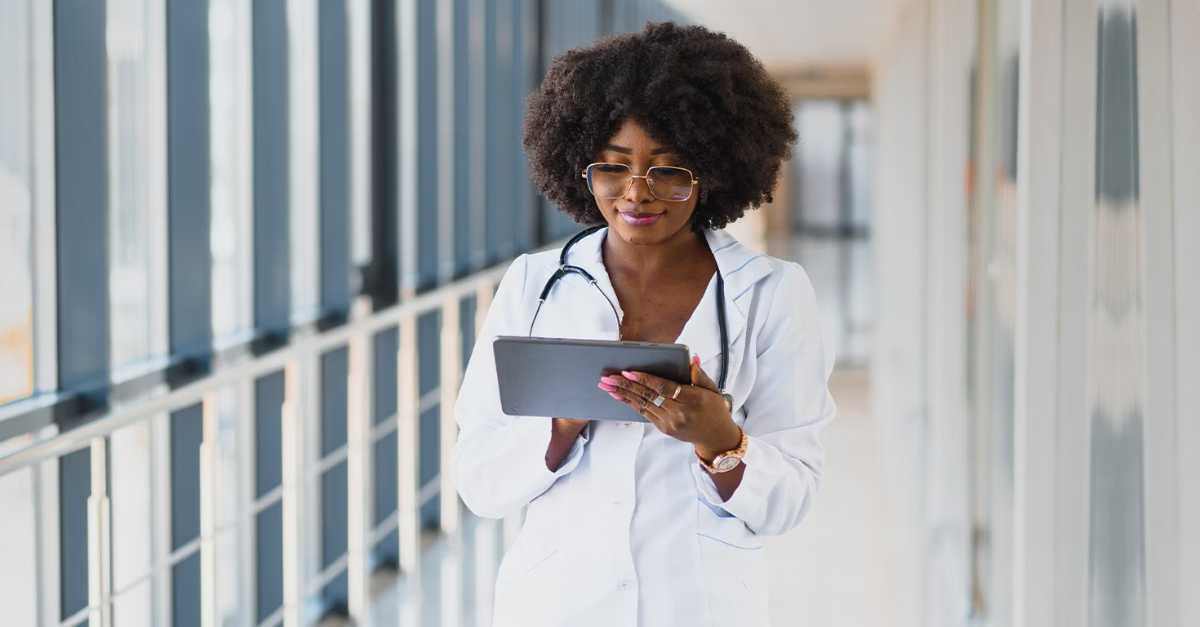
A Multi-Part Overview of Quality Management Systems in Healthcare - Part 2
Explore part 2 of our overview of Quality Management Systems in Healthcare. Learn about leadership's role and the importance of continuous learning ...
Solutions
Workplace Management Solutions
Real Estate Management Solutions
Maintenance Management Solutions
Energy Management Solutions
Engineering Document Management Solutions
Asset Management Solutions
Automate campus scheduling for classes, meetings, and exams with our EMS software.
Plan and manage conferences effortlessly with EMS software to impress guests and streamline operations.
Boost workplace flexibility and maximize space use with seamless desk and room booking.
Organize workplace or campus events smoothly, creating memorable experiences.
Optimize workspace, manage allocations efficiently, and reduce costs with our space management solutions.
Deliver projects on time and within budget by improving communication, collaboration, and efficiency with our software.
Streamline lease accounting for ASC 842, IFRS, and GASB compliance.
Manage leases efficiently by tracking key dates, analyzing costs, and ensuring compliance.
Centralize data and analytics for better insights, faster negotiations, and revenue growth.
Centralize facility and asset maintenance, automate work orders, and ensure compliance with our CMMS software.
Extend asset life, reduce downtime, and prevent costly repairs with data-driven monitoring.
Prevent equipment failures and extend asset life by detecting and addressing issues early.
Make sustainable, cost-efficient energy decisions by monitoring and optimizing power consumption.
Remotely monitor and control equipment with real-time data to predict issues, boost efficiency, and reduce downtime.
Easily share and collaborate on documents, creating a single source of truth for engineers and contractors.
Manage and analyze assets across their lifecycle to schedule maintenance, reduce downtime, and extend lifespan.
Improve visibility, automate work orders, and ensure compliance for efficient facility and asset management.
Resources
Browse our full library of resources all in one place, including webinars, whitepapers, podcast episodes, and more.
Support
Looking for access to technical support, best practices, helpful videos, or training tools? You’ve come to the right place.
