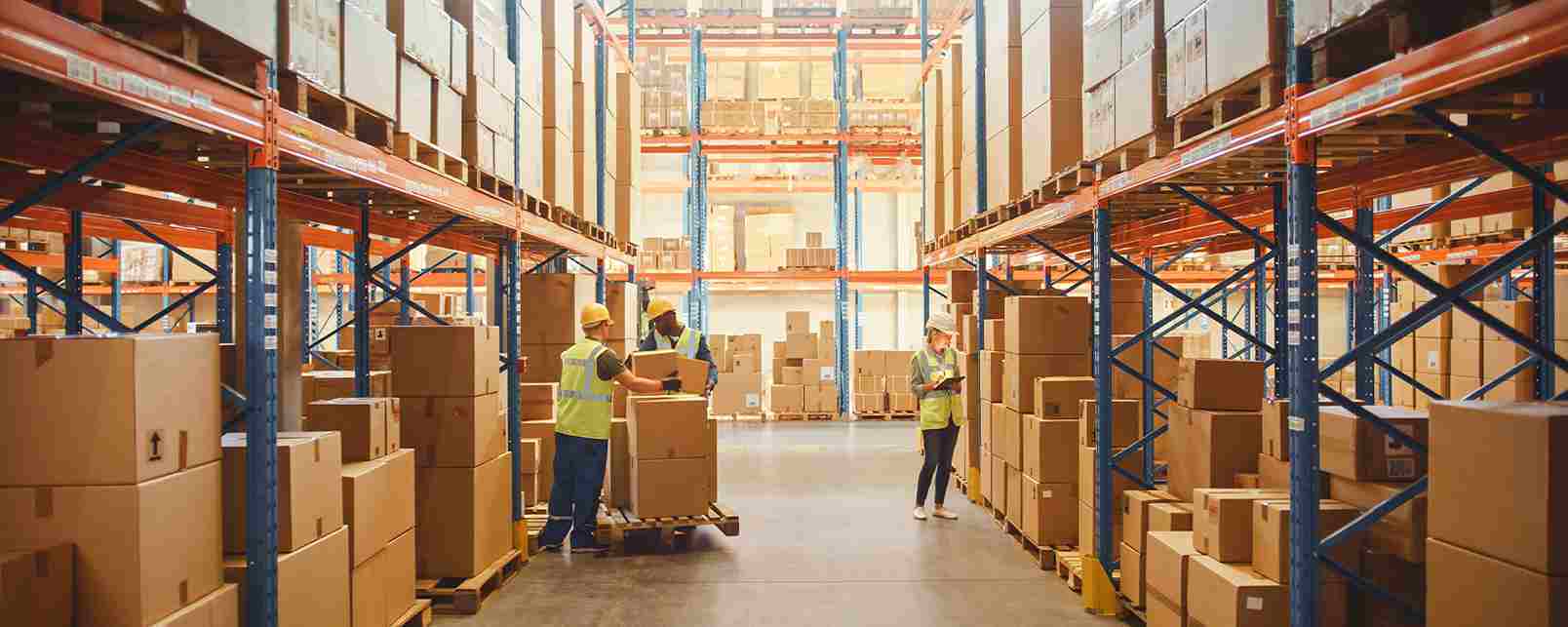
Husky Rack & Wire
Learn how Husky Rack and Wire used Maintenance Connection to automate work order management and implement effective preventive maintenance strategies.
Solutions
Workplace Management Solutions
Real Estate Management Solutions
Maintenance Management Solutions
Energy Management Solutions
Engineering Document Management Solutions
Asset Management Solutions
Automate campus scheduling for classes, meetings, and exams with our EMS software.
Plan and manage conferences effortlessly with EMS software to impress guests and streamline operations.
Boost workplace flexibility and maximize space use with seamless desk and room booking.
Organize workplace or campus events smoothly, creating memorable experiences.
Optimize workspace, manage allocations efficiently, and reduce costs with our space management solutions.
Deliver projects on time and within budget by improving communication, collaboration, and efficiency with our software.
Streamline lease accounting for ASC 842, IFRS, and GASB compliance.
Manage leases efficiently by tracking key dates, analyzing costs, and ensuring compliance.
Centralize data and analytics for better insights, faster negotiations, and revenue growth.
Centralize facility and asset maintenance, automate work orders, and ensure compliance with our CMMS software.
Extend asset life, reduce downtime, and prevent costly repairs with data-driven monitoring.
Prevent equipment failures and extend asset life by detecting and addressing issues early.
Make sustainable, cost-efficient energy decisions by monitoring and optimizing power consumption.
Remotely monitor and control equipment with real-time data to predict issues, boost efficiency, and reduce downtime.
