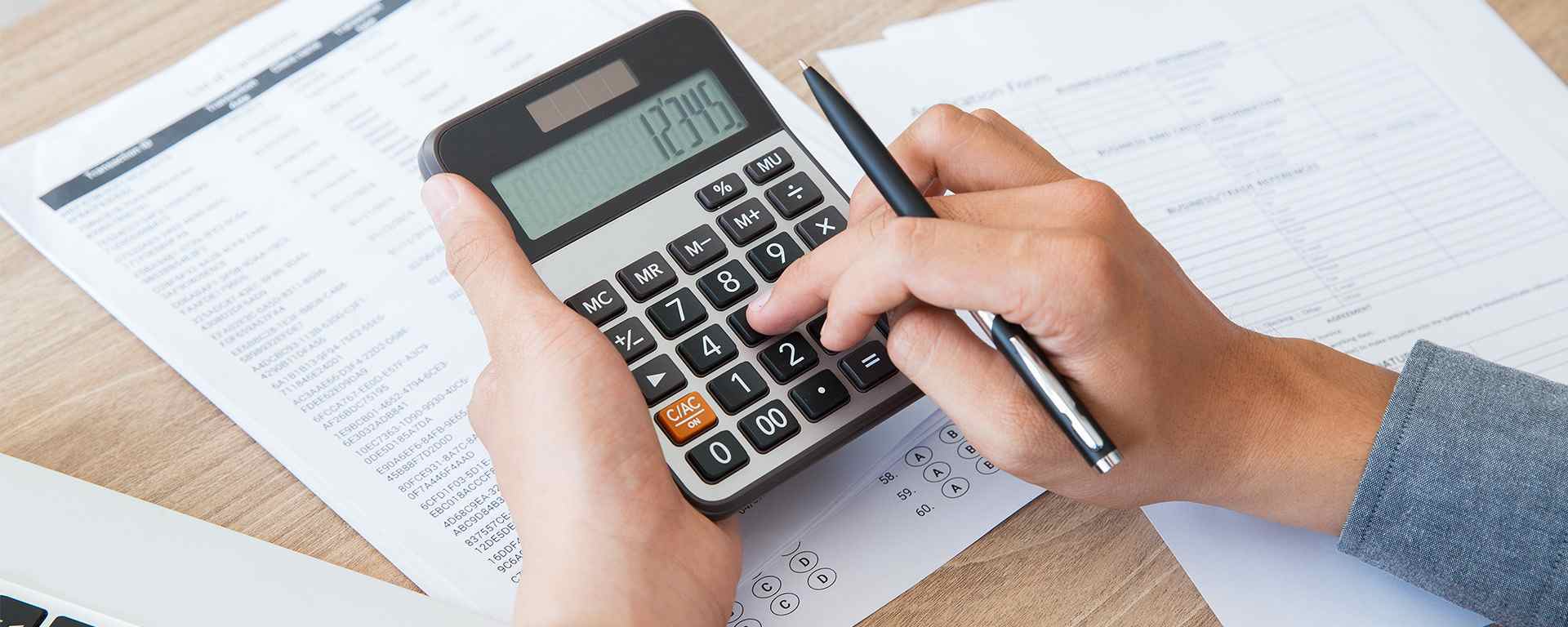
Improving Manufacturing Overall Equipment Effectiveness (OEE) with a CMMS
Looking to improve your Overall Equipment Effectiveness (OEE)? Here's how Maintenance Connection can help make that happen.
Solutions
Workplace Management Solutions
Real Estate Management Solutions
Maintenance Management Solutions
Energy Management Solutions
Engineering Document Management Solutions
Asset Management Solutions
Automate campus scheduling for classes, meetings, and exams with our EMS software.
Plan and manage conferences effortlessly with EMS software to impress guests and streamline operations.
Boost workplace flexibility and maximize space use with seamless desk and room booking.
Organize workplace or campus events smoothly, creating memorable experiences.
Optimize workspace, manage allocations efficiently, and reduce costs with our space management solutions.
Deliver projects on time and within budget by improving communication, collaboration, and efficiency with our software.
Streamline lease accounting for ASC 842, IFRS, and GASB compliance.
Manage leases efficiently by tracking key dates, analyzing costs, and ensuring compliance.
Centralize data and analytics for better insights, faster negotiations, and revenue growth.
Centralize facility and asset maintenance, automate work orders, and ensure compliance with our CMMS software.
Extend asset life, reduce downtime, and prevent costly repairs with data-driven monitoring.
Prevent equipment failures and extend asset life by detecting and addressing issues early.
Make sustainable, cost-efficient energy decisions by monitoring and optimizing power consumption.
Remotely monitor and control equipment with real-time data to predict issues, boost efficiency, and reduce downtime.
