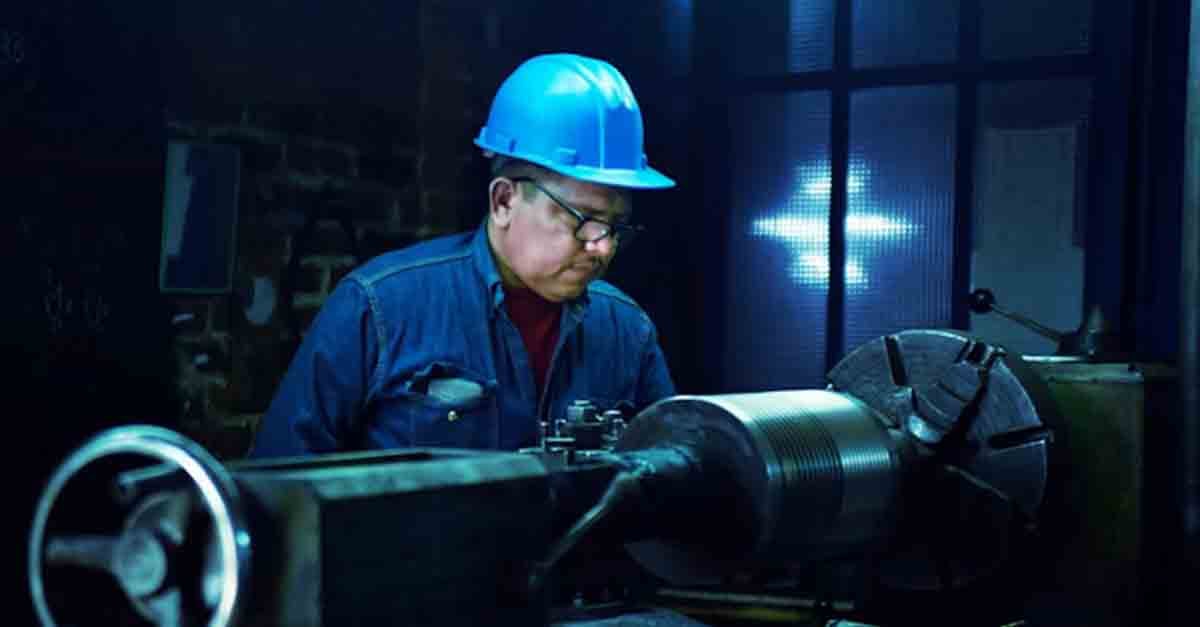
Maintenance Management: 7 Key Strategies for Success
Discover the meaning and secrets to successful maintenance management in 2024. Explore strategies to cut maintenance costs and boost operational ...
Solutions
Workplace Management Solutions
Real Estate Management Solutions
Maintenance Management Solutions
Energy Management Solutions
Engineering Document Management Solutions
Asset Management Solutions
Automate campus scheduling for classes, meetings, and exams with our EMS software.
Plan and manage conferences effortlessly with EMS software to impress guests and streamline operations.
Boost workplace flexibility and maximize space use with seamless desk and room booking.
Organize workplace or campus events smoothly, creating memorable experiences.
Optimize workspace, manage allocations efficiently, and reduce costs with our space management solutions.
Deliver projects on time and within budget by improving communication, collaboration, and efficiency with our software.
Streamline lease accounting for ASC 842, IFRS, and GASB compliance.
Manage leases efficiently by tracking key dates, analyzing costs, and ensuring compliance.
Centralize data and analytics for better insights, faster negotiations, and revenue growth.
Centralize facility and asset maintenance, automate work orders, and ensure compliance with our CMMS software.
Extend asset life, reduce downtime, and prevent costly repairs with data-driven monitoring.
Prevent equipment failures and extend asset life by detecting and addressing issues early.
Make sustainable, cost-efficient energy decisions by monitoring and optimizing power consumption.
Remotely monitor and control equipment with real-time data to predict issues, boost efficiency, and reduce downtime.
Easily share and collaborate on documents, creating a single source of truth for engineers and contractors.
Manage and analyze assets across their lifecycle to schedule maintenance, reduce downtime, and extend lifespan.
Improve visibility, automate work orders, and ensure compliance for efficient facility and asset management.
Resources
Browse our full library of resources all in one place, including webinars, whitepapers, podcast episodes, and more.
Support
Looking for access to technical support, best practices, helpful videos, or training tools? You’ve come to the right place.
About Accruent
Get the latest information on Accruent, our solutions, events, and the company at large.
Explore the essentials of equipment maintenance, from its fundamental purpose to best practices that optimize machinery performance and longevity. Learn how to implement proactive strategies to reduce downtime, extend equipment lifespan, and boost reliability in industrial operations.
