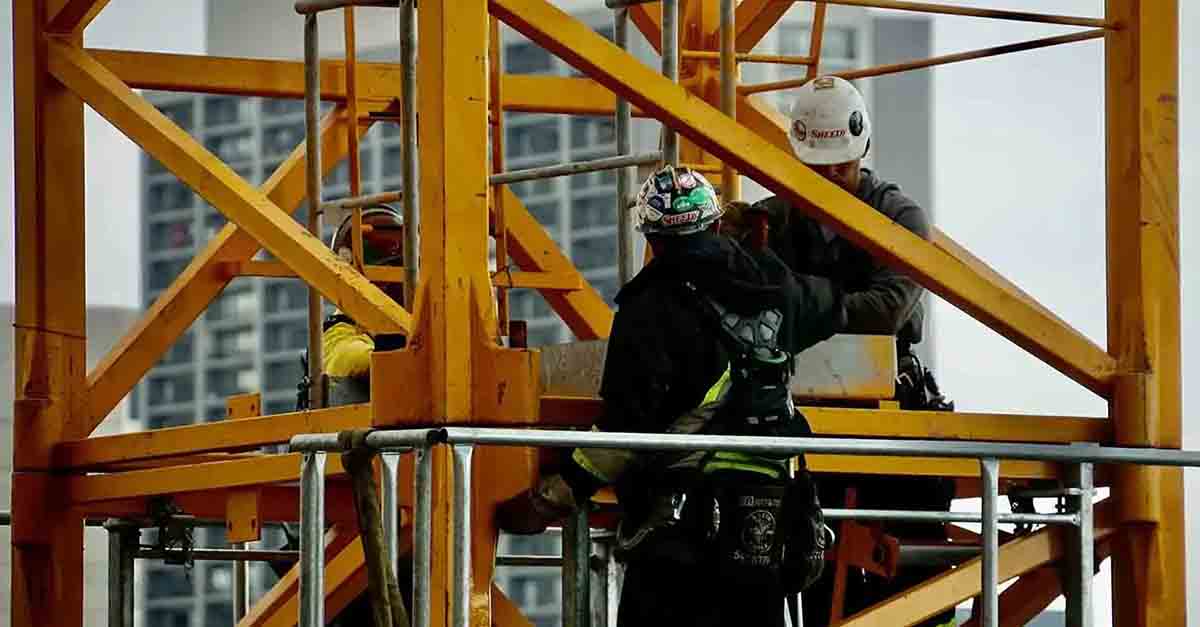
How To Develop A Preventive Maintenance Program
Discover the key steps to creating an effective preventive maintenance program. This practical guide is designed to help you establish a routine that ...
Solutions
Solutions
Workplace Management Solutions
Real Estate Management Solutions
Maintenance Management Solutions
Energy Management Solutions
Engineering Document Management Solutions
Asset Management Solutions
Automate campus scheduling for classes, meetings, and exams with our EMS software.
Plan and manage conferences effortlessly with EMS software to impress guests and streamline operations.
Boost workplace flexibility and maximize space use with seamless desk and room booking.
Organize workplace or campus events smoothly, creating memorable experiences.
Optimize workspace, manage allocations efficiently, and reduce costs with our space management solutions.
Deliver projects on time and within budget by improving communication, collaboration, and efficiency with our software.
Streamline lease accounting for ASC 842, IFRS, and GASB compliance.
Manage leases efficiently by tracking key dates, analyzing costs, and ensuring compliance.
Centralize data and analytics for better insights, faster negotiations, and revenue growth.
Centralize facility and asset maintenance, automate work orders, and ensure compliance with our CMMS software.
Extend asset life, reduce downtime, and prevent costly repairs with data-driven monitoring.
Prevent equipment failures and extend asset life by detecting and addressing issues early.
Make sustainable, cost-efficient energy decisions by monitoring and optimizing power consumption.
Remotely monitor and control equipment with real-time data to predict issues, boost efficiency, and reduce downtime.
Easily share and collaborate on documents, creating a single source of truth for engineers and contractors.
Manage and analyze assets across their lifecycle to schedule maintenance, reduce downtime, and extend lifespan.
Improve visibility, automate work orders, and ensure compliance for efficient facility and asset management.
Resources
Browse our full library of resources all in one place, including webinars, whitepapers, podcast episodes, and more.
Support
Looking for access to technical support, best practices, helpful videos, or training tools? You’ve come to the right place.
