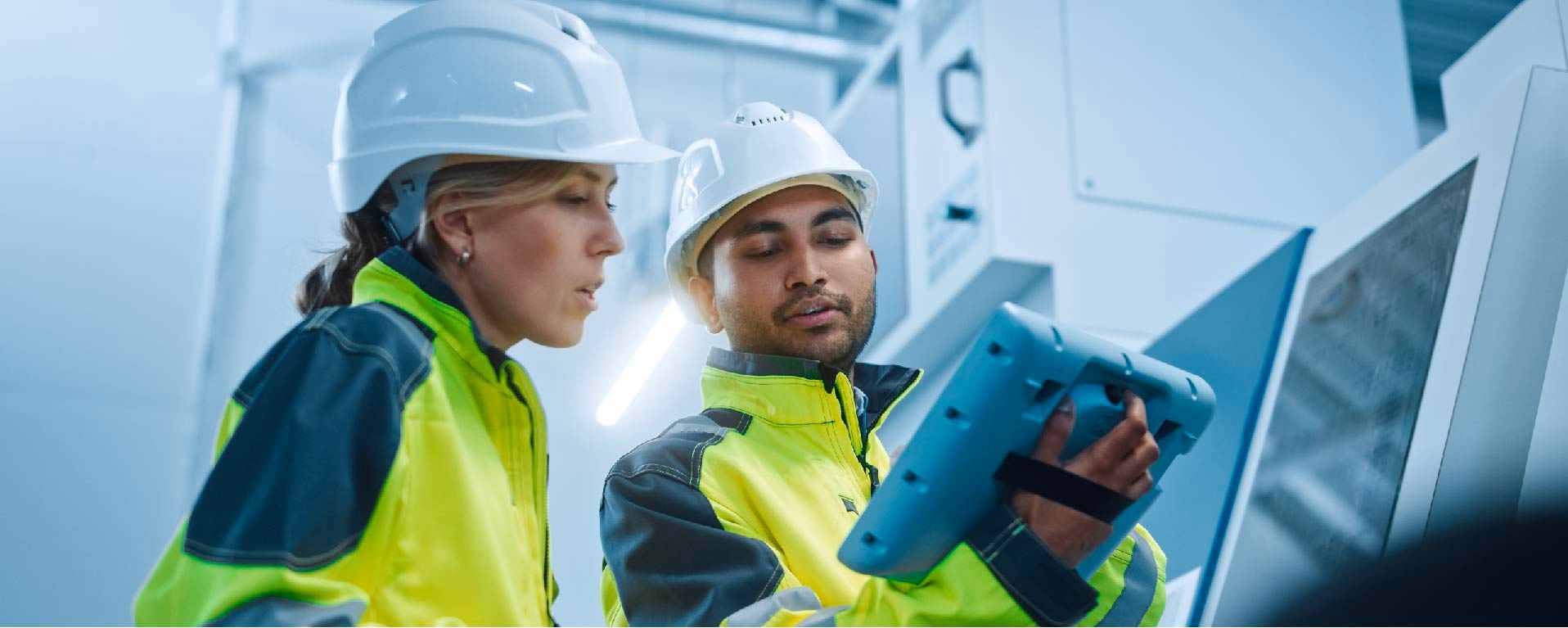
How Maintenance Managers Extend Asset Life and Decrease Downtime with CMMS
The right CMMS can help your organization minimize downtime and extend asset life. Here's how.
Solutions
Workplace Management Solutions
Real Estate Management Solutions
Maintenance Management Solutions
Energy Management Solutions
Engineering Document Management Solutions
Asset Management Solutions
Automate campus scheduling for classes, meetings, and exams with our EMS software.
Plan and manage conferences effortlessly with EMS software to impress guests and streamline operations.
Boost workplace flexibility and maximize space use with seamless desk and room booking.
Organize workplace or campus events smoothly, creating memorable experiences.
Optimize workspace, manage allocations efficiently, and reduce costs with our space management solutions.
Deliver projects on time and within budget by improving communication, collaboration, and efficiency with our software.
Streamline lease accounting for ASC 842, IFRS, and GASB compliance.
Manage leases efficiently by tracking key dates, analyzing costs, and ensuring compliance.
