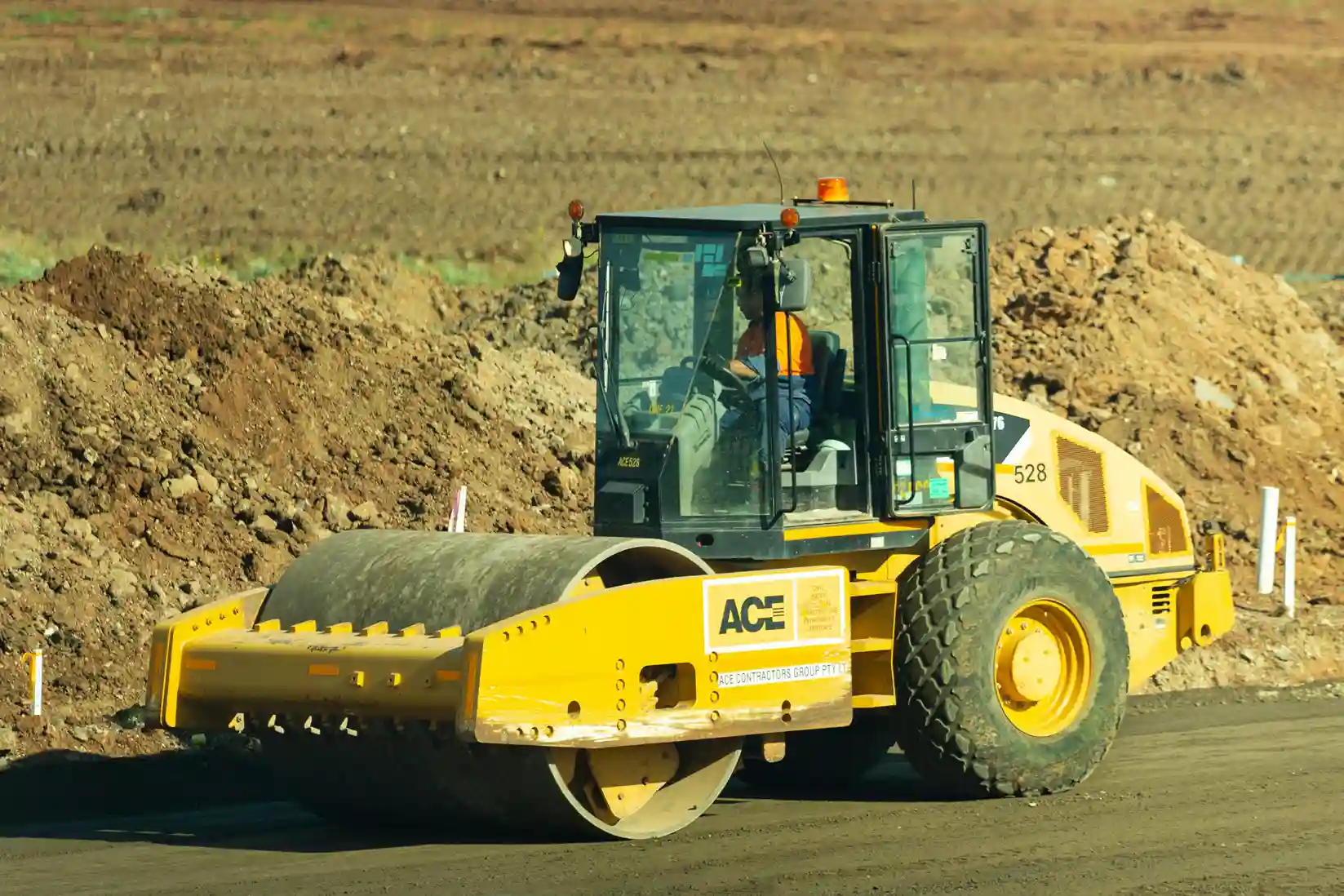
Construction Equipment Maintenance Software: Tools, Best Practices & Benefits
Discover the best construction equipment maintenance software to streamline operations, minimize downtime, and extend equipment lifespan. Learn more ...
Solutions
Workplace Management Solutions
Real Estate Management Solutions
Maintenance Management Solutions
Energy Management Solutions
Engineering Document Management Solutions
Asset Management Solutions
Automate campus scheduling for classes, meetings, and exams with our EMS software.
Plan and manage conferences effortlessly with EMS software to impress guests and streamline operations.
Boost workplace flexibility and maximize space use with seamless desk and room booking.
Organize workplace or campus events smoothly, creating memorable experiences.
Optimize workspace, manage allocations efficiently, and reduce costs with our space management solutions.
Deliver projects on time and within budget by improving communication, collaboration, and efficiency with our software.
