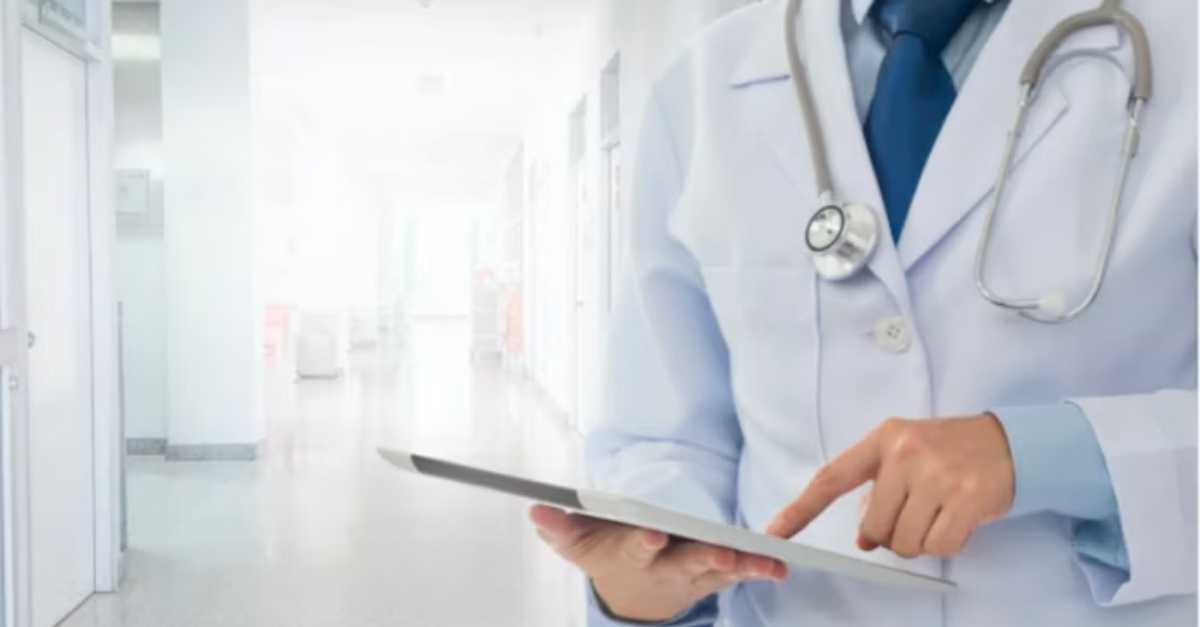
How to Improve Healthcare Facilities and Plant Operations Management with a Modern CMMS
If you're using an outdated healthcare CMMS, you could be costing your business more than you know. Here's why having the right tech matters.
Solutions
Workplace Management Solutions
Real Estate Management Solutions
Maintenance Management Solutions
Energy Management Solutions
Engineering Document Management Solutions
Asset Management Solutions
Automate campus scheduling for classes, meetings, and exams with our EMS software.
Plan and manage conferences effortlessly with EMS software to impress guests and streamline operations.
Boost workplace flexibility and maximize space use with seamless desk and room booking.
Organize workplace or campus events smoothly, creating memorable experiences.
Optimize workspace, manage allocations efficiently, and reduce costs with our space management solutions.
Deliver projects on time and within budget by improving communication, collaboration, and efficiency with our software.
Streamline lease accounting for ASC 842, IFRS, and GASB compliance.
Manage leases efficiently by tracking key dates, analyzing costs, and ensuring compliance.
Centralize data and analytics for better insights, faster negotiations, and revenue growth.
Centralize facility and asset maintenance, automate work orders, and ensure compliance with our CMMS software.
Extend asset life, reduce downtime, and prevent costly repairs with data-driven monitoring.
Prevent equipment failures and extend asset life by detecting and addressing issues early.
Make sustainable, cost-efficient energy decisions by monitoring and optimizing power consumption.
Remotely monitor and control equipment with real-time data to predict issues, boost efficiency, and reduce downtime.
Easily share and collaborate on documents, creating a single source of truth for engineers and contractors.
Manage and analyze assets across their lifecycle to schedule maintenance, reduce downtime, and extend lifespan.
Improve visibility, automate work orders, and ensure compliance for efficient facility and asset management.
Resources
Browse our full library of resources all in one place, including webinars, whitepapers, podcast episodes, and more.
