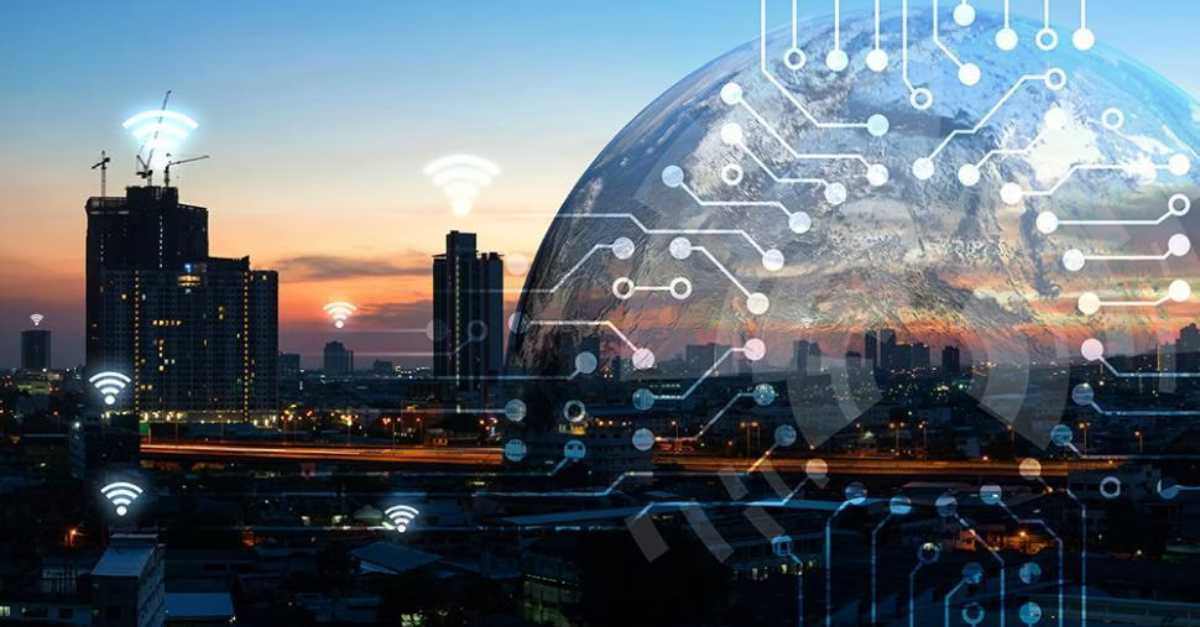
How IoT Remote Monitoring Can Improve Corporate Real Estate Facilities Management Systems
Learn how IoT remote monitoring can positively impact your facilities management systems.
Solutions
Workplace Management Solutions
Real Estate Management Solutions
Maintenance Management Solutions
Energy Management Solutions
Engineering Document Management Solutions
Asset Management Solutions
Automate campus scheduling for classes, meetings, and exams with our EMS software.
Plan and manage conferences effortlessly with EMS software to impress guests and streamline operations.
Boost workplace flexibility and maximize space use with seamless desk and room booking.
Organize workplace or campus events smoothly, creating memorable experiences.
Optimize workspace, manage allocations efficiently, and reduce costs with our space management solutions.
Deliver projects on time and within budget by improving communication, collaboration, and efficiency with our software.
Streamline lease accounting for ASC 842, IFRS, and GASB compliance.
Manage leases efficiently by tracking key dates, analyzing costs, and ensuring compliance.
Centralize data and analytics for better insights, faster negotiations, and revenue growth.
Centralize facility and asset maintenance, automate work orders, and ensure compliance with our CMMS software.
Extend asset life, reduce downtime, and prevent costly repairs with data-driven monitoring.
Prevent equipment failures and extend asset life by detecting and addressing issues early.
Make sustainable, cost-efficient energy decisions by monitoring and optimizing power consumption.
Remotely monitor and control equipment with real-time data to predict issues, boost efficiency, and reduce downtime.
Easily share and collaborate on documents, creating a single source of truth for engineers and contractors.
Manage and analyze assets across their lifecycle to schedule maintenance, reduce downtime, and extend lifespan.
Improve visibility, automate work orders, and ensure compliance for efficient facility and asset management.
Resources
Browse our full library of resources all in one place, including webinars, whitepapers, podcast episodes, and more.
Support
Looking for access to technical support, best practices, helpful videos, or training tools? You’ve come to the right place.
About Accruent
Get the latest information on Accruent, our solutions, events, and the company at large.
