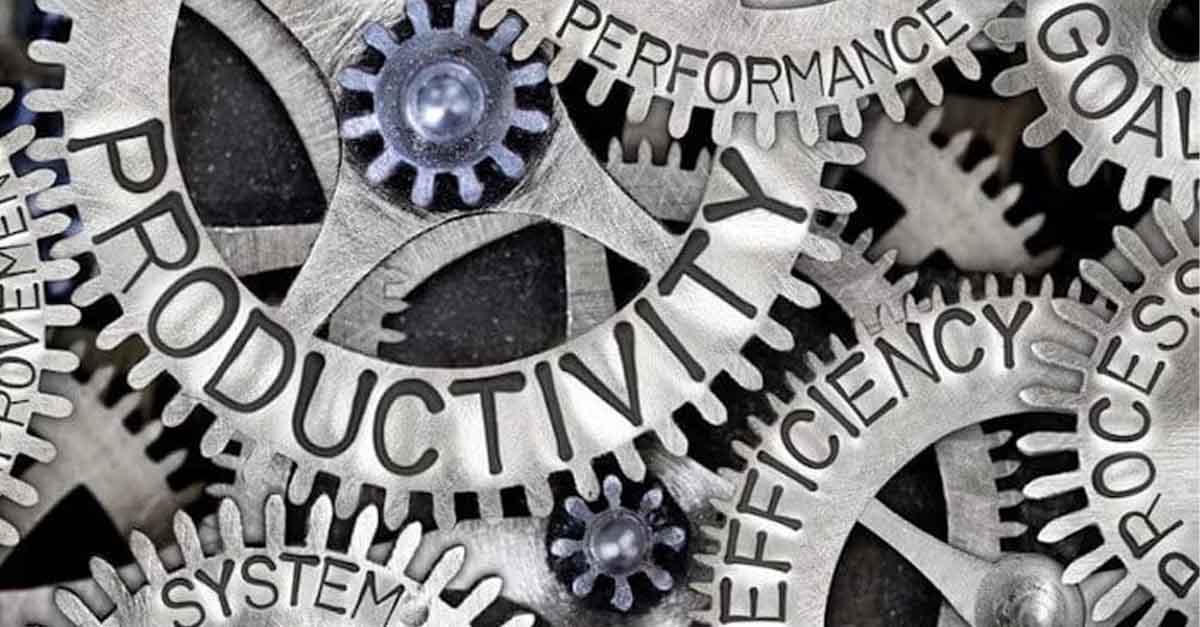
Using Your EAM to Drive Maintenance Improvement
An enterprise asset management (EAM) system can help your organization drive maintenance improvement and increase your ROI. Here's how.
Solutions
Workplace Management Solutions
Real Estate Management Solutions
Maintenance Management Solutions
Energy Management Solutions
Engineering Document Management Solutions
Asset Management Solutions
Automate campus scheduling for classes, meetings, and exams with our EMS software.
Plan and manage conferences effortlessly with EMS software to impress guests and streamline operations.
Boost workplace flexibility and maximize space use with seamless desk and room booking.
Organize workplace or campus events smoothly, creating memorable experiences.
Optimize workspace, manage allocations efficiently, and reduce costs with our space management solutions.
Deliver projects on time and within budget by improving communication, collaboration, and efficiency with our software.
Streamline lease accounting for ASC 842, IFRS, and GASB compliance.
Manage leases efficiently by tracking key dates, analyzing costs, and ensuring compliance.
Centralize data and analytics for better insights, faster negotiations, and revenue growth.
Centralize facility and asset maintenance, automate work orders, and ensure compliance with our CMMS software.
Extend asset life, reduce downtime, and prevent costly repairs with data-driven monitoring.
Prevent equipment failures and extend asset life by detecting and addressing issues early.
Make sustainable, cost-efficient energy decisions by monitoring and optimizing power consumption.
Remotely monitor and control equipment with real-time data to predict issues, boost efficiency, and reduce downtime.
Easily share and collaborate on documents, creating a single source of truth for engineers and contractors.
Manage and analyze assets across their lifecycle to schedule maintenance, reduce downtime, and extend lifespan.
Improve visibility, automate work orders, and ensure compliance for efficient facility and asset management.
Resources
Browse our full library of resources all in one place, including webinars, whitepapers, podcast episodes, and more.
Support
Looking for access to technical support, best practices, helpful videos, or training tools? You’ve come to the right place.
About Accruent
Get the latest information on Accruent, our solutions, events, and the company at large.
Explore how an enterprise management solution can benefit your organization and learn how to optimize it for your organization’s needs.
Table of contents
However, evaluating EAM solutions can be challenging and since it is not something most companies do more than a few times, it is not always obvious where or how to begin. A great place to start is with a complete analysis of your specific business needs and organizational goals. While there are many factors that lead companies to seek an EAM solution, some known contributing factors include:
The cumulative effects of these challenges are typically high maintenance costs, which an EAM solution can lower while simultaneously improving overall maintenance performance.
Organizational decision makers need to be clear on which functions are most essential for their maintenance programs before beginning their search. There are varied approaches to EAM and different vendors offer different advantages and disadvantages. The field of providers is wide, so selecting the right vendor solution will directly impact your EAM success.