About Accruent
Get the latest information on Accruent, our solutions, events, and the company at large.
Dive into the essentials of routine maintenance with our in-depth guide tailored for facility managers in the manufacturing sector. This resource offers strategic insights into leveraging CMMS solutions to maintain operational excellence and extend asset longevity.
Table of contents
The cost of downtime in modern manufacturing costs businesses over $50 billion per year. This startling statistic highlights the serious need for effective maintenance strategies. By implementing a routine maintenance strategy, facilities will prevent expensive halts in production while improving the lifespan of their machinery.
This guide focuses on how to implement routine maintenance. Here, we explore key benefits, practical examples from various industries, and the advanced tools available.
Routine maintenance is a form of maintenance management that uses regular, scheduled activities designed to prevent equipment failure and maintain smooth system operations. Unlike reactive maintenance — which addresses problems after they occur — routine maintenance takes a proactive approach. The goal is to successfully maintain equipment with the goal of both functionality and extending its lifespan.
Typical tasks in routine maintenance include cleaning, inspections, and conducting minor repairs. These small, regular measures add up and help prevent unexpected equipment failures while reducing downtime.
In 2024, the average manufacturer faces 800 hours of equipment downtime per year (more than 15 hours per week). Companies must take proactive approaches to avoid these unfortunate costs.
Routine maintenance is fundamental to maintaining the longevity and reliability of machinery, infrastructure, and even personal habits. Consistently following a maintenance schedule helps individuals and organizations experience significant benefits, such as the following five:
Protect team members and foster a culture of safety among employees. Routine maintenance minimizes the risk of malfunctions that can lead to accidents or hazardous situations. Regular checks and repairs keep equipment running safely while adhering to safety standards and regulations to avoid any potential legal issues.
Avoid unnecessary expenses. By identifying and addressing small issues early, regular maintenance prevents expensive, large-scale repairs down the line. Regular upkeep prolongs the functional lifespan of equipment while improving its performance. The equipment then runs smoother which can also result in significant savings on energy costs, as well.
Achieve peak performance and get the full value out of investments. Well-maintained equipment and systems are more likely to operate at their best efficiency. This consistent level of maintenance reduces the likelihood of unexpected breakdowns that disrupt productivity. It also means that the quality of output from machinery stays at the highest level.
Take advantage of what assets can offer in the long term. Maintaining equipment regularly preserves the asset’s value. Well-kept assets tend to retain a higher resale value over time and depreciate at a slower rate. Further, a well-maintained portfolio is often more attractive to potential investors or buyers. It is a win for the market value.
Know the value of assets and plan accordingly. Routine maintenance schedules help for more precise budgeting and resource allocation. The clear timelines help improve scheduling while minimizing the impact on daily operations. Predictability means all parties involved have confidence in the stability and reliability of the assets.
Routine maintenance is integral across various industries. Here, we highlight examples from manufacturing, healthcare, and oil & gas sectors to highlight the value of regular upkeep.
In manufacturing, routine maintenance supports continuous production line operations. Machinery calibration is conducted regularly to maintain operation standards and product quality. Conveyor belt inspections help avert breakdowns that could stop production.
Preventive equipment maintenance includes scheduled downtime for machinery servicing, such as replacing parts before they fail and keeping machines running smoothly.
Meanwhile, in healthcare, the goal is both optimized operations and patient safety. Routine maintenance focuses on medical devices like MRI machines and ventilators, so they function properly and accurately when needed.
This includes regular servicing and calibration while sterilization systems are checked routinely to prevent infection and cross-contamination. Also, heating, cooling, and ventilation systems maintenance is necessary to sustain a sterile and safe environment.
The oil and gas industry depends on routine maintenance for safety and efficiency. Pipeline integrity management involves regular inspections and maintenance to prevent leaks and environmental hazards.
Scheduled servicing of drilling equipment reduces the risk of malfunctions and interruptions. Safety and emergency systems undergo frequent testing, including checks on safety valves and emergency shutoff systems, to confirm their ability to handle incidents.
The concepts of routine maintenance and preventive maintenance may sound similar, but they serve different purposes and use distinct approaches.
Routine maintenance consists of regular, often straightforward tasks such as cleaning and minor adjustments to keep equipment running smoothly. This type of maintenance is typically scheduled based on time or usage and focuses on staying at current operational standards. Think of it as like a car getting an oil change.
