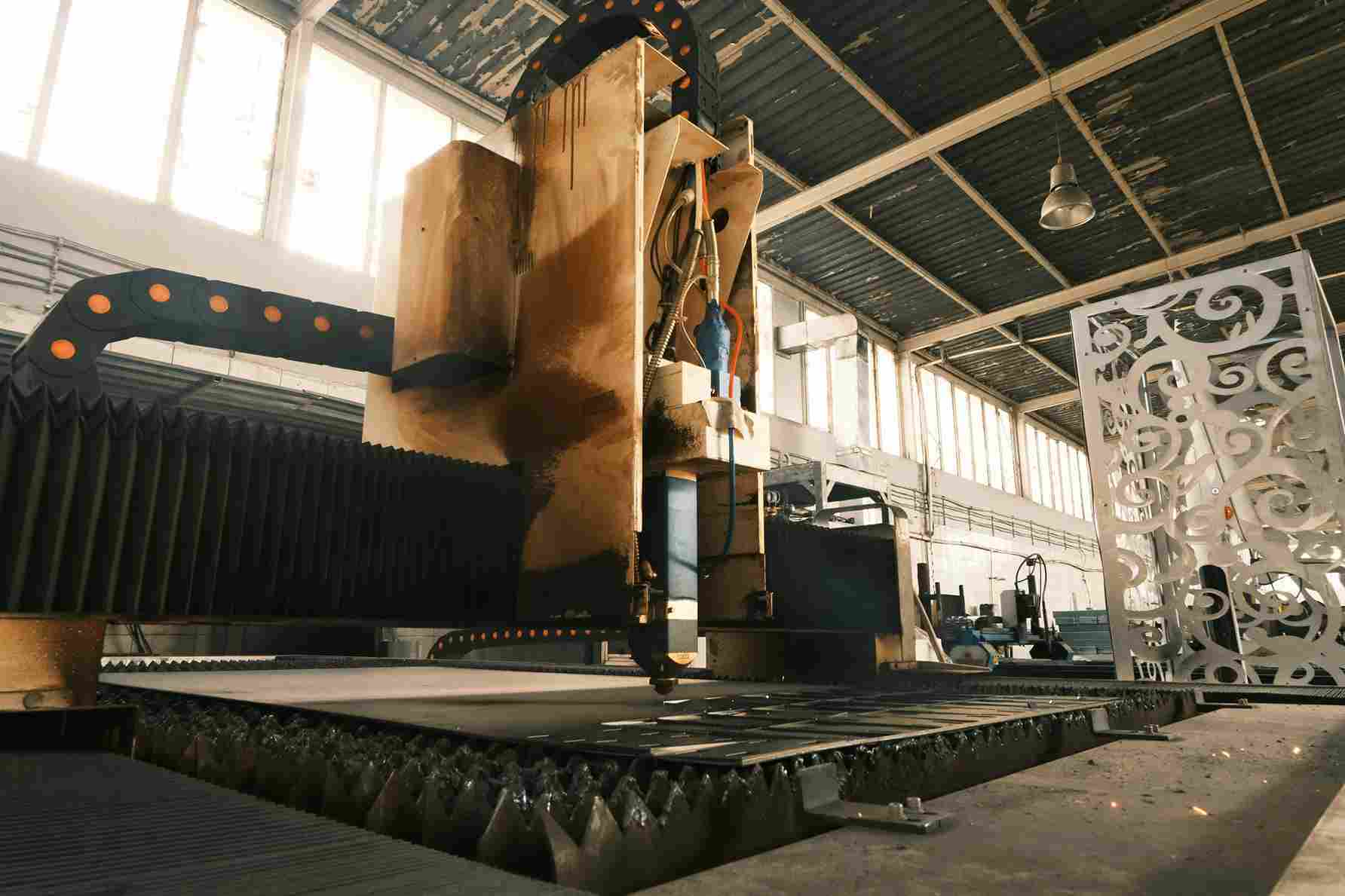
The Best CMMS Software For Manufacturing: Key Factors to Consider
Explore key factors to find the best CMMS software for manufacturing and elevate your facility's maintenance efficiency and productivity to the next ...
Solutions
Workplace Management Solutions
Real Estate Management Solutions
Maintenance Management Solutions
Energy Management Solutions
Engineering Document Management Solutions
Asset Management Solutions
Automate campus scheduling for classes, meetings, and exams with our EMS software.
Plan and manage conferences effortlessly with EMS software to impress guests and streamline operations.
Boost workplace flexibility and maximize space use with seamless desk and room booking.
Organize workplace or campus events smoothly, creating memorable experiences.
Optimize workspace, manage allocations efficiently, and reduce costs with our space management solutions.
Deliver projects on time and within budget by improving communication, collaboration, and efficiency with our software.