Centralize data and analytics for better insights, faster negotiations, and revenue growth.
Centralize facility and asset maintenance, automate work orders, and ensure compliance with our CMMS software.
Extend asset life, reduce downtime, and prevent costly repairs with data-driven monitoring.
Prevent equipment failures and extend asset life by detecting and addressing issues early.
Make sustainable, cost-efficient energy decisions by monitoring and optimizing power consumption.
Remotely monitor and control equipment with real-time data to predict issues, boost efficiency, and reduce downtime.
Easily share and collaborate on documents, creating a single source of truth for engineers and contractors.
Manage and analyze assets across their lifecycle to schedule maintenance, reduce downtime, and extend lifespan.
Improve visibility, automate work orders, and ensure compliance for efficient facility and asset management.
Resources
Browse our full library of resources all in one place, including webinars, whitepapers, podcast episodes, and more.
Support
Looking for access to technical support, best practices, helpful videos, or training tools? You’ve come to the right place.
About Accruent
Get the latest information on Accruent, our solutions, events, and the company at large.
Integrating your CMMS and ERP systems can improve communication, maximize insight and facilitate effective data management. Read on for details.
It’s no secret that software systems benefit businesses of all types, especially those in manufacturing. In fact, manufacturing output has reached a record high thanks to software advancements in robotics and automation.
These facts prove that adoption of manufacturing software has resulted in higher productivity and output, and lower production costs across the industry. But, don’t stop while you’re ahead; there are many more ways to capture productivity improvements.
To do so, manufacturing managers should consider integrating two of the most popular systems available for the industry: a computerized maintenance management system (CMMS) and an enterprise resource planning (ERP) system.
Software integrations help break down information silos across systems, manage data flow and encourage collaboration across different internal departments. The same goes for CMMS and ERP, as the two systems can cohesively work together to address manufacturing pain points.
Continue reading below to learn the top benefits of a CMMS and ERP integration, including improved communication, better insight into inventory and more effective data management.
Many departments work together to keep a manufacturing plant a well-oiled machine. Yet, areas from research to accounting to production may lose out when trying to communicate across different systems.
ERP solutions enable different departments across the plant to effectively exchange information about HR, time management and distribution planning. Meanwhile, managers rely on a CMMS to make decisions on technician scheduling or backlogged work orders based off schedules, service statuses and overtime hours logged in the system.
By integrating the two, managers can have one interface to make decisions based off information from all departments. For example, managers can quickly see if a technician is eligible for overtime based on HR info, and schedule someone for an emergency work order request if needed.
Inventory levels can either make or break the success of a manufacturing team. For example, if stockout occurs, it may not be possible to fulfill an emergency work order.
With a CMMS and ERP integration, purchase orders are easier for managers than ever. Simply generate a purchase order in your CMMS, and send the info off to the ERP as a purchase request. From there, the integration will automatically sync the data to update the applicable quantities and cost information for easy inventory ordering.
Maintenance managers know the importance of data to help make informed decisions. Managers can use data to understand factors ranging from average response time to open monthly work orders. But when different information is kept in separate systems, it’s difficult to get a full scope of data-backed information.
As SelectHub points out, an ERP and CMMS integration gives all parties across departments access to a single reporting system. With this single reporting hub, upper management can pull the data they need to make executive decisions on hiring or budgets. Meanwhile, the manufacturing team can find gaps in technician efficiencies, data on asset downtime and average response times.
Keep in mind that a CMMS and ERP integration is best suited for well-defined data. For example, the integration process will work smoother when specific KPIs are scoped and integrated into both systems. In addition, a defined purchasing process helps trigger the data to pass between both systems.
Maintenance Connection’s CMMS offers various integrations with ERP software. To see how a CMMS can transform your business with improved communication and better inventory management, watch a demo of Maintenance Connection.
The right CMMS can help your organization minimize downtime and extend asset life. Here's how.
Here's how a CMMS can help you optimize inventory management, aggregate maintenance data, and digitize your operations in the chemical industry.
How comprehensive asset intelligence, effective preventive maintenance, and efficient labor scheduling can lead to success in the chemical industry.
Subscribe to stay up to date with our latest news, resources and best practices