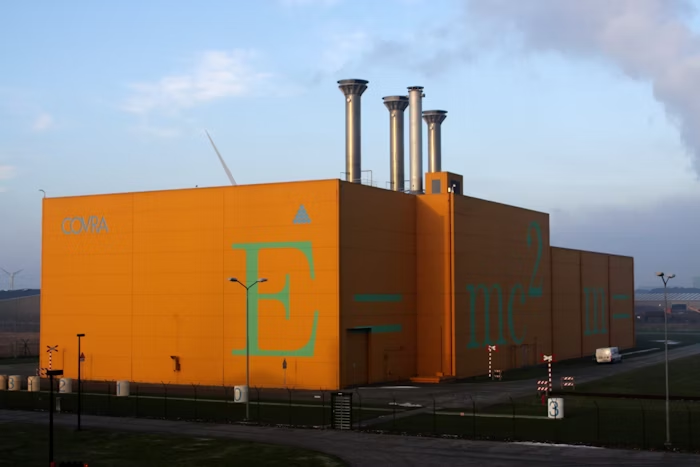
COVRA
Learn how COVRA uses Meridian to safely and efficiently manage operational assets and related engineering data to comply with the Dutch Nuclear ...
Solutions
Workplace Management Solutions
Real Estate Management Solutions
Maintenance Management Solutions
Energy Management Solutions
Engineering Document Management Solutions
Asset Management Solutions
Automate campus scheduling for classes, meetings, and exams with our EMS software.
Plan and manage conferences effortlessly with EMS software to impress guests and streamline operations.
Boost workplace flexibility and maximize space use with seamless desk and room booking.
Organize workplace or campus events smoothly, creating memorable experiences.
Optimize workspace, manage allocations efficiently, and reduce costs with our space management solutions.
Deliver projects on time and within budget by improving communication, collaboration, and efficiency with our software.
Streamline lease accounting for ASC 842, IFRS, and GASB compliance.
Manage leases efficiently by tracking key dates, analyzing costs, and ensuring compliance.
Centralize data and analytics for better insights, faster negotiations, and revenue growth.
Centralize facility and asset maintenance, automate work orders, and ensure compliance with our CMMS software.
Extend asset life, reduce downtime, and prevent costly repairs with data-driven monitoring.
Prevent equipment failures and extend asset life by detecting and addressing issues early.
Make sustainable, cost-efficient energy decisions by monitoring and optimizing power consumption.
Remotely monitor and control equipment with real-time data to predict issues, boost efficiency, and reduce downtime.
Easily share and collaborate on documents, creating a single source of truth for engineers and contractors.
Manage and analyze assets across their lifecycle to schedule maintenance, reduce downtime, and extend lifespan.
Improve visibility, automate work orders, and ensure compliance for efficient facility and asset management.
Resources
Browse our full library of resources all in one place, including webinars, whitepapers, podcast episodes, and more.
Support
Looking for access to technical support, best practices, helpful videos, or training tools? You’ve come to the right place.
About Accruent
Get the latest information on Accruent, our solutions, events, and the company at large.
See how BASF initiated an integration to streamline the data handover between engineering and maintenance, leading to direct access to updated assets.
Table of contents
Improving efficiency through integrated maintenance and engineering.
BASF is the world’s leading chemical company with more than 250 production sites worldwide and over 115,000 employees. Headquartered in Germany, where the company operates the world’s largest integrated chemical complex, the BASF Group comprises subsidiaries and affiliates in more than 80 countries. To take advantage of the opportunities for profitable growth throughout the world, BASF is represented through production and sales facilities in all economic regions.
CHEMICAL PRODUCER IN THE WORLD
DOCUMENTS
INSTRUMENTS
PROCESS FUNCTIONS
The integration has improved the quality, availability and accessibility of asset information. Contractors now have easy access to all relevant engineering information."— René Baron, Maintenance and Engineering Manager
BASF Nijehaske in the Netherlands is part of the Chemicals division of BASF. At this location, 158 employees work with 800 process functions and more than 6,000 instruments. The Technical Services Department manages inspections and corrective actions. Strict environmental regulations such as NEN 3140, Seveso I+II, Atex 95+137 and ISO 14001 must be applied and verified by authorized bodies.
The data handover challenge is keeping process functions and instruments up-to-date in the as-built environment, while changing the engineering data in the project environment. BASF started an integration project to streamline the data handover between Engineering and Maintenance.
During the zero-tolerance test, an inconsistency of five to ten percent between the operations and Engineering databases was measured. Therefore, BASF decided to streamline the handover procedures and create a direct link between Ultimo and Meridian, creating a single source of information.”— René Baron, Maintenance and Engineering Manager
The assets and documents in both applications are one hundred percent identical and provide us with the necessary regulatory compliance. As a result, our people have a better view of the as-built environment and, therefore, work more efficiently. Consequently, management costs have been reduced.”— René Baron, Maintenance and Engineering Manager
The integration between Ultimo and Meridian was chosen by BASF because of the low cost of ownership for future upgrades and releases of both Ultimo and Meridian.
“We have been able to realize an intelligent connection between Ultimo and Meridian. The efficiency of both the Maintenance and Engineering processes has been improved. All our assets are maintained and the documents are directly available from Meridian to keep a real-time relationship with more than twenty thousand technical documents.”
Learn how COVRA uses Meridian to safely and efficiently manage operational assets and related engineering data to comply with the Dutch Nuclear ...
Discover how Dunea uses Meridian to manage all engineering information and other technical documentation, providing a reliable and stable system.
Learn how Seattle City Light has used Meridian for more than 20 years to implement controls and workflow processes to find up-to-date asset ...
Subscribe to stay up to date with our latest news, resources and best practices