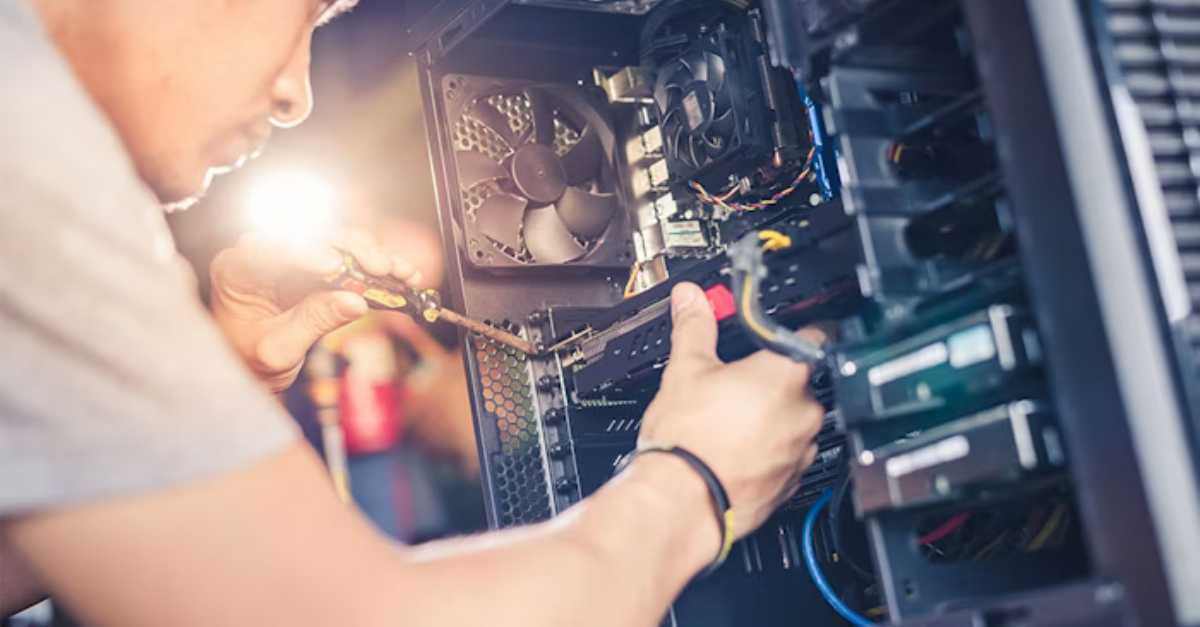
The Importance of Hardware Agnostic IoT Platforms
Investing in agnostic IoT remote monitoring tools can eliminate data siloes and improve cross-device communication and insight.
Solutions
Workplace Management Solutions
Real Estate Management Solutions
Maintenance Management Solutions
Energy Management Solutions
Engineering Document Management Solutions
Asset Management Solutions
Automate campus scheduling for classes, meetings, and exams with our EMS software.
Plan and manage conferences effortlessly with EMS software to impress guests and streamline operations.
Boost workplace flexibility and maximize space use with seamless desk and room booking.
Organize workplace or campus events smoothly, creating memorable experiences.
Optimize workspace, manage allocations efficiently, and reduce costs with our space management solutions.
Deliver projects on time and within budget by improving communication, collaboration, and efficiency with our software.
Streamline lease accounting for ASC 842, IFRS, and GASB compliance.
Manage leases efficiently by tracking key dates, analyzing costs, and ensuring compliance.
Centralize data and analytics for better insights, faster negotiations, and revenue growth.
Centralize facility and asset maintenance, automate work orders, and ensure compliance with our CMMS software.
Extend asset life, reduce downtime, and prevent costly repairs with data-driven monitoring.
Prevent equipment failures and extend asset life by detecting and addressing issues early.
Make sustainable, cost-efficient energy decisions by monitoring and optimizing power consumption.
Remotely monitor and control equipment with real-time data to predict issues, boost efficiency, and reduce downtime.
Easily share and collaborate on documents, creating a single source of truth for engineers and contractors.
Manage and analyze assets across their lifecycle to schedule maintenance, reduce downtime, and extend lifespan.
Improve visibility, automate work orders, and ensure compliance for efficient facility and asset management.
Resources
Browse our full library of resources all in one place, including webinars, whitepapers, podcast episodes, and more.
Support
Looking for access to technical support, best practices, helpful videos, or training tools? You’ve come to the right place.
About Accruent
Get the latest information on Accruent, our solutions, events, and the company at large.
Learn how to “turn down the noise” on alarms that detect anomalies and discover how to detect real problems that affect your company’s bottom line.
By Basant Singhatwadia, VP of IoT Product Strategy, Accruent
Equipment controllers alarm whenever an anomaly is detected. This causes a lot of alarm noise and distraction for store employees as equipment cannot dynamically tell you which alarms are real problems that need to be addressed and which ones are not. Did a customer leave a refrigerator door open too long? Is a cabinet in a defrost cycle? All the refrigerator can do is send an alarm and your employee will need to follow up.
This is where remote monitoring comes in to help. Remote monitoring sits on top of your equipment’s control system to help you contextualize and filter out excess alarms that these devices generate and will only alert your store and maintenance staff to issues that need to be addressed. This helps prevent your staff from getting bogged down with or ignoring all alarms or chasing non-issues rather than helping your customers.
Device manufacturers sell their hardware based on the capability to generate numerous alarms, promising that no issues will fall between the cracks. In the real world, only 5-10% of these alarms will actually be an issue that a person has to stop and fix. But increased alerts cause businesses to bring on additional resources to look at each individual alarm, only to ensure they catch the 5-10% of issues that really make an impact to the business. This is common practice in today’s facilities call centers.
Adding a call center to your business is costly and introduces even more possibility for human error. People misinterpret, miss key trends and they can even fall asleep on their shifts. This also causes problems when looking at repeat alarms.
Our customers have seen a couple key areas where call centers tend to go wrong. The first is around first-time fix. If the first-time fix is not achieved on a maintenance related work order, a call center agent can only call a provider back once they have left, potentially causing trip charges and additional invoices. The second issue is around identifying root cause for alarms. If an electrical problem is causing seven lights to be out at once, a call center agent will place seven different work orders. This often leads to multiple truck rolls and wasted spend.
When selecting a remote monitoring platform, your business should take into consideration the system’s capacity and ability to accurately handle your needs without throwing people at the problem. A remote monitoring platform should be able to handle the ingestion of millions of controller alarms per a day at an enterprise level, while adding the context of your buildings and devices to ensure it is filtering the most noise possible.
Contextualizing your data is also extremely important when filtering out nuisance alarms. Otherwise you can miss key issues or even worse create more issues than expected. Pairing your asset data with maintenance history, weather data, location data and building attributes can greatly increase accuracy and give much needed context to your maintenance team when addressing alarm issues.
Ultimately, a successful IoT platform is key to helping reduce excessive equipment alarm noise and ensure that your staff stays focused on only the alarms that really matter.
Investing in agnostic IoT remote monitoring tools can eliminate data siloes and improve cross-device communication and insight.
Explore the essentials of IoT remote monitoring in this introduction.
Discover how to implement a closed maintenance loop that identifies potential risks and solves them with automated processes.
Subscribe to stay up to date with our latest news, resources and best practices