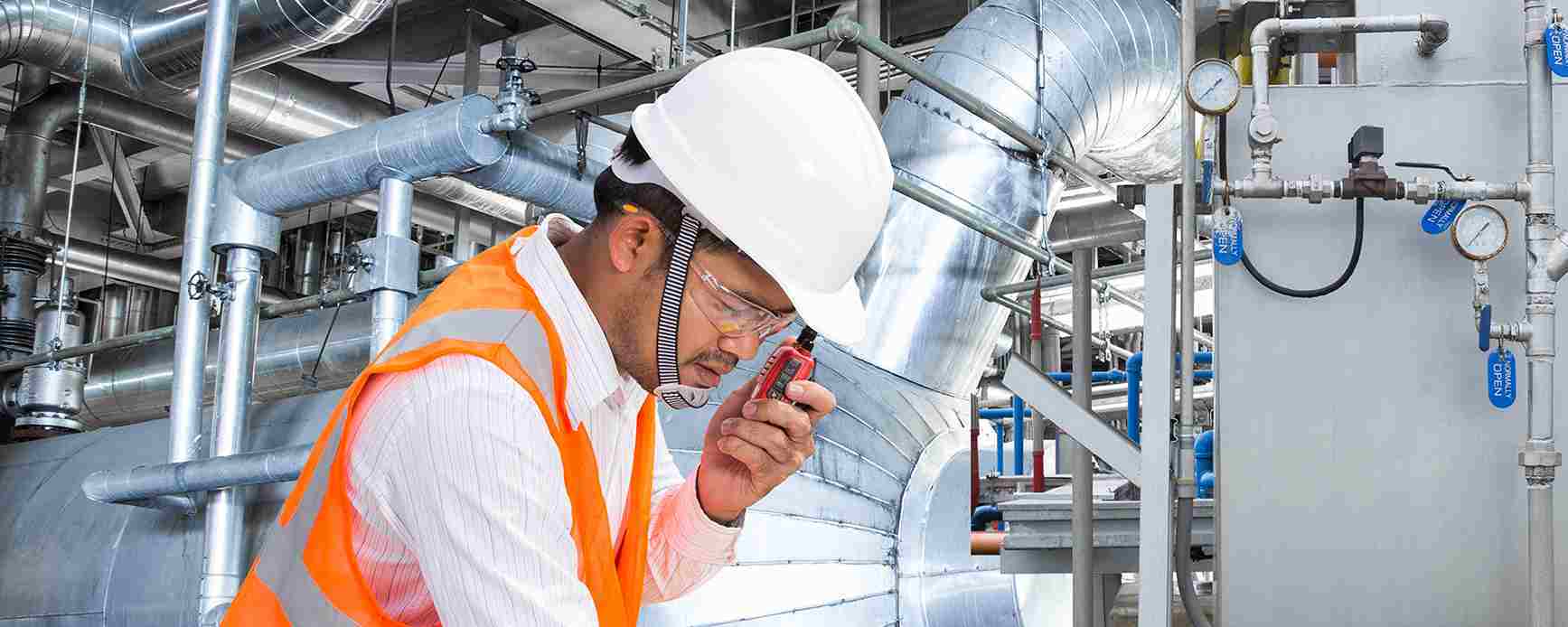
How to Create an Equipment Downtime Report in a CMMS
Use real-time data in Maintenance Connection's downtime reports to better understand your downtime causes and reduce it altogether.
Solutions
Workplace Management Solutions
Real Estate Management Solutions
Maintenance Management Solutions
Energy Management Solutions
Engineering Document Management Solutions
Asset Management Solutions
Automate campus scheduling for classes, meetings, and exams with our EMS software.
Plan and manage conferences effortlessly with EMS software to impress guests and streamline operations.
Boost workplace flexibility and maximize space use with seamless desk and room booking.
Organize workplace or campus events smoothly, creating memorable experiences.
Optimize workspace, manage allocations efficiently, and reduce costs with our space management solutions.
Deliver projects on time and within budget by improving communication, collaboration, and efficiency with our software.
Streamline lease accounting for ASC 842, IFRS, and GASB compliance.
Manage leases efficiently by tracking key dates, analyzing costs, and ensuring compliance.
Centralize data and analytics for better insights, faster negotiations, and revenue growth.
Centralize facility and asset maintenance, automate work orders, and ensure compliance with our CMMS software.
Extend asset life, reduce downtime, and prevent costly repairs with data-driven monitoring.
Prevent equipment failures and extend asset life by detecting and addressing issues early.
Make sustainable, cost-efficient energy decisions by monitoring and optimizing power consumption.
Remotely monitor and control equipment with real-time data to predict issues, boost efficiency, and reduce downtime.
Easily share and collaborate on documents, creating a single source of truth for engineers and contractors.
Manage and analyze assets across their lifecycle to schedule maintenance, reduce downtime, and extend lifespan.
Improve visibility, automate work orders, and ensure compliance for efficient facility and asset management.
Resources
Browse our full library of resources all in one place, including webinars, whitepapers, podcast episodes, and more.
Support
Looking for access to technical support, best practices, helpful videos, or training tools? You’ve come to the right place.
About Accruent
Get the latest information on Accruent, our solutions, events, and the company at large.
If your crucial retail equipment breaks down unexpectedly, you face waste, downtime, and skyrocketing costs. IoT remote monitoring can help.
When a machine stops working, downtime can negatively impact your business.
Equipment such as coolers, freezers, fryers and cash registers break. It happens. You can lose efficiency, pay more in operating costs and miss key customer service interactions.
Equipment downtime can have a big impact on your day-to-day business practices. When a heavily used asset breaks down it affects everything else in the store. Your employees now need to create processes to work around the faulty equipment, you must wait for the contractor to fix the problem, and you still need to continue to serve food in the best way possible.
Let’s take the example of a cooler breaking down. Your employees must spend time moving the food from the cooler to another location. That is, if the food is still safe to use and it does not need to be thrown away. Then, a manager has to delegate someone to clean the cooler before it starts to defrost, causing mold and mildew. This process alone can take hours to accomplish. Not to mention, you have a manager overseeing the broken cooler instead of overseeing day-to-day store operations, including serving customers. Of course, that is if you still have food to serve (depending on what food was thrown out from the faulty cooler).
With a remote monitoring solution and a work order management solution, these kind of days can be avoided!
By using remote monitoring on your equipment, you can identify a breakdown before it happens. That cooler was probably being overworked for weeks from food blocking fans, or a motor slowly giving out. Remote monitoring can detect the temperature difference or the excessive energy usage days before the cooler would actually break down. This monitoring gives you time to call a repair person, and fix the issue before equipment downtime affects you.
Through an integrated work order management solution, the flagged temperature or the excessive energy usage can automatically create a work order or highlight problems that can be handled remotely. This process saves the time of evaluating the problem and tracking down a contractor in the area to fix the issue. The site operator saves money off the emergency repair, saves inventory and saves the hours spent working around a compromised asset.
See how our Computer Managed Maintenance Software solutions can help your organization or contact us to schedule a demo today!
Use real-time data in Maintenance Connection's downtime reports to better understand your downtime causes and reduce it altogether.
Learn how to create automated equipment downtime reports in your CMMS -- and how to use these reports to optimize repairs and minimize downtime ...
In the chemical industry, billions of dollars can be lost annually due to unplanned downtime. Here's how to utilize a CMMS to decrease downtime for ...
Subscribe to stay up to date with our latest news, resources and best practices