System Validation: The Basics
What’s Validation and Why Do You Need to Do It?
If you work in an industry like Life Sciences, your industry – and your software and hardware – will be regulated by the Food and Drug Administration (FDA), which means that your software will need to be regularly validated. This applies to all software that could impact product quality or the safety of the end users. In Life Sciences, then, this includes all software related to:
- Pharmaceuticals
- Food and beverages
- Botanicals
- Medical devices
- Surgical instruments
- Dental equipment
- Ophthalmic supplies
- Diagnostic substances
To get this right, according to the FDA, you need to provide documented evidence that confirms, beyond a shadow of a doubt, that your facility, product, processes and software meet quality standards, that everything has been installed correctly, that everything will meet end users’ needs and that it will all function properly over time. This will not only prove your systems and GxP but also help your organization identify and address any concerns before they actually become production problems.
In theory, this makes sense. To make safe medical devices, your software and equipment needs to be working as well as possible, right? And there’s no room for error when people’s lives are on the line. What’s more, strict regulations require that organizations establish good practices (GxP) to minimize risk and ensure that products are being produced according to high quality standards. And establishing good practice is always the best way to go.
In practice, system validation is very complex, costly and time-consuming. Why? To start, it touches all business processes, and it takes immense time for people to create, maintain and follow strict procedures.
Where Validation Can Get Complicated
Validation gets even more complex because there is no set way to validate your systems. The only rules that the FDA set are that:
The products you make and the processes you follow must meet the FDA’s Code for Federal Regulations (CFR).
To maintain records or submit information to FDA, electronic records and electronic signatures need to adhere to 21 CFR Part 11.
The rest largely depends on your particular use case -- even though the FDA does have comprehensive compliance guidance – as the definition of success or the risk factors associated with your product will vary based on your particular offering or sub-industry.
The IQ, OQ, PQ Process
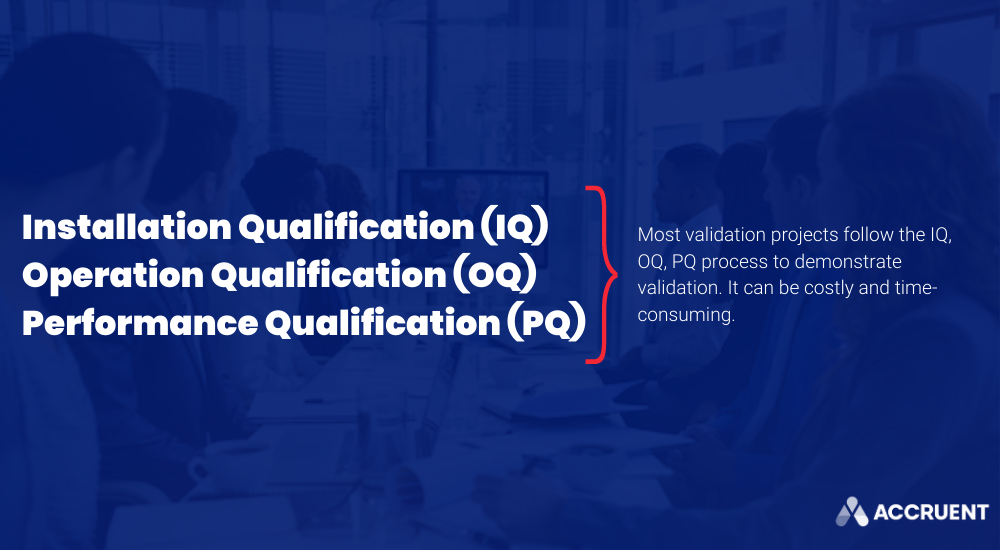
That said, most validation projects follow the IQ, OQ, PQ process to demonstrate that:
- The installation of the facility, product line, equipment, and systems are installed with a high degree of quality assurance and in accordance with all FDA quality requirements
- The quality of the production process meets FDA standards
- The quality of the documentation about the process and equipment meets FDA standards
Installation Qualification (IQ)
This step applies to newly installed or modified equipment to ensure that the, “system has the necessary prerequisite conditions to function as expected.” In other words, IQ ensures that the instrument or unit (as well as any associated systems) is installed and configured according to the manufacturer’s specifications/installation checklist. For an asset, these specifications could include details about electrical voltage or about the required amount of floor space. For software like an electronic document management system (EDMS), the IQ process includes verifying folder structures and ensuring that minimum system requirements are met. Throughout this process, all relevant cGMP requirements and methodologies used must be thoroughly documented. There’s a lot that goes into proper IQ execution, including:
- Documentation of all computer-controlled instrumentation
- Gathering all relevant certifications or manuals
- Identifying any damage to the equipment
- Cross-checking that all components are there and working
- Installing any ancillary components
- Documenting firmware serial numbers and versions
- Recording the calibration and validates of the tools you use for the IQ process
- Verifying connection with all integrated units
- Checking the environmental conditions
In short, it’s a lot.
Operation Qualification (OQ)
Once IQ is complete, organizations then move on to OQ. This step is all about functionality and inspecting equipment to make sure that it is running within specified limits and that nothing will negatively impact the final product quality. In other words, it’s about making sure that you did everything correctly during IQ and that the system is running correctly. OQ action items typically include checking things like:
- Temperature controls and variations
- Humidity
- Fans
- Card readers
- Display units
- Temperature protection systems
During operation qualification, users must document everything – including buildings, processes, equipment and systems – to prove that everything is operating properly.
