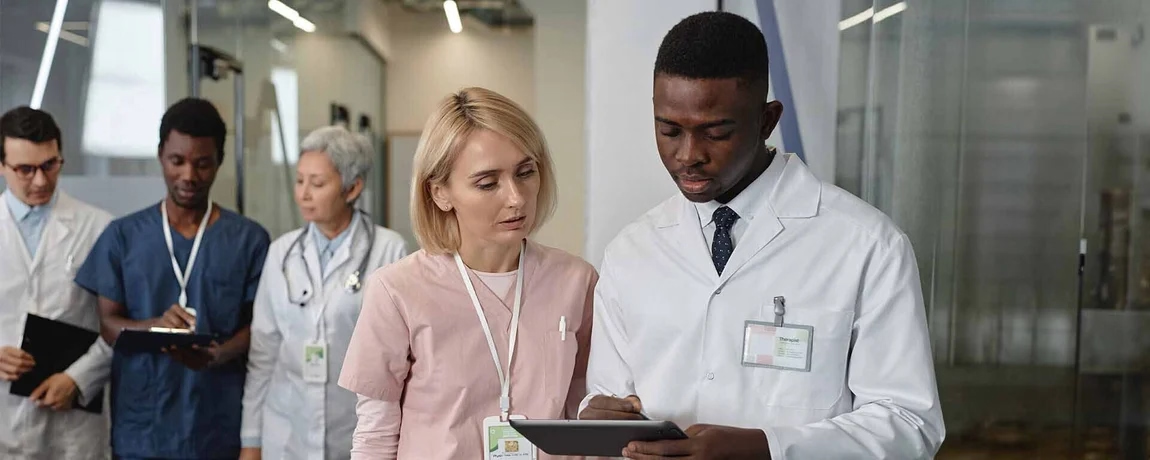
Non-Profit Hospital
Discover how a non-profit hospital maintained corporate compliance by transitioning to TMS OnLine, simplifying upgrades and ensuring easier access to ...
Solutions
Workplace Management Solutions
Real Estate Management Solutions
Maintenance Management Solutions
Energy Management Solutions
Engineering Document Management Solutions
Asset Management Solutions
Automate campus scheduling for classes, meetings, and exams with our EMS software.
Plan and manage conferences effortlessly with EMS software to impress guests and streamline operations.
Boost workplace flexibility and maximize space use with seamless desk and room booking.
Organize workplace or campus events smoothly, creating memorable experiences.
Optimize workspace, manage allocations efficiently, and reduce costs with our space management solutions.
Deliver projects on time and within budget by improving communication, collaboration, and efficiency with our software.
Streamline lease accounting for ASC 842, IFRS, and GASB compliance.
Manage leases efficiently by tracking key dates, analyzing costs, and ensuring compliance.
Centralize data and analytics for better insights, faster negotiations, and revenue growth.
Centralize facility and asset maintenance, automate work orders, and ensure compliance with our CMMS software.
Extend asset life, reduce downtime, and prevent costly repairs with data-driven monitoring.
Prevent equipment failures and extend asset life by detecting and addressing issues early.
Make sustainable, cost-efficient energy decisions by monitoring and optimizing power consumption.
Remotely monitor and control equipment with real-time data to predict issues, boost efficiency, and reduce downtime.
Easily share and collaborate on documents, creating a single source of truth for engineers and contractors.
Manage and analyze assets across their lifecycle to schedule maintenance, reduce downtime, and extend lifespan.
Improve visibility, automate work orders, and ensure compliance for efficient facility and asset management.
Resources
Browse our full library of resources all in one place, including webinars, whitepapers, podcast episodes, and more.
Support
Looking for access to technical support, best practices, helpful videos, or training tools? You’ve come to the right place.
About Accruent
Get the latest information on Accruent, our solutions, events, and the company at large.
Learn how Accruent’s Maintenance Connection helped this leading agricultural cooperative save time and money by utilizing crucial functionalities in the CMMS’ work order management system.
Table of contents
This leading agricultural cooperative specializes in producing high-quality beet sugar. The farmer-owned major beet sugar extraction cooperative has over 500 shareholders who annually plant and harvest sugarbeets on approximately 125,000 acres producing nearly 1 billion pounds (about 453592000 kg) annually in the Midwestern United States.
With an impressive annual revenue of $418M and a remarkable 2844% ROI on annual MC subscriptions, the cooperative has increased its profit by $250K. The company is committed to providing superior products and services and is a testament to excellence and innovation.
The company was losing nearly $250K in productivity due to frequent downtime on their beet washer. The cause of the downtime was unknown since there was no record of work completed and no standardized process for work order requests. Instead, the scheduling relied solely on the "best judgment" of the scheduler. This lack of comprehensive data prevented them from getting to the bottom of the issue and maximizing uptime and operational efficiency.
The cooperative deployed Accruent’s Maintenance Connection, utilizing crucial functionalities in the CMMS’ work order management system, such as:
Work Order Tracking: Easily create, view, update, and execute work orders more effectively. Accessing critical service details (area, duration, order status, task type, parts required) to identify the source of downtime.
Reporting and Analytics: Understand key metrics and share findings to optimize scheduling and purchasing.
Centralized Dashboard: View maintenance requests, manage daily maintenance schedules, update metrics, add notes, and stay on top of the field team’s maintenance activities.
Data revealed the root cause of the beet washer downtime, i.e., bearings were too old and past their useful life of 10 years. To resolve this, the cooperative funded a $500K bearing replacement project, replacing 16 bearings with a 10-year useful life.
The data and work order automation capabilities found in Maintenance Connection ended up saving time and money for the sugar extraction cooperative.
Discover how a non-profit hospital maintained corporate compliance by transitioning to TMS OnLine, simplifying upgrades and ensuring easier access to ...
See how TMS, Accruent’s Healthcare CMMS solution, helped this medical center go from a cost center to a revenue generator.
See how Accruent TMS helped this leading hospital network save time and money with its CMMS solution.
Subscribe to stay up to date with our latest news, resources and best practices