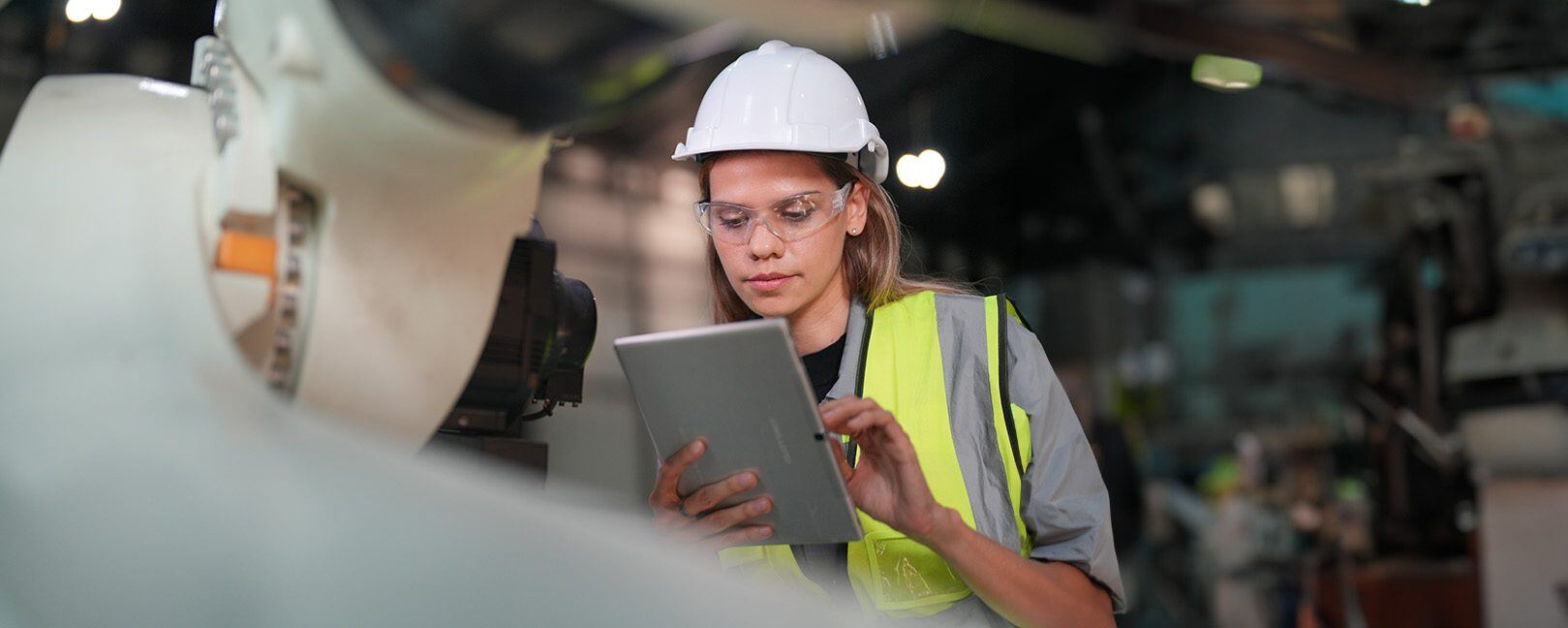
SSAB
Discover how a CMMS helps keep assets fully managed, improve equipment lifespan, increase preventive maintenance, eliminate downtime, and lower costs.
Solutions
Solutions
Workplace Management Solutions
Real Estate Management Solutions
Maintenance Management Solutions
Energy Management Solutions
Engineering Document Management Solutions
Asset Management Solutions
Automate campus scheduling for classes, meetings, and exams with our EMS software.
Plan and manage conferences effortlessly with EMS software to impress guests and streamline operations.
Boost workplace flexibility and maximize space use with seamless desk and room booking.
Organize workplace or campus events smoothly, creating memorable experiences.