Table of contents
Unplanned downtime costs manufacturers over $50 billion a year. Avoid being part of that statistic by implementing a proactive equipment maintenance strategy. When crafted correctly, this strategy saves money and boosts overall production reliability. The goal is to extend equipment lifespan, improve machine availability, and reduce the risk of sudden failures that disrupt production schedules.
Cut costs and reduce failures with a proactive maintenance strategy
Equipment maintenance is the systematic upkeep, inspection, and repair of industrial machinery to maintain optimal performance and prevent failures. The proactive approach is fundamental to sustaining high operational standards in manufacturing settings. The primary objectives of a maintenance strategy are to extend the machinery's lifespan, reduce downtime due to equipment failure, and minimize repair costs.
By maintaining equipment regularly, facilities achieve higher efficiency and safety. It ensures that production processes run smoothly and reliably. Moreover, effective maintenance helps manufacturers comply with safety regulations while improving the return on investment in expensive manufacturing equipment.
Equipment maintenance consists of three main types: preventive, predictive, and reactive. Each type addresses different aspects of maintenance management to enhance machinery life and performance.
Preventive Maintenance involves scheduled interventions and routine checks. Facilities conduct maintenance at regular intervals, regardless of the equipment's current condition, to avert breakdowns. Systematic inspections and part replacements maintain machinery functionality. This approach can use preventive maintenance software to reduce long-term repair expenses and minimize production losses due to scheduled downtime.
Predictive Maintenance relies on condition monitoring and data analysis. This method monitors equipment performance using real-time data and technology to forecast potential failures. Maintenance is scheduled based on actual equipment conditions, which prevents unnecessary servicing and conserves time and resources.
Reactive Maintenance happens in response to equipment failures or breakdowns. It includes emergency repairs and addresses unplanned downtime, which can disrupt production. Although this approach might incur higher costs due to urgent repair needs and possible secondary damages, addressing immediate and unforeseen issues is necessary.
Equipment maintenance's effectiveness rests on efficiency and tapping its full potential. Here are several best practices, such as utilizing maintenance management software, that can significantly improve equipment maintenance procedures.
Establishing and adhering to a consistent maintenance timetable is foundational to successful equipment maintenance. A well-defined schedule means all equipment receives the necessary attention before any issues arise. This practice prevents unexpected failures and costly downtime.
Maintaining comprehensive logs of all maintenance activities, repairs, and replacements is very important. These logs record equipment history and are instrumental in forecasting future maintenance needs and preparing for them efficiently.
It may seem obvious, but don’t cut corners. The longevity and performance of machinery depend on the quality of the tools and parts used during repairs and maintenance. Investing in high-quality tools and genuine parts helps ensure that repairs are durable and that the equipment continues to operate at its intended performance level.
Stay ahead of trends. Ongoing training for maintenance staff on the latest techniques and technologies helps teams stay proficient and up-to-date with industry best practices. This knowledge improves the employee's ability to diagnose and fix issues promptly and accurately.
Advanced equipment maintenance software, such as Computerized Maintenance Management Systems (CMMS), will transform maintenance operations. These technologies automate scheduling, streamline workflows, and improve the accuracy and efficacy of maintenance tasks. By integrating such software, facilities can achieve a higher standard of maintenance management. This leads to better overall equipment reliability and performance.
Implementing an equipment maintenance program offers many advantages, transforming how facilities manage their assets. From enhancing operational efficiency to reducing costs, these programs are critical for maintaining equipment health and longevity. Here are some key benefits of adopting an equipment maintenance program.
An effective maintenance program ensures that machinery operates at peak performance levels by addressing issues before they escalate into significant problems. Regular maintenance reduces the risk of unexpected breakdowns, keeping operations running smoothly and improving overall productivity.
An equipment maintenance program minimizes the need for costly emergency repairs by identifying and resolving minor issues early. Preventive and predictive measures also extend equipment lifespan, delaying the need for expensive replacements. This proactive approach results in substantial savings over time.
Well-maintained equipment is less likely to cause workplace accidents or malfunctions, jeopardizing employee safety. Maintenance programs also help organizations comply with industry regulations and safety standards, reducing the risk of fines or legal complications.
Equipment running at optimal performance consumes less energy and operates more efficiently, leading to lower operational costs. Maintenance programs also streamline workflows by minimizing downtime and ensuring that machinery is available.
Modern equipment maintenance technology, like Maintenance Connection, integrates with advanced software solutions, enabling organizations to collect and analyze maintenance data. This data provides valuable insights into equipment performance, helping managers make informed decisions about resource allocation, upgrades, and future maintenance schedules.