Streamline lease accounting for ASC 842, IFRS, and GASB compliance.
Manage leases efficiently by tracking key dates, analyzing costs, and ensuring compliance.
Centralize data and analytics for better insights, faster negotiations, and revenue growth.
Centralize facility and asset maintenance, automate work orders, and ensure compliance with our CMMS software.
Extend asset life, reduce downtime, and prevent costly repairs with data-driven monitoring.
Prevent equipment failures and extend asset life by detecting and addressing issues early.
Make sustainable, cost-efficient energy decisions by monitoring and optimizing power consumption.
Remotely monitor and control equipment with real-time data to predict issues, boost efficiency, and reduce downtime.
Easily share and collaborate on documents, creating a single source of truth for engineers and contractors.
Manage and analyze assets across their lifecycle to schedule maintenance, reduce downtime, and extend lifespan.
Improve visibility, automate work orders, and ensure compliance for efficient facility and asset management.
Resources
Browse our full library of resources all in one place, including webinars, whitepapers, podcast episodes, and more.
Support
Looking for access to technical support, best practices, helpful videos, or training tools? You’ve come to the right place.
About Accruent
Get the latest information on Accruent, our solutions, events, and the company at large.
Facility management software streamlines operations by centralizing maintenance, asset tracking, and compliance processes, ensuring efficiency and cost control. This guide explores its key features and benefits, demonstrating how it enhances operational performance across industries.
Table of contents
Managing a facility without the right tools is like running a factory with outdated blueprints. Details get lost, mistakes pile up, and efficiency suffers. Unsurprisingly, 35% of facility owners struggle to keep accurate records without software.
Facility management software changes that. It simplifies maintenance, cuts costs, and helps meet compliance standards. Plant managers, operations teams, and IT specialists rely on it to bring order and efficiency to facility management. This article explains how facility management software works, its key features, and how it supports more innovative operations across industries.
Facility management software is a comprehensive digital solution designed to optimize the operations and maintenance of organizational facilities. This technology centralizes critical data and processes, enabling businesses to manage their physical assets more efficiently.
The software provides a unified platform that connects multiple aspects of facility management, from tracking equipment conditions to scheduling maintenance activities. Core functionalities include precise asset management, automated maintenance scheduling, real-time inventory control, and comprehensive compliance tracking.
This software is an essential tool for maintenance teams. In environments where machine downtime can cost thousands per minute, the ability to proactively monitor equipment, predict maintenance needs, and maintain regulatory standards can significantly impact operational performance and financial outcomes.
Optimize asset performance, reduce downtime, and maintain compliance.
Modern facility management software goes beyond simple record-keeping. It's a robust system that provides manufacturers with comprehensive tools to control, monitor, and optimize their facility operations.
These features change how maintenance teams manage equipment, shifting from reactive maintenance to a proactive strategy.
Tracking assets is more than knowing their location. This feature creates a digital fingerprint for each piece of machinery, documenting its location, current condition, repair history, and performance metrics.
Maintenance teams can instantly view equipment's entire lifecycle and make informed decisions about repairs, replacements, and resource allocation.
Unexpected equipment failures can halt production and drain budgets. Automated maintenance scheduling predicts potential issues before they occur, creating systematic inspection and preventive maintenance plans.
The software analyzes equipment performance data to recommend precise maintenance intervals, reducing unexpected breakdowns and extending machine lifespans.
Work order management centralizes maintenance tasks, creating a clear workflow for repair and maintenance activities. Teams actively track, assign, and complete tasks precisely, ensuring they address every detail and fulfill every responsibility.
Technicians receive detailed instructions, parts requirements, and priority levels, which leads to streamlined communication and accountability.
Running out of critical spare parts often means extended downtime. This feature tracks inventory levels in real-time and automatically generates purchase orders when supplies run low. Effective inventory maintenance avoids overstocking while preventing shortages that could interrupt production.
Regulatory compliance is non-negotiable in manufacturing. The software maintains detailed records of safety inspections, equipment certifications, and maintenance activities. It generates reports demonstrating adherence to industry standards, helping companies avoid fines and maintaining a safe working environment.
Data transforms guesswork into strategy. Advanced dashboards provide deep insights into maintenance costs, asset performance, and operational efficiency.
Managers can identify trends, predict future maintenance needs, and make data-driven decisions that improve overall facility performance.
Modern maintenance doesn't happen behind a desk. Cloud-based software with mobile access allows technicians to update work orders, check inventory, and access equipment histories from anywhere on the facility floor.
Real-time information means faster response times and more accurate record-keeping.
When dollars talk, managers listen. Facility management software improves operational efficiency while delivering measurable business impact on the bottom line.
