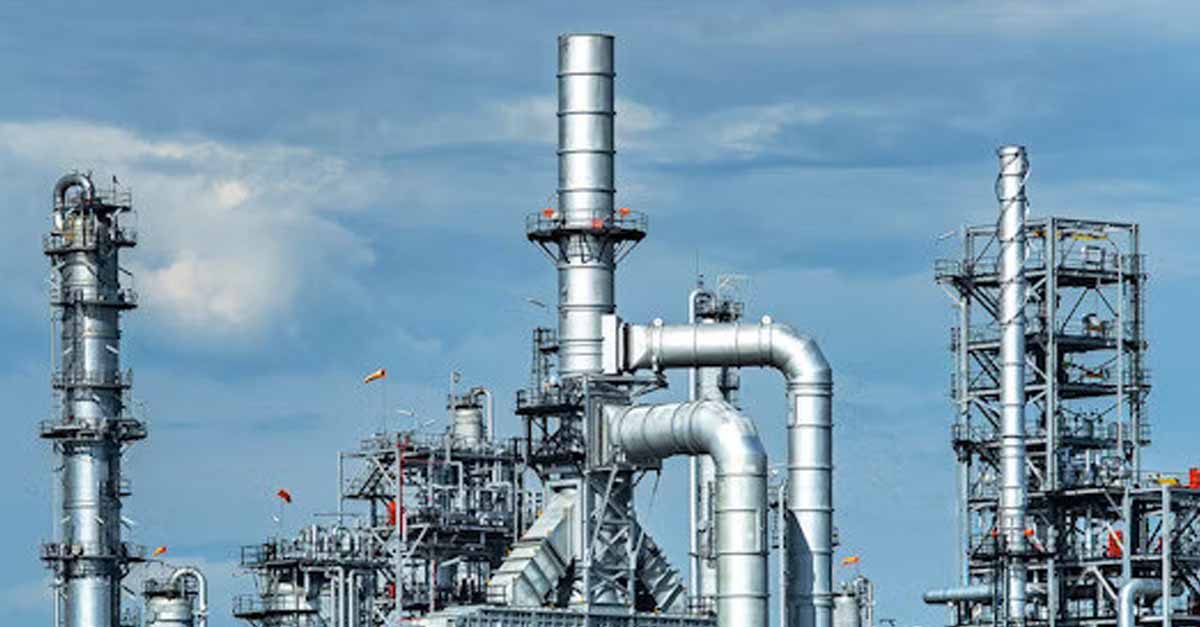
3 Elements of Maintenance Success in the Chemical Industry
How comprehensive asset intelligence, effective preventive maintenance, and efficient labor scheduling can lead to success in the chemical industry.
Solutions
Workplace Management Solutions
Real Estate Management Solutions
Maintenance Management Solutions
Energy Management Solutions
Engineering Document Management Solutions
Asset Management Solutions
Automate campus scheduling for classes, meetings, and exams with our EMS software.
Plan and manage conferences effortlessly with EMS software to impress guests and streamline operations.
Boost workplace flexibility and maximize space use with seamless desk and room booking.
Organize workplace or campus events smoothly, creating memorable experiences.
Optimize workspace, manage allocations efficiently, and reduce costs with our space management solutions.
Deliver projects on time and within budget by improving communication, collaboration, and efficiency with our software.
Streamline lease accounting for ASC 842, IFRS, and GASB compliance.
Manage leases efficiently by tracking key dates, analyzing costs, and ensuring compliance.
Centralize data and analytics for better insights, faster negotiations, and revenue growth.
Centralize facility and asset maintenance, automate work orders, and ensure compliance with our CMMS software.
Extend asset life, reduce downtime, and prevent costly repairs with data-driven monitoring.
Prevent equipment failures and extend asset life by detecting and addressing issues early.
Make sustainable, cost-efficient energy decisions by monitoring and optimizing power consumption.