An effective equipment maintenance program fosters collaboration among maintenance teams, operators, and management by providing a centralized platform for tracking tasks, sharing updates, and accessing real-time data. With everyone having access to the same information, it becomes easier to coordinate schedules, prioritize tasks, and address issues promptly. Operators can report potential problems directly through the system, enabling swift action from maintenance teams. At the same time, management can monitor progress, allocate resources, and ensure alignment with organizational goals, breaking down communication silos and encouraging teamwork.
Equipment maintenance plays a vital role across industries, ensuring operational efficiency, compliance, and asset longevity.
Effective equipment maintenance is fundamental for tapping the potential of an operation. It ensures machinery longevity across various industries, particularly the manufacturing plant and hospitality sectors. Here’s how it works:
These maintenance activities are designed to extend the lifespan of equipment and ensure reliability in demanding industries. For a real-life example, according to PlantServices.com, Noranda Alumina, a Louisiana-based alumina refinery, significantly reduced its maintenance costs and downtime by implementing a new lubrication solution. This change led to a 60% decline in bearing changes, saving about $900,000 and potentially preventing $1 million in lost production every four hours of downtime.
This case illustrates the massive impact that effective equipment management can have on efficiency and cost reduction in industrial settings. Facilities can improve their performance and reliability by focusing on preventive measures and innovative solutions.
Software solutions transform equipment maintenance tracking. Here’s how these tools improve the efficiency of maintenance operations.
The term ‘maintenance’ itself is deceiving because it leads us to believe the maintenance job is simply to keep operations running as they are. Because of this perception, maintenance departments are usually seen as cost centers when they should be utilized as core business drivers.”
Modern software solutions gather all maintenance-related data into a single platform. This centralization simplifies the tracking process and management by providing a unified view of all maintenance activities. This central equipment maintenance log improves coordination and allows for better oversight of equipment health.
Maintenance software automates the process of sending out notifications for scheduled maintenance tasks. This feature ensures accountability for every task and guarantees timely performance of all maintenance activities. By automating alerts, facilities can maintain equipment proactively, which reduces the likelihood of unplanned downtime.
Computerized Maintenance Management Systems store and analyze historical maintenance data. It enables detailed trend analysis, facilitating the planning of predictive maintenance. By understanding past patterns, facilities can anticipate and address potential failures before they lead to significant issues.
Maintenance software supports the decision-making process with real-time updates and reporting. It helps managers and technicians stay informed of the current state of machinery. With this information, they can make informed decisions quickly. The real-time data feed improves response times to potential equipment issues and prevents minor problems from escalating.
Accruent Maintenance Connection is a versatile and robust CMMS software solution for streamlining maintenance management across various industries. It facilitates enterprise-wide preventive maintenance and ensures that assets are kept in the best condition possible with minimal downtime.
Key features of the software include the following:
Various sectors can benefit from a CMMS, such as Maintenance Connection, including manufacturing, education, healthcare, government, etc. Each industry benefits from tailored features that address specific maintenance needs and challenges, from managing vast asset inventories to complying with strict regulatory standards.
See how CMMS can help you jumpstart your equipment maintenance management.
Maintenance software is helpful for manufacturing professionals, plant managers, production supervisors, and facility managers. It improves maintenance operations by minimizing unplanned downtime and the associated costs. Additionally, it streamlines workflows through automation, improving overall asset management and reliability. Integrating Maintenance Connection into operations enhances the planning, execution, and monitoring of maintenance tasks.
Effective equipment maintenance requires regular inspections, timely repairs, and consistent adherence to a maintenance schedule. It includes training personnel, using the correct tools and parts, and maintaining detailed logs to manage and forecast maintenance needs.
The cost of equipment maintenance varies widely depending on the industry, equipment type, maintenance frequency, and whether the approach is reactive, preventive, or predictive. Generally, investing in preventive maintenance is more cost-effective in the long term than dealing with unplanned repairs.
Facilities can effectively track their equipment maintenance using CMMS software to centralize maintenance records, schedule and monitor tasks, and analyze historical data. This technology helps with accuracy while improving productivity. It fosters a culture of informed decision-making with real-time updates and notifications.
Discover the meaning and secrets to successful maintenance management in 2024. Explore strategies to cut maintenance costs and boost operational ...
A CMMS or computerized maintenance management system is software that helps plan, monitor, & report maintenance tasks, track work orders & ...
Learn how to develop a robust preventive maintenance program. Explore step-by-step guidelines and expert tips to streamline maintenance operations.
Subscribe to stay up to date with our latest news, resources and best practices