Learn how to harness the power of Big Data, IoT remote monitoring, and mobile tools to transform your retail operations.
But how does big data, mobile, and IoT help you improve your operations? To conduct an ongoing analysis of your business and improve your operations, your business processes must be evaluated in light of big data, mobile, and IoT remote monitoring.
To make things practical, you need to make big data small. Making big data small, meaning actionable, is the way to actually improve a business process or answer a question that you ask everyday in your business. You can apply big data to facilitate your processes, monitor assets remotely, maximize capital spend, and project return on investment.
Most often, from a business perspective, you’re collecting data to review and validate your business processes. There’s another variant of data that’s enabled by the “things” that you’re attaching to the Internet. More advanced hardware at lower costs provides information in real time about the condition and location of “things” and enables remote diagnostics and even remote service. For example, equipment, refrigeration units, HVAC systems, are being equipped with sensors, so you can better understand your business processes and make smarter decisions.
“Things” can’t communicate without a mobile communications infrastructure. Mobility is also about putting information in the hands of stakeholders throughout the service supply chain, no matter where they are, so decisions can be made.
When you connect the cloud and security with high-speed wireless networks, you have an enabling force for IoT. A critical factor for IoT is utilizing the big data from tracking these “things”. To make the data frictionless and improve business processes, you must own your data.
The convergence of big data, mobile, and IoT is being fueled by connected devices. The price of devices is falling. The computing firepower is rising. The value of connectivity is increasing.
But your existing monitoring system may not be able to highlight equipment issues efficiently. You may receive a high volume of duplicate and inaccurate alarms. Employees may become frustrated with and distrustful of the alarms. With a monitoring system that’s integrated with an asset management system, your data is available in one database, rather than disparate systems. Your work orders can be streamlined, effective, and even predictive.
You must ask yourself what’s important from a facilities perspective. What really matters? Quality, safety, the customer experience, efficiency, cost savings? Investigate your maintenance practices across the organization to find efficiencies, improve processes, and reduce costs.
Work with the relevant suppliers and manufacturers or the people who have a detailed understanding of the assets, including how each asset operates, the data available, and how that data can be communicated. You need to determine which of your assets are most critical. Those assets should be tagged and entered into an asset management system for tracking.
Because you can track all the different “things” at the asset level, you can make the appropriate fix/replace decisions against investment thresholds to generate savings. For example, warranty claims and vendor compliance, in terms of the effectiveness in fixing particular pieces of equipment. Now you can gain an understanding of every one of your assets. Not just manage work orders, but determine the lifecycle of costs to the asset level.
There’s structured data (fields, forms, and tables). There’s also control-based or text-based information which must be correlated to be understood. This unstructured data is pulled into a data warehouse and a sophisticated rules engine provides recommendations. This data management system becomes your central hub to access data in a usable format.
You need to utilize data in such a way, so that you’re doing the right thing at the right time with the right person. You need to reverse-engineer your maintenance activity. Start at the repair and work backwards to understand what went wrong in the first place. This analysis will help build the rules engine.
For example, telemetry data is the remote measurement of equipment, collecting and transmitting data to receiving equipment for monitoring. With telemetry data, you can predict the asset will fail within a 3-10 day period. If equipment isn’t operating within established parameters as determined by correlating its telemetry data, there’s usually a spike in energy. Less-than-efficient equipment typically uses 20-30% more energy than it should; an indicator of a potential problem.
Through predictive maintenance, you can schedule work orders in advance for more efficient labor management. With predictive maintenance, you can reduce the volume of alarms, increase equipment uptime, identify energy usage which drives savings, as well as improve the quality of work and the positive impact on customers, employees, technicians, and third-party contractors.
What starts as a technology project can realize tangible results from a people perspective, especially for problems during off-hours. In the past, when something broke, technicians had to arrive as quickly as possible and repair the equipment as quickly as possible. Now, you can predict when equipment is going to fail and schedule maintenance activity accordingly.
The concept of predictive maintenance is applicable across various industries. Previously, it would have been difficult to correlate savings. But predictive maintenance changes that. You can reallocate budgets to improve the customer experience and maintain trust in your brand.
Improve operations with big data, mobile, and IoT remote monitoring.
Learn how IoT remote monitoring can positively impact your facilities management systems.
Mobile CMMS functionality is crucial for remote, multi-site and digitally transformed operations. If you're not mobile, here's why you're missing out.
Little inefficiencies in facility management can add up to big consequences like high downtime and poor customer service. IoT remote monitoring can ...
Subscribe to stay up to date with our latest news, resources and best practices