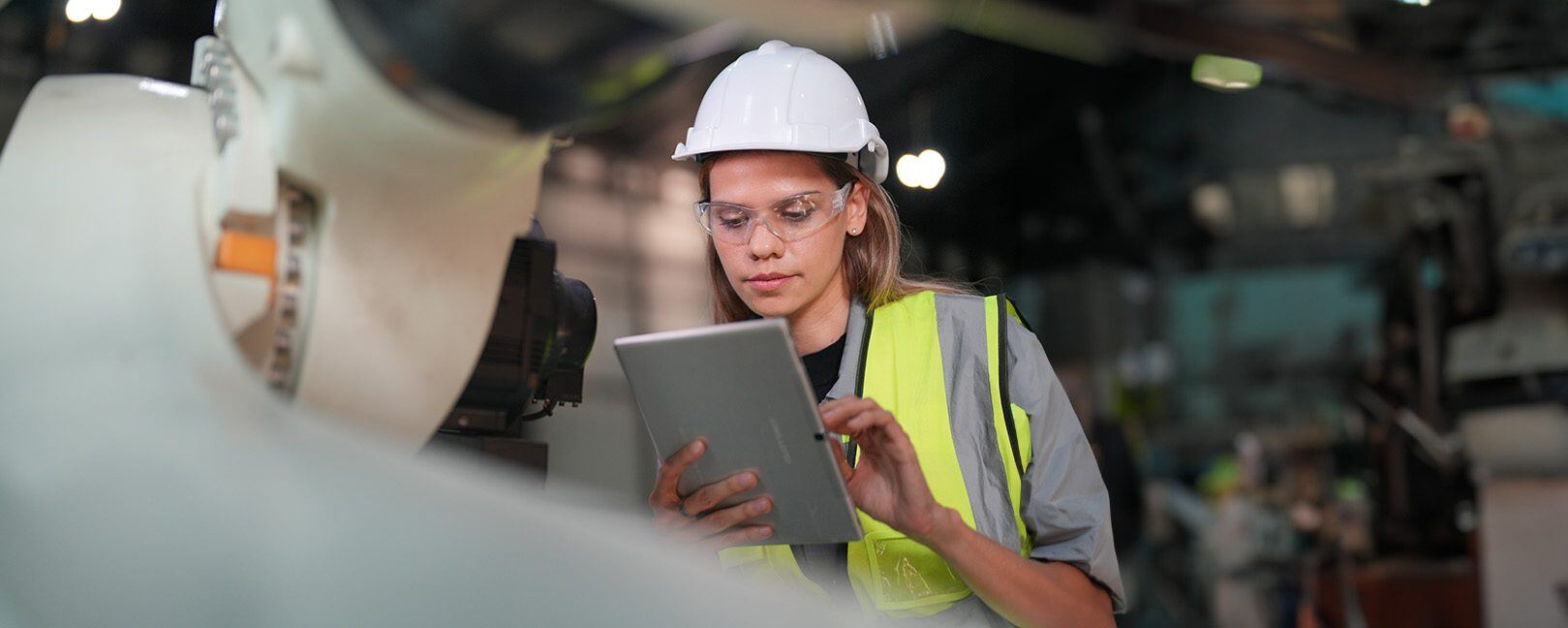
SSAB
Discover how a CMMS helps keep assets fully managed, improve equipment lifespan, increase preventive maintenance, eliminate downtime, and lower costs.
Solutions
Workplace Management Solutions
Real Estate Management Solutions
Maintenance Management Solutions
Energy Management Solutions
Engineering Document Management Solutions
Asset Management Solutions
Automate campus scheduling for classes, meetings, and exams with our EMS software.
Plan and manage conferences effortlessly with EMS software to impress guests and streamline operations.
Boost workplace flexibility and maximize space use with seamless desk and room booking.
Organize workplace or campus events smoothly, creating memorable experiences.
Optimize workspace, manage allocations efficiently, and reduce costs with our space management solutions.
Deliver projects on time and within budget by improving communication, collaboration, and efficiency with our software.
Streamline lease accounting for ASC 842, IFRS, and GASB compliance.
Manage leases efficiently by tracking key dates, analyzing costs, and ensuring compliance.
Centralize data and analytics for better insights, faster negotiations, and revenue growth.
Centralize facility and asset maintenance, automate work orders, and ensure compliance with our CMMS software.
Extend asset life, reduce downtime, and prevent costly repairs with data-driven monitoring.
Prevent equipment failures and extend asset life by detecting and addressing issues early.
Make sustainable, cost-efficient energy decisions by monitoring and optimizing power consumption.
Remotely monitor and control equipment with real-time data to predict issues, boost efficiency, and reduce downtime.
Easily share and collaborate on documents, creating a single source of truth for engineers and contractors.
Manage and analyze assets across their lifecycle to schedule maintenance, reduce downtime, and extend lifespan.
Improve visibility, automate work orders, and ensure compliance for efficient facility and asset management.
Resources
Browse our full library of resources all in one place, including webinars, whitepapers, podcast episodes, and more.
Support
Looking for access to technical support, best practices, helpful videos, or training tools? You’ve come to the right place.
About Accruent
Get the latest information on Accruent, our solutions, events, and the company at large.
Learn how Cook Medical created an organized database of all assets, past equipment failures, and service history to improve processes.
Table of contents
Cook Medical is a medical device manufacturing company headquartered in Bloomington, Indiana. Founded in 1963, Cook Medical produces more than 16,000 products for a variety of specialties, ranging from anesthesiology to plastic surgery to transplant surgery.
Products Manufactured
Medical Specialties
Countries Served
Employees
It used to take us three to four hours to go search for paper records. With Maintenance Connection, it’s almost immediate. As soon as you run the report, [the information] is there. Now we’re able to sit in a conference room and pull it up on the screen for the auditor to view in real time."
— Mike McCormick, Maintenance Manager
With thousands of products produced daily and assets spread across the manufacturing plant, Cook Medical needed a way to track work order status and requests from the floor. A paper-based system caused headaches for everyone from the compliance operator to the manufacturing technicians.
The users really like the work order tracking system. They’re able to track what work orders they have, and then we can schedule a lot easier."— Mike McCormick, Maintenance Manager
After implementing Maintenance Connection, Cook Medical was able to create an organized database of all assets, past equipment failures, and service history. The company was also able to create a preventive maintenance (PM) schedule, including automated work orders based on historic asset data.
For the FDA, the software has to be validated, and Maintenance Connection helped in that validation process. The other thing [the FDA] wants to know is the history of every piece of equipment that touches a medical device. And with Maintenance Connection, it’s at your fingertips."— Mike McCormick, Maintenance Manager
As a result of using Maintenance Connection, Cook Medical has improved work order tracking, automated maintenance procedures, and ensured compliance with FDA requirements. The company has also streamlined reporting processes, significantly reducing the time spent searching and processing reports. Additionally, the new PM schedule has reduced downtime by alerting technicians that service is needed before equipment failure.
Discover how a CMMS helps keep assets fully managed, improve equipment lifespan, increase preventive maintenance, eliminate downtime, and lower costs.
Learn how L'Oreal decreased asset downtime, improved reporting and maximized asset life with Maintenance Connection CMMS.
See how the publishing plant easily organized all assets and implemented a preventive maintenance schedule to service equipment before it breaks.
Subscribe to stay up to date with our latest news, resources and best practices