Easily share and collaborate on documents, creating a single source of truth for engineers and contractors.
Manage and analyze assets across their lifecycle to schedule maintenance, reduce downtime, and extend lifespan.
Improve visibility, automate work orders, and ensure compliance for efficient facility and asset management.
Resources
Browse our full library of resources all in one place, including webinars, whitepapers, podcast episodes, and more.
Support
Looking for access to technical support, best practices, helpful videos, or training tools? You’ve come to the right place.
About Accruent
Get the latest information on Accruent, our solutions, events, and the company at large.
How comprehensive asset intelligence, effective preventive maintenance, and efficient labor scheduling can lead to success in the chemical industry.
The chemical industry and its chemical plant maintenance are comprised of many segments with diverse and complex operations, which can make a standardized maintenance plan challenging.
Manufacturing downtime costs constitute a significant concern. For example, in a batch operation chemical plant, they typically have more frequent opportunities for a preventive maintenance program, which can provide greater flexibility for maintenance planning and labor scheduling than continuous operation facilities. Regardless of product segments or operational processes, comprehensive asset intelligence, effective preventive maintenance (PM), and efficient labor scheduling are three fundamental elements to ensure chemical industry maintenance success.
Knowing the history of equipment, and having immediate access to that information, is a vital element of an effective preventive maintenance program.
Consider a polymer process, where if the reactor agitator goes down, the polymer can harden inside the reactor within an hour or so. When the polymer hardens, it can take between two and four days to have the reactor cleaned. In addition to the cleaning and maintenance costs, all this wasted time contributes to accumulating production losses. If the prior work order history is not easily accessible and readily available, it is unlikely that maintenance technicians will be able to review it in time to get the agitator repaired quickly.
However, with a comprehensive computerized maintenance management system (CMMS) like Accruent's Maintenance Connection, the entire work order history of the agitator can be viewed quickly by technicians to troubleshoot the issue and get the agitator back into service faster. With Maintenance Connection, technicians also have easy access to maintenance and operational documents, procedures, instructions and drawings that can assist in improving repair times.
In the past, maintenance work was typically reactive. A reactive maintenance schedule, usually established manually, often lacks consideration for the capacity and availability of resources. As a result, these schedules are only followed loosely, if at all. A preventive maintenance schedule, however, assesses the availability of skills and parts and includes analytics for optimization according to Past, Present, and Future Trends in EAM and CMMS, ARC Advisory Group, December 2017. From a maintenance management perspective, having substantial asset intelligence information provides an opportunity to identify trends and shift maintenance tasks from reactive, unplanned downtime events to proactive preventive maintenance. For example, looking at the collective work order history of a particular motor, it may become evident that the motor fails after 5,000 hours of use. With this data, Maintenance Connection's preventive maintenance software can be used to deliver scheduled PM work orders based on equipment usage.
Why is this shift to a preventive maintenance plan significant? One recent report, Asset Performance Management: Blazing A Better Path to Operational Excellence, Aberdeen Group, November 2017, indicates that manufacturing companies lose $50 billion annually in unplanned downtime. When an unplanned downtime event occurs in a chemical plant during off-hours, labor costs increase because of overtime, expedited materials and equipment needed for repairs, and production loss for significant periods of time.
When equipment maintenance tasks are planned, the parts are available, the labor scheduled, and the maintenance performed more efficiently. Production downtime can also be predicted — meaning operations can potentially build product inventory levels in a way that customer shipments are still made, and production revenue losses do not occur.
One of the key challenges facing maintenance management in the chemical industry is reduced staffing to maintain aging facilities. It is critical then that labor is scheduled in a manner that maximizes efficiency and drives labor productivity.
Leveraging the asset work history within Maintenance Connection can help managers improve the accuracy of estimated repair times to fix equipment. This accuracy can aid the labor planning process as well.
Maintenance Connection's planning and scheduling CMMS software ultimately helps drive efficient labor scheduling by giving maintenance managers and schedulers:
There are many factors that can contribute to a successful maintenance plan, and the chemical industry's diversity of processes, facility sizes, etc. can make it challenging to establish an effective maintenance strategy across all assets. The cornerstone of maintenance success is a strong maintenance management software that can deliver three core benefits: comprehensive asset intelligence, effective preventive maintenance (PM), and efficient labor scheduling.
Looking to improve your Overall Equipment Effectiveness (OEE)? Here's how Maintenance Connection can help make that happen.
Explore effective facility management tips for the beverage industry with Accruent. Learn to reduce asset downtime and enhance operational efficiency.
Here's how a CMMS can help you optimize inventory management, aggregate maintenance data, and digitize your operations in the chemical industry.
Subscribe to stay up to date with our latest news, resources and best practices