Streamline lease accounting for ASC 842, IFRS, and GASB compliance.
Manage leases efficiently by tracking key dates, analyzing costs, and ensuring compliance.
Centralize data and analytics for better insights, faster negotiations, and revenue growth.
Centralize facility and asset maintenance, automate work orders, and ensure compliance with our CMMS software.
Extend asset life, reduce downtime, and prevent costly repairs with data-driven monitoring.
Prevent equipment failures and extend asset life by detecting and addressing issues early.
Make sustainable, cost-efficient energy decisions by monitoring and optimizing power consumption.
Remotely monitor and control equipment with real-time data to predict issues, boost efficiency, and reduce downtime.
Easily share and collaborate on documents, creating a single source of truth for engineers and contractors.
Manage and analyze assets across their lifecycle to schedule maintenance, reduce downtime, and extend lifespan.
Improve visibility, automate work orders, and ensure compliance for efficient facility and asset management.
Resources
Browse our full library of resources all in one place, including webinars, whitepapers, podcast episodes, and more.
Support
Looking for access to technical support, best practices, helpful videos, or training tools? You’ve come to the right place.
About Accruent
Get the latest information on Accruent, our solutions, events, and the company at large.
Discover the potential of Manufacturing Enterprise Resource Planning (ERP) software with our informative guide that breaks down how it integrates and streamlines all facets of production and operations. Learn how a CMMS can be an integral part of your manufacturing ERP strategy, enhancing efficiency and driving growth.
Table of contents
In 2024, 95% of businesses report improvement after implementing ERP software. This compelling statistic shows the genuine impact of enterprise resource planning systems in manufacturing. As digital solutions become increasingly important, this guide explores how ERP software can streamline operations, improve decision-making, and foster a competitive edge in manufacturing.
Manufacturing Enterprise Resource Planning (ERP) is a comprehensive software system within the manufacturing sector. It is designed to unify and streamline all facets of production, management, and operations. The maintenance management software integrate various functions — from inventory and order management to accounting and human resources — into a single, cohesive platform.
This unification allows manufacturers to automate processes, improve data visibility, and facilitate better decision-making across departments. Serving as an all-in-one solution, Manufacturing ERP software helps businesses truly optimize workflows, increase efficiency, and maintain competitive advantage. It is about simplifying through evolution, software with the potential to transform a business on all levels.
In modern manufacturing, finding efficiency wins in maintenance management is more important than ever. ERP systems help facilitate integration across all operational areas by improving coordination. They allow for superior management of resources, ranging from raw materials to human capital, which means manufacturers tap the highest potential of their resources.
Further, by maintaining stringent quality control, ERP assists in navigating the tricky world of industry regulations and standards. When utilized properly, they also help mitigate any legal risks or issues.
Given the evolving nature of the manufacturing world, ERP provides businesses with an automation tool to maintain consistent quality control as requirements and guidelines continuously shift and change.
Depending on the manufacturer’s specific needs, the ERP systems are tailored to meet various scales and complexities. Each is equipped with unique features and functionalities to suit different business needs.
Cloud-based ERP systems offer accessibility from anywhere with an internet connection, which means flexibility and mobility. These systems are typically available on a subscription basis. That means less upfront costs and simplified budget management. Additionally, they are scalable, making it easy to adjust resources as business needs evolve and grow.
On-premise ERP systems offer complete control over the ERP infrastructure and data security. These systems allow for extensive customization to meet specific business requirements. They are particularly ideal for unique or highly specialized operations. While they do require a significant initial investment, on-premise systems can be more cost-effective over the long term due to their durability and tailored fit to exact business needs.
Hybrid ERP systems combine the benefits of both cloud and on-premise solutions. It is an optimal balance of flexibility and control. These systems offer phased migration and seamless integration with existing systems. That means reduced disruption to ongoing operations. With hybrid systems, businesses can decide which components to host on-premise and which to operate in the cloud. The customized approach can adapt to any manufacturing environment.
Manufacturing ERP software is built with features designed to streamline complex manufacturing processes.
ERP systems provide real-time tracking to monitor inventory levels continuously. This avoids both stockouts and overstocking. Automated reordering features trigger purchase orders automatically when inventory drops below certain thresholds. Then, these systems offer detailed analysis and reporting capabilities. Those insights provide useful inventory trends that help forecast future stock levels.
Supply chain management within ERP systems improves coordination with suppliers through direct communication channels. This supply planning leads to a more streamlined shipping and receiving process, and that leads to faster and more accurate order fulfillment. Additionally, ERP systems provide visibility and control over the entire supply chain. It allows businesses to avoid any potential disruptions through proactive management.
