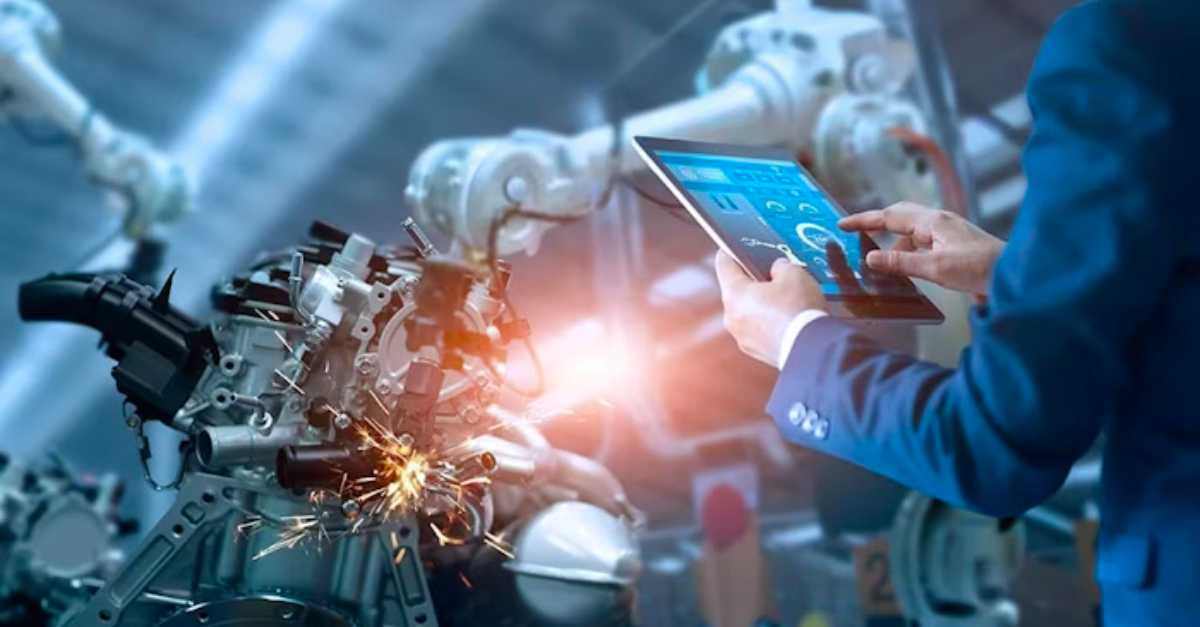
What is the Role of IoT in Managing & Maintaining Assets?
Identify the role that IoT plays in your organization and how to successfully implement it to meet your needs.
Solutions
Workplace Management Solutions
Real Estate Management Solutions
Maintenance Management Solutions
Energy Management Solutions
Engineering Document Management Solutions
Asset Management Solutions
Automate campus scheduling for classes, meetings, and exams with our EMS software.
Plan and manage conferences effortlessly with EMS software to impress guests and streamline operations.
Boost workplace flexibility and maximize space use with seamless desk and room booking.
Organize workplace or campus events smoothly, creating memorable experiences.
Optimize workspace, manage allocations efficiently, and reduce costs with our space management solutions.
Deliver projects on time and within budget by improving communication, collaboration, and efficiency with our software.
Streamline lease accounting for ASC 842, IFRS, and GASB compliance.
Manage leases efficiently by tracking key dates, analyzing costs, and ensuring compliance.
Centralize data and analytics for better insights, faster negotiations, and revenue growth.
Centralize facility and asset maintenance, automate work orders, and ensure compliance with our CMMS software.
Extend asset life, reduce downtime, and prevent costly repairs with data-driven monitoring.
Prevent equipment failures and extend asset life by detecting and addressing issues early.
Make sustainable, cost-efficient energy decisions by monitoring and optimizing power consumption.
Remotely monitor and control equipment with real-time data to predict issues, boost efficiency, and reduce downtime.
Easily share and collaborate on documents, creating a single source of truth for engineers and contractors.
Manage and analyze assets across their lifecycle to schedule maintenance, reduce downtime, and extend lifespan.
Improve visibility, automate work orders, and ensure compliance for efficient facility and asset management.
Resources
Browse our full library of resources all in one place, including webinars, whitepapers, podcast episodes, and more.
Support
Looking for access to technical support, best practices, helpful videos, or training tools? You’ve come to the right place.
About Accruent
Get the latest information on Accruent, our solutions, events, and the company at large.
In today’s data-driven world, knowledge management is power. Learn how it can improve processes, close the skills gap, and bring products to market faster.
In 1994, Tom Davenport defined knowledge management (KM) as “the process of capturing, distributing and effectively using knowledge.” It seems simple enough, and it’s indispensable to any organization.
But effective knowledge management is often easier said than done – and this fact has been detrimental to the progress of many organizations. This is especially true for those in manufacturing industries, including general manufacturing, information technology, telecoms, chemicals and consumer goods. In such companies, an aging workforce and largely manual processes have inhibited the effective transfer of knowledge and caused a massive skills gap to emerge. And this has hobbled one of the greatest economic drivers in the U.S.
Here’s how to implement knowledge management in industries across the board to close the skills gap, save money and bring your organization into the future.
