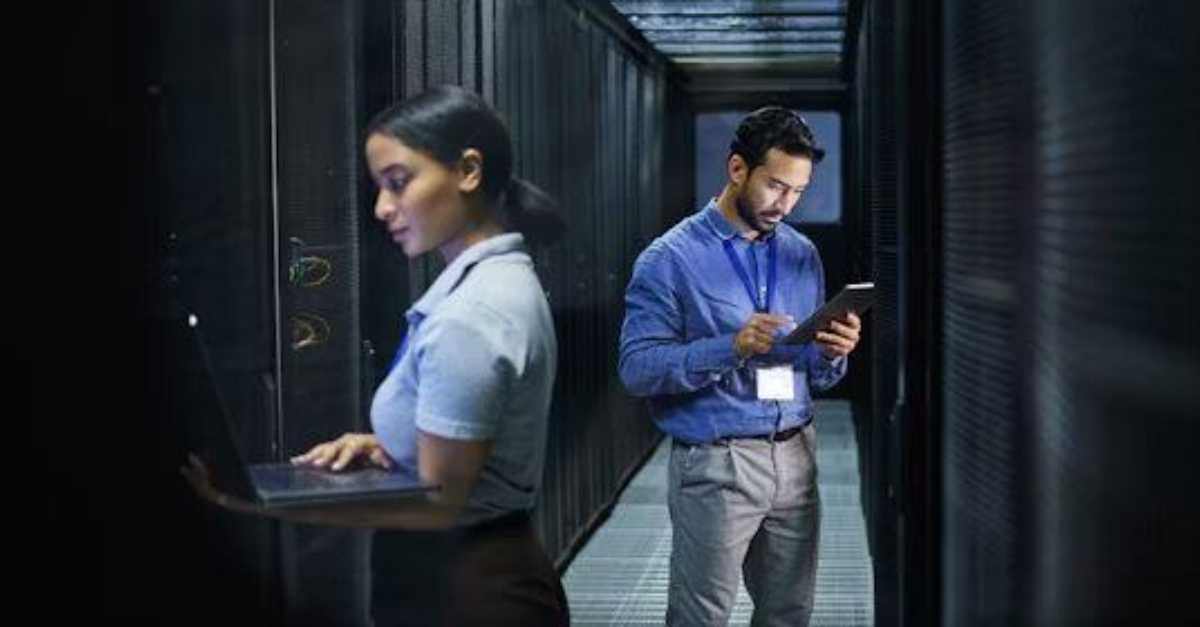
From Fork to Firewall: Assessing the Impact of Cybersecurity on the Post-COVID F&B Industry
Learn more about the latest cyber security challenges that food and beverage organisations face post-COVID and what you can do to protect your ...
Solutions
Resources
Browse our full library of resources all in one place, including webinars, whitepapers, podcast episodes, and more.
Support
Looking for access to technical support, best practices, helpful videos, or training tools? You’ve come to the right place.
About Accruent
Get the latest information on Accruent, our solutions, events, and the company at large.
Explore the role that quality management systems and product recalls play in maintaining consumer trust and safety in the food and beverage industry.
In the competitive and dynamic landscape of the food and beverage industry, product quality takes center stage, influencing everything from brand reputation to consumer safety and compliance. Yet product quality is not achieved in isolation. Rather, it is the result of a robust quality management program that not only strives to achieve a high level of quality in production processes but also to identify and mitigate potential quality issues before they can escalate.
In this article, we will discuss why food and beverage organisations need comprehensive quality management plans, what they include, and the integral role that product recalls play in quality management.
Quality management is a method for ensuring that a product or service consistently satisfies internal and external quality standards. A comprehensive quality management program has four key components: quality planning, quality control, quality assurance, and quality improvement. Quality management is particularly important in the food and beverage industry for several reasons.
First, quality management systems help ensure that products are safe for human consumption. Through quality control processes, organisations can help prevent contamination and other safety issues that can result in harm to consumers. Second, the industry is among the most highly regulated, with strict regulations and standards that control how products are produced and distributed. Quality control makes sure that products comply with these regulations, while quality improvement allows organisations to continually refine their processes to boost compliance.
Third, the food and beverage industry is highly competitive. Satisfying consumers through products that are manufactured to their quality expectations is crucial to building brand loyalty and repeat business. A comprehensive quality management program is needed to address all aspects of the customer experience.
