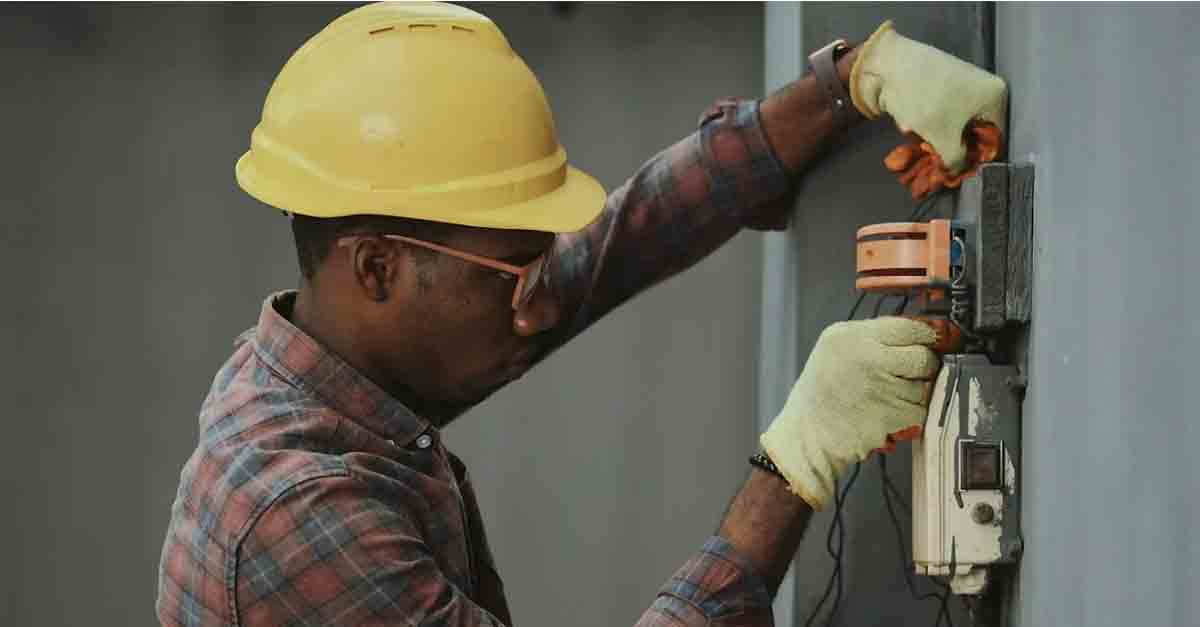
Maintenance Scheduling: Best Practices, Benefits & Software
Discover the best practices, benefits, and software solutions for effective maintenance scheduling. Essential insights for manufacturing ...
Solutions
Workplace Management Solutions
Real Estate Management Solutions
Maintenance Management Solutions
Energy Management Solutions
Engineering Document Management Solutions
Asset Management Solutions
Automate campus scheduling for classes, meetings, and exams with our EMS software.
Plan and manage conferences effortlessly with EMS software to impress guests and streamline operations.
Boost workplace flexibility and maximize space use with seamless desk and room booking.
Organize workplace or campus events smoothly, creating memorable experiences.
Optimize workspace, manage allocations efficiently, and reduce costs with our space management solutions.
Deliver projects on time and within budget by improving communication, collaboration, and efficiency with our software.
Streamline lease accounting for ASC 842, IFRS, and GASB compliance.
Manage leases efficiently by tracking key dates, analyzing costs, and ensuring compliance.
Centralize data and analytics for better insights, faster negotiations, and revenue growth.
Centralize facility and asset maintenance, automate work orders, and ensure compliance with our CMMS software.
Extend asset life, reduce downtime, and prevent costly repairs with data-driven monitoring.
Prevent equipment failures and extend asset life by detecting and addressing issues early.
Make sustainable, cost-efficient energy decisions by monitoring and optimizing power consumption.
Remotely monitor and control equipment with real-time data to predict issues, boost efficiency, and reduce downtime.
Easily share and collaborate on documents, creating a single source of truth for engineers and contractors.
Manage and analyze assets across their lifecycle to schedule maintenance, reduce downtime, and extend lifespan.
