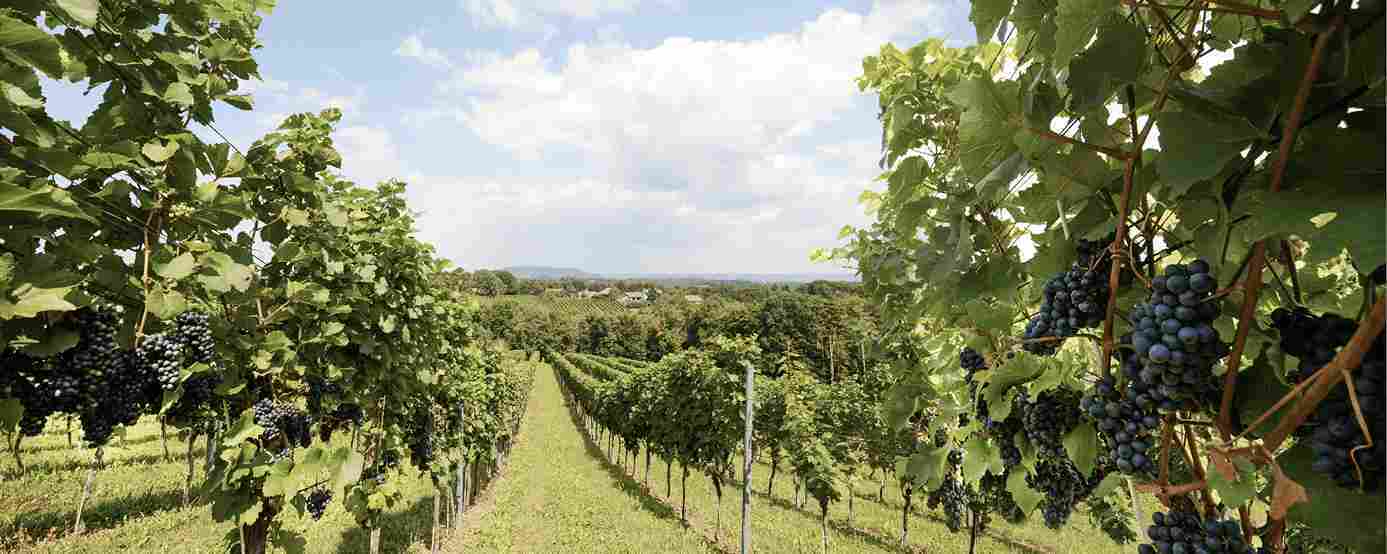
Trinchero Family Estates
Read how the wine industry leader deployed an automated CMMS system for its more than 130 maintenance team members throughout 11 locations.
Solutions
Workplace Management Solutions
Real Estate Management Solutions
Maintenance Management Solutions
Energy Management Solutions
Engineering Document Management Solutions
Asset Management Solutions
Automate campus scheduling for classes, meetings, and exams with our EMS software.
Plan and manage conferences effortlessly with EMS software to impress guests and streamline operations.
Boost workplace flexibility and maximize space use with seamless desk and room booking.
Organize workplace or campus events smoothly, creating memorable experiences.
Optimize workspace, manage allocations efficiently, and reduce costs with our space management solutions.
Deliver projects on time and within budget by improving communication, collaboration, and efficiency with our software.
Streamline lease accounting for ASC 842, IFRS, and GASB compliance.
Manage leases efficiently by tracking key dates, analyzing costs, and ensuring compliance.
Centralize data and analytics for better insights, faster negotiations, and revenue growth.
Centralize facility and asset maintenance, automate work orders, and ensure compliance with our CMMS software.
Extend asset life, reduce downtime, and prevent costly repairs with data-driven monitoring.
Prevent equipment failures and extend asset life by detecting and addressing issues early.
Make sustainable, cost-efficient energy decisions by monitoring and optimizing power consumption.
Remotely monitor and control equipment with real-time data to predict issues, boost efficiency, and reduce downtime.
Easily share and collaborate on documents, creating a single source of truth for engineers and contractors.
Manage and analyze assets across their lifecycle to schedule maintenance, reduce downtime, and extend lifespan.
Improve visibility, automate work orders, and ensure compliance for efficient facility and asset management.
Resources
Browse our full library of resources all in one place, including webinars, whitepapers, podcast episodes, and more.
Support
Looking for access to technical support, best practices, helpful videos, or training tools? You’ve come to the right place.
About Accruent
Get the latest information on Accruent, our solutions, events, and the company at large.
Learn how Husky Rack and Wire used Maintenance Connection to automate work order management and implement effective preventive maintenance strategies.
Table of contents
Husky Rack and Wire is one of the largest manufacturers of material handling products in the US. They have been in business over 50 years. Since 1964, the company has grown and prospered due to a strong commitment to product development, quality control and, most importantly, the ability to meet the needs of customers. Husky Rack & Wire services the material handling industry nationwide through an extensive network of distributors. They have manufacturing facilities in Denver, NC and Sterling, MA.
Employees
Years in Business
In Revenue
We generally ship out product within 48 hours, so we have to keep our machines running at all times. Downtime is a big thing for us. We need to make sure that the machines are up and running, ready to go. We need to keep high standards, and that’s what we’re doing at Husky Rack and Wire, keeping high standards with our product."
—Eric Stegall, Husky Rack and Wire
Before selecting and implementing Maintenance Connection as their CMMS platform, Husky Rack and Wire used a very manual, email-based process. As a result, there were many areas of improvement in the organization. Specifically, they wanted to address:
Husky Rack and Wire utilized many Maintenance Connection solutions initially, including:
They were so impressed with the results they received from their implementation, that they subsequently decided to implement Maintenance Connection’s robust inventory module, which includes barcoding of parts and inventory management. The goal: to have cross-departmental visibility into their parts and inventory warehouse to help them save money, stock correct parts, and better understand their inventory needs.
One of the great capabilities Husky has gained from using the Maintenance Connection CMMS is the ability to automate work orders. Now with electronic work orders, technicians can conduct work immediately and supervisors are notified of any updates or changes to equipment status in real time. As a result of this automation, performance has increased. Equipment downtime has been reduced and product output has increased.
Husky Rack and Wire has also benefited from the robust PM’s module, the excellent reporting capabilities and the real-time functionality gained for their maintenance department.
“We needed somebody that could come in and implement something very well for us. The MC implementation consultant came in and did that. Everything was scattered all over the place. Everything went great, we never had any problem,” said Stegall.
Husky Rack and Wire streamlined their operations, increased productivity and created visibility into their daily operations. Now, they have become one of the largest manufacturers of material handling products in the US.
Read how the wine industry leader deployed an automated CMMS system for its more than 130 maintenance team members throughout 11 locations.
Read how Townson University used Maintenance Connection to improve the work order process for its students and maintenance team, creating a healthy ...
Discover how Northern Water improved record-keeping, maintenance, reimbursements, and safety for critical infrastructure with Maintenance Connection.
Subscribe to stay up to date with our latest news, resources and best practices