You should be looking for vendors that understand your business, both in your industry and in your implementation needs. The right EAM will be a solution that increases your competitive edge and bottom line by:
The process of managing upgrades, IT infrastructure costs, overall costs and available support resources should also be evaluated in your EAM decision. Working with your chosen vendor to estimate these costs and setting reasonable expectations can help you and the vendor achieve benchmarks that show the success of an implementation and use of your new EAM solution.
How do you know what to look for and what is going to deliver the best value and highest ROI?
You need something that gives you comprehensive insight into your assets. Extending systems and equipment life for an enterprise—rather than replacing old systems and equipment—could be the key to paying for some of your other maintenance initiatives, including meeting compliance requirements and achieving greater competitiveness in a demanding business environment.
On the graphic below, you can see the common EAM function requirements on the left-hand side, while the right-side highlights common CMMS functionality requirements. The functionary wheel reflects the overall capability of Accruent Maintenance Connection to bridge the gap between these two worlds.
To maximize your return and data driven decisions, you need to fully utilize the comprehensive capabilities of your EAM. While all EAM functions are important, there are three functions that will quickly transform your maintenance performance and deliver superior results:
Maintenance Connection simplifies labor management by providing drag-and-drop calendar functionality. As an industry leading EAM, Maintenance Connection also allows for splitting task assignments within a work order, and building assignment backups into the labor system, while easily viewing resource availability.
Asset history provides clarity into assets that have unique histories and specific maintenance records associated with them. Without this information, organizations may struggle with maintenance repair times because they do not have the insights that will aid in troubleshooting. A thorough asset management solution like Maintenance Connection can act as a single source of information for all stakeholders.
Additionally, a critical part of an asset history are the drawings and documents that are associated with that piece of equipment. Accruent’s Asset Lifecycle Information Management (ALIM) solution Meridian is now accessible through a link in Maintenance Connection, enabling immediate access to current, accurate engineering documentation. Instantaneous access to the latest revision of asset documents makes maintenance technicians more efficient and promotes a safe working environment.
Inventory optimization is having the necessary parts on-hand when you need them, as spare parts are essential to a complex working environment. You want to avoid spending money on parts you do not need, and cause downtime and lost money on parts you do not have.
See how the Trinchero Family Estates uses Maintenance Connection to both fulfill their overall digital reporting and visualization needs, and those of the people doing the work.
When evaluating an EAM solution there are several non-feature factors that can significantly impact EAM success.
Ease of use is a critical aspect of an effective EAM, driving user adoption and enabling ROI. The choice you make should consider each user’s need to drive user adoption. Does it make their jobs easier, faster and better? Is the solution responsive to their day to day work life or is it adding to their load? Is it intuitive? These are important questions to answer.
Some EAM systems can require complex configuration and overcomplicate the workflow, causing user adoption to lag, particularly among less technology-proficient users. Maintenance Connection is known for its ease of use and quick user adoption, expediting benefits and ROI.
Implementation services are a necessary part of the process and can be complex since these systems become a part of your internal fabric. Many solution providers work to integrate into your current systems and have professional services to help configure your system to your needs.
Accruent is one of these solution providers, offering codeless configuration for much of our reporting with Maintenance Connection.
How should you prepare for the cost of implementation? Do you know the right questions to ask and when is the best time for you to implement?
Learn how integration can happen at many different levels with Accruent’s Blog "How to Transform Your Processes with CMMS Strategic Integrations". It can provide clarity into what can be a complex decision and will make it easier to understand. Where some vendors can take 9-12 months to implement, a full implementation of Maintenance Connection takes only weeks to months.
Ease of use and implementation circle back to cost and your bottom line. There are two points to consider in cost.
The first cost point is comes after your initial investment: what can you expect to receive and how much can you save? Visit our Cost Savings Calculator and select your industry to see what maintenance Connection can do for your company.
Second is the total cost of ownership: Has your EAM solution shown you the data you need to find cost overages, or has the lack of preventive maintenance extended the lifecycle of your assets? Do you have a clear visualization into your processes such as scheduling, work orders and inventory?
Maintenance Connection offers scalable options to best fit your organization.
For example, both cloud and on-premise versions are available. Our multi-site capabilities simplify the configuration process by enabling tagging, building id numbers for locations to add to your system as you grow. Go mobile for less wrench time and use barcodes for tracking, smart reporting and many other features providing high returns for maximum value.
The knowledge that, in the end, you will have asset management intelligence, data and asset viability tracking available when and where you need it is the light at the end of the tunnel. The data will dictate your maintenance activities and provide overall visibility, ultimately helping plan the costs of an operating asset over the entirety of its lifecycle. This lowers your operating costs, boosts ROI and brings data insight into your planning process.
Find out if Maintenance Connection is the EAM solution you are looking for by scheduling a demo today!
An enterprise asset management (EAM) system can help your organization drive maintenance improvement and increase your ROI. Here's how.
Is CMMS or EAM most appropriate for your organization? Compare use cases and features to determine which maintenance software fits your operational ...
Explore how Energy Demand Response programs can help your organization identify energy consumption trends and allow your organization to address it ...
Subscribe to stay up to date with our latest news, resources and best practices