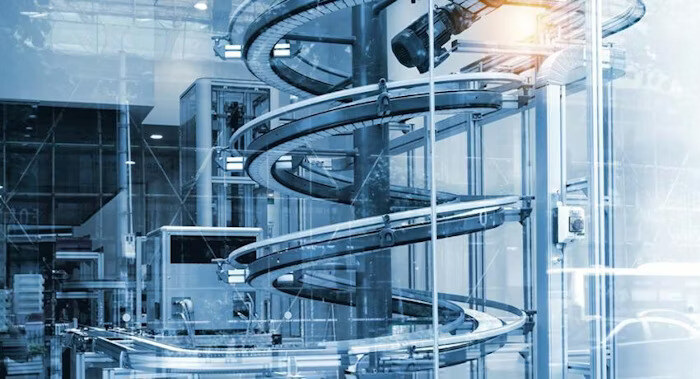
The 3 S's of Beyond Lean for Food Processing: Sustainability, Standardizing & Scalability
If you want to make your food and beverage operations more scalable, standardized, and sustainable, a CMMS can help.
Solutions
Workplace Management Solutions
Real Estate Management Solutions
Maintenance Management Solutions
Energy Management Solutions
Engineering Document Management Solutions
Asset Management Solutions
Automate campus scheduling for classes, meetings, and exams with our EMS software.
Plan and manage conferences effortlessly with EMS software to impress guests and streamline operations.
Boost workplace flexibility and maximize space use with seamless desk and room booking.
Organize workplace or campus events smoothly, creating memorable experiences.
Optimize workspace, manage allocations efficiently, and reduce costs with our space management solutions.
Deliver projects on time and within budget by improving communication, collaboration, and efficiency with our software.
Streamline lease accounting for ASC 842, IFRS, and GASB compliance.
Manage leases efficiently by tracking key dates, analyzing costs, and ensuring compliance.
Centralize data and analytics for better insights, faster negotiations, and revenue growth.
Centralize facility and asset maintenance, automate work orders, and ensure compliance with our CMMS software.
Extend asset life, reduce downtime, and prevent costly repairs with data-driven monitoring.
Prevent equipment failures and extend asset life by detecting and addressing issues early.
Make sustainable, cost-efficient energy decisions by monitoring and optimizing power consumption.
Remotely monitor and control equipment with real-time data to predict issues, boost efficiency, and reduce downtime.
Easily share and collaborate on documents, creating a single source of truth for engineers and contractors.
Manage and analyze assets across their lifecycle to schedule maintenance, reduce downtime, and extend lifespan.
Improve visibility, automate work orders, and ensure compliance for efficient facility and asset management.
Resources
Browse our full library of resources all in one place, including webinars, whitepapers, podcast episodes, and more.
Support
Looking for access to technical support, best practices, helpful videos, or training tools? You’ve come to the right place.
About Accruent
Get the latest information on Accruent, our solutions, events, and the company at large.
How to configure your CMMS/EAM to optimize your food and beverage manufacturing operations, both now and in the long-term.
(Source: Productivity and Costs)
One of the ways to solve this cost issue is to minimize its risk footprint—and you can do this by implementing technology. It does not have to be a full ERP system that overrides your legacy processes and procedures; it can be a computerized maintenance management system (CMMS) that fulfills your independent needs.
There are many benefits to implementing a robust CMMS in the food and beverage industry. For one thing, you benefit from a monitor and maintenance plan with proven results, as did Masters Gallery Foods. And while everyone is looking to reduce their costs to boost ROI, you can do so simply by having a forward thinking, problem solving technology in place.
Here are three proven strategies for success when implementing your CMMS:
Use a “Nested” preventative management strategy
Nesting in manufacturing is well known as laying out patterns to minimize raw material waste. Here we are referring to nesting in software, where you group matching parameter data to figure out patterns, which minimizes financial waste. Using preventive maintenance (PM) by nesting your work orders together, you can group work orders of different length and complexity together when they are due to occur at the same time. This means you can cut the number of PM reports you must manage down to one. Organizations using a CMMS without a nested PM feature are most likely creating additional work.
An example where this may be the most useful is with an overabundance of work orders, which can significantly increase your maintenance effort. Does your monthly PM require a 1-hour procedure to lubricate a production line roller unit? How about an actuator valve on a product filler or maybe an essential lift arm on a packaging conveyor? Does your annual procedure require the total replacement of these vital parts? If so, you risk spending an hour of unnecessary time lubricating a component that is scheduled to be replaced a week later.
This is a common problem that many organizations do not realize. By utilizing a nested PM functionality, users will be required to include all activities and tasks, with monthly tasks being included in every annual PM.
This helps determine which tasks are released to the work order based on the schedule. When the monthly PM is due, the nested PM only releases the monthly tasks. Likewise, when the annual PM is due, the nested PM will release both the monthly and annual tasks.
Need Insight? Use preventative maintenance automation
Two common maintenance challenges in the food and beverage industry are maintaining complex equipment and compliance with regulatory standards. Without the aid of automation, teams can be left scrambling when reactive maintenance and break-fix requests arise, leading to a decrease in controllable risks that range from labor safety concerns to possible compliance violations.
Although these challenges are daunting, organizations can excel in these industry-wide areas of opportunity by leveraging maintenance& automation within their day-to-day maintenance operations.
The advantage that automation provides can be staggering—from an increased return on asset lifecycle cost, enhanced performance safety management, and more effective processes aimed at compliance and regulatory standard execution.
Whether managing maintenance at a single site or multiple locations around the world, it is important to establish a standard approach to maintenance automation. A baseline of automation standards will help:
Understanding the frequency that assets should be maintained and what approach works best is vital to success. A CMMS/EAM with a high level of automation will allow you to mold your maintenance activities based on your processes and best practices, as well as develop and automate the generation of corrective work orders based on certain reading thresholds of any asset.
It is important to notify technicians of work assigned to them and provide them with automated updates regarding the work order's status, specifically work orders approaching their targeted completion date.
You want to ensure that your CMMS/EAM platform includes a robust mobile application so technicians can receive real-time notifications in the field. Automated daily, weekly and monthly reports are a great way to inspire your maintenance team to work harder towards performance targets. When you know where you stand, it becomes more transparent where your need to improve at the team, individual and contributor level.
Enhance efficiency with seamless integration
Accruent’s CMMS/EAM cloud platform Maintenance Connection integrates seamlessly with Meridian – Accruent's best-in-class Engineering Document Management System (EDMS) and Observe – Accruent’s Energy Management & IoT Remote Monitoring software. This integrated solution allows stakeholders to easily access up-to-date documentation from multiple devices, giving technicians access to the information that they need to perform their jobs efficiently. It saves hours in work order preparation, avoids duplication of work, and identifies energy-saving opportunities by leveraging data analytics. The integration capabilities also boost productivity while providing a user-friendly experience by eliminating the need to switch between programs and enter data into disparate systems.
If you want to make your food and beverage operations more scalable, standardized, and sustainable, a CMMS can help.
Explore effective facility management tips for the beverage industry with Accruent. Learn to reduce asset downtime and enhance operational efficiency.
How comprehensive asset intelligence, effective preventive maintenance, and efficient labor scheduling can lead to success in the chemical industry.
Subscribe to stay up to date with our latest news, resources and best practices