Easily share and collaborate on documents, creating a single source of truth for engineers and contractors.
Manage and analyze assets across their lifecycle to schedule maintenance, reduce downtime, and extend lifespan.
Improve visibility, automate work orders, and ensure compliance for efficient facility and asset management.
Resources
Browse our full library of resources all in one place, including webinars, whitepapers, podcast episodes, and more.
Support
Looking for access to technical support, best practices, helpful videos, or training tools? You’ve come to the right place.
About Accruent
Get the latest information on Accruent, our solutions, events, and the company at large.
Discover how Northern Water improved record-keeping, collaboration, reimbursements, and maintenance for critical infrastructure with Maintenance Connection.
Northern Water was established in 1937 and partners with the U.S. Bureau of Reclamation to manage the Colorado-Big Thompson Project. This project captures water on the West Slope and transports it to the East Slope through a 13-mile tunnel beneath Rocky Mountain National Park, supporting parts of eight counties across 615,000 acres of irrigated land. Today, Northern Water also provides drinking water to more than 1 million people.
To protect and maintain this critical water infrastructure, Northern Water turned to Accruent’s Maintenance Connection (MC) solution. With an extensive network of pipelines, reservoirs, and dams—plus a unique cost-reimbursement model shared among multiple participants—Northern Water needed a single, dependable system for:
Below, Doug Morter, EAM System Administrator at Northern Water, shares how Maintenance Connection helps unify their processes, bolster collaboration, and streamline financial structures to support critical infrastructure and safety for the communities they serve.
Q: Why did you get Maintenance Connection?
A (Doug Morter):
In 2013, there were some big floods in Colorado that damaged a lot of infrastructure, and my company was positioned to assist FEMA with rehabilitation work. At the time, we had organizational issues matching up records. Having siloed information led to challenges with federal reimbursement. Maintenance Connection gave us a clear, organized structure to work effectively with the federal government and better tell the story of what work we performed.
Q: How did you resolve those issues with Maintenance Connection?
A (Doug Morter):
Now we have a single source where our technicians can add assets to the facilities we work on and show precisely what tasks we perform. It really increased our collaboration with the Bureau of Reclamation and made it easier to show FEMA the records needed for reimbursement. Maintenance Connection allowed us to tell a complete story of our work history—something that has continued to help with other collaborative projects.
Q: What do you use Maintenance Connection for today?
A (Doug Morter):
Maintenance Connection drives a large part of our business, covering everything from simple preventive maintenance—like on a lawnmower—to managing the largest dam built in the United States in 30 years. When the new dam goes online, we will need to perform many daily inspections for state reporting, so integrating it with Maintenance Connection was a top priority.
Q: How does Maintenance Connection support your financial structure within asset management?
A (Doug Morter):
We have a complicated financial structure at Northern Water. Maintenance Connection offered solutions that other systems did not. For instance, we treat vehicles almost like labor when they perform work on assets, and multiple participants can reimburse us depending on which portion of a pipeline is being serviced. MC lets us add these “vehicle assets” to work orders and ensures the correct participant is billed. This process is seamless for our technicians—they only focus on the asset and log time, mileage, or even expenses like lunches, while Maintenance Connection handles the coding behind the scenes. It simplifies reimbursements and ensures each participant pays their fair share.
Q: How was Maintenance Connection adoption among technicians?
A (Doug Morter):
We started with a “carrot” approach: using MC to improve time entry. Our HR system for logging hours was cumbersome, so when we showed technicians that MC makes time entry easier, it built trust quickly. Over time, we have implemented more preventive and predictive maintenance features, and now Maintenance Connection is our platform for maintaining our entire infrastructure.
Q: How does Maintenance Connection assist with your Hazardous Energy Control Program?
A (Doug Morter):
We recently integrated a hazardous energy control program into Maintenance Connection, moving from paper documentation to a digital process. Now, our technicians can access up-to-date lockout/tagout procedures from any job site. This shift helps us maintain accurate records in real time, improving both safety and efficiency.
At Accruent, we believe in empowering customers to unlock the full potential of their built environment, from water projects to multi-site facilities. Maintenance Connection is designed to streamline operations, automate critical workflows, and help you make data-driven decisions—so you can focus on delivering vital services to the communities you serve.
Learn how Husky Rack and Wire used Maintenance Connection to automate work order management and implement effective preventive maintenance strategies.
Learn how Maintenance Connection has helped a major broadcast company perform tower maintenance across remote areas in the Artic, delivering ...
Learn how Bay Area Hospital streamlined compliance, simplified maintenance request management and maximized transparency with Maintenance Connection.
Subscribe to stay up to date with our latest news, resources and best practices