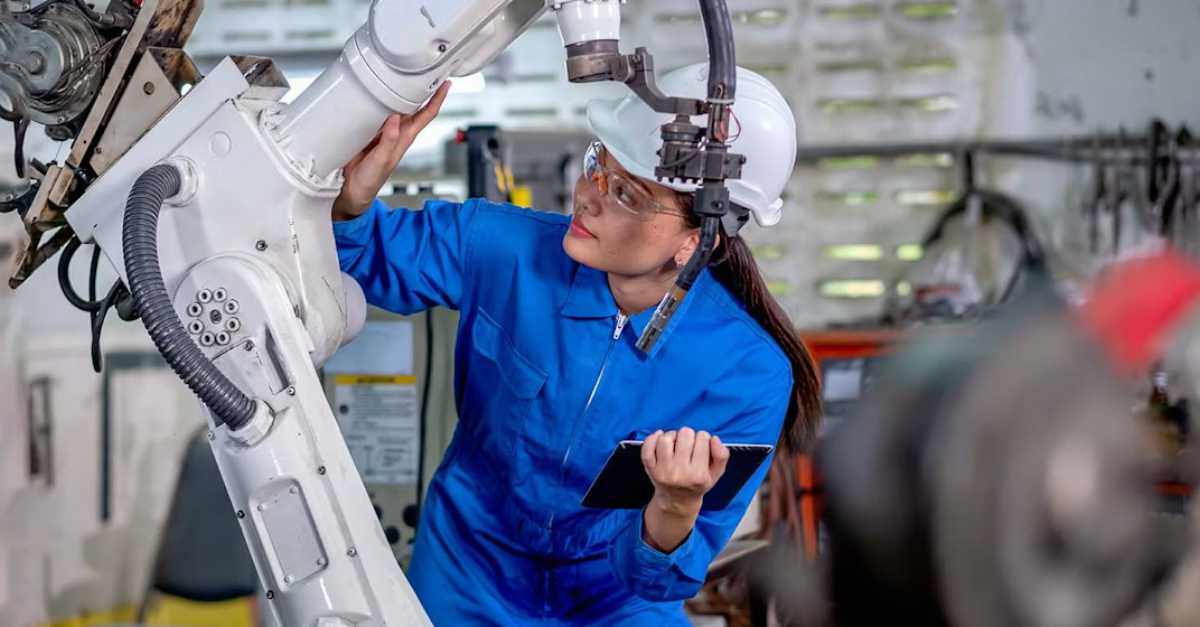
How CMMS is Transforming Manufacturing
As manufacturers digitally transform, their maintenance practices also need to evolve. Shifting to proactive forms of maintenance makes sense, but to ...
Solutions
Resources
Browse our full library of resources all in one place, including webinars, whitepapers, podcast episodes, and more.
Support
Looking for access to technical support, best practices, helpful videos, or training tools? You’ve come to the right place.
About Accruent
Get the latest information on Accruent, our solutions, events, and the company at large.
Discover why food and beverage manufacturers experience asset downtime and learn strategies to overcome challenges and transform your processes.
In the fast-paced world of food and beverage manufacturing, time is a valuable commodity. The bustling manufacturing floor and constant hum of machinery are a testament to the relentless pursuit of quality and productivity. Yet when unexpected equipment breakdowns occur, it can all come to a grinding halt. In this article, we will explore some of the factors that can contribute to asset downtime, the negatives associated with unplanned interruptions, and some strategies that you can use to mitigate such challenges.
Causes of asset breakdown in the food and beverage industry generally fall into several categories, including:
When machine components succumb to breakdowns, the entire production line can be forced to the sidelines. Frequent breakdowns can lead to extended periods of unplanned downtime, resulting in substantial costs. According to research by Aberdeen, a single hour of machine downtime costs a company an average of $260,000, which does not even account for maintenance expenses.
Proactive strategies such as preventive maintenance involve performing routine maintenance tasks to ensure that assets are operating at peak efficiency and do not break down unexpectedly. However, when there are delays in routine maintenance, whether due to oversight or resource constraints, breakdowns can and do occur. This often results in more extensive repairs and longer periods of downtime.
Inefficient processes can contribute to asset downtime. For instance, poor resource allocation and production planning such as not planning the transition from one recipe to another, and inadequate training can contribute to extended periods of downtime.
