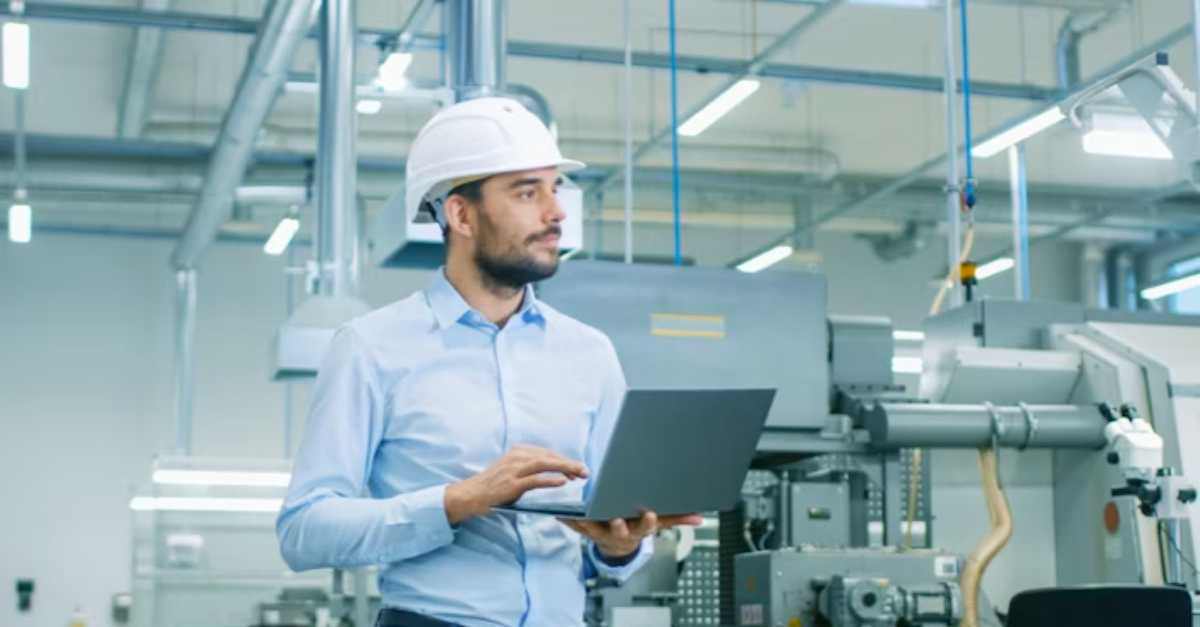
Why Good Data Structure is Critical for your Digital Transformation
Discover why good data structure, governance, and strategy are core to effective digital transformation and how to better organize data with the ...
Solutions
Workplace Management Solutions
Real Estate Management Solutions
Maintenance Management Solutions
Energy Management Solutions
Engineering Document Management Solutions
Asset Management Solutions
Automate campus scheduling for classes, meetings, and exams with our EMS software.
Plan and manage conferences effortlessly with EMS software to impress guests and streamline operations.
Boost workplace flexibility and maximize space use with seamless desk and room booking.
Organize workplace or campus events smoothly, creating memorable experiences.
Optimize workspace, manage allocations efficiently, and reduce costs with our space management solutions.
Deliver projects on time and within budget by improving communication, collaboration, and efficiency with our software.
Streamline lease accounting for ASC 842, IFRS, and GASB compliance.
Manage leases efficiently by tracking key dates, analyzing costs, and ensuring compliance.
Centralize data and analytics for better insights, faster negotiations, and revenue growth.
Centralize facility and asset maintenance, automate work orders, and ensure compliance with our CMMS software.
Extend asset life, reduce downtime, and prevent costly repairs with data-driven monitoring.
Prevent equipment failures and extend asset life by detecting and addressing issues early.
Make sustainable, cost-efficient energy decisions by monitoring and optimizing power consumption.
Remotely monitor and control equipment with real-time data to predict issues, boost efficiency, and reduce downtime.
Easily share and collaborate on documents, creating a single source of truth for engineers and contractors.
Manage and analyze assets across their lifecycle to schedule maintenance, reduce downtime, and extend lifespan.
Improve visibility, automate work orders, and ensure compliance for efficient facility and asset management.
Resources
Browse our full library of resources all in one place, including webinars, whitepapers, podcast episodes, and more.
Support
Looking for access to technical support, best practices, helpful videos, or training tools? You’ve come to the right place.
About Accruent
Get the latest information on Accruent, our solutions, events, and the company at large.
Industry 4.0 literacy has become crucial for manufacturing organizations. Here's how to increase buy-in and invest in tools that really work.
With industry 5.0 already looming and heightening the focus on human-machine interaction, literacy in industry 4.0 practices and tools have become a have-to-have for businesses in manufacturing. But this is often easier said than done, and many companies still face resistance or confusion – both from decision-makers and team members -- about how to truly get Industry 4.0 tools and best practices off the ground.
Getting this right is all about remaining focused on the true value and purpose of your tools so you can increase buy-in and continuously adopt technology that will work.
Here’s everything you need to know.
Industry 4.0, or the Fourth Industrial Revolution, is the fourth revolution to occur in manufacturing. It involves the use of data, smart tools and autonomous systems – powered by data and machine learning – to make computers and automations smarter (and, in turn, make your lives easier).
This, of course, was preceded by:
In manufacturing, specifically, there is significant promise to Industry 4.0 technologies. The right suite of tools— backed by AI, machine learning, the Internet of Things and the Internet of Systems – can help make smart factories a reality. Translation? More productivity, more automation and more precise, cost-saving operations.
