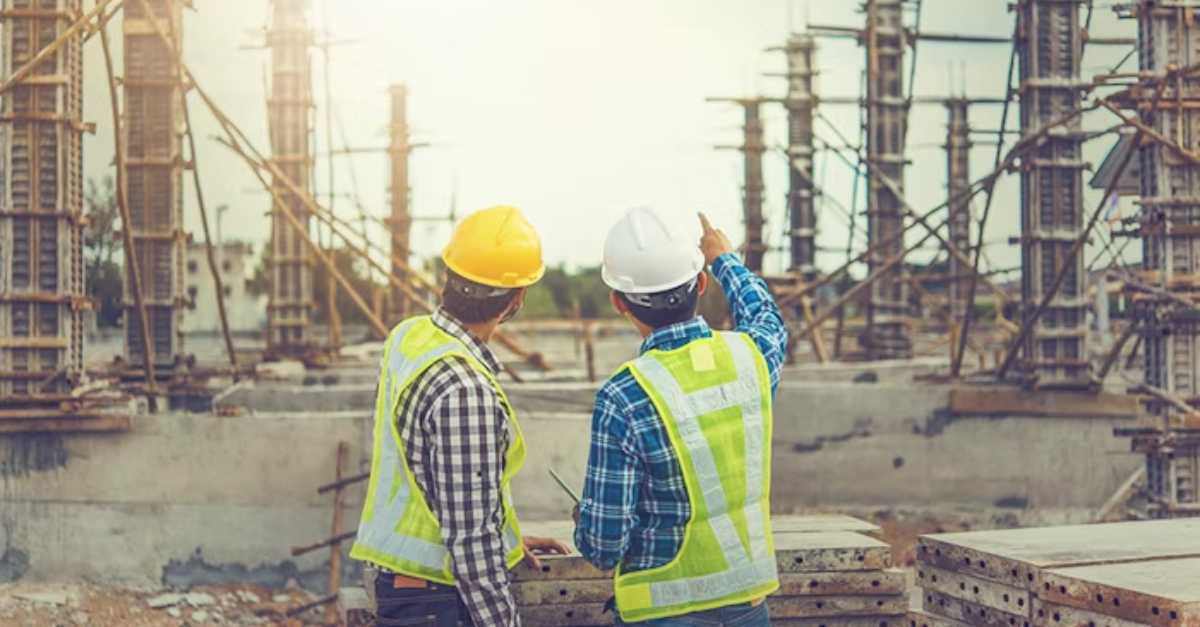
Ensuring Access to the Most Up-to-Date Engineering Drawings for Anytime, Anywhere Access
Meridian EDMS integrated with Maintenance Connection unifies engineering and maintenance teams with streamlined access to accurate dynamic asset ...
Solutions
Workplace Management Solutions
Real Estate Management Solutions
Maintenance Management Solutions
Energy Management Solutions
Engineering Document Management Solutions
Asset Management Solutions
Automate campus scheduling for classes, meetings, and exams with our EMS software.
Plan and manage conferences effortlessly with EMS software to impress guests and streamline operations.
Boost workplace flexibility and maximize space use with seamless desk and room booking.
Organize workplace or campus events smoothly, creating memorable experiences.
Optimize workspace, manage allocations efficiently, and reduce costs with our space management solutions.
Deliver projects on time and within budget by improving communication, collaboration, and efficiency with our software.
Streamline lease accounting for ASC 842, IFRS, and GASB compliance.
Manage leases efficiently by tracking key dates, analyzing costs, and ensuring compliance.
Centralize data and analytics for better insights, faster negotiations, and revenue growth.
Centralize facility and asset maintenance, automate work orders, and ensure compliance with our CMMS software.
Extend asset life, reduce downtime, and prevent costly repairs with data-driven monitoring.
Prevent equipment failures and extend asset life by detecting and addressing issues early.
Make sustainable, cost-efficient energy decisions by monitoring and optimizing power consumption.
Remotely monitor and control equipment with real-time data to predict issues, boost efficiency, and reduce downtime.
Easily share and collaborate on documents, creating a single source of truth for engineers and contractors.
Manage and analyze assets across their lifecycle to schedule maintenance, reduce downtime, and extend lifespan.
Improve visibility, automate work orders, and ensure compliance for efficient facility and asset management.
Resources
Browse our full library of resources all in one place, including webinars, whitepapers, podcast episodes, and more.
Support
Looking for access to technical support, best practices, helpful videos, or training tools? You’ve come to the right place.
About Accruent
Get the latest information on Accruent, our solutions, events, and the company at large.
Streamline your processes and ensure teams receive quick access to changing asset information with Accruent's new functionality and integration capabilities.
Table of contents
To help manufacturers streamline their business processes and ensure maintenance teams receive quick and easy access to ever-changing asset information, Accruent is adding new functionality and integration capabilities to its manufacturing industry solutions. These new additions will help manufacturers to be able to work smarter and become more agile and helps to support safety of maintenance teams in the field.