Establishing a robust quality management program requires a multi-faceted approach. This process can vary among organisations but generally consists of the following components:
The first step is to define the quality standards that products must meet. This involves identifying applicable standards and regulations, what they require, as well as documenting internal quality standards. Some examples of relevant parameters may include manufacturing processes, ingredient specifications, and final product characteristics.
This step involves creating and implementing documented processes and procedures that guide employees in adhering to quality standards. In addition to production processes and quality control inspections, your standards should cover things like preventive maintenance tasks to ensure that equipment performs at an optimal level.
Regular inspections and audits are essential components of a comprehensive quality management program. These processes involve the systematic review of production processes, equipment, facilities, and products to ensure compliance with documented standards. Inspections may occur at various stages, such as raw material sourcing and final product checks. Routine internal and external audits provide a holistic view of the organisation’s adherence to quality standards.
Testing protocols help verify the quality of raw materials, intermediates, and finished products. Organisations develop and implement specific testing procedures, which may include chemical analysis, microbial testing, physical attributes assessment, and sensory evaluations. Rigorous testing helps identify deviations from standards and allows for corrective actions to be taken before products reach consumers.
Many businesses leverage digital technologies to enhance their quality control processes. For instance, automation, data analytics, and artificial intelligence can play significant roles in ensuring precision and efficiency in testing and monitoring procedures. These technologies enable real-time data analysis, quick identification of potential issues, and faster decision-making. Moreover, they make it easy to assign inspection and maintenance tasks and track their status to ensure that they are completed on time.
While quality management strives to prevent lapses in product quality, the reality is that unforeseen issues can still arise. This is where product recalls can become a necessity, serving as a strategic move to protect consumers, uphold brand integrity, and demonstrate a commitment to transparency and accountability. Product recall procedures should be addressed and detailed in your quality management documentation. They generally consist of three key steps.
The first and perhaps the most important step in the process is to identify the issues. Advanced technologies, routine testing protocols, and continuous quality assessments are integral components of this proactive identification process. By pinpointing issues early on, organisations can initiate corrective actions promptly, preventing widespread harm and demonstrating a commitment to consumer safety.
Engaging in transparent and open dialogue with stakeholders, including consumers, retailers, and regulatory bodies, is paramount. Clear and concise messaging regarding the nature of the recall, potential risks, and corrective measures not only fosters trust but also empowers consumers to make informed decisions. Timely and honest communication demonstrates accountability and underscores the company's commitment to putting consumer safety above all else.
Time is of the essence when it comes to product recalls. Once issues are identified and communicated, the next critical step is the prompt removal of affected products from the market. This requires a well-coordinated effort involving logistics, distribution channels, and collaboration with retailers. A rapid response not only minimises the potential harm to consumers but also reduces the window of reputational damage.
For instance, in 2006 Cadbury recalled more than one million chocolate due to a leaking pipe in its Marlbrook plant in Leominster. The company feared that milk chocolate crumb produced at the plant was contaminated with salmonella due to the leak in January 2006. While Cadbury proactively recalled the products, the company waited until June to notify the UK Food Standards Agency. In addition to the cost of the recall (£20m), Cadbury also had to pay a fine of £1m to Birmingham City Council, which illustrates how failing to comply with regulations can result in substantial unnecessary costs.
Maintaining equipment is a crucial component of a comprehensive quality management program. When equipment malfunctions, it can not only lead to unplanned downtime but also process deviations. These issues can introduce contamination or variability in product quality, posing serious threats to consumer health and brand identity.
Accruent is a leading provider of innovative solutions that help food and beverage organisations maximise the performance of the built environment, streamline day-to-day operations, and maintain compliance and quality standards. Maintenance Connection is a best-in-class CMMS solution that helps food and beverage organisations analyse, manage, and track their assets throughout all stages of the lifecycle. This helps streamline maintenance tasks and maximise machine performance.
Want to discover more about how Maintenance Connection can help your organisation to consistently achieve quality standards? Visit the Maintenance Connection product page to learn more. For more information and to request a demo, get in touch via our website.
Learn more about the latest cyber security challenges that food and beverage organisations face post-COVID and what you can do to protect your ...
Discover why food and beverage manufacturers experience asset downtime and learn strategies to overcome challenges and transform your processes.
Explore some proven methods for ensuring that a successful CMMS implementation in the food and beverage manufacturing industry.
Subscribe to stay up to date with our latest news, resources and best practices