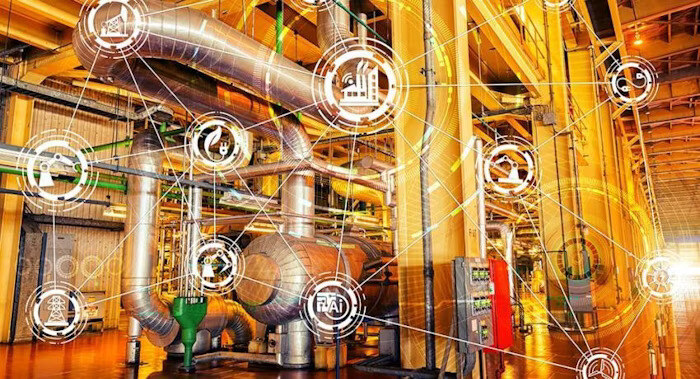
3 IoT Strategies for Improving Your Manufacturing Processes with Maintenance Connection
Explore three IoT strategies that improve processes and efficiency using maintenance connection software.
Solutions
Workplace Management Solutions
Real Estate Management Solutions
Maintenance Management Solutions
Energy Management Solutions
Engineering Document Management Solutions
Asset Management Solutions
Automate campus scheduling for classes, meetings, and exams with our EMS software.
Plan and manage conferences effortlessly with EMS software to impress guests and streamline operations.
Boost workplace flexibility and maximize space use with seamless desk and room booking.
Organize workplace or campus events smoothly, creating memorable experiences.
Optimize workspace, manage allocations efficiently, and reduce costs with our space management solutions.
Deliver projects on time and within budget by improving communication, collaboration, and efficiency with our software.
Streamline lease accounting for ASC 842, IFRS, and GASB compliance.
Manage leases efficiently by tracking key dates, analyzing costs, and ensuring compliance.
Centralize data and analytics for better insights, faster negotiations, and revenue growth.
Centralize facility and asset maintenance, automate work orders, and ensure compliance with our CMMS software.
Extend asset life, reduce downtime, and prevent costly repairs with data-driven monitoring.
Prevent equipment failures and extend asset life by detecting and addressing issues early.
Make sustainable, cost-efficient energy decisions by monitoring and optimizing power consumption.
Remotely monitor and control equipment with real-time data to predict issues, boost efficiency, and reduce downtime.
Easily share and collaborate on documents, creating a single source of truth for engineers and contractors.
Manage and analyze assets across their lifecycle to schedule maintenance, reduce downtime, and extend lifespan.
Improve visibility, automate work orders, and ensure compliance for efficient facility and asset management.
Resources
Browse our full library of resources all in one place, including webinars, whitepapers, podcast episodes, and more.
Support
Looking for access to technical support, best practices, helpful videos, or training tools? You’ve come to the right place.
About Accruent
Get the latest information on Accruent, our solutions, events, and the company at large.
Remote, multi-device tools – like an offline, native mobile CMMS – are must-haves in today’s connected workplace. Here’s why.
Bill Gates once said, “The advance of technology is based on making it fit in so that you don't really even notice it, so it's part of everyday life.” And when it comes to our everyday lives, we’re there. Smartphones, Wi-Fi, apps, wearables, and IoT devices have inextricably connected people, tools, and computers – and, for better or worse, fundamentally changed how we navigate all aspects of our lives.
Yet, when it comes to the Industrial world, many “legacy” organizations are woefully behind the eight ball, relying on systems, assets, and best practices put in place well before smartphones, Industry 4.0, IIoT, or the widespread availability of sensor technology.
And they’re falling further and further behind. According to Polaris Market Research, the global Connected Worker market is anticipated to grow from 4.21 billion in 2021 to 24.32 billion in 2029. Additionally, Gen Z and Gen Y workers – 96% of whom own a smartphone – now expect to use that phone to engage and execute in the workplace.
Translation? The world and workforce are demanding that the Industrial workplace gets with the times – and the consequences of ignoring those demands are getting increasingly starker.
Here’s what a successful “connected workplace” can look like in your organization.
To understand where we’re at today, it’s important to take a quick look at where we’ve been.
The Industrial Revolution, as we all know, was a complete overhaul of Industry and manufacturing, with metal machines, new physical assets, and electricity automating and scaling once-manual operations – and quite literally changing the industrial world.
In subsequent decades, these plants continued to evolve as manufacturers refined processes, improved tools, and began using computers to further connect, automate, and draw insights.
And many legacy organizations are still somewhere on that track, cobbling together tools and best practices as they become available to create patchwork operations. It works – just as it has worked for the past 70 years – but it’s ignoring the digital-first world that we live in today.
On the one hand, it makes sense. After all, everyone working on the plant floor cares primarily about what’s happening on that floor – how the assets are looking, how they’re sounding, how the team is doing, what the reports are saying. And, in many cases, new software and systems wind up being more trouble than they’re worth, providing functionalities that nobody needs and operating systems that just don’t fit into day-to-day routines.
But this mindset is ignoring crucial developments and benefits of the digital-first connected workplace.
There has been a culmination of technology events that have given rise to the connected workplace, including:
Then there are the social factors. The pandemic, for one, was an imperfect storm forcing organizations to work remotely and across multiple devices and locations.
What’s more, the workforce has fundamentally changed. Boomers continue to rapidly leave the workforce, taking their skills and tribal knowledge with them. At the same time, Millennials and Gen Z are taking over, bringing their heightened workplace expectations and nuanced relationship with technology with them. Gen Y, or Millennials, is the first generation of digital natives, a group that is:
Gen Z takes this even further. They never knew a world without smartphones and advanced technology. As a result, they’re extremely savvy, discerning, mobile-first, and digital-first. And these generations are quickly taking over as the present and future of manufacturing.
This brings us to the present moment. In 2023 and beyond, smart and future-ready manufacturing will be about having the data you need in the palm of your hand so you can reduce work orders, predict failures, reduce spending, automate, and decrease your energy footprint. This will require:
And 84% of organizations are already engaged in this digital-first strategy.
The good news? This doesn’t have to be a tough mountain to climb. Tools like a fully native, offline CMMS application can empower maintenance teams to execute preventive maintenance, optimize maintenance operations, and utilize their data using one connected, centralized tool - no connectivity concerns, no efficiency losses, and no difficulty locating assets or parts. And that’s just the start.
Learn more about native, offline CMMS options here, or reach out directly to frederic.baudart@accruent.com to get more information about our suite of smart manufacturing solutions.
Explore three IoT strategies that improve processes and efficiency using maintenance connection software.
Industry 4.0 literacy has become crucial for manufacturing organizations. Here's how to increase buy-in and invest in tools that really work.
Explore four workplace challenges and how to show them using a connected workspace that can grow with your organization.
Subscribe to stay up to date with our latest news, resources and best practices