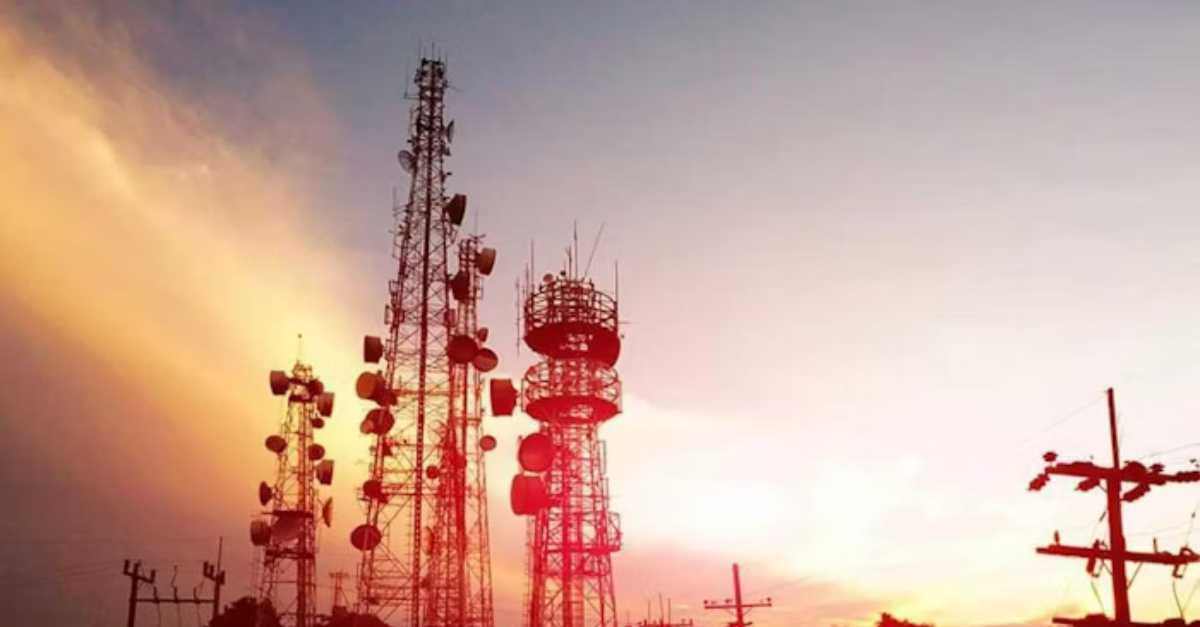
Monitor Critical Telecom Equipment with IoT Remote Monitoring
Find out how to achieve significant cost savings by switching from reactive to preventive maintenance.
Solutions
Workplace Management Solutions
Real Estate Management Solutions
Maintenance Management Solutions
Energy Management Solutions
Engineering Document Management Solutions
Asset Management Solutions
Automate campus scheduling for classes, meetings, and exams with our EMS software.
Plan and manage conferences effortlessly with EMS software to impress guests and streamline operations.
Boost workplace flexibility and maximize space use with seamless desk and room booking.
Organize workplace or campus events smoothly, creating memorable experiences.
Optimize workspace, manage allocations efficiently, and reduce costs with our space management solutions.
Deliver projects on time and within budget by improving communication, collaboration, and efficiency with our software.
Streamline lease accounting for ASC 842, IFRS, and GASB compliance.
Manage leases efficiently by tracking key dates, analyzing costs, and ensuring compliance.
Centralize data and analytics for better insights, faster negotiations, and revenue growth.
Centralize facility and asset maintenance, automate work orders, and ensure compliance with our CMMS software.
Extend asset life, reduce downtime, and prevent costly repairs with data-driven monitoring.
Prevent equipment failures and extend asset life by detecting and addressing issues early.
Make sustainable, cost-efficient energy decisions by monitoring and optimizing power consumption.
Remotely monitor and control equipment with real-time data to predict issues, boost efficiency, and reduce downtime.
Easily share and collaborate on documents, creating a single source of truth for engineers and contractors.
Manage and analyze assets across their lifecycle to schedule maintenance, reduce downtime, and extend lifespan.
Improve visibility, automate work orders, and ensure compliance for efficient facility and asset management.
Resources
Browse our full library of resources all in one place, including webinars, whitepapers, podcast episodes, and more.
Support
Looking for access to technical support, best practices, helpful videos, or training tools? You’ve come to the right place.
About Accruent
Get the latest information on Accruent, our solutions, events, and the company at large.
Discover how to implement a closed maintenance loop that identifies potential risks and solves them with automated processes.
By Basant Singhatwadia, VP of IoT Product Strategy, Accruent
Most of the remote monitoring solutions on the market today do not integrate with downstream Computerized Maintenance Management System (CMMS) solutions, which makes a closed-loop system nearly impossible. This can cause many problems for the end-user and maintenance teams, and inherently limits the scope of your solution.
A comprehensive IoT solution should integrate several CMMS solutions and the architecture should also allow additional integrations for other CMMS solutions with ease, requiring less time to set up. This allows for problem identification-to-resolution coverage for your facilities with a closed-loop system that ensures work orders are fixed correctly the first time.
By creating a closed-loop system for your maintenance, you are streamlining the process from problem to solution and ultimately making it easier on your maintenance teams to track spending, reduce reactive maintenance and spend more time thinking strategically about your business’s critical assets.
Find out how to achieve significant cost savings by switching from reactive to preventive maintenance.
Learn how to harness the power of Big Data, IoT remote monitoring, and mobile tools to transform your retail operations.
IoT remote monitoring helps companies manage their assets remotely, in real-time, with devices and sensors that collect data and transmit it over the ...
Subscribe to stay up to date with our latest news, resources and best practices