That said, just because it’s promising doesn’t make it easy.
One of the main points of resistance with Industry 4.0 and digital transformation is that it does seemingly make life more complex in the day-to-day. Just the sheer number of things that we can do in a day – and the sheer amount of data, analytics and tech that we have at our fingertips – can be overwhelming. And many team members might think that it’s just not worth it, particularly when compared to familiar, comfortable legacy systems and processes.
You always have to keep in mind, though, that the technology is continuing to get more complex, but the end result is becoming more simplistic. And your competitors – and the technology itself – are going to continue to move on whether you decide to adopt or not. you must get on board and get comfortable with the complexity of Industry 4.0 if you want to remain agile, modernize your business and be a true competitor in your industry.
Here’s how to get it right.
Getting Industry 4.0 right is all about preparing your people, processes and technology. More specifically, you should:
When considering how to implement Industry 4.0 tools and best practices, never start by looking at the technology that’s out there and all the bells and whistles it might have. Instead, start with your strategy and the value that you want to get out of your technology. Where does the value reside? What do you want to accomplish with your Industry 4.0 tools? Do you want to maintain competitiveness in your business, keep up margins, steady your company’s position in the market?
Starting with these end goal questions and then working retroactively to figure out what technology will give you the value you’re looking for is the only way to get Industry 4.0 deployments right. Do it the other way around and you’ll be amongst the 50% of technology deployments that fail.
It’s also important to remember that your team will always be crucial to the success of any tech you deploy. While technology fills in the gaps and makes things easier, it’s the people that push that technology forward and use it day-to-day. You must make sure that your team is doing that and always ready to continuously improve and learn.
That said, this can require a significant cultural shift for many companies. A common adage in manufacturing is that people are the most unreliable asset in the plant – and there’s some truth to that. Your team members will always be one of the biggest barriers to digital transformation if you let them be, particularly if they don’t buy into what you’re doing or why. To prevent this from happening, you must change your people and change how they utilize technology as part of their everyday work.
This, in turn, will require that they understand the value of the new tech and the new processes. No easy feat.
This is where you can really leverage your younger employees. When new technology arrives (and with it, new processes) you will have to find ways to upskill your employees so they can understand the technology and learn how to operate and gather information in new ways.
Your younger generation will be used to this. Think about it: Millennial and Gen Z employees are used to making technology their friend, and they easily Google things and looks for answers to questions on their smartphones. This digital-first mentality will help these teams leverage data and use information, thereby decreasing your efficiency and your reliance on tribal knowledge.
Many organizations are still hesitant about new technology – and, more particularly, cloud tools.
This is a misplaced and dated concern. Since cloud deployments really took off in 2015, there has always been conversation about keeping data and IP information safe (along with fear of relinquishing data into the cloud).
And, even though cloud companies focus exclusively on making data safe, secure and compliant, a lot of these misconceptions and concerns remain. This must be addressed.
There’s a lot that’s drastically different in Industry 4.0 -- like digital twin.
Now, the concept of a digital twin itself is nothing new: companies have tried to recreate things in the digital world since computers first came out 40+ years ago. However, things like augmented reality, virtual reality, big data, connectivity and increases in bandwidth have made digital twin much more advanced – and the future of automation is largely dependent on the digital twin continuing to mature.
Think about it: with a digital twin that’s truly interactive and reflective of the built environment, teams will be able to:
In short, as digital twin matures it will allow teams to both get a true vision of the current state and look into the future. But teams will also have to mature and be ready to embrace this kind of tech. Otherwise, it will be too much for them to handle.
Technicians and maintenance teams are often concerned that Industry 4.0 will replace them or leave them without a job. This is not true.
The work of a technician—whether it’s repairing an asset, performing preventive maintenance or conducting a visual inspection – is a face-to-face, in-person job. And this demand for technician presence will never go away.
Instead, Industry 4.0 tech will help those technicians:
This must be clear to get them on board.
A great irony about many engineers is that – even though they understand the new technology best (and often because they understand the technology best) – they're often most adverse to change and adoption.
On one hand, this makes sense. They understand the pitfalls, limitations and drawbacks that often come with new tech, so they want to be conservative in their approach.
These engineers will have to change if you want to get Industry 4.0 right. This is because, in the future, everything that engineers touch will be digital, including drawings, designs, operations and production. And this is necessary to help them maintain higher expectations and work to a higher standard. You just have to get them on board.
True digital transformation and adoption of Industry 4.0 technologies can help manufacturing organizations access information, lower costs, increase efficiency, set higher standards and transform operations. And, with so much information and data at their fingertips, there really are no limits to growth and achievement. You just have to keep your value at the forefront, get your team on board and find technology that will really work for your operations.
You can learn more in our webinar, Industry 4.0 Explained: Driving Excellence Across Manufacutring. Want to explore some options? Schedule a demo of Maintenance Connection CMMS, Meridian engineering document management system, or Observe remote monitoring system to see how these tools can help your organization digitally transform today.
Discover why good data structure, governance, and strategy are core to effective digital transformation and how to better organize data with the ...
Identify the role that IoT plays in your organization and how to successfully implement it to meet your needs.
Remote, multi-device tools – like an offline, native mobile CMMS – are crucial in today’s connected workplace. Here’s why.
Subscribe to stay up to date with our latest news, resources and best practices