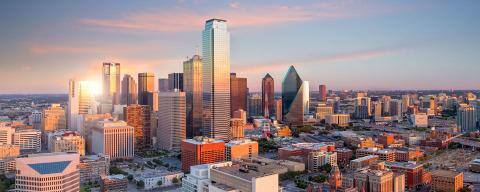
How Lucky Eagle Casino Reduced Maintenance Costs with a CMMS
Learn how Lucky Eagle Casino streamlined work order management and reduced maintenance costs with Maintenance Connection.
Solutions
Workplace Management Solutions
Real Estate Management Solutions
Maintenance Management Solutions
Energy Management Solutions
Engineering Document Management Solutions
Asset Management Solutions
Automate campus scheduling for classes, meetings, and exams with our EMS software.
Plan and manage conferences effortlessly with EMS software to impress guests and streamline operations.
Boost workplace flexibility and maximize space use with seamless desk and room booking.
Organize workplace or campus events smoothly, creating memorable experiences.
Optimize workspace, manage allocations efficiently, and reduce costs with our space management solutions.
Deliver projects on time and within budget by improving communication, collaboration, and efficiency with our software.
Streamline lease accounting for ASC 842, IFRS, and GASB compliance.
Manage leases efficiently by tracking key dates, analyzing costs, and ensuring compliance.
Centralize data and analytics for better insights, faster negotiations, and revenue growth.
Centralize facility and asset maintenance, automate work orders, and ensure compliance with our CMMS software.
Extend asset life, reduce downtime, and prevent costly repairs with data-driven monitoring.
Prevent equipment failures and extend asset life by detecting and addressing issues early.
Make sustainable, cost-efficient energy decisions by monitoring and optimizing power consumption.
Remotely monitor and control equipment with real-time data to predict issues, boost efficiency, and reduce downtime.
Easily share and collaborate on documents, creating a single source of truth for engineers and contractors.
Manage and analyze assets across their lifecycle to schedule maintenance, reduce downtime, and extend lifespan.
Improve visibility, automate work orders, and ensure compliance for efficient facility and asset management.
Resources
Browse our full library of resources all in one place, including webinars, whitepapers, podcast episodes, and more.
Support
Looking for access to technical support, best practices, helpful videos, or training tools? You’ve come to the right place.
About Accruent
Get the latest information on Accruent, our solutions, events, and the company at large.
Learn how Maintenance Connection helped The New York Times automate reports, allocate resources, and improve labor productivity.
With 64 newspaper print facilities across the world and more than 10,000 assets to sustain, The New York Times maintenance team is nothing short of busy. And with more than 1 million weekly readers, the well-respected news source realized its need for a more reliable maintenance strategy enabled by a CMMS.
The New York Times sought a user-friendly system to organize its assets and track equipment health across sites. After finding gaps with its legacy software, the company chose Maintenance Connection's CMMS. Since implementation, the maintenance team has seen improvements on asset uptime and plant productivity.
To learn more about how The New York Time’s integrated CMMS, read below to learn how the maintenance team relies on Maintenance Connection for improved team communication and asset organization.
Before implementing Maintenance Connection’s CMMS, The New York Times struggled to organize its assets. And with thousands of assets let alone employees spread out across the plant the facility needed a way to report on deficiencies. With the help of Maintenance Connection, the maintenance team is now able to track asset health and work order status to report downtime more effectively. Beyond that, the CMMS organized its 10,000+ assets into the system, improving internal operations.
As a result, the team was able to implement a preventive maintenance (PM) program to service equipment before breakdown and plan ahead for inventory requests.
Since the plant-wide rollout, the maintenance team has witnessed improvements on labor, resources and planning. With the CMMS, the team plans for maintenance and schedules accordingly. As a result, the team can identify equipment usage and automate recurring PM work orders to decrease downtime and reduce repairs. The PM schedule also provides maintenance with a snapshot of reports concerning where and how the plant allocates resources and budget. This saves the facility time and money due to a reduction in emergency requests.
Overall, Maintenance Connection’s CMMS provides The New York Times with the ability to foster plant communications, house asset information and track maintenance status. For more on how The New York Times depends on a CMMS for maintenance operations, read the full story here. Also, remember to check out our Profiles of Success page for more stories on: Or, start a free trial of Maintenance Connection to see how a CMMS can save your team money and labor time to get more out of your assets.
With Maintenance Connection, everybody is well aware what’s going on in the plant"
- Greg Zarafa, The New York Times Maintenance Manager
Learn how Lucky Eagle Casino streamlined work order management and reduced maintenance costs with Maintenance Connection.
Automakers are always looking for ways to streamline operations, improve communications, and create safe, smart vehicles. A CMMS can help.
Maintenance management in the public sector is all about ensuring uptime and maintaining effective resource management. A CMMS can help.
Subscribe to stay up to date with our latest news, resources and best practices