About Accruent
Get the latest information on Accruent, our solutions, events, and the company at large.
Auditing the entire QMS program is essential, focusing on compliance with internal documents and standards, establishing an auditing program, and conducting management reviews, measure and constant improvement.
Table of contents
By: Rick Joslin, Senior Advisor, Healthcare Strategy
In this final installment on implementing a compliant ISO 9001:2015 Quality Management Systems (QMS) in a healthcare environment, we tackle how an organization will measure the success of the QMS and identify ways to improve the quality of the product\service they provide. These topics are found within Clause 9 and Clause 10, and it is crucial that an organization take the time to define how, when, and where specific processes are to be monitored, measured, analyzed, and evaluated. This is crucial if organizations hope to determine if the QMS is effective and if the goals are being met. Generally, these steps fall under the “Check” (Clause 9) and “Act” (Clause 10) portions of the Plan\Do\Check\Act cycle.
A QMS has many components where the organization must determine its own destiny, and Clause 9 is no different. The organization must set the standards, then define how they will know the program is working. There are four key areas for consideration in the initial Clause 9 Section 9.1.1:
Inherent in these requirements are supporting needs, such as ensuring you have adequate and correct resources to execute these requirements. Also included is the need to gather and present evidence that the activities were completed, as well as evidence of any considered and executed changes to the QMS process.
ISO 9001:2015 then gives you specific examples of what to do. Since a primary purpose of a QMS is to meet or exceed customer’s expectations (customer satisfaction), having a means to identify if you’ve met those expectations is almost as important as the process itself. Clause 9 is all about making sure you’re getting it done by evaluating those activities and identifying areas for continual improvement. Here are some general activities to accomplish contained within Section 9.1:
Once the data has been collected, reviewed, and processed, it must be audited. But you should not simply audit your outputs, but instead the whole QMS program, since the goal of these audits are to ensure the QMS program is compliant with both ISO 9001:2015 and the organizations QMS program as written. The audit process is about identifying what’s going well and what could use some improvement; it’s not about finding fault with individuals or teams. The expectations found within Clause 9.2 are:
Once the audits are completed and sent to the appropriate management team(s) for action, they take over and complete the auditing process. Section 9.3 covers the Management Review requirements of a compliant QMS program. There are specific activities required by “top management” geared toward supporting the QMS program and ensuring the results and recommendations of the audits are reviewed and implemented. Key activities of Section 9.3 Management Review are:
Once you’ve completed all these steps, you must execute on identified areas for improvement. Remember, a core component of a QMS is constant improvement, and it should be a rare occurrence when a review does not uncover something that can be improved. Clause 10 gives you guidance on how to identify and implement improvements.
Understanding that a compliant ISO 9001:205 QMS program’s primary goal is to achieve (or improve) customer satisfaction, the efforts expended in developing and executing a QMS program will result in an institutional drive toward self-reflection and continual improvement. The resulting certification can increase increased revenue, higher employee satisfaction, and increased reputation within your industry. As stated in earlier posts, the cumulative QMS process continues to manifest itself as higher patient satisfaction, lower cost, and improved outlook for the healthcare organization.
To see how Accruent’s purpose-built healthcare CMMS can help you support and document your QMS program, reach out to the Accruent Healthcare team today.
About The Author
For more than 23 years, Rick Joslin IRCC, Senior Advisor, Healthcare Strategy at Accruent, has helped hundreds of healthcare systems navigate the ins and outs of managing service missions within their organizations. He has 35+ years in the maintenance management industry, including roles such as technician, inspector/compliance surveyor, and director. He is known for promoting continuous improvement, driving operational efficiency, increasing resource utilization, and ensuring regulatory success by identifying gaps and inefficiencies in business processes. Rick leverages LEAN thinking and Six Sigma processes to guide customers in the development of short and long-term goals. His broad knowledge of healthcare operations and regulatory requirements, coupled with an intimate knowledge of CMMS systems, allow him to assist customers in developing easily implemented solutions to unique, and changing, business needs.
Updated on September 24, 2024
Explore part 2 of our overview of Quality Management Systems in Healthcare. Learn about leadership's role and the importance of continuous learning ...
Explore an overview of Quality Management Systems in Healthcare. Learn about ISO 9000-Series Standards, quality requirements in healthcare, and their ...
Explore part 3 of our overview of Quality Management Systems in Healthcare. Learn how to execute your QMS plan and create a conducive workplace for ...
Subscribe to stay up to date with our latest news, resources and best practices