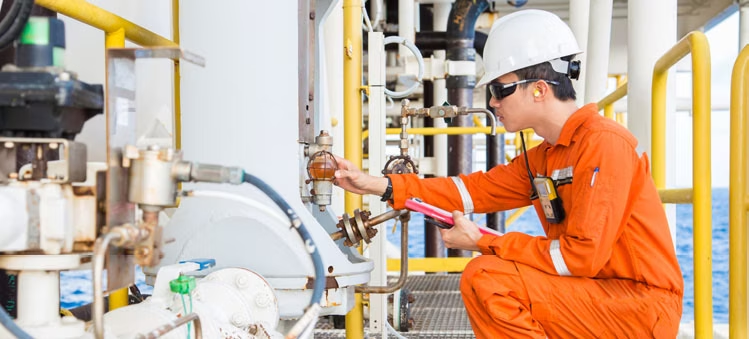
Mitton Group
See how Mitton Group increased visibility into and control over its field service and workflow processes to improve efficiency and reduce costs.
Solutions
Resources
Browse our full library of resources all in one place, including webinars, whitepapers, podcast episodes, and more.
Support
Looking for access to technical support, best practices, helpful videos, or training tools? You’ve come to the right place.
About Accruent
Get the latest information on Accruent, our solutions, events, and the company at large.
Table of contents
ANNUAL TURNOVER
INCREASE IN THE NUMBER OF ASSETS
TIME SPENT MANAGING THE SYSTEM
Our primary objective is to drive continuous improvement and implement best practices to achieve excellence in manufacturing and engineering. Accruent Maintenance Connection has been transformative in realising this.”
–George Morant, Global Manufacturing Engineering Manager, WMFTS
Watson-Marlow Fluid Technology Solutions (WMFTS) is a division of the Spirax Group, a multinational industrial engineering company. With an annual turnover of almost £400m in 2023, WMFTS is a world leader in manufacturing peristaltic pumps and associated fluid path technologies for the life sciences and process industries. Its solutions keep industries productive worldwide, saving time and money by handling the toughest applications for end users, OEMs, and integrators.
WMFTS had been a Maintenance Connection user for several years. The CMMS was initially adopted to help the company evolve from paper-based processes, and to make it easier for its engineers to improve recordkeeping, workflows, and compliance. It was widely adopted, with multiple businesses within the group using it at their sites.
While this approach fostered autonomy, it inadvertently led to some operational inefficiencies, such as the unintended reallocation of licences between sites.
This, in turn, created a number of issues, particularly around system access and the handling of maintenance work orders. WMFTS had thousands of open work orders that were difficult to manage due to licence availability issues.
This highlighted the need for a more centralised and structured approach. At the same time, it was also made clear that the escalation process needed refinement, as multiple helpdesk tickets for the same issues were causing delays in response times from Accruent’s support team.
In late 2023, WMFTS embarked on a year of positive transformation to unlock the full potential of the Maintenance Connection platform. This involved making a series of changes, including:
This strategy of continuous improvement has had a transformative impact on the day-to-day operations at WMFTS, leading to a number of benefits. Centralised licence management has ensured consistent and efficient management across WMFTS, while increased efficiency in the escalation process has significantly reduced delays and improved response times. Creating one centralised platform has also made the solution a valuable resource for updates, best practices, and user engagement, with engineering teams able to instantly access the necessary tools and knowledge to maximise their use of the system.
Additionally, despite seeing an almost 150% increase in assets within the system in a year, WMFTS has seen no impact on management time. Indeed, the single system owner estimates Accruent takes up no more than 5% of the working week, while the focused effort has led to significant improvements in how WMFTS operates globally. For this reason, Maintenance Connection has been extended beyond facilities to encompass additional functions of the business.
Accruent has become a valued tool across WMFTS extending beyond the facilities department to benefit other areas of the business. This expansion highlights its growing role in improving operational efficiency and collaboration.”
-George Morant, Global Manufacturing Engineering Manager, WMFTS
See how Mitton Group increased visibility into and control over its field service and workflow processes to improve efficiency and reduce costs.
Learn how French company L'Oreal decreased asset downtime, improved reporting, and maximised asset life with Maintenance Connection CMMS.
Learn how Urban Utilities migrate over 900,000 asset records from an on-premise system to a cloud-based solution, improving the management and ...
Subscribe to stay up to date with our latest news, resources and best practices