Given the growing labor shortage, maintenance departments can hardly afford added challenges stemming from inefficiencies. In fact, according to the Plant Services annual PdM survey, some 9% of respondents reported that their organisation’s maintenance department consisted of “Just Me,” while another 20% indicated that they were on a team of between 2 and 4 people.
When unexpected downtime does occur, it can negatively impact manufacturing processes throughout the organisation. Some consequences of asset downtime include:
Unplanned asset downtime almost always results in production delays. This not only negatively impacts overall output but can disrupt supply chains and fulfillment schedules, potentially resulting in contractual penalties, a tarnished reputation, and jeopardising relationships with distributors and suppliers.
Unplanned downtime directly translates into higher costs, such as emergency repairs, expedited shipping for replacement parts, and overtime pay for technicians. And these added expenses are not insignificant, with experts estimating that maintenance costs range between 15% and 40% of total production costs.
In the food and beverage industry, customer satisfaction is paramount. Unplanned downtime can lead to product shortages, delays, and issues with product quality, potentially leading to customer dissatisfaction and a loss of trust.
Fortunately, there are some proven strategies that food and beverage manufacturers can implement to reduce the likelihood of unplanned asset downtime.
Implementing proactive maintenance strategies, such as preventive and condition-based maintenance, can significantly reduce the likelihood of experiencing unplanned downtime. Preventive maintenance involves regular and scheduled inspections, routine cleaning, lubrication of moving parts, calibration of machines that rely on precision, periodic testing of equipment performance, and replacement of equipment components before they fail.
In addition to reducing the frequency of unplanned downtime, preventive maintenance can dramatically reduce repair costs. One survey conducted by Viking Analytics compared preventive maintenance to reactive maintenance and found that preventive maintenance can lower the cost of machinery repairs by as much as 40%.
Leveraging predictive analytics helps to identify potential issues before they escalate. The method involves analysing historical data, monitoring equipment performance, and using predictive modeling to anticipate maintenance needs and address them proactively.
According to one report, the use of predictive analytics can help organisations to realise a tenfold return on investment, resulting in savings of 30% to 40%.
Real-time asset monitoring involves utilising sensors and IoT devices to collect data on equipment health, performance, and potential failure. Technicians can then perform maintenance tasks at more opportune times, such as during periods of low or no production.
The role that employee training plays in reducing unplanned downtime cannot be overstated. Routine training significantly reduces the likelihood of unplanned downtime in several ways. First, employees who are trained on the proper use of machines can correctly operate, maintain, and troubleshoot equipment. They can identify potential issues early on and take preventive measures.
Second, training in maintenance procedures ensures that employees know how to perform routine inspections and maintenance tasks. Third, training fosters a culture of continuous improvement. This encourages employees to actively seek ways to optimise processes and minimise downtime.
Leveraging innovative solutions that enable proactive maintenance strategies and data-driven decision-making can significantly reduce unplanned asset downtime. Here are a few examples of how technology can help reduce asset downtime:
For food and beverage manufacturers, managing unplanned downtime is an ongoing and dynamic undertaking. By understanding the factors that contribute to downtime and acknowledging the negatives associated with it, organisations can chart a course toward proactive solutions. Embracing strategies such as proactive maintenance, predictive analytics, and real-time monitoring not only mitigates the risks of downtime but also fosters a culture of efficiency, reliability, and resilience within the organisation.
Accruent is a leading provider of innovative solutions that help food and beverage manufacturers mitigate unplanned downtime and get the most out of their assets. Maintenance Connection is an industry-leading CMMS solution that makes it easy to implement proactive maintenance strategies, allowing food and beverage organisations to analyse, manage, and track their assets throughout all stages of the lifecycle.
Observe is an IoT remote monitoring software solution that can connect, monitor, predict, and control multiple equipment types to help your organisation improve maintenance processes and even energy efficiency.
Want to discover more about how our solutions can help your organisation to dramatically reduce unplanned downtime? Visit the Maintenance Connection and Observe product pages to learn more. For more information and to request a demo, get in touch via our website.
As manufacturers digitally transform, their maintenance practices also need to evolve. Shifting to proactive forms of maintenance makes sense, but to ...
Explore some proven methods for ensuring that a successful CMMS implementation in the food and beverage manufacturing industry.
IoT will continue to have a massive impact in the maintenance management field - and it's a technology that you shouldn't sleep on.
Subscribe to stay up to date with our latest news, resources and best practices