your assets and their sustainability? A CMMS and EAM can extend the life of your physical assets through optimized maintenance programs.
Just like your air conditioner at home, changing the filter monthly, instead of every-so-often helps the compressor last longer. Establishing a proactive and preventive maintenance plan to leverage your internal resources can help pay for the many expensive trends that food and beverage manufacturers are seeing evolve in the businesses today.
It can be as simple as scheduling work orders to supply preventive maintenance to your daily critical assets, such as package assembly, or as complex as monitoring your blast chill or freeze rooms.
Most manufacturers already have processes in place to provide regular maintenance, which inherently promotes sustainability. Utilizing these best practices can improve your bottom line by improving the lifecycle of your critical assets and asset sustainability, which equals lower downtime. Having a CMMS in place for record-keeping and modernizations keeps manufacturing in FSMA compliance for reporting.
Process standardization can be your biggest ally when combating the endless void of cost.
Standardization allows you to:
A CMMS provides the ability to automate, capturing data quickly and enabling mobility as a solution. You can move your processes from a reactive state to a preventive state.
Have you considered utilizing an asset everyone carries on them all the time?
A mobile CMMS is the definition of Lean, adhering to a standard of any device, any time. The standardization of work orders saves both time and money, from the technician to procurement. If your technician can report real-time work, take pictures or videos of the asset and connect directly to inventory, manual inputs or running from building to building is removed from the wrench time equation.
A mobile CMMS should highlight everything you need to know about an asset in real-time, without data re-entry and station check-in, all with a feature-rich and configurable project application tool.
Food and beverage manufacturers have high-quality, expensive equipment across a varied supply chain.
Standardizing your inventory processes through automation shows when and where the parts are, the ability to produce purchase orders when low on parts and removes the occurrence of over purchasing. Users of this system will see the advantage in the departmental forecasting and an improved bottom line by not over-spending and storing parts that are not needed.
A CMMS can help overcome fragmented department and streamline assets through asset mapping, moving and tracking using reliable data to make informed decisions. This addition to your process is beyond lean, green and cost-effective.
Time is money in the manufacturing sector and plays a more critical part in Lean processes than ever before. Reporting is how internal departments communicate, but in some instances, it takes maintenance management away from the job at hand.
An intuitive CMMS solution provides a dashboard overview for easy access to what you want to see, the way you need to see it and to generate sharable reports. A CMMS that knows your needs and provides codeless configurations and KPI data is essential to Lean reporting. Live stream it on time, every time to those who need to know when they want it.
Here is what you should look for when choosing the right CMMS solution.
FSMA is one of the biggest challenges this industry has faced, creating many new regulations to incorporate into your process, supply chain and manufacturing. Scalability to fit these changes is essential to long-term success, both in practice and in overall cost.
By putting a CMMS and EAM together in one solution, you can grow and scale without additional implementations, without having to replace your software.
Accruent Maintenance Connection has both CMMS and EAM capabilities, all in one solution. You can utilize the different features as they fit your business, activating new ones as the need arises.
The racetrack above shows Meridian, Accruent’s engineering document solution, and how it works with Maintenance Connection for further scalability.
Meridian connects engineering plans with their history through a link in Maintenance Connection. Your technicians can see the most up-to-date drawings, submit comments and ensure that all asset maintenance is connected.
This scalability is beyond Lean in that it is integrated into your CMMS and EAM when the operations are ready. Your time to benefit is immediate, specifically in the matter of time saved. Many manufacturers are still looking at paper copies or finding the right engineer to work on an asset. Through the ALIM portal, you can share documents with engineers, managers, technicians and contractors, immediately.
Sustainability, scalability and standardization all play a role in beyond Lean, and in the end, manufacturing is integral in producing a profitable, marketable product for the food and beverage industry. A CMMS and EAM helps to squeeze the costs out of ongoing operations, giving a competitive edge through preventive maintenance practices and providing visibility into asset uptime and lifecycle. Preventive maintenance plans should be one of your beyond Lean goals.
Taking advantage of this business opportunity is crucial to planning maintenance, protecting your supply chain and reducing the risk of downtime. You can create shared value in the way business is done through data-driven management. You will also gain machine efficiency and sustainability over time through manufacturing efficiencies by integrating sustainable and scalable cost-saving processes.
Maintenance Connection provides affordable scalability and ease-of-use as both a CMMS and EAM solution and is known for its short time to benefit. It enables food and beverage manufacturers to digitize labor efficiency and asset history, while optimizing inventories through work order and scheduling maintenance management. These innovations can bring about both standardization and sustainability to your operations, providing the data you need when and where you need it.
Use our Cost Savings Calculator to forecast how much a CMMS could help you save.
See how Trinchero Family Estates, the second largest family owned winery in the US, used Maintenance Connection to save $105,000 last year through centralized vendor comparisons and inventory tracking.
Explore three IoT strategies that improve processes and efficiency using maintenance connection software.
How to configure your CMMS/EAM to optimize your food and beverage manufacturing operations, both now and in the long-term.
Explore effective facility management tips for the beverage industry with Accruent. Learn to reduce asset downtime and enhance operational efficiency.
Subscribe to stay up to date with our latest news, resources and best practices