Manufacturing ERP systems help in capacity planning by evaluating production capabilities to maximize throughput. Shop floor control features monitor production progress and provide valuable insights that allow for real-time adjustments to workflows. These systems work in harmony with the larger production process by creating and managing schedules. It is about finding harmony between production and timely delivery.
Manufacturing processes must adhere to industry standards and quality benchmarks. The software reduces the risk of non-compliance. The tracking features identify and monitor product defects and orchestrate swift corrective actions. Product quality is not sacrificed. Further, ERP systems analyze data to drive continuous improvements in processes over time.
There are numerous benefits ERP systems bring to manufacturing companies. The focus is to improve operations across various levels of the organization.
Transform what manufacturing means to the business. Automating and optimizing workflows reduces the need for manual efforts, which decreases the likelihood of errors. Productivity is improved through the smoother flow of information, which will speed up decision-making and task execution. Minimize production lead times through proactive resource planning and scheduling.
Spend and invest wisely and see the results. ERP systems provide integrated financial insights that identify areas where costs can be reduced. These systems are equipped with tools that support accurate budgeting and financial forecasting. Identify the most profitable product lines and find the right pricing strategies to increase revenue.
Manage resources more effectively. ERP provides a comprehensive view of supplier performance and procurement needs and monitors inventory levels to ensure they remain at the right levels. This avoids any holding costs or stockouts. The demand planning features align production with demand forecasts to avoid any overproduction or missed sales opportunities.
Stay ahead of any potential issues across the board. ERP systems reduce legal risks or compliance issues by constantly monitoring production processes. They keep detailed and accurate records of operations to prevent any potential challenges around audits or compliance checks. Companies use the software to stay within the bounds of regulatory frameworks.
Selecting the right manufacturing ERP system is a significant business decision, but where to begin? Here are some best practices to keep in mind.
Start by assessing business requirements by thoroughly evaluating the specific needs of the manufacturing operations. Consider factors such as the size of the business, the complexity of processes, and any unique challenges posed by the industry.
It is essential that the ERP system offers scalability and growth. The chosen ERP should accommodate future growth and adapt to changes in the business environment without requiring extensive modifications. This flexibility will ensure the system remains useful as the business evolves and expands.
Opt for an ERP system that offers key functionalities tailored to the manufacturing processes. Key features to look for should include robust inventory management, detailed production planning, and comprehensive quality control.
Then, make sure the ERP system is compatible with existing technology infrastructure. Compatibility allows for smoother integration with other tools and platforms the business currently uses. This leads to a unified technological environment.
Finally, perform a cost analysis. Carefully examine the total expense of ownership of the ERP system. This should include all expenses related to licensing, implementation, customization, and ongoing maintenance.
Maintenance Connection’s CMMS (Computerized Maintenance Management System) offers a robust solution that complements other ERP systems. By specifically targeting the maintenance aspects that ERP systems often cover in less detail, the CMMS improve capabilities with dedicated tools for detailed scheduling, tracking, and execution.
This integration means that maintenance data – such as equipment status, downtime, and repair history – are tracked in the system.
Better data synchronization means that maintenance and production efforts are well-coordinated. Maintenance Connection’s CMMS works to reduce downtime, optimize resource allocation, and manage maintenance costs more effectively. Here is what it looks like in practice.
Strategic integration helps maximize the functionality of each system while improving operational efficiency. When harmony is found, the CMMS software quickly become an indispensable solution for modern manufacturing environments.
ERP solutions in manufacturing offer several benefits. With the right software, they can improve financial management, increase operations, and manage stringent quality controls. To tap the most potential, consider pairing an ERP system with Maintenance Connection’s CMMS to truly optimize maintenance management.
Want to learn more? Learn how Maintenance Connect works as an ERP partner.
Standard ERP systems manage general business processes like finance, HR, and procurement across various industries. Manufacturing ERP, however, is specifically designed to handle the unique requirements of manufacturing operations. These include production planning, quality control, and machine maintenance.
SAP ERP is one of the most common ERP systems used in manufacturing. It offers extensive features that support complex manufacturing processes such as production planning, supply chain management, and product lifecycle management. It is a favored choice among large manufacturers.
An example of manufacturing ERP software is Accruent’s Maintenance Connection. This CMMS solution is tailored to improve manufacturing by integrating maintenance management directly with ERP functionalities. It supports manufacturing processes with asset lifecycle management, preventive maintenance scheduling, and real-time operational analytics. These features foster a seamless link between daily production activities and long-term asset management strategies.
Explore key factors to find the best CMMS software for manufacturing and elevate your facility's maintenance efficiency and productivity to the next ...
Discover the power of Manufacturing Execution Systems (MES) to improve production efficiency, quality control, and real-time decision-making.
Learn how the right inventory management system can reduce costs, improve efficiency, and simplify processes for manufacturing professionals. Explore ...
Subscribe to stay up to date with our latest news, resources and best practices