In contrast, preventive maintenance is more comprehensive and proactive. It is designed to anticipate and prevent potential equipment failures before they occur. This approach includes detailed inspections, parts replacements, or even system overhauls.
Preventive maintenance software builds schedules based on predictive analysis and recommendations from equipment manufacturers. The goal is to identify and resolve issues that may disrupt operations if left unaddressed, like inspecting and replacing a battery in a car before a long road trip.
A routine maintenance schedule is necessary for any operation that relies on machinery, equipment, or infrastructure. Here are key steps to put such a strategy into place:
Begin by cataloging all equipment and assets that require maintenance. Assess the maintenance needs for each item based on the manufacturer's guidelines or past performance data. Develop a comprehensive maintenance calendar that schedules each task at optimal times to minimize disruption to workflows.
Then, to ensure consistency and completeness in maintenance tasks, create detailed checklists for each one. Establish standard operating procedures (SOPs) for common maintenance activities to maintain quality across all operations. Document all maintenance activities thoroughly for tracking purposes and future planning.
Make sure the team has clear directions. Provide the necessary tools and resources to perform maintenance tasks safely and effectively. Additionally, set up support systems like help desks or technical support to assist with complex maintenance issues.
Start executing the maintenance schedule. Prioritizing the most important assets first. Regularly monitoring compliance means that maintenance tasks are performed as scheduled and meet the required standards. Use the data collected from these checks to adjust the maintenance schedule and procedures as needed.
Build towards an effective future. Encourage ongoing feedback from teams to identify any challenges or areas for improvement. Periodically review the entire maintenance process to find opportunities. Continuously update training programs to keep maintenance skills relevant and effective.
A Computerized Maintenance Management System (CMMS) is a powerful software platform designed to improve the management of maintenance operations within organizations.
Through centralized data management, CMMS software consolidates all maintenance-related data, including maintenance schedules, equipment history, and inventory levels. The single database simplifies access for all stakeholders. It helps foster a culture of quick decision-making based on data not instinct, while tracking maintenance activities and outcomes.
Then, the system streamlines routine maintenance tasks by automating scheduling and alerts. It alerts relevant personnel when maintenance is due or inventory levels are low. This automation means maintenance activities and handyman services are carried out on time. The goal is to maintain continuous operation by preventing equipment downtime.
From a data perspective, CMMS offers robust reporting and analysis tools that help managers analyze operations, spot trends, and make informed, data-driven decisions. These insights help in understanding costs, performance, and team productivity. The takeaways can build towards a more refined future that builds towards better results.
Accruent's Maintenance Connection is a leading CMMS software that stands out due to its ability to streamline maintenance operations across a diverse range of industries. From manufacturing to healthcare, and from educational facilities to large utilities, Maintenance Connection provides a robust platform that supports maintenance professionals, plant managers, production supervisors, and facility managers by improving their maintenance procedures.
By implementing this maintenance management software, organizations can significantly improve efficiency, reduce operational costs, and extend the lifespan of critical assets. Here are some of the key features of Maintenance Connection:
Through these features, Maintenance Connection supports a variety of sectors by maintaining high standards. This CMMS tool facilitates daily maintenance tasks while contributing to strategic planning and long-term asset management.
Routine maintenance includes regular, scheduled tasks to keep equipment and systems operating at the highest level. These tasks can range from cleaning, lubricating, and making minor adjustments to conducting inspections and minor repairs. The goal is to maintain the current functioning state of the equipment.
Routine maintenance refers to regular tasks that keep systems running smoothly. Meanwhile, scheduled maintenance is typically more comprehensive and may involve detailed inspections and replacements planned at specific intervals. Scheduled maintenance is often based on manufacturer recommendations or legal requirements and is more structured than routine maintenance.
The three basic methods of routine maintenance are visual inspection, cleaning, and lubrication. Visual inspections are simply checking equipment for any obvious issues that could lead to failure. Cleaning is important to prevent buildup that could damage operations. Lubrication focuses on moving parts operating smoothly without excessive wear or friction.
Discover the key steps to creating an effective preventive maintenance program. This practical guide is designed to help you establish a routine that ...
Discover the essential strategies for achieving maintenance management excellence in the manufacturing industry. Learn how to leverage maintenance ...
Discover the essentials of maintenance scheduling, from industry-recommended best practices to the tangible benefits and innovative software that ...
Subscribe to stay up to date with our latest news, resources and best practices