Leveraging facilities management solutions can afford businesses more opportunities to focus on top-line revenue. An analytical approach can inform them when to replace a system rather than repair it, saving money in the long run.”
Facility management software optimizes maintenance schedules and tracks inventory in real-time, helping companies reduce costs, avoid emergency repairs, and more effectively manage budgets.
By implementing proactive maintenance, organizations are able to avoid emergency repairs with better planning, ultimately, reducing costs tied to downtime. As such, many companies save thousands annually by switching to proactive maintenance strategies and leveraging the features to efficiently allocate resources, and keep budgets in the green.
With computerized workflows eliminating guesswork and reducing delays, work order tracking ensures teams complete tasks on time.
Centralized data keeps everyone on the same page, streamlining communication between teams. Improved response times mean fewer interruptions, helping operations run smoothly even during high-pressure situations.
Preventive maintenance tools catch issues before they become real problems. Regular checkups and accurate tracking extend the life of machinery, reducing expensive replacements.
Facilities can rely on their assets for longer while maintaining consistent performance. The result? Less downtime, better equipment reliability, and significant cost savings over time.
Automated compliance tracking reduces risks tied to audits or violations by keeping detailed records of safety inspections, certifications, and maintenance activities. With a safer workplace, employee are more confident and the organization is able to avoid fines and interruptions.
Analytics tools provide clear insights into operational trends and potential inefficiencies. Identify where to cut costs, predict future maintenance needs, and plan upgrades.
Data-backed decisions help managers focus on what matters most. Instead of reacting to problems, you can proactively improve performance and drive long-term success.
Get Insights on maximizing savings and performance with maintenance tools.
Getting the most out of facility management software takes more than just implementation and deployment. Consistent processes and team-wide participation are critical to ensuring wide-spread adoption.
Clear guidelines help teams avoid errors and system gaps. When everyone follows the same standards, reports become more accurate, enabling faster decision-making. Well-documented records save time and reduce frustration during audits or equipment checks.
Connect your facility management software with ERP, HR, and accounting tools. Integrated systems eliminate redundancies and create a smooth flow of information across departments. This connection reduces manual data entry, saving time and reducing errors.
Set regular maintenance schedules instead of waiting for breakdowns. This simple practice reduces emergency repairs and helps equipment last longer. Teams can plan, minimize disruptions, and keep operations running smoothly without surprises.
Data helps you identify cost-saving opportunities, track performance, and improve workflows. Teams that use insights effectively can fix problems before they escalate.
Well-trained staff use tools more effectively, reducing errors and downtime. Refresher sessions help new and seasoned users stay confident and productive.
Maintenance Connection simplifies the complex demands of facility maintenance. It is designed for property managers and maintenance professionals and provides a centralized platform for managing assets, tracking work orders, and generating actionable insights.
The Computerized Maintenance Management System (CMMS) supports more innovative operations with intuitive dashboards, real-time asset tracking, and comprehensive reporting. These features simplify maintenance management, reduce costs, and improve efficiency.
Key Features and Attributes:
Effective facility maintenance starts with the right tools. Maintenance Connection drives efficiency, reduces costs, and keeps operations running smoothly. Explore these capabilities today. Schedule a demo or consultation to see how better maintenance management can support long-term success.
Here are common questions about facility management software.
Facility management software centralizes operations across locations. It provides real-time access to each site's maintenance schedules, asset data, and compliance records. This unified view improves coordination, simplifies reporting, and allows teams to monitor performance and address issues efficiently, regardless of the number of sites involved. Facility management software centralizes operations across locations. It provides real-time access to each site's maintenance schedules, asset data, and compliance records. This unified view improves coordination, simplifies reporting, and allows teams to monitor performance and address issues efficiently, regardless of the number of sites involved.
Yes, many solutions offer features tailored to industry-specific needs. For manufacturing, this includes preventive maintenance tools and compliance tracking. Healthcare facilities may prioritize safety protocols and asset tracking for medical equipment. Customization options ensure the software supports unique workflows and regulatory requirements across different sectors.
Facility management software uses analytics to highlight inefficiencies, such as equipment downtime or overstocked inventory. Report insights help reduce unnecessary expenses, optimize maintenance schedules, and improve resource allocation. Over time, these adjustments lead to significant cost savings while maintaining high operational standards.
Discover the best construction equipment maintenance software to streamline operations, minimize downtime, and extend equipment lifespan. Learn more ...
Explore key factors to find the best CMMS software for manufacturing and elevate your facility's maintenance efficiency and productivity to the next ...
Discover the importance of equipment maintenance, explore best practices, and find the right software solutions. Optimize your maintenance strategy ...
Subscribe to stay up to date with our latest news, resources and best practices