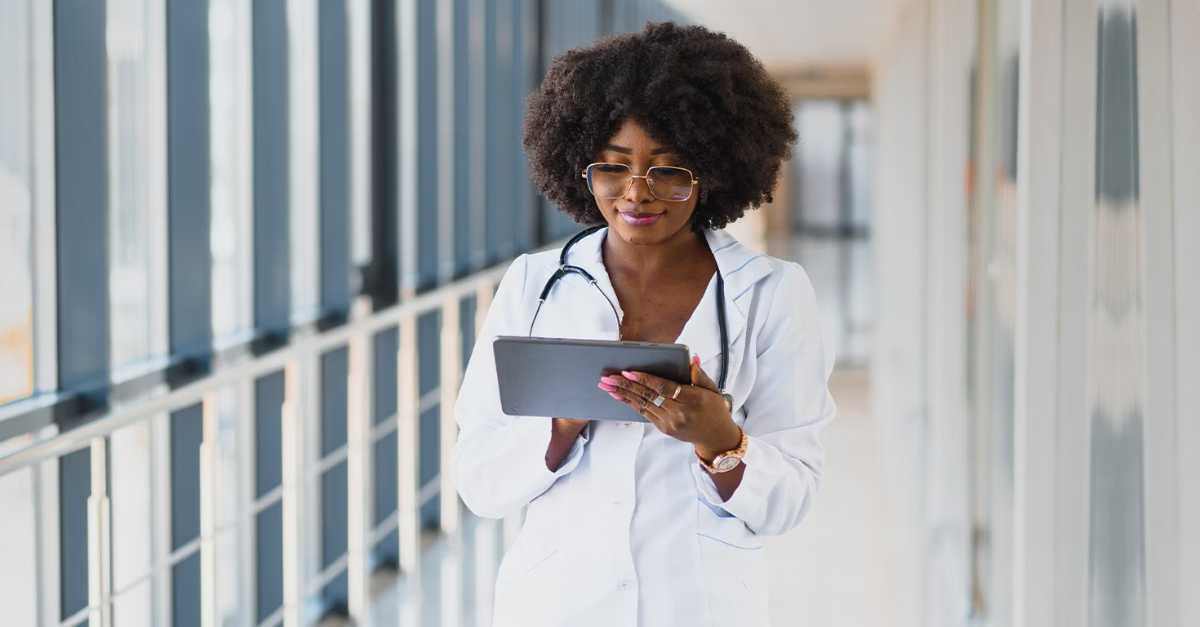
A Multi-Part Overview of Quality Management Systems in Healthcare - Part 2
Explore part 2 of our overview of Quality Management Systems in Healthcare. Learn about leadership's role and the importance of continuous learning ...
Solutions
Workplace Management Solutions
Real Estate Management Solutions
Maintenance Management Solutions
Energy Management Solutions
Engineering Document Management Solutions
Asset Management Solutions
Automate campus scheduling for classes, meetings, and exams with our EMS software.
Plan and manage conferences effortlessly with EMS software to impress guests and streamline operations.
Boost workplace flexibility and maximize space use with seamless desk and room booking.
Organize workplace or campus events smoothly, creating memorable experiences.
Optimize workspace, manage allocations efficiently, and reduce costs with our space management solutions.
Deliver projects on time and within budget by improving communication, collaboration, and efficiency with our software.
Streamline lease accounting for ASC 842, IFRS, and GASB compliance.
Manage leases efficiently by tracking key dates, analyzing costs, and ensuring compliance.
Centralize data and analytics for better insights, faster negotiations, and revenue growth.
Centralize facility and asset maintenance, automate work orders, and ensure compliance with our CMMS software.
Extend asset life, reduce downtime, and prevent costly repairs with data-driven monitoring.
Prevent equipment failures and extend asset life by detecting and addressing issues early.
Make sustainable, cost-efficient energy decisions by monitoring and optimizing power consumption.
Remotely monitor and control equipment with real-time data to predict issues, boost efficiency, and reduce downtime.
Easily share and collaborate on documents, creating a single source of truth for engineers and contractors.
Manage and analyze assets across their lifecycle to schedule maintenance, reduce downtime, and extend lifespan.
Improve visibility, automate work orders, and ensure compliance for efficient facility and asset management.
Resources
Browse our full library of resources all in one place, including webinars, whitepapers, podcast episodes, and more.
Support
Looking for access to technical support, best practices, helpful videos, or training tools? You’ve come to the right place.
About Accruent
Get the latest information on Accruent, our solutions, events, and the company at large.
In Part 1 of this overview series, we cover the ISO 9001:2015 holistic approach recognizes service departments as crucial to quality efforts, not just patient-focused areas.
By: Rick Joslin, Senior Advisor, Healthcare Strategy
“Quality”, as an objective, has been a force within healthcare for over 100 years, dating back to the 1850’s when handwashing was identified as effective way to reduce infection and poor living conditions were found to lead to higher death rates.