Support
Looking for access to technical support, best practices, helpful videos, or training tools? You’ve come to the right place.
About Accruent
Get the latest information on Accruent, our solutions, events, and the company at large.
If you're running on outdated legacy maintenance solutions, it can create downtime, impact workflows and more. Here's when it might be time to switch.
Table of contents
You know the benefits of preventive maintenance (and maybe even predictive maintenance) first hand.
How? Your facility has a computerized maintenance management system (CMMS) in place to help reduce downtime and organize workflows. However, like most technology, your maintenance software may become outdated — which can cost you in the long run.
Often your CMMS will become outdated for two reasons:
If you asked the vendor about its product’s evolution before implementing, you likely already know how conscientious the vendor is about market trends and changes. If not, you can find this information by checking recent product updates or feature releases mentioned in the vendor’s PR (public relations) announcements, on community forums, or on social channels like Facebook and Twitter.
Frequently, when an organization undergoes a major change — like business growth, a mass hiring or a facility upgrade — it will outgrow the technology it’s currently using. Some maintenance solutions can scale to meet the changing demands of the business. However, this isn’t always the case, forcing some businesses to choose a new solution altogether.
Though these two reasons are usually clear to see, it’s not always apparent that your maintenance solution is falling behind. This can set your maintenance ROI on an unexpected downturn. Here are five signs that will let you know it’s time to replace your maintenance solution.
Most modern business solutions offer real-time analytics to easily create status reports and make quick decisions. This is no different in the maintenance industry.
Today, many maintenance solutions allow managers and technicians to track and check various facility and equipment metrics such as failure codes, inventory, equipment status levels, completed work orders and more. Without real-time visibility, it’s hard to make quick decisions to keep everything at peak efficiency. But more importantly, you may be risking the health of your equipment or the safety of your technicians.
If you have a maintenance solution, you probably already track the warranties, inspections, routine maintenance and repair history of your equipment. However, if keeping up with compliance codes and industry regulations is more of a manual process, you may consider replacing your maintenance solution.
Many CMMSs can automate most compliance tasks by setting notifications, scheduling routine maintenance, tracking a repair history log and organizing important documents (e.g., equipment manuals, spec sheets, ID tags) for each of your assets. This won’t only save facility managers time and boost compliance rates, it will also make inspections and audits a breeze since everything is documented and easily accessible.
When technicians use paper forms on the floor or in the field, and then come back to the office to input all the data digitally, it’s a sign your maintenance solution needs an upgrade.
Doubling up with paper processes not only causes redundant work for technicians, it also wastes valuable time and resources since the rest of the team is working with outdated data. Upgrading to a cloud-based maintenance solution will allow everyone to have access to necessary information when they need it. Taking this one step further, having a mobile CMMS will allow technicians to check and update data with smartphones, tablets and other mobile devices, anytime, anywhere.
How your organization manages work orders can make or break your whole maintenance operation. If you notice that your work orders are getting backed up, it’s probably time to look into a new CMMS.
When your work orders are falling behind, usually it’s a sign that the current workflow is insufficient or the necessary data isn’t accessible until it’s too late. Many modern CMMSs serve as central hubs for asset management, inventory management, work order management and preventive maintenance management, so managers and technicians alike can make sure all the necessary parts, time and equipment are available to finish a work order.
Usually, a maintenance solution can integrate with other business systems you use, such as property management or accounting software. These integrations allow you to make maintenance decisions that better serve the whole business.
If your CMMS doesn’t have native integrations, check to see if there is a flexible application program interface (API) available. This will allow your organization to create custom integrations with your current business applications.
However, if both avenues are extremely limited or nonexistent, you may consider looking at a different maintenance solution for your team.
Sometimes a CMMS that was great to start with doesn’t have the ability to hold up after major business changes. Keeping an eye out for these signs will make it more apparent when you need to replace your maintenance solution.
Author Bio: Elizabeth Mazenko is an editor with Better Buys, a trusted source of maintenance software news and research. Follow her at @ElizMazenko for more on enterprise software and related technology research.
If you're using an outdated healthcare CMMS, you could be costing your business more than you know. Here's why having the right tech matters.
Still trying to differentiate between CMMS, EAM, and CAFM systems? Here are the key distinctions, and how to find the best tool for your business.
Discover the roles of capital planning and computerized maintenance management systems and how to integrate them into your organization.
Subscribe to stay up to date with our latest news, resources and best practices