Improve visibility, automate work orders, and ensure compliance for efficient facility and asset management.
Resources
Browse our full library of resources all in one place, including webinars, whitepapers, podcast episodes, and more.
Support
Looking for access to technical support, best practices, helpful videos, or training tools? You’ve come to the right place.
About Accruent
Get the latest information on Accruent, our solutions, events, and the company at large.
Discover the fundamentals of scheduled maintenance and how it drives operational efficiency in manufacturing and beyond. Learn about its benefits, best practices, and how maintenance software can automate scheduling, improve reliability, and reduce costs. Explore actionable strategies to streamline equipment care and ensure consistent performance across your operations.
Table of contents
In 2024, 37% of businesses still used spreadsheets or other manual methods to track and handle maintenance management needs. Scheduled maintenance, a systematic approach to equipment care, is essential in manufacturing for operational continuity and efficiency.
Companies can significantly improve equipment reliability and uptime by shifting from manual tracking to structured, proactive maintenance strategies.
Scheduled maintenance is the routine, predetermined tasks performed on equipment to prevent breakdowns and extend its life. As a form of maintenance management, it is planned maintenance based on time intervals, usage metrics, or other measurements. This proactive approach differs from reactive maintenance, which addresses problems only after they occur, and condition-based maintenance, where actions are triggered by real-time equipment conditions, not a set timetable.
Adhering to a regular schedule allows businesses to manage maintenance resources better and minimize disruptions. Scheduled maintenance is a foundational element in effective asset management strategies. It optimizes uptime by ensuring consistent performance across facilities.
Scheduled and planned maintenance are proactive strategies but differ in approach and flexibility. Scheduled maintenance is strictly time-based and follows a fixed calendar regardless of equipment condition. This regularity helps predict and allocate resources efficiently, but it can sometimes lead to unnecessary maintenance actions if the equipment is still in optimal condition.
Conversely, planned maintenance, though prearranged, adapts to current equipment conditions. It is task-oriented and often adjusted based on equipment performance and condition monitoring. This flexibility can reduce unnecessary interventions and more effectively focus resources on pressing needs.
The impact on operations varies between the two. Scheduled maintenance helps with consistency and reliability through regular checks. It can reduce downtime by preventing unexpected failures. Planned maintenance impacts operations by enabling more targeted and efficient use of resources, which can minimize disruptions and better align maintenance activities with operational priorities.
Download the Free Maintenance KPIs Guide to track performance, improve operations, and keep your maintenance strategy on point.
Scheduled maintenance is an integral part of manufacturing. Like preventive maintenance, it offers several benefits that improve operations. The systematic approach ensures machinery runs smoothly while managing compliance and control costs through resource management.
Overall, unplanned downtime costs industrial manufacturers as much as $50 billion a year.”
-Forbes
Regular maintenance ensures equipment consistently operates at peak performance, vital for minimizing unexpected failures. Proactively addressing wear and tear prolongs machinery's usable life. Scheduling repairs during off-peak hours also reduces operational disruptions.
A rigorous maintenance schedule diminishes the likelihood of equipment malfunctions that could lead to workplace incidents, protecting workers from accidents. Regular checks and balances help maintain compliance with safety standards and regulations, boosting worker confidence and fostering a safer working environment.
Addressing maintenance issues before they escalate into something more severe can significantly reduce expensive repairs and replacements. Scheduled maintenance promotes better planning and utilization of resources. It allows for more predictable and manageable maintenance budgeting.
Make decisions based on facts and data, not feelings. Scheduled maintenance produces valuable data that can be analyzed. Tracking performance trends over time helps optimize the frequency and process of maintenance activities. This strategic use of data means better planning for future investments and continuous improvement in maintenance practices.
Implementing our best practices will help you realize scheduled maintenance's full potential and value. These guidelines are designed to streamline processes, enhance safety, and optimize resource use in manufacturing environments.
A well-structured maintenance plan is the cornerstone of effective scheduled maintenance. It should detail all the necessary tasks, the frequencies of each task, and assign responsibilities. This plan ensures the comprehensive coverage of all equipment, helps mitigate the risk of oversight, and improves machine longevity.
