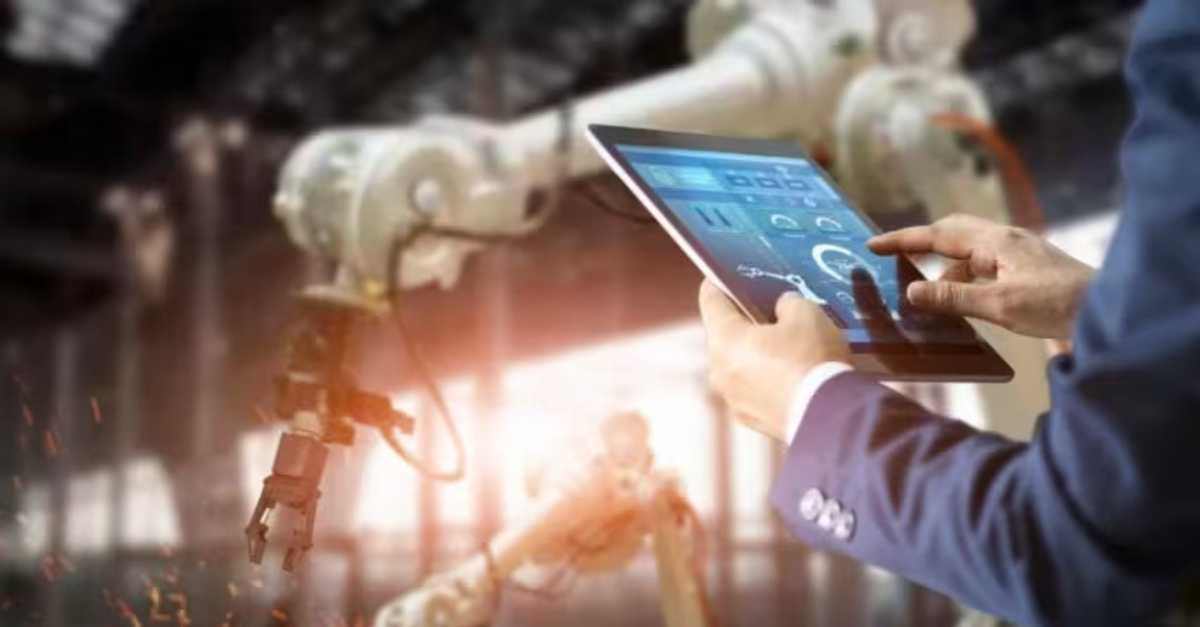
What is an EIM System? Everything You Need to Know in 2025
Read our 2024 EIM software guide to learn how an engineering information management (EIM) system can improve operations at your organization.
Solutions
Workplace Management Solutions
Real Estate Management Solutions
Maintenance Management Solutions
Energy Management Solutions
Engineering Document Management Solutions
Asset Management Solutions
Automate campus scheduling for classes, meetings, and exams with our EMS software.
Plan and manage conferences effortlessly with EMS software to impress guests and streamline operations.
Boost workplace flexibility and maximize space use with seamless desk and room booking.
Organize workplace or campus events smoothly, creating memorable experiences.
Optimize workspace, manage allocations efficiently, and reduce costs with our space management solutions.
Deliver projects on time and within budget by improving communication, collaboration, and efficiency with our software.
Streamline lease accounting for ASC 842, IFRS, and GASB compliance.
Manage leases efficiently by tracking key dates, analyzing costs, and ensuring compliance.
Centralize data and analytics for better insights, faster negotiations, and revenue growth.
Centralize facility and asset maintenance, automate work orders, and ensure compliance with our CMMS software.
Extend asset life, reduce downtime, and prevent costly repairs with data-driven monitoring.
Prevent equipment failures and extend asset life by detecting and addressing issues early.
Make sustainable, cost-efficient energy decisions by monitoring and optimizing power consumption.
Remotely monitor and control equipment with real-time data to predict issues, boost efficiency, and reduce downtime.
Easily share and collaborate on documents, creating a single source of truth for engineers and contractors.
Manage and analyze assets across their lifecycle to schedule maintenance, reduce downtime, and extend lifespan.
Improve visibility, automate work orders, and ensure compliance for efficient facility and asset management.
Resources
Browse our full library of resources all in one place, including webinars, whitepapers, podcast episodes, and more.
Support
Looking for access to technical support, best practices, helpful videos, or training tools? You’ve come to the right place.
About Accruent
Get the latest information on Accruent, our solutions, events, and the company at large.
With the right EIM software, organizations can save time and gain efficiencies resulting in significant value for both the engineering organization and business.
By Arnoud Kool
Process-driven manufacturing industries such as Oil & Gas and Pharma strive to increase their operational efficiency. Most companies in these industries have teams and departments dedicated to enhancing operational efficiency and becoming leaner in their operational excellence centers. With the right Engineering Information Management (EIM) software, companies can save a significant amount of time, potentially resulting in substantial value created for the engineering organization and the company itself.
This value can be viewed as reducing the time and effort needed to get the same job done. Alternatively, the hours spent on doing a task or project can be considered cost savings. Any way you look at it, the bottom line remains dedicated to improving operational excellence by improving process performance.