Performance Qualification (PQ)
During PQ, the qualification and validation team must test the software to show that it will perform reliably and repeatably when used as intended. In the pharmaceutical industry, for example, the electronically reviewed and approved cGMP documents need an electronic signature with watermarks, print stamps and audit log.
Getting PQ right requires that teams develop a detailed test plan to ensure thoroughness and accuracy. There are also specific FDA criteria for PQ and for Process Performance Qualification (PPQ), which documents performance over time to ensure ongoing product quality. The FDA also specifically separates PQ into two phases:
- Design of the facility and qualification of the equipment and utilities
- Process Performance Qualification (PPQ)
During the second stage, the FDA states that, “CGMP-compliant procedures must be followed,” and that, “successful completion of Stage 2 is necessary before commercial distribution.”
To this end, the FDA has specific recommendations as part of PQ and PPQ protocols. Ultimately, they require that organization produce a written protocol including:
- The manufacturing conditions, including operating parameters, processing limits and component (raw material) inputs
- The data to be collected and when and how it will be evaluated
- Tests to be performed and the acceptance criteria for each significant processing step
- The sampling plan, including sampling points, number of samples and the frequency of sampling for each unit operation and attribute
- Criteria and process performance indicators that allow for a science- and risk-based decision about the ability of the process to consistently produce quality products
- Design of facilities and the qualification of utilities and equipment, personnel training and qualification, and verification of material sources (components and containers/closures)
- Status of the validation of analytical methods used in measuring the process, in-process materials, and the product
- Review and approval of the protocol b appropriate departments and the product unit
Needless to say, these validation steps are complex, time-consuming and costly. Plus, since most organizations don’t need to constantly validate, their IT team takes on this task when necessary. This is an incredible lift that can cause plant shutdown and cost millions of dollars.
A pre-validated system can help.
A Pre-Validated System Can Help
A cloud-based EDMS system that offers validation-as-a-service can take the majority of this process – and broader compliance concerns – off your team’s plate. This can save time, money and efficiency in the long run.
General Benefits of a Validated System
A huge part of ongoing compliance and validation is document management. Any Life Sciences organization will have to create, collaborate on, and distribute hundreds – if not thousands – of documents to effectively track their business processes and standard operating procedures (SOPs) and remain compliant with regulatory bodies.
It can be difficult to manage – and getting it wrong can not only negatively impact compliance but also disrupt plant safety, economic efficiency and operational excellence.
The right document management system, on the other hand, can help organizations overcome key document management challenges, including issues with safety and quality, time to market, compliance, workflow automation and digital transformation. It can also:
- Improve quality by enabling compliance with regulations
- Lower the cost of data collection
- Increase data accuracy
- Reduce regulatory errors (by eliminating mistakes like misfiling)
- Improve control over production, quality and other processes
- Allow for more rapid search of electronics records
- Improve information transfer between departments and between companies
- Lower the total cost of ownership
- Put the appropriate risk management and government procedures in place for installation, operational and performance qualification
- Help organizations integrate both business processes and audit functions into their systems without compromising the quality of regulatory compliance
Meridian Cloud for Life Sciences: How It Simplifies Validation
Meridian Cloud for Life Sciences, in particular, is designed to take the majority of IQ, OQ and PQ tasks off your plate, dramatically simplifying your day-to-day validation efforts and reducing your validation costs.
As a cloud-based, pre-validated electronic document management system (EDMS), Meridian Cloud for Life Sciences enables organizations to easily maintain electronic records and electronic signatures while deploying procedures and controls designed to simplify validation processes.
What’s more, Meridian Cloud for Life Sciences is not just a software-as-a-service (SaaS) solution. Accruent also provides implementation services, user training and certification, and application managed services. This combination of services helps support digital transformation initiatives and facilitate ongoing IQ, OQ and PQ system validation.
IQ: We Take Care of It
Installation qualification, as we mentioned, is the testing of the software itself. Accruent is responsible for installing, qualifying and maintaining the Meridian Cloud for Life Sciences software, and we do so through ongoing:
- Defect tracking
- Disaster recovery
- Performance monitoring
- Code review
- Design review, and
- System maintenance
We also immediately provide users with key documents, including a validation plan, user requirement specifications, configuration verification and more. In short, we take the installation qualification completely off your plate.
OQ: We Mostly Take Care of It
Accruent will also own operational qualification, helping ensure that your system and processes are running as they should. This is accomplished through things like:
- Setting data migration protocols
- Assisting with change management
- Ongoing issue management
- Performance monitoring
- Continuous validation and quality assurance
Accruent will also provide crucial risk assessments every time something changes in your systems. This mitigates risks and helps ensure ongoing compliance.
That said, Accruent does not own your SOPs or your training, though we do provide ongoing training resources.
PQ: You Mostly Take Care of It
The PQ process helps guarantee that your processes are repeatable, and the customer will be in charge of key PQ activities like:
- Record retention
- Audit trail reviews
- User management
- Application use
That said, the AMS team will always be available to provide guidance and support.
And that’s just the tip of the iceberg. Learn more about key features of Meridian Cloud for Life Sciences here.