Before the 1990s, corporate knowledge and training was largely spread through word of mouth and
The modern concept of knowledge management (KM) started in the 1990s, when the internet, computers, corporate intranet, and the earliest forms of analytics made it possible to codify and capture institutional expertise. Before that time, corporate knowledge and training was largely spread through word of mouth and anecdotal conversation, which means that it wasn’t scalable or widely available to those who needed it.
Particularly in the world of consulting and corporate strategy, knowledge management promised to change that – and these corporations quickly hired “chief knowledge officers” and used dashboards, expertise locators and best practice databases to try to decrease duplication, foster innovation and improve production.
But the systems had problems from the start, and knowledge management initiatives ultimately failed, according to a report by the Economist Intelligence Unit, due to “internal silos, resistance to behavioral change and the lack of an open culture in which knowledge is shared.”
Concerns around knowledge sharing remain prevalent in organizations trying to utilize analytics, dashboards and data-driven insights today. And on top of this, today’s manufacturing organizations must quickly contend with the growing skills gap because:
The good news? There are actually more jobs available than ever.
In fact, Deloitte revealed that job openings have been growing at double-digit rates since mid-2017, and are nearing the historical peak recorded in 2001. Plus, with the Fourth Industrial Revolution of artificial intelligence (AI), advanced robotics, analytics, automations and the Internet of Things (IoT) in full swing, data capture and technological advancements hold more promise than ever before. In other words, there’s tons of opportunity in the new future of work.
However, it still requires closing the skills gap, and knowledge management can help strengthen and retain these must-have skills in the workplace. Here’s how.
The overarching idea of KM is to make formal, informal, and tacit knowledge available and easily accessible across sites and geographic locations. That way, it can be used to improve processes and bring products to market faster and more inexpensively than previously possible.
The biggest hurdle here is that this information exists in both structured and unstructured sources across systems, locations and individuals. This is particularly true if you have executives in different divisions or facilities in different cultures or in different languages.
The first step, then, is to firmly establish where all of your information resides. Then, once you have your information accounted for, you need to make sure that your knowledge management systems are properly connected to all relevant software modules, projects and systems for them to work.
With that in mind, comprehensive knowledge management efforts should include:
A content management system will make an organization’s important information readily available through dashboards, portals and collaborative systems.
To get this right, it’s important to:
If you can, you’ll want to incorporate information from your retiring skilled workers and make sure that they are involved in discussions and easily located through your expertise locator system.
Here, it’s important to remember that the old adage, “If you build it, they will come,” does not apply here. If your people are not on board, any kind of knowledge system simply won’t work. To this end, it’s important that your dashboards and tools are user-friendly and intuitive.
It’s also important that you improve your training and onboarding to improve recruiting, lessen the severity of the skills gap and ensure that your entire team can actually use your systems. To ensure this, you can digitize instructions or take advantage of digital tools like augmented reality to improve training and attract digital native top talent. That way, your people will actually use your dashboards and your content management systems will actually work.
Keep in mind that, when it comes to knowledge acquisition, there is nothing better than talking to an expert. You want to make it as easy as possible to find those experts in your network. That’s where an expertise locator comes in: a system that helps you identify and locate experts quickly and efficiently.
It’s essentially a digitized “Yellow Pages” for all of the experts in your network. You can populate your expertise locator using:
A lessons learned database is essentially an encyclopedia of best practices or, more informally, a great big book of here’s the mistakes we made and how to avoid them. This is where you can really compile the tacit, on-the-job knowledge that your workers won’t find formally in a handbook or in a classroom.
To compile this database, your employees need to immediately debrief and share their information after an activity or job. Without this kind of follow-through, the “lessons learned” section will be impossible to compile.
Communities of practice (CoPs), as the name suggests, are groups that come together within a community to discuss problems, best practices, stories and lessons learned. These communities build upon the social nature of knowledge dissemination, which is extremely important in organizations.
Think about how much you learn around the water cooler – well, you should make sure that you have the opportunity for that kind of collaborative collision across buildings and even countries.
In other words, you need to take your CoPs virtual to electronically link your communities and make sure that your organization is on the same page. This requires that you fill critical roles, including a CoP manager, a moderator and a thought leader.
To figure out exactly what your CoP team will look like, ask yourself:
Finally, keep in mind that it’s not just about organizing the information that you already have but also about identifying and filling any gaps that you may have in your knowledge databases. Think of it like organizing your belongings for a big move – you don’t just want to keep track of what you have, but also notice what might be missing that you’ll need for your new space.
Ok, now you may be wondering why should I go through all this effort to get these systems going? Well, knowledge management leads to:
Knowledge is power, particularly in the data-driven business world we live in today. When you can identify, disseminate and apply knowledge through knowledge management, you can improve processes, close the skills gap, and bring new products to the market faster and more cheaply. And that’s ultimately what every business wants to do.
See how an engineering information management system can help kickstart your digital transformation and ensure critical knowledge is preserved.
Identify the role that IoT plays in your organization and how to successfully implement it to meet your needs.
Discover how energy management systems enhance energy monitoring, conservation, and budgeting, while boosting sustainability efforts in your ...
Cloud content management has taken center stage since the pandemic. Learn what it is, why it’s essential to your business, and what leading platforms ...
Subscribe to stay up to date with our latest news, resources and best practices