Historically, the documents that CMMS typically keep track of range from work order histories to bills of materials, items that systems like Accruent’s Maintenance Connection manage well and thoroughly. However, there are numerous other types of documents and drawings that may be associated with an asset.
When a maintenance professional goes to perform a work order on a piece of equipment, the core types of asset information that they need readily available including:
For most maintenance professionals, there is no fast way to easily access current engineering documentation while out in the field. Without the ability to connect assets to their engineering documentation, it can take hours of search time looking through various folders in different locations to ensure that maintenance teams are taking the latest revision of a drawing or document with them on-site. While on-site, there may also not be an effective way for maintenance professionals to communicate redlines back to the engineering teams.
With the integration of Accruent’s industry leading engineering document management, Meridian, and CMMS, Maintenance Connection, manufacturers can unify their engineering and maintenance teams with streamlined access to accurate dynamic asset information. Maintenance professionals in the manufacturing industry can easily access all of their current technical documentation with the click of a button directly from Maintenance Connection while Meridian provides a single source of truth for all engineering information to support maintenance safety in the field—eliminating duplicate data entry into different systems.
Ensure easy access to accurate, up to-date engineering documentation related to work orders, download our brochure to learn more.
With Accruent’s Observe, manufacturers are able to avoid unnecessary services by replacing equipment only when needed rather than at arbitrary, predetermined times.
Observe can improve asset performance and operations by:
Connecting assets to a digital infrastructure can allow them to communicate with users when equipment is working too hard, too closely to failure or is performing outside of normal operating capacity.
Learn more about avoiding unnecessary repairs by moving to a preventive maintenance system.
Kykloud is a mobile surveying and inspections application that ensures consistent condition surveys, inspections and lifecycle asset management across your entire portfolio. Kykloud’s full solution suite includes:
In the manufacturing industry, it can be challenging to collect the right information and create valuable reports in a timely fashion. Kykloud replaces traditional handwritten notes and manual spreadsheets to increase project delivery time and improve client communication capabilities.
With Kykloud’s compliance capabilities, manufacturers can uphold quality standards across their operations and identify maintenance, safety and regulatory issues before they become costly repairs or lawsuits. The solution provides full visibility into the creation, issuing and completion status of assessments with easy-to-use project management tools. Kykloud provides manufacturers the knowledge and data required to make informed decisions about maintenance and planned spend for the future.
Check out our brochure on ensuring consistent condition surveys, inspections and lifecycle asset management across your enterprise.
As 50% of maintenance technicians in the field now use a mobile device when performing work orders, organizations are being pushed more and more towards mobile software solutions according to "Smart Maintenance Extends the Scope of Enterprise – ARC Web Report".
Accruent’s Meridian Mobile provides an easy-to-use, multilingual mobile interface that gives maintenance team’ access to mission-critical engineering information—with or without a network connection.
Before arriving on-site, users can download the asset information that they will need on-site from a master set. While on-site, users can annotate, add comments and attach photos to documents from their mobile device. If the maintenance professional is working in a remote, offline location, whenever they next go online, all the added information will synchronize to the master set.
With access to view and approve asset documents from their iOS, Android or Windows phones or tablets, users can take swift action on their workflow tasks or to-do lists.
Manufacturers can maximize wrench times of maintenance teams in the field even in remote locations to increase workforce productivity.
Document classification is an essential function for most organizations, as many aspects of businesses such as security and naming convention rely on it. The ability for an organization to classify a document consistency and effectively produces better data quality and more efficient document location.
Accruent’s engineering document management tool, Meridian, can assign to documents a primary location and multiple secondary locations within the classification tree—maintained based on document type, discipline and class.
A study named "AI, automation, and the future of work: Ten things to solve for" showed that 60% of manufacturers are looking to invest in automation over the next 3 years to alleviate the skills challenge issue.
Accruent provides industry solutions designed to ensure regulatory compliance and a safe working environment for manufacturers. Our solutions break down information silos between disparate departments and external contractors to consistently deliver quality products to customers.
Accruent’s manufacturing solutions manage over 500 million documents and $1.5 trillion assets, with around 650,000 users across more than 50 countries. Every single one of the top 10 pharmaceutical organizations and half of the top 10 oil and gas companies use Accruent’s solutions to reduce costly downtime and lower the total cost of maintenance.
Find out how SSAB improved user adoption and managed a successful CMMS implementation. Still not convinced? Read about Alaska Airlines, L'Oreal, The New York Times or the City of Orlando, Florida. Are you ready to see your name among these internationally recognized titans? Schedule a demo today!
Meridian EDMS integrated with Maintenance Connection unifies engineering and maintenance teams with streamlined access to accurate dynamic asset ...
Accruent's facility maintenance software keeps your business running by streamlining work order management and prioritizing preventative maintenance.
Check out recent updates to TMS, Accruent's purpose-built healthcare computerized maintenance management system.
Subscribe to stay up to date with our latest news, resources and best practices