Incorporating maintenance scheduling software is critical for automating maintenance management. Such technology facilitates timely reminders and comprehensive tracking of maintenance activities. Utilizing this technology leads to systematic execution and accountability.
Maintenance efficiency heavily relies on the preparedness of the personnel involved. Thorough training on equipment requirements and providing the appropriate tools are crucial for success. This fosters a safe environment for the effective execution of maintenance tasks.
Regularly reviewing the maintenance program’s effectiveness through equipment performance data and team feedback allows for timely adjustments. This helps manufacturers meet their customers' increasing demands and keep up with industry best practices.
But where do you start with a maintenance schedule? We have developed a structured step-by-step how-to guide to help you create a plan.
Begin by cataloging all equipment and assets. Note key details such as make and model and their importance to operations. This comprehensive inventory serves as the foundation for all subsequent maintenance planning.
Assess each asset's maintenance needs. Use manufacturer recommendations and historical maintenance data to inform these decisions. This step is essential for understanding the specific care each piece of equipment requires to remain in the best possible condition.
Evaluate and rank maintenance tasks based on the importance of each piece of equipment and the potential impact of its failure. Prioritization helps focus resources on the most significant areas. Detailed organization is how to keep systems in peak condition.
Develop a detailed timeline for carrying out maintenance tasks. Consider the big picture — both the workload and operational demands. A well-planned schedule minimizes downtime by aligning maintenance activities with lower production periods.
After implementation of the maintenance schedule, continuously monitor its effectiveness. Stay flexible and ready to adjust the schedule based on real-time feedback and performance data. Adaptbased on evolving operational needs or unexpected issues.
Maintenance management software integrates advanced automation and data analysis. When properly utilized, it profoundly impacts the overall efficiency of scheduled maintenance.
Here are a few ways the software can help improve scheduled maintenance operations.
Accruent Maintenance Connection is a computerized maintenance management system (CMMS) designed to streamline the complexities of scheduled maintenance. The robust platform supports a wide array of maintenance activities. It’s become an indispensable tool for improving overall reliability and efficiency for many businesses.
Here are some of the key features of Maintenance Connection:
Maintenance Connection is versatile enough to serve various industries, including manufacturing, healthcare, education, utilities, and mining. For manufacturing professionals, plant managers, and production supervisors, it offers benefits such as reducing costs associated with equipment downtime while extending asset life. It also helps improve regulatory compliance through better record-keeping and consistent maintenance practices.
Integrating Maintenance Connection into operations means organizations can achieve a more streamlined, cost-effective, and efficient maintenance process. It can significantly boost overall productivity and safety.
Stay ahead by staying organized. A CMMS like Maintenance Connection can be a transformative tool for various industries. It helps businesses maximize equipment efficiency, ensure safety, and control costs. Taking a proactive approach leads to asset longevity and can boost overall productivity.
Want to learn more? Contact Accruent to discuss how the software can work for you.
Here are common questions about scheduled maintenance.
Scheduled maintenance prevents unexpected equipment failures by deploying regular checks and balances, thus reducing costly emergency repairs and downtime. Planning maintenance during off-peak hours minimizes disruption to operations, improving productivity and operational efficiency.
An example of scheduled maintenance is the quarterly servicing of HVAC systems in a manufacturing plant. Filters are replaced, and system functionality is checked to prevent breakdowns. This routine care helps extend the equipment's lifespan and enhances the performance potential.
A maintenance schedule is a timetable for performing maintenance tasks on equipment and machinery. It details when each maintenance activity should occur, based on factors like operational hours and manufacturer recommendations, to keep equipment in the best condition possible and prevent breakdowns.
Discover the best practices, benefits, and software solutions for effective maintenance scheduling. Essential insights for manufacturing ...
Master routine maintenance with our comprehensive guide designed for facility management. Learn how to optimize your strategies for peak operational ...
Learn how to develop a robust preventive maintenance program. Explore step-by-step guidelines and expert tips to streamline maintenance operations.
Subscribe to stay up to date with our latest news, resources and best practices