Remotely monitor and control equipment with real-time data to predict issues, boost efficiency, and reduce downtime.
Easily share and collaborate on documents, creating a single source of truth for engineers and contractors.
Manage and analyze assets across their lifecycle to schedule maintenance, reduce downtime, and extend lifespan.
Improve visibility, automate work orders, and ensure compliance for efficient facility and asset management.
Resources
Browse our full library of resources all in one place, including webinars, whitepapers, podcast episodes, and more.
Support
Looking for access to technical support, best practices, helpful videos, or training tools? You’ve come to the right place.
About Accruent
Get the latest information on Accruent, our solutions, events, and the company at large.
Identify the role of planned downtime and how it creates challenges for manufacturing maintenance organizations and explore how to minimize those challenges.
Recent studies indicate that unplanned downtime costs industrial manufacturers an estimated $50 billion each year. “The cost of unplanned downtime can be devastating, ranging from an estimated $10,000 to $250,000 per hour for industrial plants”, according to Asset Performance Management: Blazing a Better Path to Operational Excellence, November, 2017.
Most organizations have at least some idea of their unplanned downtime costs. While it may represent significant money, many companies are not focused on addressing the problem, which is why industry-wide costs remain in the billions of dollars.
For companies that have begun to address their asset health and have implemented programs to reduce unplanned downtime, the results are significant. According to Aberdeen, plant unscheduled downtime for the Best-in-Class (top 20% of respondents based on performance) is four times better than that of All Others. Best-in-Class manufacturers also report a year over year unplanned downtime decrease of 9% while All Others reported no decrease at all, according to Asset Performance Management: Blazing a Better Path to Operational Excellence, November, 2017.
The graphic below shows several steps that manufacturing companies can take to begin addressing unplanned downtime.
Implementing a Computerized Maintenance Management System (CMMS) like Maintenance Connection is a straightforward way to begin moving from a reactionary approach to unplanned downtime events to a proactive mindset that can not only reduce unplanned downtime, saving companies money, but also lower overall maintenance program costs.
The initial entry point is, in many cases, much lower than a single unplanned downtime event. A CMMS is a critical foundation on which to build an effective maintenance program. Many companies have taken this step, while others continue to use spreadsheets or even paper-based systems. These approaches can make it challenging to concisely collect data and it can also be very difficult to extract meaningful data from manually reviewing stacks of paper with a large volume of work order history.
The insight from a CMMS can be used to create an effective proactive maintenance or Preventive Maintenance (PM) program. Calendar-based approaches to PMs are common, and may be weekly, monthly, quarterly, etc. depending on the system. Leading companies estimate that 33% of organizational asset maintenance is “proactive maintenance.” According to "The Rise of Remote Assets" by the Aberdeen Group, October 2017.
As easily searchable data becomes available in digital format, identifying trends is simplified. Conclusions can be drawn from that data about what triggers repetitive equipment downtime, whether it be the number of revolutions of a motor or something like a temperature reading from an associated piece of equipment. These triggers can be used to establish a Predictive Maintenance program. Developing a PM program generally requires having robust instrumentation in place and a complete understanding of how various process and asset information is related and the ways they can impact equipment downtime. Significant progress can be made in battling unplanned downtime through either proactive approach which can be useful in helping companies reduce, and often eliminate, unplanned downtime.
Manufacturing companies are continuing to lose significant money as a result of unplanned downtime. A CMMS is a strong first step in getting unplanned downtime under control.
Learn how Maintenance Connection helped the New York Times Automate Preventive Maintenance.
How comprehensive asset intelligence, effective preventive maintenance, and efficient labor scheduling can lead to success in the chemical industry.
Here's how a CMMS can help you optimize inventory management, aggregate maintenance data, and digitize your operations in the chemical industry.
Looking to improve your Overall Equipment Effectiveness (OEE)? Here's how Maintenance Connection can help make that happen.
Subscribe to stay up to date with our latest news, resources and best practices