Since then, there have been numerous attempts at regulating quality in healthcare. So far, though, these efforts have focused on medical equipment and care of the patient. Although CMS created and adopted Conditions of Participation (CoPs) surrounding quality, not much has changed the focus of quality in healthcare from “patient-focused” to “system-focused”. Numerous committees have been formed to influence quality, such as:
You get the point. That’s a lot of effort on a major and important aspect of healthcare as organizations routinely strive to achieve some form of quality in the products and services they deliver to their customers. Yet these efforts often fail to improve processes that are not directly focused on patient care.
At the same time as these patient-focused efforts in healthcare, other industries were pursuing methods to improve quality at all levels of operation (think Total Quality Management or TQM and Six Sigma) to reduce costs and improve revenue. Their focus was on defect management and process improvements. Starting in the 1970’s, there were various versions of quality standards, but it was in 1987 with the first publication of the ISO 9001 by International Organization for Standardization (ISO) when quality became a measurable international standard.
The 9000-series by ISO have helped organizations meet contractual requirements, improve products, and gain efficiencies in processes which increased their revenue and activity in the global market. We can summarize the intent of ISO 9001 into this: it’s a set of internal rules that are defined by a collection of people, policies, processes, documented procedures, and records that define how an organization will achieve the creation, delivery, and measurement of the products and services they provide to their customers.
Healthcare in the United States, as a whole, has been slow to adopt and apply ISO 9001:2015, often citing the difficulty and/or cost as a determining factor. But why should a healthcare organization adopt ISO 9001, regardless of the challenges that may come from doing so? To start off, we need to understand that ISO 9001 is about processes, not assets. ISO 13485 specifically focuses on the product produced (medical equipment, for example) where ISO 9001 is about the process of ensuring that everything involved with making that product is high-quality. A QMS ensures the supporting objectives, policies, data, etc. increase the quality of the delivered product.
Within healthcare, most regulatory agencies reference some form of quality requirements. The Centers for Medicare & Medicaid Services (CMS) refers to “quality measures” in various regulations, such as their MDS 3.0 QM User’s Manual V14.0. But these references are limited to patient-related outcomes like medication mishaps and falls. You get more specific within the Food & Drug Administration (FDA) and §21 CFR 820, but this is referring to manufacturing processes and Current good manufacturing practice (CGMP) and is directed at entities producing medical equipment. Neither, usually, apply to the service departments within a healthcare organization.
Often, quality requirements come from Accrediting Organizations. Since these organizations must ensure CMS CoP requirements are met, their related requirements are also limited in scope. For example, The Joint Commission (TJC) refers to “quality activities” in their Patient Safety, Quality Report, Medication Management, and Leadership chapters, providing a general overview of their notion of a quality management program. This is singularly focused on quality within patient care and misses the broader, wholistic approach to a QMS found in ISO 9001:2015. DNV, on the other hand, has fully integrated ISO 9001 into their accreditation process with at least 18 specific requirements to meet, and all their accredited organizations must be ISO 9001:2015 certified within three years of their first survey.
Beyond regulatory requirements, the benefits to the organization are immense; deciding to develop and implement a QMS commits the entire organization to quality in all they do (not just patient-related). All departments and staff within an organization that are implicated within the scope of interested parties (as defined in ISO 9001:2015 4.2) must become active participants of the QMS process to ensure the processes, procedures, and results meet or exceed the determined objectives. This leads healthcare organizations to recognize service departments (Healthcare Facilities Management (HFM), Healthcare Technology Management (HTM), Environmental Services (EVS), etc.) as equals in quality efforts as they do nursing, administration, pharmacy, and other patient-focused departments.
Now that we have a basic understanding of what quality is in healthcare, what it is in other industries, and that (like other standards) international standards are where we are going, in follow-up blogs we’ll dig into more specifics on how a QMS can elevate service departments from a necessary evil to an organizational crown.
To learn more about leadership’s role in establishing a QMS – and how to effectively plan and execute a QMS program – check out part 2 of this series, Leadership and Planning: Setting the Bar.
About The Author
For more than 23 years, Rick Joslin IRCC, Senior Advisor, Healthcare Strategy at Accruent, has helped hundreds of healthcare systems navigate the ins and outs of managing service missions within their organizations. He has 35+ years in the maintenance management industry, including roles such as technician, inspector/compliance surveyor, and director. He is known for promoting continuous improvement, driving operational efficiency, increasing resource utilization, and ensuring regulatory success by identifying gaps and inefficiencies in business processes. Rick leverages LEAN thinking and Six Sigma processes to guide customers in the development of short and long-term goals. His broad knowledge of healthcare operations and regulatory requirements, coupled with an intimate knowledge of CMMS systems, allow him to assist customers in developing easily implemented solutions to unique, and changing, business needs.
Updated on September 24, 2024
Explore part 2 of our overview of Quality Management Systems in Healthcare. Learn about leadership's role and the importance of continuous learning ...
Part 4 of our overview of Quality Management Systems in Healthcare shows how to measure QMS success and identify ways to improve the quality of your ...
Explore part 3 of our overview of Quality Management Systems in Healthcare. Learn how to execute your QMS plan and create a conducive workplace for ...
Subscribe to stay up to date with our latest news, resources and best practices