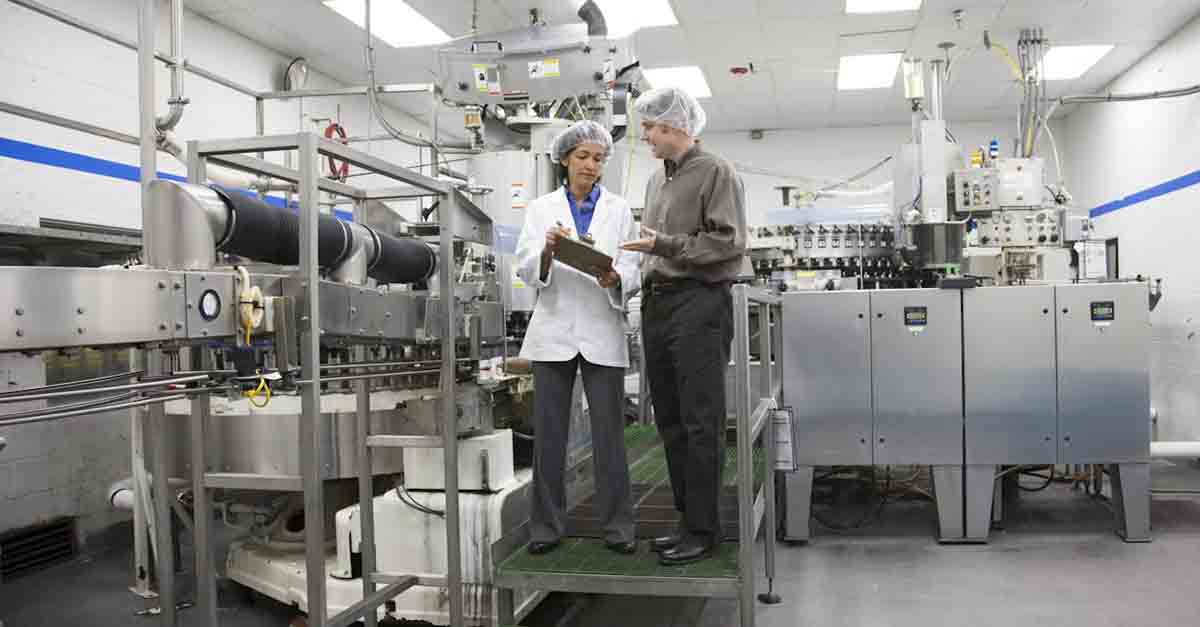
Facility Management: 26 Benefits for Efficient Operations
Discover essential insights and best practices in facility management for seamless operations, cost savings, and ongoing satisfaction.
Solutions
Resources
Browse our full library of resources all in one place, including webinars, whitepapers, podcast episodes, and more.
Support
Looking for access to technical support, best practices, helpful videos, or training tools? You’ve come to the right place.
About Accruent
Get the latest information on Accruent, our solutions, events, and the company at large.
Maintaining equipment, fleets, and machinery is a necessary but time and resource-intensive process. Viewing decentralised assets and understanding where maintenance is required without shutting down critical parts of the business can be challenging unless companies deploy CMMS.
How much does maintenance cost your company? It's likely that, with a bit of checking, any reasonably well-run business should be able to determine how much it costs to keep their production lines, fleets and other machinery and equipment running.
But what about the lost cost? Or rather, what about the lost opportunities? Any asset-rich company will know the importance of maintenance – as well as the cost of getting maintenance wrong. According to a survey by Plant Engineering, the leading cause of unscheduled downtime within respondents' facilities remains ageing equipment (40%), followed by mechanical failure (24%). Yet overcome these problems, and the rewards can be significant; a McKinsey article notes that by "dramatically reducing unplanned outages while boosting maintenance-labour productivity", some businesses have been able to increase "profitability by 4 to 10 per cent".
But how do companies get to that point? The challenge can be knowing when the time is right to take an asset out of service and run a maintenance programme. Many turn to predictive maintenance to simplify these processes – Plant Engineering's survey suggests more than three-quarters (78%) of manufacturing facilities follow a preventive maintenance strategy, while 61% have a computerised maintenance management system (CMMS) in place.
A CMMS is a software system that:
CMMS software can be deployed to manage equipment, fleet, and machinery lifespans. It can also be used to enhance asset use and availability across multiple locations, while providing transparency across a diverse, decentralised asset estate.
Modern CMMS can also provide enterprise asset management-level functionalities. To make the most out of this functionality, they should also be able to integrate with other integral tools like space planning, mobile surveying tools, and Internet of Things remote monitoring tools.
CMMS software as a concept has been around for a while, but new systems should provide users with specific benefits in line with the latest user expectations. These include:
We're all operating in the digital transformation era, with a pace of change unlike anyone has ever seen. Trying to keep up with the evolution of technology can be challenging, and it can sometimes feel like a new implementation is out of date by the time it is up and running.
To avoid this, businesses should be looking for CMMS software that offers future-proofed capabilities, including:
As with any technology investment, much of the success can lie in the solution's integration. A CMMS can be a significant commitment, so businesses must do their due diligence on the tool and the vendor themselves.
At a minimum, companies should expect a proper support programme from the vendor, including help with implementation and training and troubleshooting support.
To get that, look for a provider committed to building a partnership and doesn't see the deal as a transactional process. As well as after-sales support, this can include customised capabilities that build on the existing features to allow a business to tailor their CMMS investment to fit their specific needs. Some vendors will baulk at this, but a system as critical as CMMS should work for the customer, not the provider
Ultimately, a CMMS is an integral part of any maintenance management software toolset, helping users to manage work orders, track inventory and schedule maintenance operations. All from one centralised platform in real-time. Get in touch to see how you could acquire and deploy a CMMS that meets the needs of your equipment, fleet and machinery.
You might also like
Discover essential insights and best practices in facility management for seamless operations, cost savings, and ongoing satisfaction.
Is your organisation looking to introduce a hybrid work model that involves some combination of in-office and remote work? Discover how hot desking ...
Learn about capital lease accounting including key differences from operating leases, impact on balance sheets, and compliance with accounting ...
Subscribe to stay up to date with our latest news, resources and best practices