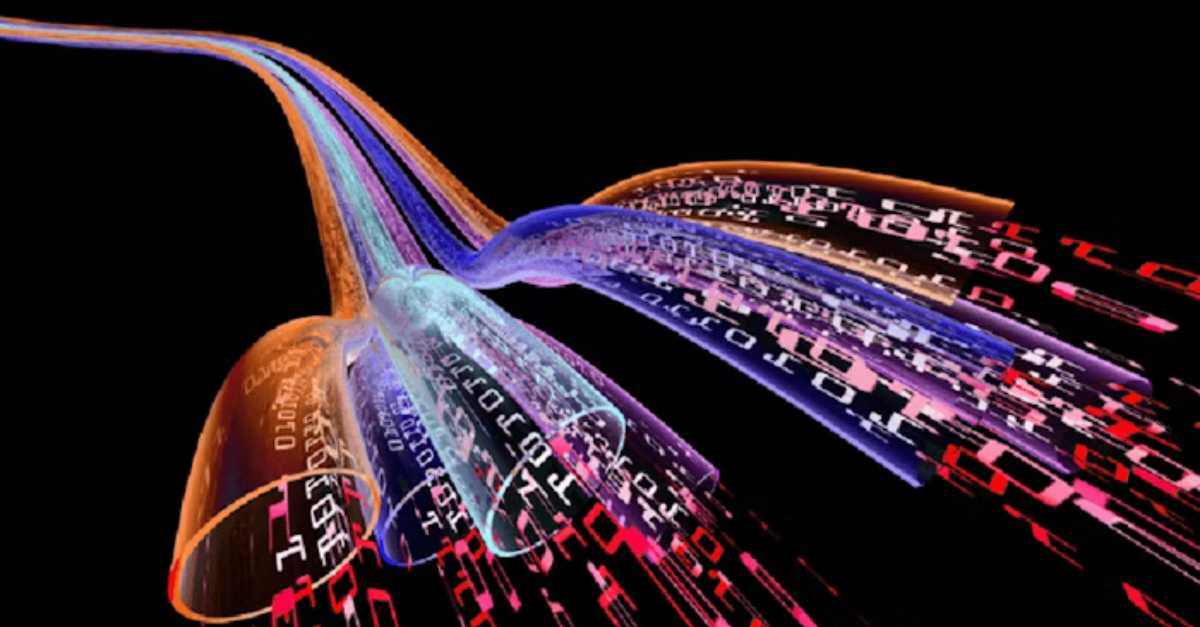
Big Data, Mobile & IoT Remote Monitoring
Learn how to harness the power of Big Data, IoT remote monitoring, and mobile tools to transform your retail operations.
Solutions
Workplace Management Solutions
Real Estate Management Solutions
Maintenance Management Solutions
Energy Management Solutions
Engineering Document Management Solutions
Asset Management Solutions
Automate campus scheduling for classes, meetings, and exams with our EMS software.
Plan and manage conferences effortlessly with EMS software to impress guests and streamline operations.
Boost workplace flexibility and maximize space use with seamless desk and room booking.
Organize workplace or campus events smoothly, creating memorable experiences.
Optimize workspace, manage allocations efficiently, and reduce costs with our space management solutions.
Deliver projects on time and within budget by improving communication, collaboration, and efficiency with our software.
Streamline lease accounting for ASC 842, IFRS, and GASB compliance.
Manage leases efficiently by tracking key dates, analyzing costs, and ensuring compliance.
Centralize data and analytics for better insights, faster negotiations, and revenue growth.
Centralize facility and asset maintenance, automate work orders, and ensure compliance with our CMMS software.
Extend asset life, reduce downtime, and prevent costly repairs with data-driven monitoring.
Prevent equipment failures and extend asset life by detecting and addressing issues early.
Make sustainable, cost-efficient energy decisions by monitoring and optimizing power consumption.
Remotely monitor and control equipment with real-time data to predict issues, boost efficiency, and reduce downtime.
Easily share and collaborate on documents, creating a single source of truth for engineers and contractors.
Manage and analyze assets across their lifecycle to schedule maintenance, reduce downtime, and extend lifespan.
Improve visibility, automate work orders, and ensure compliance for efficient facility and asset management.
Resources
Browse our full library of resources all in one place, including webinars, whitepapers, podcast episodes, and more.
Support
Looking for access to technical support, best practices, helpful videos, or training tools? You’ve come to the right place.
About Accruent
Get the latest information on Accruent, our solutions, events, and the company at large.
Strategically implemented IoT opens the door to more first-time fixes, better communication, and optimized equipment maintenance.