Optimize workspace, manage allocations efficiently, and reduce costs with our space management solutions.
Deliver projects on time and within budget by improving communication, collaboration, and efficiency with our software.
Streamline lease accounting for ASC 842, IFRS, and GASB compliance.
Manage leases efficiently by tracking key dates, analyzing costs, and ensuring compliance.
Centralize data and analytics for better insights, faster negotiations, and revenue growth.
Centralize facility and asset maintenance, automate work orders, and ensure compliance with our CMMS software.
Extend asset life, reduce downtime, and prevent costly repairs with data-driven monitoring.
Prevent equipment failures and extend asset life by detecting and addressing issues early.
Make sustainable, cost-efficient energy decisions by monitoring and optimizing power consumption.
Remotely monitor and control equipment with real-time data to predict issues, boost efficiency, and reduce downtime.
Easily share and collaborate on documents, creating a single source of truth for engineers and contractors.
Manage and analyze assets across their lifecycle to schedule maintenance, reduce downtime, and extend lifespan.
Improve visibility, automate work orders, and ensure compliance for efficient facility and asset management.
Resources
Browse our full library of resources all in one place, including webinars, whitepapers, podcast episodes, and more.
Support
Looking for access to technical support, best practices, helpful videos, or training tools? You’ve come to the right place.
About Accruent
Get the latest information on Accruent, our solutions, events, and the company at large.
See how the publishing plant easily organized all assets and implemented a preventive maintenance schedule to service equipment before it breaks.
Table of contents
Since 1835, The New York Times has operated as a global daily news source, producing more than 1 million print newspapers on Sundays alone. The company has 64 newspaper print sites across the world, with its main printing headquarters in College Point, New York. This single printing plant alone is home to approximately 10,000 assets.
Annual Revenue
Weekly Print Readers
Printing Sites Worldwide
Assets in Plant Headquarters
With Maintenance Connection, we can do a lot of automated preventive maintenance based on equipment usage. So if one piece of equipment is running a lot more than another, we’re going off cycle-based counts and those PMs are being scheduled out automatically.”— Greg Zarafa, Maintenance Manager
In delivering a paper of this magnitude, one misstep means a damaged reputation or unreliable service. Prior to implementing Maintenance Connection, The New York Times struggled to find a way to organize its assets and track the health of equipment plant-wide. With thousands of employees spread out across the plant, the facility needed a way to report on equipment downtime, work order status, and schedule updates.
Our previous CMMS software had a lot of gaps. We heard a lot from the workforce about the fact that they didn’t know what was available in the system. With Maintenance Connection, everybody is well aware what’s going on in the plant.”— Greg Zarafa, Maintenance Manager
The New York Times implemented Maintenance Connection at the entire College Point facility for asset monitoring, importing all assets into the system to track historic service information, equipment health, and upcoming work orders. The team also uses the software to automate recurring preventive maintenance, altering cycles and schedules according to equipment usage and industry trends like a reduction in print equipment usage time.
Being able to base preventive maintenance off cycle counts and equipment usage has saved us a lot of man hours and lets us move those man hours to another area that’s needed.”— Greg Zarafa, Maintenance Manager
Almost immediately after implementation, The New York Times saw improved time tracking from all employees and now has accurate records concerning where and how the plant allocates resources and budget. With Maintenance Connection, the plant has organized all its assets and implemented a preventive maintenance schedule to service equipment before it breaks. Now, the team is able to meet the demand of the newspaper’s customers without the fear of equipment breakdown.
Discover how a CMMS helps keep assets fully managed, improve equipment lifespan, increase preventive maintenance, eliminate downtime, and lower costs.
Learn how a leading US blood bank used Maintenance Connection to modernize systems, reduce asset breakdowns, and create a safer environment.
Learn how L'Oreal decreased asset downtime, improved reporting and maximized asset life with Maintenance Connection CMMS.
Subscribe to stay up to date with our latest news, resources and best practices