Managing engineering information can be a painful, inefficient process, but it does not have to be. The following five considerations for choosing an EIM solution are intended for engineering teams who see inefficiencies in the way they work on-site, how they communicate with other colleagues at other office or site locations, or even how they work with contractors and subcontracts.
When talking about increasing or improving operational efficiency, it is essential to measure the right things. Often, companies have elaborate plans to assess different kinds of processes with less focus on what matters.
Improving key business processes can deliver the highest value to any organization. Therefore, knowing what those ‘key processes’ are and how to measure them is a critical first step.
In the diagram below, the key business processes within Asset Lifecycle Information Management (ALIM) are identified. This is a good starting point in determining the critical engineering processes within an engineering company.
AILM – Key Business Processes
Once a team has agreed where to focus, the next step is identifying and mapping out what the process currently is. Process maps are required to start measuring processes, as they are the foundation to establish a baseline or zero measurements. Once the baseline is identified, the process optimization can be conducted by zeroing on efficiency gains.
Most companies do not have process flows readily available. Consider an engineering team that is looking to expand plant capacity to meet future demand. In this example, we are looking at capital planning as a fundamental business process. Although the engineering team may have a good idea of what the process looks like, they may not be fully aware of the end-to-end process flow that needs to be mapped. This involves cross-functional stakeholder involvement to outline who is included throughout the entire process and at what points.
This is more of a customer centric approach — as opposed to software-centric — to establishing and mapping processes and enables customers to achieve more immediate time to value.
Once a process is defined and thoroughly mapped, companies should create or adopt a model for collecting data points so they can benchmark performance. Over time, this measurement will enable the company to facilitate informed decision making. It is important to note that as compelling learnings surface, it is crucial to establish structural interventions to modify the process. This is also in line with a lean approach.
To understand the full value gained from implementing an EIM solution, it is essential to measure the steps within the key processes on how they are executed today. Benchmarking can be another way to accomplish this. At Accruent, our consultants have in-depth expertise and developed a proven model on which steps in the engineering processes should be measured and how they are to be measured. Having done this for many years, we have built up benchmark data relevant to different industries in process execution time.
With this information, the first areas for process improvements can be identified, laying the foundation of the future for improved processes with the support of an EIM solution.
Let us take a look at how managing engineering information with an EIM solution such as Accruent's Meridian can further help engineering teams contribute to their organization's goal of increasing operational efficiency.
Engineering teams typically manage engineering information such as technical documents, which can require frequent updates. For engineers, these technical documents are critical to performing their jobs safely and effectively.
When dealing with contractors and subcontractors involved in a project, ensuring the right level of access to the latest version is a necessity. The sharing of engineering information internally and externally can be a severe burden for engineering teams since many teams today still use email and excel sheets to share critical engineering information. This approach can expose the company to security issues.
Considerable cost savings can be made on work orders — e.g., plant turnaround, facility inspection — when they are prepared effectively by ensuring all the right information is at hand when those projects are executed. For example, not having the correct information available during a plant turnaround can result in significant delays and budget overruns of the turnaround project. Having the right information available for all internal and external experts involved in such a project is essential.
When we talk about increasing operational efficiency within a larger organization, with multiples sites across the country or even the world, we are also discussing the standardization of how processes are performed. Standardization is by no means a new concept, but one that many sites, teams and engineers are not eager to adopt.
Many companies find themselves plagued with a fixed mindset. In contrast, a growth mindset can lead to the adoption of new ideas and behaviors, simply because they can see significant benefits. This, however, is easier said than done.
Now imagine if every site, team and person within an organization worked differently, and with different processes. Inefficiencies that inevitably surface would be nearly impossible to benchmark.
For example, an Oil & Gas company may have multiple refinery sites. Each refinery more than likely deal with similar challenges when it comes to running their business and executing their processes. Does each site require a completely different solution? Or would employees at a specific location, who are used to a particular way of working, be willing to adopt a standardized footprint with small modifications? As long as the refineries continue to execute similar processes in disparate ways, it is difficult to talk about increased operational efficiency within a broader organizational scope.
This is where the capability of process flows can elevate an organization. Process flows allow engineers to see and understand the facts that lead to argumentations that initiate change and challenge the status quo. Broad organizational objectives should derive from fact-based and grounded argumentation directly related to how the entire engineering community at the company will benefit.
It is only with standardization that single-site data can then be converted to an opportunity to benchmark across multiple sites.
With the right engineering information management software, companies can save time and gain efficiencies, resulting in a significant amount of value created for the engineering organization and the company. The right engineering information at hand while executing work orders, from small maintenance work orders to large plant turnaround projects, is imperative to the effective execution of such a work order. An engineer should have access to that information and not be worried about having the right or latest version of information at hand.
Learn how Meridian can help you and your team increase operational efficiencies. Request a demo for your team today.
Read our 2024 EIM software guide to learn how an engineering information management (EIM) system can improve operations at your organization.
Optimize your organization’s processes with purpose-built integrations including CMMS, EDMS, and IoT software solutions.
Explore how an enterprise management solution can benefit your organization and learn how to optimize it for your organization’s needs.
Subscribe to stay up to date with our latest news, resources and best practices