Table of contents
From how much can be communicated in a conversation to how much can be communicated by automatically gathering information from assets to avoiding a conversation altogether. Conversations cannot always happen and are not always accurate. Often, if can you avoid the conversation, everyone‑including the customer, will be much happier.
For example, a broken asset sending alarm calls and communicating directly with the technician is typically much more accurate than an individual trying to describe what is wrong over the phone. Many times, these product users may not be “technical,” so the level of information that can be gathered is limited.
One of the keys to understanding what is happening with assets occurs after you decide to send a technician. The technician may need spare parts and a more accurate understanding of the symptoms to increase the likelihood of arriving on-site with the right parts. If the problem is not described accurately, the technician may have to make two visits. First to diagnose the problem, then to show up with the right parts. If you can avoid return visits, that is another big change in the service industry.
Another aspect of avoiding return visits is receiving “feedback” from the assets that the work has been completed successfully. For example, if an asset is fixed at the edge of a utility network with a branch of 10 houses, the work completed on one house might have disconnected another house. With connected assets, you could get information that all 10 houses are operating which indicates to the technician that the work has been finished and no other problems have been created. This feedback from the connected asset lets the technician know it’s OK to leave the site.
While communicating directly with assets is important, most assets are still unconnected. For example, connected assets are an opportunity for medical device manufacturers. Imaging machines are sophisticated equipment connected to the internet. Typically, if something is wrong with the imaging machine, there is not much information that people on-site can tell you. What if, instead, those imaging machines could send a lot information about their own health back to the manufacturer?
Part of the service process is about how work is initiated. If assets are not connected, work is initiated by a plan in place, such as a preventive maintenance plan, or by a service request. If assets are connected, work is initiated in a different way. For example, our solution can interface with a system that is already collecting and analyzing information about the assets or can conduct the analysis and make smart decisions based on that data.
With the potential to improve a lot of the things that are hard to fix with disconnected assets, connected assets will change the service industry.
If the asset is disconnected, you can put a preventive maintenance plan in place that is based on average use or meantime between failures. Then, you would analyze this information. It is like taking your car to a mechanic every 6 months. It is much more accurate if this information is correlated with how you use your car and other metrics that identify the condition of your car more specifically. With connected assets, you can make the preventive maintenance plan more cost-effective and tailored to the specific asset.
Once assets are connected, you can gain information about what is happening to the asset remotely and control settings remotely. If something goes wrong, there are things that can be done before sending someone on-site. For example, if there a problem with a refrigeration unit’s temperature cycle, it could be that the refrigeration unit’s door has been left open. You do not need to send a technician to close the door, as an employee on-site can be notified that the door needs to be closed. Just because something is wrong, does not mean you need to send someone on-site immediately. You can also triage the problem to find out what is wrong and ask someone on-site to investigate the problem or remotely solve the problem by changing the settings for that asset. If the problem cannot be resolved easily, then you can make the decision to send someone to fix the problem.
More than just a condition-based maintenance plan, by measuring different elements of performance, you can start to predict when the next failure is likely to happen. The ability to predict failures is a big change in the service industry. Previously, if a refrigeration unit would break down, you are in emergency mode. In an emergency, it is more difficult to communicate accurate information and make smart decisions.
Depending on the industry, connected assets can contribute to customer expectations and can affect how contracts are set. Previously, when customers bought a product and something went wrong, they paid someone to fix it. Then, customers started paying monthly for service instead of per transaction. You promise you will be there for your customers when something goes wrong, and customers are guaranteeing there will be work for your service organization.
With many products becoming commoditized, companies are trying to differentiate via service. The next step for customers is buying uptime instead of service. Customers are not buying products just for the sake of it, they are buying the hours that the products are functioning and useful. Today, service contracts are reactive, after something is broken. Uptime is proactive, avoiding a situation where an asset can.
It seems logical that in the next evolution, customers want your service organization to be proactive in terms of preventing things from going wrong in the first place. Because with the amount of information that your service organization could have about assets, you will be better positioned to offer uptime as the main metric in your contracts, rather than service level agreements which promise to fix the problem in X amount of time. In some industries, proactive service could be bundled with the product offering. So, customers would buy uptime, and not even worry about who is servicing the product. In the transition from buying service to paying for uptime, connected assets will drive this change much more quickly.
IoT remote monitoring can help you make smarter maintenance choices through connected devices, contact us to learn more.
Learn how to harness the power of Big Data, IoT remote monitoring, and mobile tools to transform your retail operations.
Today's retail facility managers must contend with shrinking budgets, high maintenance costs, and unexpected asset failures. Asset tracking can help.
The right CMMS can help your organization minimize downtime and extend asset life. Here's how.
Subscribe to stay up to date with our latest news, resources and best practices